Химическое полирование сплавов на
Основе железа, меди и её сплавов.
В России хп применяется как правило для меди, алюминия и их сплавов. Из сплавов на основе железа, наилучшие результаты достигаются при обработке коррозионно стойких сталей 12Х18Н9Т.
Используется следующий раствор (%): 34 H2SO4, 6,5 HCl, 4,5HNO3, 0,5 NaCl, 54 H2O, 0,5 краситель кислотный черный 3М, полирование при 70-75 градусов, 5-10 минут продолжительность может возрасти до 10 минут по мере накопления в электролите солей железа.
В 1 л раствора можно обрабатывать деталей до 8 дм2.
При химическом полировании меди и её сплавов используются смеси фосфатной, азотной, уксусной кислоты и менее концентрированные растворы с добавками перекиси водорода. В первом случае допускается изменение содержания компонентов в довольно широком интеграле: 30-80% H3PO4, 5-20 HNO3, 10-50уксусной кис-ты,0-10 H2O. это позволяет подбирать оптимальные составы растворов для полирования различных сплавов меди. Превышение допустимого содержания воды ведет к травлению металла,азотной кислоты к понижению блеска поверхности, фосфорной уменьшение эффективности сглаживания поверхности.температура=18-30 градусов.
Химическое полирование алюминия
И его сплавов.
Алюминий и его сплавы полируются в кислотных растворах, содержащих добавки небольшого количества органических соединений или солей тяжелых металлов (медь,свинец).
В результате реакций, происходящих в процессе полирования соль восстанавливается до металла , который очень тонким слоем осаждается на поверхности алюминия, образуя при этом микро-пары, способствующему лучшему полированию.
|
|
Один из растворов (г-л) 1500-1600 H3PO4, 60-80 HNO3, t=65-75,время полирования-1-5 минут, обрабатывается технический алюминий и сплавы АМг,Амц. Достигается относительно хоршая сглаживаемая поверхность.
Режим полирования устанавливается опытным путем с учетом конфигурации детали, состояния поверхности и состава сплава, из которого он изготовлен.
Промывка детаелй после обработки должна проводиться
быстро и интенсивно,иначе остатки растворов окажут травящее действие на металл(белая пленка).
Физико-химические свойства
И назначение медных покрытий.
Медные гальванические покрытия применяются, как компоненты многослойных систем с целью повышения
их защитных способностей, для увеличения электропроводностей поверхностного слоя деталей, улучшения их паяемости и при изготовлении деталей гальванопластикой.
Гальванически осажденная медь имеет розовый цвет, но в атмосферных услов-хлегко контактирует с влагой иуглекислотой воздуха, с сернистыми промышл-ми газами,покрывается окислами темнеет, следовательно, в качестве индивидуального покрытия может применяться
|
|
при обязательной дополнительной защите бесцветным лаком.Гальванически осажденная медь характеризуется кристаллической структурой и пористостью. Медь, осаждаемая из цианистых электролитов более мелкокристалична и менее пориста, имеет большую микротвёрдостьчем при осаждении из кислых электролитов. После отжига пластичность электро осаждаемой меди улучшается.
В химическом соединении медь 1 и 2 валентна, следовательно, электро-химический эквивалент=2,372 и 1,186.
Характеристика существующих
Электролитов для гальванического меднения.
Электролиты меднения подразделяются на:
-простые (кислые),в которых слой в виде
аква-ионов
-комплексные (щелочные), где медь входит в состав сложного катиона или аниона.
К щелочным электролитам относятся:
цианистые, в которых достигается наилучшее качество покрытий, железо-синеродистые, пирофосфатные и др. Старейшими и наиболее широко применяемыми явл. серно-кислые электролиты меднения. Остальные имеют
ограниченное применение.
Серно-кислые электролиты позволяют применять довольно высокие плотности тока, дают почти 100% выход по току, стабильны в работе и не требуют частых корректировок.
|
|
Недостатки: -крупнокристаллическая структура осадков
-вдвое более низкий эл.-хим. эквивалент двухвалентн. Cu по сравнению с 1Cu входит в состав цианистых электролитов.
-относительно низкая рассеивающая способность
-невозможность на непосредственно железных деталях получить покрытия, имеющие прочное сцепление с основой металла из-за контактного выделения меди на поверхности железа.
Цианистые, медные электролиты обладают высокой рассеивающей способностью, позволяют осаждать медь непосредственно на железе и стальных деталях с хорошим сцеплением.
Изготавливаясь из дорогих и ядовитых солей требуют частой корректировки, у них низкий выход по току 60-80%, постоянно требуют подогрева.
Пирофосфатные электролиты меднения стали алюминия, являются наиболее надежными заменителями цианстых. Обладают хорошей рассеивающей способностью.выход по току 90-95%.
Дата добавления: 2020-04-08; просмотров: 157; Мы поможем в написании вашей работы! |
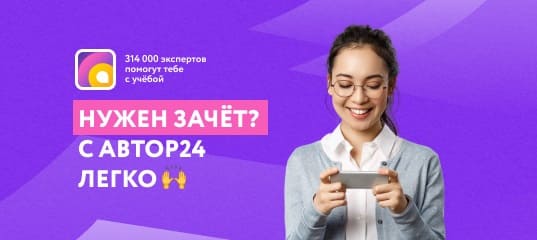
Мы поможем в написании ваших работ!