Расчёт 1-й зубчатой конической передачи
Задание
Спроектировать привод.
В состав привода входят следующие передачи:
1 - закрытая зубчатая коническая передача;
2 - закрытая зубчатая цилиндрическая передача.
Сила на выходном элементе привода F = 11,2 кН.
Скорость на ленте (цепи) привода V = 0,5 м/с.
Диаметр выходного элемента привода D = 260 мм.
Коэффициент годового использования Кг = 0,67.
Коэффициент использования в течении смены Кс = 0,33.
Срок службы L = 15 лет.
Число смен S = 3.
Продолжительность смены T = 8 ч.
Тип нагрузки - постоянный.
Содержание
1 Введение................................................................................................................ 4
2 Выбор электродвигателя и кинематический расчёт.................................... 5
3 Расчёт 1-й зубчатой конической передачи...................................................... 8
3.1 Проектный расчёт................................................................................................. 8
3.2 Проверочный расчёт по контактным напряжениям......................................... 15
3.3 Проверка зубьев передачи на изгиб.................................................................... 15
4 Расчёт 2-й зубчатой цилиндрической передачи............................................. 18
4.1 Проектный расчёт................................................................................................. 18
4.2 Проверочный расчёт по контактным напряжениям......................................... 26
4.3 Проверка зубьев передачи на изгиб.................................................................... 26
5 Предварительный расчёт валов...................................................................... 29
|
|
5.1 Ведущий вал.......................................................................................................... 29
5.2 2-й вал..................................................................................................................... 29
5.3 Выходной вал........................................................................................................ 30
6 Конструктивные размеры шестерен и колёс................................................. 33
6.1 Коническая шестерня 1-й передачи.................................................................... 33
6.2 Коническое колесо 1-й передачи......................................................................... 33
6.3 Цилиндрическая шестерня 2-й передачи............................................................ 33
6.4 Цилиндрическое колесо 2-й передачи................................................................ 34
7 Выбор муфт.......................................................................................................... 35
7.1 Выбор муфты на входном валу привода............................................................ 35
7.2 Выбор муфты на выходном валу привода......................................................... 36
8 Проверка прочности шпоночных соединений............................................... 39
8.1 Колесо 1-й зубчатой конической передачи........................................................ 39
8.2 Шестерня 2-й зубчатой цилиндрической передачи.......................................... 39
8.3 Колесо 2-й зубчатой цилиндрической передачи............................................... 40
9 Конструктивные размеры корпуса редуктора.............................................. 43
|
|
10 Расчёт реакций в опорах.................................................................................... 44
10.1 1-й вал..................................................................................................................... 44
10.2 2-й вал..................................................................................................................... 44
10.3 3-й вал..................................................................................................................... 45
11 Построение эпюр моментов на валах.............................................................. 47
11.1 Расчёт моментов 1-го вала................................................................................... 47
11.2 Эпюры моментов 1-го вала.................................................................................. 48
11.3 Расчёт моментов 2-го вала................................................................................... 49
11.4 Эпюры моментов 2-го вала.................................................................................. 50
11.5 Расчёт моментов 3-го вала................................................................................... 51
11.6 Эпюры моментов 3-го вала.................................................................................. 52
12 Проверка долговечности подшипников......................................................... 53
12.1 1-й вал..................................................................................................................... 53
12.2 2-й вал..................................................................................................................... 55
12.3 3-й вал..................................................................................................................... 58
13 Уточненный расчёт валов................................................................................. 60
|
|
13.1 Расчёт 1-го вала..................................................................................................... 60
13.2 Расчёт 2-го вала..................................................................................................... 61
13.3 Расчёт 3-го вала..................................................................................................... 63
14 Выбор сорта масла.............................................................................................. 68
15 Выбор посадок..................................................................................................... 69
16 Технология сборки редуктора........................................................................... 70
17 Заключение........................................................................................................... 71
18 Список использованной литературы.............................................................. 72
Введение
Машиностроению принадлежит ведущая роль среди других отраслей экономики, так как основные производственные процессы выполняют машины. Поэтому и технический уровень многих отраслей в значительной мере определяет уровень развития машиностроения.
Повышение эксплуатационных и качественных показателей, сокращение времени разработки и внедрения новых машин, повышение их надежности и долговечности – основные задачи конструкторов-машиностроителей. Одним из направлений решения этих задач является совершенствование конструкторской подготовки инженеров высших технических учебных заведений.
|
|
Большие возможности для совершенствования труда конструкторов дает применение ЭВМ, позволяющее оптимизировать конструкции, автоматизировать различную часть процесса проектирования.
Объектами курсового проектирования являются приводы различных машин и механизмов, использующие большинство деталей и узлов общемашиностроительного применения.
Важной целью выполняемого проекта является развитие инженерного мышления, включающее умения использовать предшествующий опыт, находить новые идеи, моделировать, используя аналоги. Курсовому проекту по деталям машин свойственна многовариантность решений при одном и том же задании развивает у студентов мыслительную деятельность и инициативу.
Важнейшая задача курсового проектирования – развитие умения разрабатывать техническую документацию. Базируясь на исходных предпосылках из курса графики и машиностроительного черчения, в процессе самостоятельной работы над курсовым проектом, студенты овладевают свободным чтением и выполнением чертежей неограниченной сложности.
Выбор электродвигателя и кинематический расчёт
По табл. 1.1[1] примем следующие значения КПД:
- для закрытой зубчатой конической передачи: h1 = 0,965
- для закрытой зубчатой цилиндрической передачи: h2 = 0,975
Общий КПД привода вычисляем по формуле:
h = h1 · h2 · hподш.3 · hмуфты2 (2.1)
где hподш. = 0,99 - КПД одной пары подшипников.
hмуфты = 0,98 - КПД одной муфты.
Подставляя, получим:
h = 0,965 · 0,975 · 0,993 · 0,982 = 0,877
Угловая скорость на выходном валу будет:
wвых. = (2.2)
Подставляя соответствующие значения, получаем:
wвых. = = 3,846 рад/с
Требуемая мощность двигателя будет:
Pтреб. = (2.3)
После подстановки имеем:
Pтреб. = = 6,385 кВт
В таблице 24.7[2] по требуемой мощности выбираем электродвигатель 160S8 (исполнение IM1081), с синхронной частотой вращения 750 об/мин, с параметрами: Pдвиг.=7,5 кВт. Номинальная частота вращения с учётом скольжения nдвиг. = 727 об/мин,
Угловая скорость:
wдвиг. = (2.4)
В итоге получаем:
wдвиг. = = 76,131 рад/с.
Oбщее передаточное отношение:
uобщ. = (2.5)
После подстановки получаем:
uобщ. = = 19,795
Для передач выбрали следующие передаточные числа:
u1 = 4
u2 = 5
Рассчитанные частоты и угловые скорости вращения валов сведены ниже в таблицу.
Таблица 2.1. Частоты и угловые скорости вращения валов.
Вал | Частота вращения, об./мин | Угловая скорость вращения, рад/с |
Вал 1-й | n1 = nдвиг. = 727 | w1 = wдвиг. = 76,131 |
Вал 2-й | n2 = = = 181,75 | w2 = = = 19,033 |
Вал 3-й | n3 = = = 36,35 | w3 = = = 3,807 |
Мощности на валах:
P1 = Pтреб. · hподш. · h(муфты 1) = 6,385 · 103 · 0,99 · 0,98 = 6194,727 Вт
P2 = P1 · h1 · hподш. = 6194,727 · 0,965 · 0,99 = 5918,132 Вт
P3 = P2 · h2 · hподш. = 5918,132 · 0,975 · 0,99 = 5712,477 Вт
Вращающие моменты на валах:
T1 = = = 81369,311 Н·мм = 81,369 Н·м
T2 = = = 310940,577 Н·мм = 310,941 Н·м
T3 = = = 1500519,307 Н·мм = 1500,519 Н·м
По таблице 24.7(см. приложение учебника Дунаева/Леликова) выбран электродвигатель 160S8 (исполнение IM1081), с синхронной частотой вращения 750 об/мин, с мощностью Pдвиг.=7,5 кВт. Номинальная частота вращения с учётом скольжения nдвиг. = 727 об/мин.
Таблица 2.2. Передаточные числа и КПД передач.
Передачи | Передаточное число | КПД |
1-я закрытая зубчатая коническая передача | 4 | 0,965 |
2-я закрытая зубчатая цилиндрическая передача | 5 | 0,975 |
Таблица 2.3. Рассчитанные частоты, угловые скорости вращения валов и моменты на валах.
Валы | Частота вращения, об/мин | Угловая скорость, рад/мин | Момент, Нxмм |
1-й вал | 727 | 76,131 | 81369,311 |
2-й вал | 181,75 | 19,033 | 310940,577 |
3-й вал | 36,35 | 3,807 | 1500519,307 |
Расчёт 1-й зубчатой конической передачи
Рис. 3.1. Передача зубчатая коническая.
Проектный расчёт
Так как в задании нет особых требований в отношении габаритов передачи, выбираем материалы со средними механическими характеристиками (см. табл. 2.1-2.3[2]):
- для шестерни:
сталь: 45
термическая обработка: улучшение
твердость: HB 269...302
средняя твердость: HBср. = = = 285,5
- для колеса:
сталь: 45
термическая обработка: улучшение
твердость: HB 235...262
средняя твердость: HBср. = = = 248,5
Допустимые контактные напряжения (стр. 13[2]) , будут:
[s]H = , (3.1)
По таблицам 2.1 и 2.2 гл. 2[2] имеем для сталей с твердостью поверхностей зубьев менее HB 350:
sH lim b = 2 · HBср + 70. (3.2)
sH lim(шестерня) = 2 · 285,5 + 70 = 641 МПа;
sH lim(колесо) = 2 · 248,5 + 70 = 567 МПа;
Предварительное значение диаметра внешней делительной окружности шестерни:
d'e1 = K · (3.3)
d'e1 = 30 · = 86,453 мм.
где коэффициент K в зависимости от поверхностной твёрдости, для выбранных материалов K = 30; для прямозубой конической передачи коэффициент uH = 0,85.
Окружную скорость Vm на среднем делительном диаметре вычисляем по формуле (при Kbe = 0,285):
Vm = (3.4)
Vm = = 2,82 м/с.
SH - коэффициент безопасности SH = 1,1; ZN - коэффициент долговечности, учитывающий влияние ресурса.
ZN = , (3.5)
где NHG - число циклов, соответствующее перелому кривой усталости, определяется по средней твёрдости поверхности зубьев:
NHG = 30 · HBср2.4 £ 12 · 107 (3.6)
NHG(шест.) = 30 · 285,52.4 = 23473395,971
NHG(кол.) = 30 · 248,52.4 = 16823044,669
NHE = mH · Nк - эквивалентное число циклов. (3.7)
Nк = 60 · n · c · tS (3.8)
Здесь :
- n - частота вращения, об./мин.; n(шест.) = n1 = 726,997 об./мин.; n(колеса) = n2 = 181,749 об./мин.
- c = 1 - число колёс, находящихся в зацеплении;
- продолжительность работы передачи в расчётный срок службы, ч.:
tS = 365 · Lг · C · tc · kг · kс (3.9)
- Lг=15 г. - срок службы передачи;
- С=3 - количество смен;
- tc=8 ч. - продолжительность смены;
- kг=0,67 - коэффициент годового использования;
- kс=0,33 - коэффициент суточного использования.
tS = 365 · 15 · 3 · 8 · 0,67 · 0,33 = 29052,54 ч.
mH = 0,18 - коэффициент эквивалентности по табл. 2.4[2] для среднего номинального режима нагрузки (работа большую часть времени со средними нагрузками).Тогда:
Nк(шест.) = 60 · 726,997 · 1 · 29052,54 = 1267266565,343
Nк(кол.) = 60 · 181,749 · 1 · 29052,54 = 316816205,548
NHE(шест.) = 0,18 · 1267266565,343 = 228107981,762
NHE(кол.) = 0,18 · 316816205,548 = 57026916,999
В итоге получаем:
ZN(шест.) = = 0,685
Так как ZN(шест.)<1.0 , то принимаем ZN(шест.) = 1
ZN(кол.) = = 0,816
Так как ZN(кол.)<1.0 , то принимаем ZN(кол.) = 1
ZR = 0,9 - коэффициент, учитывающий влияние шероховатости сопряжённых поверхностей зубьев.
Zv - коэффициент, учитывающий влияние окружной скорости: Zv = 1...1.15
По предварительно найденной окружной скорости получим Zv:
Zv = 0.85 · V0.1 = 0.85 · 2,820.1 = 0,943 (3.10)
Допустимые контактные напряжения:
для шестерни [s]H1 = = 524,455 МПа;
для колеса [s]H2 = = 463,909 МПа;
Для прямозубых колес за расчетное напряжение принимается минимальное допустимое контактное напряжение шестерни или колеса.
Тогда расчетное допускаемое контактное напряжение будет:
[s]H = [s]H2 = 463,909 МПа.
Допустимые напряжения изгиба (стр. 15[2]) , будут:
[s]F = . (3.11)
По таблицам 2.1 и 2.2 гл. 2[2] имеем
sF lim(шестерня) = 499,625 МПа;
sF lim(колесо) = 499,625 МПа;
SF - коэффициент безопасности SF = 1,7; YN - коэффициент долговечности, учитывающий влияние ресурса.
YN = , (3.12)
где NFG - число циклов, соответствующее перелому кривой усталости:
NFG = 4 · 106
NFE = mF · Nк - эквивалентное число циклов. (3.13)
Nк = 60 · n · c · tS (3.14)
Здесь :
- n - частота вращения, об./мин.; n(шест.) = n1 = 726,997 об./мин.; n(колеса) = n2 = 181,749 об./мин.
- c = 1 - число колёс, находящихся в зацеплении;
- продолжительность работы передачи в расчётный срок службы, ч.:
tS = 365 · Lг · C · tc · kг · kс (3.15)
- Lг=15 г. - срок службы передачи;
- С=3 - количество смен;
- tc=8 ч. - продолжительность смены;
- kг=0,67 - коэффициент годового использования;
- kс=0,33 - коэффициент суточного использования.
tS = 365 · 15 · 3 · 8 · 0,67 · 0,33 = 29052,54 ч.
mF = 0,036 - коэффициент эквивалентности по табл. 2.4[2] для среднего номинального режима нагрузки (работа большую часть времени со средними нагрузками).Тогда:
Nк(шест.) = 60 · 726,997 · 1 · 29052,54 = 1267266565,343
Nк(кол.) = 60 · 181,749 · 1 · 29052,54 = 316816205,548
NFE(шест.) = 0,036 · 1267266565,343 = 45621596,352
NFE(кол.) = 0,036 · 316816205,548 = 11405383,4
В итоге получаем:
YN(шест.) = = 0,667
Так как YN(шест.)<1.0 , то принимаем YN(шест.) = 1
YN(кол.) = = 0,84
Так как YN(кол.)<1.0 , то принимаем YN(кол.) = 1
YR = 1 - коэффициент, учитывающий влияние шероховатости, переходной поверхности между зубьями.
YA - коэффициент, учитывающий влияние двустороннего приложения нагрузки (реверса). При нереверсивной нагрузке для материалов шестерни и колеса YA = 1 (стр. 16[2]).
Допустимые напряжения изгиба:
для шестерни [s]F1 = = 293,897 МПа;
для колеса [s]F2 = = 293,897 МПа;
При полученной скорости для конической прямозубой передачи выбираем 7-ю степень точности.
Уточняем предварительно найденное значение диаметра внешней делительной окружности шестерни:
de1 = 165 · (3.16)
где коэффициент внутренней динамической нагрузки KHv = 1,141 для прямозубой конической передачи выбираем по табл. 2.6[2], условно принимая точность на одну степень грубее фактической, то есть: 8. Коэффициент KHb, учитывающий неравномерность распределения нагрузки по длине контактных линий, находим через коэффициент KHbo = 1,12. Для конических колёс с прямыми зубьями:
KHb = KHbo = 1,12 (3.17)
В итоге получаем:
de1 = 165 · = 86,104 мм.
Так как ширина зубчатого венца и диаметр шестерни ещё не определены, значение коэффициента ybd вычисляем ориентировочно:
ybd = 0,166 · = 0,166 · = 0,684 (3.18)
Угол делительного конуса шестерни:
d1 = arctg = arctg = 14,036o (3.19)
Внешнее конусное расстояние:
Re = = = 177,511 мм (3.20)
Ширина зубчатого венца:
b = 0,285 · Re = 0,285 · 177,511 = 50,591 мм (3.21)
Принимаем по табл. 24.1[2] b = 52 мм.
Внешний торцовой модуль передачи:
me ³ (3.22)
где коэффициент внутренней динамической нагрузки KFv = 1,226 для прямозубой конической передачи выбираем по табл. 2.9[2], условно принимая точность на одну степень грубее фактической, то есть :8. коэффициент KFb, учитывающий неравномерность распределения напряжений у основания зубьев по ширине зубчатого венца, для конических передач с прямыми зубьями:
KFb = K'Fb, (3.23)
здесь:
K'Fb = 0,18 + 0,82 · KHbo = 0,18 + 0,82 · 1,12 = 1,098 (3.24)
KFb = 1,098
Для прямозубой конической передачи коэффициент uF = 0,85.
Тогда:
me ³ = 1,371 мм.
Принимаем по табл. 24.1[2] me = 3,2 мм.
Числа зубьев шестерни:
z1 = = = 26,908 » 27 (3.25)
Числа зубьев колеса:
z2 = z1 · u1 = 27 · 4 = 108 (3.26)
Фактическое передаточное число будет:
u1ф = = = 4 (3.27)
Фактическое значение передаточного числа отличается на 0%, что меньше, чем допустимые 4% для двухступенчатого редуктора.
Углы делительных конусов шестерни и колеса:
d1 = arctg = arctg = 14,036o (3.28)
d2 = 90o - d1 = 90o - 14,036o = 75,964o (3.29)
Делительные диаметры колёс:
de1 = me · z1 = 3,2 · 27 = 86,4 мм; (3.30)
de2 = me · z2 = 3,2 · 108 = 345,6 мм. (3.31)
Внешние делительные диаметры колёс:
dae1 = de1 + 2 · (1 + xe1) · me · cos(d1) (3.32)
dae1 = 86,4 + 2 · (1 + 0,36) · 3,2 · cos(14,036o) = 94,844 мм
dae2 = de2 + 2 · (1 + xe2) · me · cos(d2) (3.33)
dae2 = 345,6 + 2 · (1 - 0,36) · 3,2 · cos(75,964o) = 346,593 мм
где xe1 = 0,36 - смещение для шестерни, находится по таблице 2.12[2]. Смещение для колеса xe2 = -xe1 = -0,36.
Средний делительный диаметр шестерни и колеса:
d1 = 2 · (Re - 0,5 · b) · sin(d1) (3.34)
d1 = 2 · (177,511 - 0,5 · 52) · sin(14,036o) = 73,492 мм.
d2 = 2 · (Re - 0,5 · b) · sin(d2) (3.35)
d2 = 2 · (177,511 - 0,5 · 52) · sin(75,964o) = 293,975 мм.
Силы в зацеплении:
окружная сила на среднем диаметре:
Ft = = = 2197,826 H (3.36)
здесь: dm1 = 0,857 · de1 = 0,857 · 86,4 = 74,045 мм
осевая сила на шестерне:
Fa1 = Ft · tg(a) · sin(d1) = 2197,826 · tg(20o) · sin(14,036o) = 194,011 H (3.37)
радиальная сила на шестерне:
Fr1 = Ft · tg(a) · cos(d1) = 2197,826 · tg(20o) · cos(14,036o) = 776,06 H (3.38)
осевая сила на колесе:
Fa2 = Fr1 = 776,06 H (3.39)
радиальная сила на колесе:
Fr2 = Fa1 = 194,011 H (3.40)
Дата добавления: 2019-11-16; просмотров: 361; Мы поможем в написании вашей работы! |
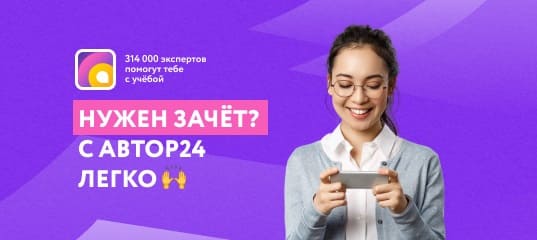
Мы поможем в написании ваших работ!