Основные свойства и характеристики металлов и сплавов
Для получения достаточно полной и надежной информации о свойствах конструкционных материалов проводится ряд испытаний, по результатам которых может быть получена информацию о тех свойствам, которые обеспечивают технологичность изготовления изделий, а также надежность и долговечность в эксплуатации.
При определении пригодности конструкционных материалов для изготовления конкретных видов изделий необходимо иметь информацию о механических, физических, химических, технологических свойствах.
Свойство – это категория, выражающая такую сторону предмета, которая обусловливает его различие или общность с другими предметами и обнаруживается в его отношении к ним. Количественно свойство выражается в виде характеристики, определяемой способом и условиями испытания материала (изделия). Уровень значений любой характеристики является следствием внутреннего строения материала и строения его поверхности.
Характеристики механических свойств.
Механическими свойствами называются свойства, которые определяются при испытаниях под действием внешних нагрузок. Результатом таких испытаний являются количественные характеристики механических свойств.
Механические свойства характеризуют поведение материала под действием напряжений, приводящих к деформация и разрушению, и действующих как в процессе изготовления изделий (литье, обработка давлением, сварка и т.п.), так и при эксплуатации.
|
|
Прочность – способность материала сопротивляться деформации или разрушению под действием статических, циклических или динамических нагрузок. Стандартные характеристики механических свойств определяют в лабораторных условиях на образцах стандартных размеров посредством создания необратимой пластической деформации или разрушения образцов (ГОСТ 1497–84). Значения полученных характеристик обычно приводятся в справочниках.
Испытания на статическое одноосное растяжение являются первичным источником информации о прочности и пластичности материалов. При этих испытаниях получают несколько характеристик:
Временное сопротивление разрыву (предел прочности) – σв (МПа) - напряжение, отвечающее наибольшей нагрузке, предшествующей разрушению образца.
Предел текучести – σт или σ0,2 (МПа) - напряжение, вызывающее остаточную деформацию, равную 0,2 %.
Предел упругости – σ0,05 (МПа) – напряжение, при котором остаточное удлинение составляет 0,05 %; характеризует предельное напряжение, которое допустимо при работе упругих элементов.
Пластичность– свойство материала под действием внешних сил изменять свою форму и размеры не разрушаясь, и сохранять остаточную (пластическую) деформацию после снятия нагрузки.
|
|
Относительное удлинение – δ ( %) – отношение прироста длины образца после разрыва, вызванного действием приложенной силы, к его исходной длине.
Относительное сужение – ψ (%) – уменьшение площади поперечного сечения образца в месте разрыва, вызванного действием приложенной силы, к исходной площади поперечного сечения.
Два последних свойства объединяют в понятие «пластичность» материала.
Твёрдость - интегральная характеристика, показывающая сопротивление материала пластической деформации при контактном воздействии (при вдавливании индентора). Для целого ряда материалов численные значения твёрдости и временного сопротивления пропорциональны. Измерение твёрдости - самый доступный и распространённый вид механических испытаний. В зависимости от метода испытания на твердость (типа индентора) эту характеристику обозначают:
HRC – твердость по Роквеллу;
HB – твердость по Бринеллю;
HV – твердость по Виккерсу.
Предел выносливости – напряжение, которое материал выдерживает при циклическом нагружении с заданной частотой нагружения и в течение определённого количества циклов - без разрушения.
|
|
При испытаниях на усталость база испытания образцов обычно составляет 107, 2·107, 108 циклов. База испытания– число циклов, которое выдерживает образец. Предел выносливости имеет различные обозначения: при симметричном цикле нагружения он обозначается s-1, а при несимметричном цикле - s0.
В большинстве случаев предел выносливости определяют при испытании на изгиб с кручением. Существуют также испытания на консольный изгиб.
При испытании на выносливость партии образцов их нагружают с постепенно уменьшающимся напряжением, пока не будет достигнуто напряжение, при котором все образцы проходят базу испытания без разрушения. Это значение и является пределом выносливости s -1.
Ударная вязкость – характеристика способности материала сопротивляться разрушению при динамической нагрузке. Она оценивается по работе, затраченной на излом образца с надрезом при разрушении посредством удара на маятниковом копре: испытание на ударный изгиб. Работу разрушения относят к площади поперечного сечения образца в месте надреза. Размерность ударной вязкости – КДж/м2. Обозначение этой характеристики зависит от типа надреза: KCU – U - образный надрез; KCV – V - образный надрез; KCT – V - образный надрез с нанесенной на него усталостной трещиной.
Дата добавления: 2020-01-07; просмотров: 157; Мы поможем в написании вашей работы! |
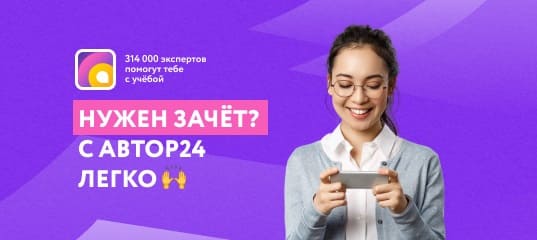
Мы поможем в написании ваших работ!