Новые процессы разработки изделий и гибкое производство
Новые процессы разработки изделий не должны строиться на «классических» подходах, описанных в ГОСТ «доцифровой» эпохи, но должны представлять собой их глобальное переосмысление в разрезе парадигмы цифрового проектирования. Таким образом, прежде чем разрабатывать новые процессы, следует внимательно присмотреться к имеющимся работоспособным процессам, изучить их: может быть, они пригодны для переосмысления, оптимизации.
В конечном счете, цель оптимизации существующих процессов, как и разработки новых, в первую очередь – повышение конкурентоспособности предприятия на глобальных рынках в свете тренда цифровизации и Индустрии 4.0.
Новые процессы разработки изделий тесно связаны с другой концепцией – гибкого производства. Гибкое производство – это производство, оптимизировавшее все свои производственные процессы, чтобы иметь возможность быстро реагировать на потребности клиентов и изменения на рынке, сохраняя при этом контроль над затратами и качеством.
При разработке новых процессов в рамках реализации концепции гибкого производства следует принимать во внимание:
· максимально возможное распараллеливание работ;
· смещение циклов доработок изделия на начальные стадии ЖЦ;
· внедрение новых технологий производства – в частности, аддитивных технологий (ГОСТ Р 57590-2017);
· переход на прогрессивные модели управления ЖЦ изделий;
· оптимизацию штатного состава организации согласно новой парадигме цифрового проектирования (см. раздел 2.2.2);
|
|
· развитие интеграционных сервисов – платформ корпоративных шин данных (см. раздел 2.2.1.4.2), интеграцию прикладных АС между собой;
· широкое распространение прикладных АС, решающих задачи автоматизации выполнения проектно-конструкторских работ (ПКР, ГОСТ 58300-2018);
· представление результатов проектно-конструкторских работ – РКР (ГОСТ 58299-2018) в виде электронных макетов изделий – ЭМИ (ГОСТ 58301-2018).
Максимально возможное распараллеливание работ
Данный подход призван устранить основной недостаток классических подходов к выстраиванию последовательных процессов разработки и производства изделий – когда мы вынуждены дожидаться окончания предыдущего этапа разработки, не имея возможности начать следующий этап. В конечном счете, это увеличивает время вывода изделия на рынок (time-to-market) и снижает конкурентоспособность предприятия.
Чтобы устранить этот недостаток, мы должны выстраивать бизнес-процессы с параллельной рассылкой заданий и с обязательными этапами сведения частей выполненных работ в единое целое (документ, часть изделия и т.п.). Такое распараллеливание работ должно управляться, автоматизироваться и настраиваться в рамках системы управления бизнес-процессами (Business-process EDM, EDMS). Зачастую функциональность управления бизнес-процессами присутствует также в PDM- и EDM-системах (Система электронного документооборота (Electronic Document Management), СЭД, EDM).
|
|
Система организует параллельную выдачу заданий исполнителям, может быть установлено время исполнения заданий, благодаря чему система будет сигнализировать о факте просрочки.
Смещение циклов доработок изделия на начальные стадии ЖЦ осуществляется за счет:
· использования концепции модельно-ориентированного проектирования (см. раздел 2.2.3.3);
· использования PDM-системы для обеспечения раннего доступа всех вовлеченных пользователей к материалам проекта;
· построения цифровых фабрик с использованием технологий цифрового проектирования изделий (см. главу 1).
Внедрение новых технологий производства и, в частности, аддитивных технологий позволяет:
· перейти от массового производства к массовой кастомизации (возможность удовлетворения запросов как можно большего числа индивидуальных заказчиков);
· сократить производственные издержки по причине отсутствия длинных технологических переделов;
|
|
· не содержать большого парка технологического оборудования;
· создавать изделия со сложной или даже невозможной в обычном производстве конфигурацией (бионический/генеративный дизайн);
· исключить использование технологической оснастки;
· повысить гибкость производства (отсутствует необходимость переналадки оборудования под новое изделие, достаточно загрузить новую 3D-модель);
· полностью автоматизировать процесс производства (весь производственный процесс проходит в автоматическом режиме без дополнительных технологических операций со стороны оператора);
· децентрализовать производство и организовать дистанционное управление (для запуска производства нет необходимости в личном присутствии оператора, можно удаленно отправить 3D-модель по Сети интернет, а затем лишь забирать готовые партии изделий);
· значительно уменьшить объем отходов;
· влиять на качество получаемых изделий за счет улучшения качества используемых материалов (дисперсность и т.д.).
Выстраивание единой цифровой шины производства с обратными связями
В концепции единой цифровой шины код управляющих программ генерируется на основании ЭМИ и в автоматическом режиме поступает на производство, загружаясь в соответствующее производственное оборудование.
В то же время информация о состоянии станочного оборудования, режимах обработки деталей, характеристиках обработанных партий и т.д. в режиме онлайн поступает на рабочие места технологов, мастеров, начальников цехов – что позволяет осуществлять управляющие воздействия на оборудование, оптимизируя производственный процесс. Данная технология носит название «цикл обратной связи» – closed loop feedback [33].
Дата добавления: 2020-01-07; просмотров: 201; Мы поможем в написании вашей работы! |
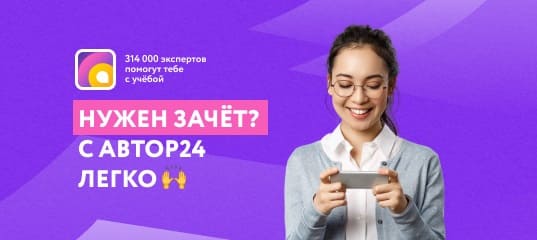
Мы поможем в написании ваших работ!