Б – твёрдый раствора замещения со статистическим распределением атомов; в – упорядоченный твёрдый раствор замещения
В твёрдых растворах внедрения атомы легирующего компонента располагаются в междуузлиях (рис. 2.4, а). Твердые растворы внедрения образуются в сплавах, содержащих металлоиды: водород, азот, углерод, бор, атомы которых имеют малые радиусы, сравнимые с размером пор и междуузельных пространств в кристаллической решётке металлов.
Твёрдые растворы замещения образуются в сплавах, легированных металлами. В этих твёрдых растворах атомы легирующего компонента замещают атомы основного металла в узлах кристаллической решётки (рис.2.4, б). В большинстве сплавов это замещение является хаотическим, беспорядочным (рис. 2.4, б). Но существует ряд сплавов, в твёрдых растворах которых атомы легирующего элемента располагаются упорядоченно, в определённых узлах кристаллической решётки (рис. 2.4, в).
Промежуточные фазы (ПФ) – это химические соединения, которые образуются в сплавах при определённом соотношении компонентов, в интервале концентраций между чистыми компонентами сплавов. Их частицы отделены от матричного твёрдого раствора поверхностью раздела. ПФ отличаются от твердых растворов также типом межатомной связи: она может быть ковалентной, ковалентно-металлической, ионной. В любом случае это более сильные связи, чем металлическая связь, вследствие чего ПФ имеют более высокую температуру плавления, модуль упругости, твердость, чем твердые растворы.
В сплавах промежуточные фазы подразделяются по названию легирующего элемента, образующего соединение с металлом: соединения с кислородом – оксиды; соединения с водородом – гидриды; соединения с углеродом – карбиды; соединения с азотом – нитриды; соединения с бором – бориды; соединения кремнием – силициды; соединения с другим металлом – интерметаллиды или интерметаллические фазы.
|
|
Наибольшее значение в сплавах на основе чёрных металлов, сталях и чугунах, имеют карбиды и нитриды.
В порядке увеличения карбидообразующей (нитридообразующей) способности легирующие элементы располагаются в ряд:
| |||||
(Fe, Ni) → | (Mn) → | (Cr, Mo, W) → | (V, Nb) → | (Ti, Zr) | |
увеличение карбидообразующей (нитридообразующей) способности |
Карбиды и нитриды элементов, имеющих большую карбидообразующую (нитридообразующую) способность, чем железо и образуются практически на всех технологических этапах изготовления изделий, связанных с повышенными температурами. Их обычно называют «специальными». Это фазы:
· TiC, NbC, VC, ZrC, TiN, NbN, с общей формулой MeX (МеС, MeN), имеющие гранецентрированную кристаллическую решётку;
· Карбиды Fe3C, Cr7C3, Cr23C6, Mo6C, имеющие сложные кристаллические решетки.
|
|
Такие промежуточные фазы как нитриды FeN, Fe2N, Fe4N, CrN, AlN, образуютсяпри специальной обработке поверхности – азотировании
Карбиды и нитриды в сталях имеют твердость в несколько раз более высокую, чем твёрдые растворы, а модуль упругости ихпревышает модуль упругости сталей более чем в 2 раза. Эти соединения различным образом влияют на свойства сплавов; их используют для упрочнения объёма сплава и для упрочнения поверхности.
Промежуточные фазы в виде интерметаллидов существенно влияют на свойства цветных сплавов. Они обычно обозначаются прописными буквами греческого алфавита. Количество групп и типов этих соединений в сплавах чрезвычайно велико. Практическое значение в машиностроительных сплавах имеют четыре группы интерметаллидов: фазы Лавеса (λ), сигма - фазы (σ), фазы типа Ni3Al (γ΄), электронные соединения (δ, ε, γ) .
Фазовые превращения. Возможность получения разнообразных свойств в сплавах обусловлена тем, что в них могут протекать различные фазовые превращения. Фазовые превращения в сплавах в твёрдом состоянии происходят при нагреве или при охлаждении исостоят в замене одной фазы (или нескольких фаз) на другую фазу (или нескольких фаз). В упрощённом виде эти превращения описываются той или иной твердофазной реакцией между исходной фазой («старой» – old) – Фold и вновь образующейся («новой» - new) фазой – Фnew:
|
|
Фold → Фnew
или для двух образующихся фаз
Фold → Ф 1new + Ф2new .
В результате твёрдофазной реакции образуется фаза (фазы), отличающиеся от исходной – или только кристаллической структурой или одновременно и кристаллической структурой, и химическим составом.
Твёрдофазные превращения протекают в сплавах под воздействием температуры, количественного соотношения элементов (химического состава).
В зависимости от того, насколько новая фаза отличается от исходной – только кристаллической структурой или кристаллической структурой и химическим составом существует несколько типов фазовых превращений:
1. Распад твёрдого раствора. При этом новая фаза (фазы) имеет и кристаллическую решётку, и химический состав, отличные от исходной фазы:
Cхема I
кристаллическая решётка (Фold) ≠ кристаллическая решётка (Фnew)
химический состав(Фold) ≠ химический состав (Фnew)
2. Полиморфное превращение в сплавах, обусловленное полиморфизмом одного из компонентов. Полиморфное превращение может протекать как по схеме I, так и схеме II:
|
|
Cхема II
кристаллическая решётка (Фold) ≠ кристаллическая решётка (Фnew)
химический состав(Фold) = химический состав (Фnew)
Все указанные превращения протекают равновесно, т.е. в соответствии с диаграммами состояния. Равновесное состояние получают при очень медленных скоростях нагрева или охлаждения. Равновесие сплава данного состава – состояние, которое не может быть изменено при изменении внешних условий, в частности температуры. Обычно полученное состояние характеризуется наименьшей прочностью и наибольшей пластичностью.
Если в результате фазовых превращений получается метастабильное состояние, то оно обычно характеризуется повышенной прочностью.
Неравновесный распад твёрдого раствора происходит в том случае, когда из высокотемпературной области твёрдый раствор охлаждается ускоренно и равновесный распад предотвращается. Например, распад твёрдого раствора не происходит, а при комнатной температуре получается твёрдый раствор пересыщенный по содержанию легирующего элемента.
В результате неравновесного полиморфного превращения получается фаза, не соответствующая низкотемпературной модификации на диаграмме состояния. Это – неравновесная фаза, называемая мартенсит.
Мартенсит – это матричная фаза, которая может быть твердым раствором замещения или внедрения, ненасыщенным и пересыщенным.
Когда мартенсит является твердым раствором замещения (стали систем Fe - Ni, Fe – Cr - Ni, титановые и др. сплавы), то он имеет невысокую твердость и повышенную пластичность, даже, если он является пересыщенным. Когда мартенсит представляет собой твердый раствор внедрения, да к тому же и пересыщенный, то он имеет очень высокую твердость и хрупкость. Таким является мартенсит углеродистых, низко- и среднелегированных сталей. При нагреве такой фазы из твёрдого раствора обычно выделяются высокодисперсные фазы, не соответствующие равновесию, что приводит к значительному упрочнению сплава. Неравновесные фазы при последующем нагреве распадаются с образование стабильных или метастабильных новых фаз.
Зерна, дендриты, волокна, гранулы, порошки. Эти составляющие строения материалов могут быть различным образом расположены в реальном материале, что и составляет его структуру.
Структура материала – это закономерная пространственная организация, т.е. взаимное расположение объектов, составляющих материал и фаз, расположенных внутри материала, включая границы их раздела.
Рис. 2.5. Обобщённая схема технологии изготовления деталей
Из сплавов (деформируемых)
Формирование структуры реальных металлов и сплавов (промышленных, экспериментальных) происходит на всех этапах технологического процесса получения изделия (детали) с заданными свойствами (рис. 2.5). При традиционном способе изготовления после выбора химического состава сплава проводится выплавка, разливка, деформация (горячая и холодная), механическая обработка, а также промежуточная и окончательная термическая обработка. На каждом технологическом этапе происходит изменение структуры материала – слитка, деформированного полуфабриката, заготовки под деталь, самой детали (изделия).
В результате этого формируется не идеальная (совершенная) кристаллическая структура, а структура искажённая, несовершенная. Это происходит по нескольким причинам:
– реальный сплав является поликристаллическим, т.е. состоит из множества монокристаллов; эти монокристаллы могут иметь различную форму: если она сферическая, то они называются зернами, если она сложная, древовидная, то они называются дендритами. По фазовому составу – это твёрдые растворы;
– между зернами и дендритами существуют границы раздела, в которых кристаллическая решётка идеального кристалла искажена; эти границы представляют собой несовершенства поверхностные;
– внутри зерен и дендритов кристаллическая решётка также формируется неидеальной, в ней присутствуют даже посторонние плоскости, края которых являются линейными несовершенствами, их называют дислокации;
– кроме дополнительных плоскостей, в кристаллической решётке реального металла между основными узлами решётки могут находиться посторонние атомы (междуузельные), а часть узлов может быть не занята атомами, быть вакантными. Междуузельные атомы и вакансии являются точечными несовершенствамикристаллической структуры.
Таким образом, зерна, дендриты, несовершенства кристаллической решётки являются объектами структуры реального сплава, его структурными составляющими.Кним также относятся частицы промежуточных фаз. Эти объекты периодически повторяются во всех частях материала – слитка, деформированного полуфабриката, заготовки, детали, изделия.
В зависимости от основного объекта структуры, она может носить различные названия: если объект – дендрит, то это дендритная структура (рис. 2.6), если объект – зерно, то это зёренная структура, а если объект – дислокация, то это дислокационная структура.
Рис. 2.6. Схема дендритного строения слитка
В зависимости от технологической операции, в результате которой получена та или иная структура, её называют: литой, деформированной, рекристаллизованной, отожжённойили иной.
В связи с тем, что эти объекты структуры имеют различные размеры, существует иерархия структурной организации материала:
– макроуровень – размеры структурных составляющих находятся в пределах 10-3 - 10-1 м; изучаемая структура называется макроструктурой.
– микроуровень – размеры структурных составляющих находятся в пределах 10-4 - 10-7 м, изучаемая структура называется микроструктурой.
– субмикро - или наноуровень – размеры структурных составляющих находятся в пределах 10-7 - 10-9 м; изучаемая структура называется тонкой структурой и наноструктурой соответственно.
Прямое наблюдение и идентификацию структуры (ее визуализацию) проводят при помощи микроскопического (металлографического) анализа, при котором используются специальные приборы – микроскопы.
На различных уровнях структурной организации в сплавах возможно наблюдение следующих составляющих:
![]() | ![]() |
![]() | ![]() |
Рис. 2.7. Дендриты (а), кристаллиты (б); зерна в литом сплаве(в); световая микроскопия: а – увеличение х200; б – х100, в – х 500; г – х 50;
Г – волокна (макроструктура)
1) на макроуровне (визуально или при небольшом увеличении) наблюдают дендриты, волокна, размер которых, внутри границ, которыми они образованы, составляет от нескольких десятков микрометров до нескольких сантиметров (рис. 2.7, а, г);
2) на микроуровне (световая микроскопия) наблюдают зёрна, субзёрна, частицы промежуточных фаз, размеры которых существенно меньше, чем объекты п.1; частицы фаз в большинстве сплавов располагаются внутри зёрен;
3) на микроуровне (провечивающая электронная микроскопия) наблюдают дислокации, дефекты упаковки, размеры которых составляют от нескольких нанометров до десятков нанометров; они располагаются как внутри твёрдых растворов, так и внутри промежуточных фаз;
Дендриты являютсяобъектами структуры литого сплава, они образуются при кристаллизации; имеют различные форму и структуру в зависимости от условий затвердевания (рис. 2.6 и 2.7, а.)
После того, как дендриты, вырастая одновременно в слитке сталкиваются друг с другом, между ними образуется граница, и такие частицы уже носят название кристаллиты (рис. 2.7, б).
При деформировании слитка дендриты и кристаллиты претерпевают изменения, они вытягиваются вдоль направления деформации. При макроанализе такого полуфабриката выявляются вытянутые образования – так называемые волокна (рис. 2.7, г).
При исследовании волокон с большим увеличением внутри них различимы вытянутые вдоль направления деформации зёрна.
Зерно – часть сплава, однородная по ориентации кристаллической решётки в пространстве, отделенная поверхностью раздела, от другого зерна. Зёрна представляют собой фактически монокристаллы, различным образом ориентированные в пространстве металлического объекта (полуфабрикат, деталь, изделие), разделённые границами (рис. 2.6), а сплав – это конгломерат монокристаллов. Такой сплав называют поликристаллическим. Сплавы однофазные состоят из зёрен твёрдого раствора.
Зерна образуются на различных этапах производства деталей: при кристаллизации; при горячей деформации;при отжиге после холодной пластической деформации;при термической обработке.
Из разноориентированных зёрен состоят все промышленные сплавы, получаемые по традиционной технологии (выплавка→ разливка→ деформация → обработка → (в т.ч. и термическая).
Зёренная структура сплава характеризуются следующими параметрами: размером и формой. Размер зерна – это количественная характеристика зеренной структуры. Он находится в пределах 2,7 - 250 мкм (средний диаметр). Размер зерна при металлографическом анализе оценивается в баллах (при увеличении в 100 раз) посредством сравнения наблюдаемой структуры с эталонной, которая состоит из 14 баллов. Балл указывает на количество зёрен в квадратном миллиметре шлифа; поэтому, чем выше балл, тем меньше размер зерна (ГОСТ 5639-78).
Качественно сплавы и стали обычно подразделяют на крупнозернистые (балл зерна 1 - 6) и мелкозернистые (балл зерна 7 - 14).
Рис. 2.8.Ориентированная в направлении деформации (а) и равноосная (б) зёренная структура
Форма зерна может быть оценена качественно (равноосная, вытянутая - ориентированная) (рис. 2.8). Для оценки анизотропии формы ориентированных зёрен используют количественную характеристику – так называемый «форм-фактор»: коэффициент формы зерна (отношение длины зерна к его ширине, l з / d з ).
Микроструктура многофазных сплавов включает твёрдый раствор и промежуточные фазы (ПФ). Частицы микронных размеров визуализируются при помощи оптической электронной микроскопии; частицы размером в сотни и десятки нанометров – при помощи электронной микроскопии.
Гранулы – частица или нераздельный конгломерат частиц диаметром 1 - 10 мм.Гранулы получают при высоких скоростях охлаждения (103 – 105 К/с), когда расплав распыляется струей инертного газа или центробежным разбрызгиванием. При производстве гранул распыление расплава представляет собой один из способов перевода его в слиток, хотя размеры «слитка» (гранулы) чрезвычайно малы.
Порошки – продукт порошковой металлургии, которая включает получение порошков, их переработку и превращение в изделие. Порошки (размером 50 - 200 мкм) получают при более высоких скоростях охлаждения, чем гранулы ( 105 - 106 К/с), которые достигаются как при распылении расплава, так и при распылении вращающегося расходуемого электрода в инертном газе или вакууме. В порошковой металлургии монолитные полуфабрикаты из порошков и гранул получают путём их смешивания, компактирования, спекания и последующей деформации.
Дата добавления: 2020-01-07; просмотров: 207; Мы поможем в написании вашей работы! |
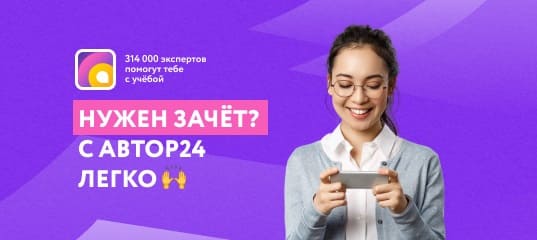
Мы поможем в написании ваших работ!