Температуры отжига холоднодеформированного металла
Наименьшую температуру начала рекристаллизации называют температурой рекристаллизацииТр (К) или t р (°С).
Температура рекристаллизации одного и того же сплава может изменяться от: химического состава (исходное состояние); степени предшествующей деформации (процесс деформирования); времени отжига (технология последеформационного нагрева).
Температура рекристаллизации определяется по формуле А.А.Бочвара:
Т.р = kТпл К
где k – коэффициент, зависящий от чистоты металла и степени легирования.
Для чистых металлов и сплавов температура Тр составляет (0,25 - 0,30) Тпл. Для металлов и сплавов технической чистоты, деформированных на 60 - 70 %, Тр составляет (0,3 - 0,4) Тпл. Для высоколегированных сплавов со структурой твердых растворов Тр возрастает до (0,5 - 0,6) Тпл. В практике термообработки используют температуру в °С ( tр).
Для осуществления рекристаллизации и снятия наклепа проводят специальную термическую обработку, называемую рекристаллизационным отжигом. При этой термообработке холоднодеформированный сплав нагревают до температур, превышающий температуру рекристаллизации, для того, чтобы обеспечить высокую скорость рекристаллизации и полноту ее протекания: tотж = tр + 150 – 200ºС. По окончании первичной рекристаллизации, несмотря на существенное уменьшение свободной энергии металла, структура остается нестабильной вследствие сильно развитой поверхности границ зерен при мелком зерне. Дальнейшее повышение стабильности структуры происходит во время собирательной рекристаллизации, которая протекает при температурах выше температуры рекристаллизации.
|
|
Собирательная рекристаллизация – стадия после деформационного нагрева, во время которой происходит увеличение размеров рекристаллизованных зерен. Движущая сила собирательной рекристаллизации – стремление системы к минимуму свободной энергии за счёт уменьшения поверхностной энергии при росте зерен.При собирательной рекристаллизации плотность дислокаций практически не изменяется, поэтому незначительное снижение прочности происходит только за счет уменьшения протяженности границ, являющихся барьерами для перемещения дислокаций; характеристики пластичности изменяются незначительно.
Горячая пластическая деформация (ГПД) происходит при температурах, значительно превышающих температуру рекристаллизации (табл. 2.4). В связи с этим во время горячей деформации в сплаве происходят одновременно как процессы упрочнения (от деформации), так и разупрочнения (от повышенной температуры).
Таблица 2.2
|
|
Температура начала рекристаллизации, интервал температур рекристаллизационного отжига и горячей обработки давлением
Металл | Температура рекристаллизации,ºС | Температура рекристаллизационного отжига,°С | Температура горячей обработки давлением,°С |
Железо | 450 | 600 - 700 | 800 - 1300 |
Медь | 270 | 450 - 500 | 600 - 800 |
Алюминий | 150 | 250 - 350 | 350 - 450 |
Молибден | 900 | 1400 - 1600 | 1400 - 2000 |
Разупрочнение обусловлено протеканием как рекристаллизации динамической, так и полигонизации динамической.
Динамическая полигонизация в отличие от полигонизации, развивающейся только при термическом воздействии, сопровождается увеличением плотности дислокаций в сформировавшихся субзернах. Когда получается полигонизованная структура, то уровень прочностных свойств повышается: например, предел текучести σ0,2 может быть увеличен на 20 - 60 %.
Динамическая рекристаллизация отличается от статической тем, что появившиеся рекристализованные зерна с низкой плотностью дислокаций во время своего роста наклепываются из-за продолжающейся (во время технологического процесса) – деформации. Участки, рекристаллизовавшиеся в первую очередь, наклепываются раньше, и в них быстрее достигается критическая плотность дислокаций, необходимая для зарождения новых рекристаллизовавшихся зерен, которые затем наклепываются и т.д., следствием чего является значительное разупрочнение материала.
|
|
Изменяя условия прокатки – степень деформации (), скорость (Vдеф) и температуру деформации (tдеф), можно регулировать конечную, после деформации, структуру сплава, размер зёрен, и, следовательно, его свойства.
Конечная структура и механические свойства горячедеформированного металла зависят не только от технологических параметров деформирования (степень, температура, скорость), но и от скорости охлаждения (Vохл) после окончания процесса в последеформационный период, когда металл еще остается горячим. Повышение прочности происходит в том случае, когда заторможены процессы диффузии, способствующие рекристаллизации: деформация с большими скоростями; пониженная температура; высокая скорость охлаждения после деформирования.
Достоинства горячей обработки давлением.
1. Экономическая целесообразность, т.к. в отличие от холодной не требуется проведение промежуточных отжигов для снятия наклепа
2. Возможность получения мелкозернистой структуры при увеличении скорости деформации.
|
|
Недостатки горячей обработки давлением:
1. Большая неоднородность структуры и свойств, что связано с градиентом деформации (поверхность сильнее деформирована, чем сердцевина) и температуры (поверхность охлаждается быстрее сердцевины).
2. Низкое качество поверхности из-за образования окалины (после холодной пластической деформации окисление минимально).
3. Трудности поддержания постоянной температуры при деформировании тонких полуфабрикатов. Изделия с небольшим сечением, как правило, деформируют в холодном состоянии.
Термическая обработка.
Термическая обработка - технологический процесс обработки заготовок и изделий путём теплового воздействия, приводящий к изменению фазового состава, структуры и свойств.
Термическую обработку подразделяют на собственно термическую обработку, термомеханическую обработку и химико-термическую обработку:
- термическая обработка включает тепловое воздействие на материал;
- термомеханическая сочетает одновременно тепловое и деформационное воздействие;
- химико-термическая обработка сочетает тепловое воздействие на весь объем материала и изменение химического состава приповерхностных слоев.
Термической обработке подвергают практически все материальные объекты машиностроительного производства: слитки, полуфабрикаты, детали на различных стадиях изготовления – после обработки резанием, сварки и т.п. Таким образом, если какой-либо из технологических этапов обработки (деформацию, сварку, обработку резанием) можно применять или не применять при изготовлении деталей, то термическую обработку применяют практически ко всем деталям.
Термомеханическую обработку используют как промежуточную для полуфабрикатов и как окончательную – для деталей относительно простой формы (рессоры, штанги).
Химико-термическая обработка используется для деталей специального назначения, например, работающих в условиях износа, циклических контактных нагрузок. В результате ее проведения меняются структурно-фазовое состояние и свойства приповерхностного слоя детали.
Виды термической обработки подразделяют также на промежуточные (межоперационные) и окончательные – по расположению в общем цикле изготовления деталей машин.
Цель промежуточных видов термической обработки – устранение негативных изменений структуры и химического состава, возникающих на различных этапах изготовления деталей: при литье, горячей и холодной деформации, при механической обработке резанием, при сварке.
Цель окончательных видов термообработки – обеспечение комплекса механических свойств детали. Необходимый комплекс свойств достигается за счет того, что при термической обработке происходит изменение структурно-фазового состояния материалов:
К основным видам объемной термообработки относят следующие четыре технологические операции: отжиг, нормализация (для сталей), закалка, отпуск, старение (рис. 2.17).
Рис. 2.17. Схема классификации основных видов термообработки
Отжиг для большинства сплавов применяют в основном как межоперационную, промежуточную обработку. Для углеродистых сталей и титановых сплавов отжиг может быть окончательной термообработкой.
Отжиг , при котором не происходит фазовых превращений, называется отжигом I рода; а при котором протекают фазовые превращения – отжигом II рода.
Для обеспечения повышенного уровня прочности ответственных деталей используют термическое упрочнение (упрочняющую термическую обработку).
Упрочняющая термическая обработка проводится в два последовательных этапа: закалка + старение или закалка + отпуск.
Дата добавления: 2020-01-07; просмотров: 370; Мы поможем в написании вашей работы! |
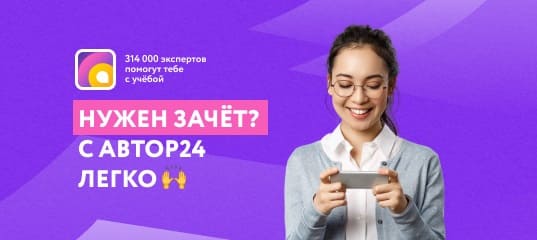
Мы поможем в написании ваших работ!