Выполнение работы и оформление результатов
1. Ознакомиться с сущностью объемной штамповки в открытых штампах, характером течения металла в открытом ручье штамповки и ролью облоя в его заполнении.
![]() |
Рис. 5. Схемы устройства штампов:
1 – пуансон; 2 – матрица
Занести схему использования открытого штампа и поэтапного заполнения его полости металлом в отчет.
2. Ознакомиться с сущностью объемной штамповки в закрытых штампах. Занести схему закрытого штампа в отчет.
3. Ознакомиться с основными операциями холодной листовой штамповки и занести схемы их выполнения в отчет.
4. Ознакомиться с конструкцией заданного штампа для холодной листовой штамповки, определить функциональное назначение его деталей и тип, определить рабочие размеры штампа.
5. Ознакомиться с устройством и принципом действия паровоздушного штамповочного молота, занести в отчет его схему, составить техническую характеристику молота.
6. Ознакомиться с устройством и принципом действия кривошипного листоштамповочного пресса, занести его схему в отчет, составить и занести в отчет техническую характеристику пресса.
Контрольные вопросы
1.
![]() |
В чем состоит сущность разделения операции штамповки на горячую и холодную?
Рис. 6 Технологические переходы штамповки сепаратора:
1 - вырубка и вытяжка; 2 - пробивка дна; 3 - отбортовка;
4 - обрезка припуска первого фланца; 5 - отбортовка под углом 45°;
|
|
6 - отбортовка под углом 90°; 7 - обрезка припуска второго
фланца; 8 – пробивка отверстий
2. Каково конструктивное различие открытого и закрытого штампов?
3. Каким требованиям должен отвечать материал штампов для горячей и холодной штамповки?
4. Перечислите оборудование, применяемое для горячей объемной штамповки.
5. Охарактеризуйте технологические переходы горячей объемной штамповки.
6. Какие заготовки сварочного производства изготавливают холодной листовой штамповкой (приведите примеры)?
7. Охарактеризуйте технологические переходы холодной листовой штамповки.
8. Как классифицируются штампы для холодной листовой штамповки?
ЛАБОРАТОРНАЯ РАБОТА 3
ИЗУЧЕНИЕ МЕТОДОВ ОБРАБОТКИ МАТЕРИАЛОВ
РЕЗАНИЕМ И ПРИМЕНЯЕМОГО РЕЖУЩЕГО
ИНСТРУМЕНТА
Задание
1. Изучить основные способы обработки заготовок резанием - точение, сверление, растачивание, строгание, фрезерование, шлифование.
2. Изучить классификацию металлорежущих станков и выяснить характерные отличия станков различных групп.
3. Изучить основные принципы обработки заготовок на токарных, сверлильных и фрезерных станках (установка и фиксация заготовок, движения резания, виды обрабатываемых деталей и поверхностей).
|
|
Цель работы: закрепить теоретические знания, полученные на лекциях и в процессе самостоятельного изучения технологии обработки материалов резанием.
Оборудование, инструмент и образцы
Токарный станок.
Фрезерный станок.
Вертикально-сверлильный станок.
Основные виды режущего инструмента: токарные резцы, сверла, зенкеры, развертки, фрезы цилиндрические, торцевые и др.
Общие сведения об обработке заготовок резанием
Механическая обработка поверхностей заготовок резанием является одной из основных завершающих стадий изготовления деталей машин, сварных конструкций, а также при подготовке заготовок под сварку. Для этого используют режущий инструмент, имеющий хотя бы одну острую кромку (режущее лезвие), благодаря чему появляется возможность отделять от заготовки меньшую часть материала, превращая ее в стружку, а из оставшейся части получать требуемую деталь. Способы обработки резанием различают по видам применяемого режущего инструмента и металлорежущих станков. Основными видами режущих инструментов являются резцы, зенкеры, сверла, развертки, фрезы, протяжки и др.
|
|
Токарная обработка. Различают обработку: обдирочную; черновую; получистовую; тонкую.
Обдирку применяют для поковок и крупных отливок. Обдиркой уменьшают пространственные отклонения и погрешности формы черновой заготовки. При обдирке могут быть выдержаны размеры: для поковок - по 16…17 квалитету точности, для отливок - по 15…16.
Черновую обработку применяют для: заготовок, подвергавшихся обдирке; крупных штампованных поковок П класса точности; крупных отливок.
Получистовую обработку применяют, если при черновой обработке не может быть удален весь припуск или предъявляются повышенные требования к точности геометрических форм обрабатываемой заготовки и пространственным отклонениям ее элементов. Обработка обеспечивает 11…16 квалитеты точности.
Чистовуюобработку применяют как окончательную или промежуточную под последующую отделку. Обеспечивает 9…11 квалитеты точности.
Однократную чистовую обработку применяют для: точных; полученных литьем в кокиль, по выплавляемым моделям; точной штамповкой и др.
Однократная обработка обеспечивает 11…14 квалитеты точности.
Тонкая обработка резцами является методом окончательной отделки и заменяет шлифование. Обеспечивает 7…9 квалитеты точности.
|
|
Фрезерование. Различают черновое, получистовое и чистовое фрезерование, а при обработке торцовыми фрезами - и тонкое фрезерование.
Черновое фрезерование применяют для предварительной обработки отливок и поковок с припуском свыше 3 мм. Обеспечивает отклонение от прямолинейности 0,15…0,3 мм на длине 1 м.
Получистовое фрезерование обеспечивает отклонение от плоскостности 0,1…0,2 мм на длине 1м.
Чистовое фрезерование применяют как окончательную обработку после чернового и получистового фрезерования перед последующей отделочной обработкой. Отклонение от плоскостности 0,04…0,08 мм на 1 м длины.
Тонкое фрезерование (торцовыми фрезами) применяют в качестве окончательной обработки плоскостей с припуском 0,2…0,5 мм. Отклонение от плоскостности 0,02…0,04 мм на длине 1 м.
Однократное фрезерование применяют, когда погрешность черной заготовки обуславливают припуск на обработку менее 2 мм. Отклонение от плоскостности 0,06-0,1 мм на 1 м длины.
Сверление. Спиральными сверлами получают отверстия в сплошном металле диаметром до 80 мм. Применяют в качестве предварительной обработки точных отверстий. Для грубых отверстий часто ограничиваются одним сверлением. При сверлении отверстий диаметром более 30 мм сначала сверлят отверстия меньшего диаметра (одна треть заданного), а затем производят его рассверливание.
Зенкерование. Черновое зенкерование применяют для обработки литых или прошитых отверстий диаметром до 100…120 мм в черновых заготовках, чистовое - для обработки просверленных или предварительно расточенных отверстий. Повышает точность формы исходного отверстия, при использовании кондукторной втулки выправляет увод и смещение оси отверстия. При (черновом) зенкеровании литых и прошитых отверстий в черных заготовках получают 12…13 квалитеты точности, при чистовом (после сверления или чернового зенкерования) - 11 квалитет.
Однократное скоростное с охлаждением зенкерование литых отверстий в заготовках из черного чугуна обеспечивает 11 квалитет точности.
Развертывание. Применяют для окончательной обработки отверстий диаметром до 100…120 мм или перед их последующим хонингованием, тонким растачиванием, притиркой. Не исправляет увода и смещения оси отверстия и применяется для получения точного диаметрального размера. Развертыванию предшествуют сверление, чистовое зенкерование и чистовое растачивание. Применяется предварительное (9…10 квалитет точности), чистовое (8-й квалитет точности) и тонкое (6…7 квалитет точности) развертывания.
Протягивание. Применяют для обработки сквозных отверстий и пазов любого сечения, плоских, криволинейных поверхностей и наружных поверхностей вращения. Позволяет упростить обработку в массовом производстве, одна протяжка заменяет комплект инструментов (например, зенкер или расточной резец и развертку; черновую и чистовую фрезы и т.п.). Обеспечивает 8…10 квалитеты точности.
Прошивание. Применяют для окончательной обработки отверстий любой формы небольшой длины. Обеспечивает 7-й квалитет точности.
Шлифование. Обдирочное шлифование как метод однократной обработки применяют при обработке плоских базовых поверхностей для обеспечения необходимой плоскостности, обычно без выдерживания размера. При обдирочном шлифовании применяют сегментные круги зернистостью 80…125, иногда 50…80, достигается шероховатость поверхности Ra 2,5.
Предварительное шлифование плоских поверхностей после обработки лезвийным инструментом проводят периферией круга зернистостью 40…50 или торцов чашечного круга зернистостью 50…80. Для чистового шлифования применяют круги зернистостью 12…40 и для тонкого - 6…10.
Для обработки наружных поверхностей вращения применяют предварительное (9…10 квалитеты точности); чистовое (7…8 квалитеты точности); тонкое шлифование (5…6 квалитеты точности).
Однократное круговое наружное шлифование применяют для заготовок, не подвергающихся термической обработке после точения для достижения 9…10 квалитетов точности.
Для обработки отверстий применяют предварительное (9…10 квалитеты точности), чистовое и однократное шлифование (7…9 квалитеты точности).
При изготовлении точных и ответственных деталей машин широко применяют отделочные методы обработки: хонингование; суперфиниш; притирку; обработку поверхностным пластическим деформированием и др.
Для осуществления процессов обработки резанием режущему инструменту и заготовке сообщают движение резания, подразделяемые на главное движение и движение подач. Главное движение всегда одно, движений подачи может быть несколько [1-3].
В основу классификации металлорежущих станков положен технологический метод обработки заготовок по следующим признакам: вид режущего инструмента; характер обрабатываемых поверхностей; схема обработки.
Станки делят на токарные, сверлильные, шлифовальные, фрезерные, строгальные, протяжные и др.
Резание металлов - сложный процесс взаимодействия режущего инструмента и заготовки, сопровождающийся рядом физических явлений - деформированием срезаемого слоя, обрабатываемой заготовки и режущего инструмента; наростообразованием на режущем инструменте; упрочнением (наклепом) поверхностного слоя заготовки; значительным теплообразованием; трением между инструментом, заготовкой и стружкой; возникновением вибраций и пр. Поэтому важное значение имеет выбор оптимальных геометрических параметров инструмента и режимов резания [1-3].
Дата добавления: 2020-01-07; просмотров: 213; Мы поможем в написании вашей работы! |
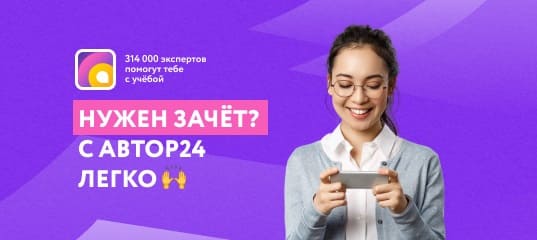
Мы поможем в написании ваших работ!