Технология погрузки грузов навалом в полувагоны
При погрузке в полувагоны грузов навалом весом отдельных кусков до 1 кН
общий вес груза, падающего на пол полувагона, не должна превышать 50 кН, а
высота падения – 3 м.
При погрузке навалочных грузов навалом массой отдельных кусков свыше
100 кг, но не более 500 кг на дно кузова полувагона должен быть насыпан слой
из мелкокускового груза толщиной не менее 300 мм. Общий вес груза, падаю-
щего на насыпной слой, не должна превышать 70 кН, а высота падения от пола
полувагона 3 м. Навалочные грузы в виде отдельных кусков весом брутто более
5 кН должны в вагон грузиться без сбрасывания (опусканием).
Технология выгрузки насыпных грузов из крытых вагонов
И открытого подвижного состава
The technology of unloading of embankments cargoes from
Covered cars and open top rolling stock
Технология выгрузки насыпных грузов из крытых вагонов
В крытых вагонах перевозят грузы, требующие защиты от атмосферных
осадков. Это ценные химические грузы, инертно-строительные материалы (це-
мент, алебастр и др.), зерно и др.
Имеются следующие технологии выгрузки насыпных грузов из крытых
вагонов:
1-я технология. С применением ЭП или малогабаритными АП с нейтрали-
зацией выхлопных газов, оборудованными бульдозерно-грейферными или ков-
шовыми захватами. При этом ЭП или малогабаритный АП с рампы склада че-
рез переходной мостик заезжает в вагон, захватывает груз, высыпает его в при-
|
|
ёмный бункер и далее груз конвейером подаётся в кузов автомобиля или на
117
склад. Эта технология такая же, как и ТШГ. Техническая производительность в
зависимости от рода груза Птех = 250…300 кН/ч.
2-я технология. С применением механизированной лопаты (скребка). Уст-
ройство механизированной лопаты довольно простое. Схема работы с такой
лопатой показана на рис. 5.13.
Рис. 5.13, а. Выгрузка грузов механической лопатой:
1 − скребок; 2 − тяговый канат; 3 − привагонный блок; 4 − вертикаль-
ный блок; 5 − лебедка; 6 − приемный бункер; 7 − конвейер
Рис. 5.13, б. Схема работы с механизированной лопатой:
1 − крытый вагон; 2 − лопата (скребок); 3 − трос;
4 − блок; 5 − электродвигатель; 6 − завальная яма
После открытия двери крытого вагона насыпной груз самотёком высыпа-
ется в завальную яму. При этом в вагоне с каждой стороны дверного проёма
под углом естественного откоса ñ остается насыпной груз. Механизированная
лопата используется именно для выгрузки этого остатка груза. Технология вы-
грузки груза следующая:
– рабочий, который находится внутри вагона, тащит скребок (лопату) на
|
|
верхний участок груза и внедряет его на груз;
118
– рабочий, который находится внизу, включает электродвигатель;
– рабочий, который находится внутри вагона, перемещаясь вместе со
скребком, способствует высыпанию насыпного груза в приёмное устройство.
Таким образом, механизированная лопата − эта установка периодического
действия. Количество рабочих nраб = 2.
Иногда груз выгружают спаренной механизированной лопатой, т. е. третий
рабочий выгружает лопатой и с другой стороны дверного проёма. В этом слу-
чае количество рабочих nраб = 3.
Поскольку рабочие находятся в неблагоприятных условиях, то они должны
быть обеспечены защитными средствами (респираторы, защитные очки и др.).
Техническая производительность такой установки Птех = 300 кН/ч.
3-я технология. С применением специальных погрузочно-разгрузных ма-
шин непрерывного действия типа МВС − машины вагонные самоходные (для
выгрузки слеживающихся грузов из крытых вагонов, рис. 10.23).
Технология работы разгрузчика следующая. После открывания дверей ва-
гона и снятия ограждения разгрузчик по переходному мостику подъезжает к
грузу, рабочий орган - питатель захватывает груз и передаёт на наклонно рас-
|
|
положенный ковшовый элеватор, после чего груз передаётся отвальному лен-
точному конвейеру в автомобиль или на отвал. При освобождении одной сто-
роны вагона разгрузчик выезжает задним ходом, разворачивается и выгружает
другую половину вагона.
4-я технология. С применением специальных погрузочно-разгрузных ма-
шин – инерционных разгрузочных машин (ИРМ-7), предназначенных для вы-
грузки насыпных грузов из четырехосных крытых вагонов. Схема (рис. 10.14),
устройство, преимущество и недостатки будут рассмотрены на практическом
занятии 10.8.
119
Рис. 10.14. Схема ИРМ-7 ВНИИЖТа:
1 − мост-платформа; 2 − рычаг балансир;
3 − дебалансный вибратор;
4 − поворотный «замок» с рельсовой вставкой; 5 − упорный зажим,
6 − щитоотжиматель; 7 − приёмный бункер с тремя выпускными
отверстиями
Технология выгрузки вагонов следующая. Вагоны под разгрузку подаются
поочерёдно с расцепкой. Благодаря постепенному возвышению одного наруж-
ного рельса вагоны получают поперечный наклон, причём в 15 м от ИРМ этот
наклон уже достигает 10°и первый вагон въезжает на мост, и устанавливается
|
|
примерно посередине моста, а остальные вагоны группы отводятся на 5…10 м
назад.
Оператор включает двигатели винтовых механизмов передвижения упо-
ров, которые выходят из межрельсовых углублений, подходят к вагону и цен-
трируют его. После этого срабатывают конечные выключатели и электродвига-
тели упоров выключаются. В это время на пульте загорается лампа «Упоры у
вагона». Одновременно включается гидросистема и упоры поджимаются, вы-
водятся из работы пружинные аппараты автосцепных приборов вагона и уби-
раются стабилизаторы. Привод насосной станции выключается.
При выгрузке зерна, открыв дверь вагона со стороны выгрузки и закрепив
струбцинкой, подводят к дверному проёму щитовыжиматель и включают авто-
номную насосную станцию его гидросистемы. С помощью прижимной плиты с
шипами и горизонтального цилиндра хлебный щит отжимается вовнутрь ваго-
на, а посредством вертикального цилиндра поднимается вверх и удерживается в
поднятом состоянии.
Выгрузка лёгкосыпучих грузов вагона вначале осуществляется самотёком.
В течение 70…80 с из вагона выгружается самотёком зерно примерно 15…19
тc. После этого оператор включает основной двигатель привода возбудителя
колебаний и вагон колеблется с заданной амплитудой и частотой. Разгон при-
вода до 85…90 об/мин занимает 6…8 с, и зерно начинает высыпаться через
120
дверной проём в приёмный бункер под действием сил инерции. По мере высы-
пания груза и уменьшения общей массы (вагона с грузом и моста) увеличивает-
ся частота и амплитуда колебаний. К концу выгрузки частота колебаний со-
ставляет 118…124 колебаний в минуту, а амплитуда в центре пола вагона
65…70 мм. Через 4.5…5 мин. работы дебалансного вибратора вагон освобож-
дается от груза и не требуется никакой дальнейшей очистки вагона. Продолжи-
тельность разгрузки четырехосного вагона − 10…12 мин.
5-я технология. С применением пневматических установок непрерывного
действия (ПНУ). ПНУ предназначена для перемещения насыпных грузов из
крытых вагонов посредством воздуха. Смесь насыпного груза с воздухом
(аэрированная смесь) перемещается по трубопроводам за счёт разности давле-
ния вначале и в конце трубопровода: ∆p = p к - p н. Разность давлений создаётся
за счёт отсоса воздуха из трубопровода, т. е. за счёт создания в нём вакуума.
Такие установки называются установками всасывающего действия. Разность
давлений может быть создана за счёт напора (нагнетания) воздуха. Поэтому
эти установки ещё называются установками нагнетания.
Для примера рассмотрим схему установки всасывающего действия
(рис. 5.15).
Рис. 5.15. Схема установки всасывающего действия:
1 − заборное устройство; 2 − шланг; 3 − рабочий трубопровод;
4 − осадительная камера (разгружатель);
5 − шлюзовой затвор; 6 − приёмное устройство; 7 − фильтр;
8 − вакуум-насос; 9 − патрубок для выпуска воздуха;
10 − ленточный конвейер
Установка позволяет совершить одновременную выгрузку насыпного груза
из сухогруза (т. е. судна – плавучего средства, предназначенного для перевозки
грузов) и из крытого вагона с использованием заборных устройств, имеющихся
на концах шлангов. При этом сухогруз, крытый вагон, шланг с заборными уст-
121
ройствами и часть трубопровода образуют пункт (фронт) выгрузки. Комплекс
устройств, включающий в себя часть трубопровода, осадительную камеру или
разгружатель, где осаждается груз, шлюзевой затвор, приёмное устройство,
фильтр, вакуум-насос, который отсасывает воздух, и ленточный конвейер, ко-
торый подаёт груз на склад, образуют склад. Склад может находиться на неко-
тором расстоянии от пункта (фронта) погрузки.
Технология выгрузки насыпных грузов следующая. Рабочий после откры-
вания дверей крытого вагона вставляет внутрь вагона заборное устройство и
включает вакуум-насос. На конце трубопровода ∅100…150 мм создаётся раз-
ность давлений. При этом аэрированная смесь перемещается по трубопроводу и
насыпной груз попадает в осадительную камеру, где происходит осаждение
груза. Поскольку сечение этой камеры значительно больше, чем сечение трубо-
провода, то скорость воздуха резко снижается согласно формуле Бернулли: p 1 v 1
= p 2 v 2 , где v 1 > v 2 и p 1 < p 2. Поэтому более тяжёлые частицы аэрированной
смеси падают вниз, а лёгкие частицы вместе с воздухом продолжают переме-
щаться дальше. Более тяжёлые частицы смеси через шлюзовой затвор переме-
щаются вниз.
Устройство шлюзового затвора таково, что он пропускает груз, но не про-
пускает воздух, поскольку в нём вначале открывается верхний клапан и груз
поступает в шлюз. Потом клапан закрывается. После этого открывается нижний
клапан и груз падает на конвейерную ленту, по которой он транспортируется в
бункеры-силосы или на склад.
Через очистительные фильтры также проходят некоторые частицы. Они,
проходя через шлюзовые затворы, попадают на ленточные конвейеры. Фильтры
загрязняются. Воздух, выпущенный через патрубок, также не чист. Поэтому за-
грязняется атмосфера.
Преимущества такой технологии выгрузки насыпных грузов следующие:
– высокий уровень комплексной механизации и автоматизации перегрузоч-
ных работ, т.е. транспортно-грузовой системы;
– герметичность установки, что повышает её экологичность;
– возможность перемещения выгружаемого груза по сложной конфигурации
по пространственной трассе;
– достаточно высокая техническая производительность Птех > 1000 кН/ч. ≈ 2
ваг./ч;
– возможность одновременного забора груза из нескольких транспортных
средств;
– возможность перемещения груза по разветвлениям, т. е. в разные склады.
Недостатки этой технологии:
– невозможность перемещения влажных и налипающих (липких) грузов;
– ограниченность сферы применения из-за того, что размер перемещаемой
частицы груза небольшой (например, в пределах размера зерна);
– достаточно высокий расход электроэнергии из-за того, что электродвига-
тель работает непрерывно.
122
Дата добавления: 2020-04-08; просмотров: 711; Мы поможем в написании вашей работы! |
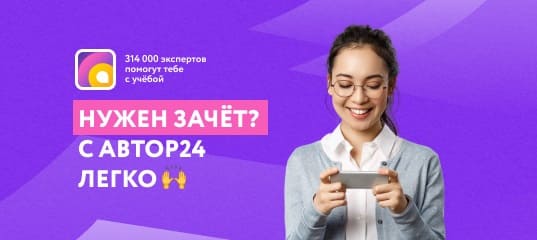
Мы поможем в написании ваших работ!