РАСЧЕТ СЕБЕСТОИМОСТИ ГИДРИРОВАНИЯ ВЫСОКОНЕОДИМОВЫХ СПЛАВОВ Nd-Fe
В данном разделе проводится оценка себестоимости получения порошков гидридов высоконеодимовых сплавов Nd-Fe. Исходные данные приведены в таблице 13.
Таблица 13 – Исходные данные
Наименование | Значение |
Производительность основного аппарата по готовой продукции, тонн/год | 50 |
Предполагаемая продолжительность инвестиционного проекта, год – Разработка проекта – Оборудование помещения – Эксплуатация, год | 6 0,5 0,5 5 |
Стоимость сырья: – лигатура Nd-Fe, руб/кг – водород, руб/м3 – аргон, руб/м3 − сорбент NaF, руб/кг | 300 0 8,1 133 |
Стоимость энергоресурсов: Электроэнергия, руб/кВт×ч | 1,20 |
Ставка ЕСН, % | 26 |
Ставка налога на прибыль, % | 24 |
Расчёт производился по основному аппарату – реактору гидрирования-дегидрирования. Производственная мощность отделения определялась максимально возможным выпуском продукции при наиболее полном использовании оборудования и производственных площадей. При расчётах учитывалось все оборудование (как действующее, так и бездействующее, из-за ремонта, неисправности и т.д.) за исключением резервного.
Суммарная стоимость оборудования, включающего два реактора, водородную и аргоновую рампы, систему дожига, систему контроля и регулирования процесса гидрирования, систему вентиляции, вакуумный пост составляет 802,23 тыс. руб.
Для размещения установки необходимо помещение площадью 30 м2 и высотой 2,5 м. Объем производственных помещений — Vп = 30×2,5 = 75 м3.
|
|
Фонд заработной платы РСС рассчитывали, исходя из действующих тарифных условий, запроектированной численности основных и вспомогательных рабочих и их фонда рабочего времени.
Определение затрат на сырье и материалы производили, исходя из принятого объема производства (Q = 50 т/год), удельных норм расхода сырья и материалов, установленных по материальному балансу и планово-заготовительных цен.
За единицу продукции принято количество продукции, полученное за 1 час рабочего времени.
В качестве приобретаемого сырья выступает водород и гелий (или аргон).
Проектная калькуляция затрат на производство приведена в таблице 14, которая сводится к расчету валовых затрат для переработки 50 тонн лигатуры в год, а исходные данные для калькуляции приведены в приложении В.
Таблица 14 - Проектная калькуляция затрат на проведение операции гидрирования
Статьи калькуляции | Затраты на годовой выпуск продукции, тыс. руб. | Затраты на единицу продукции, руб. |
1 | 2 | 3 |
1 Переменные затраты | ||
а) химическое сырье | 15177 | 302 |
б) энергия на технологические цели | 72,5 | 1,5 |
в) ЗП производственных рабочих | 586 | 11 |
г) ЕСН (26% от п. 1в) | 152,5 | 3 |
Итого переменных затрат: | 15989 | 319 |
Продолжение таблицы 14
|
|
1 | 2 | 3 |
2 Постоянные затраты а) цеховые расходы; б) расходы на содержание и эксплуатацию оборудования; в) общезаводские расходы (10 % от п.1в - 1г); г) внепроизводственные расходы (2 % от п.1а - 2б) | ||
190 | 3,8 | |
202 | 5 | |
74 | 1,5 | |
329 | 6,6 | |
Итого постоянных затрат: | 869 | 17,5 |
Итого валовые затраты: | 16858,1 | 336 |
Итого себестоимость операции гидрирования (валовые затраты минус стоимость исходного сырья) | 34 руб./кг |
Таким образом, в результате проведенной экономической оценки стоимости операции измельчения РЗМ-содержащих лигатур было установлено, что даже при условии изготовления нестандартного оборудования, и затрат, связанных с переоборудованием помещений под работу с водородом. Стоимость гидрирования килограмма лигатуры для ТФЛ составит 34 руб. (таблица 14). Эта сумма несравнима с затратами на повторную переплавку и коррекцию некондиционных сплавов, а также с увеличением стоимости магнитов, изготовленных из стандартных сплавов Nd-Fe-B с улучшенными, благодаря ТФЛ, свойствами.
ВЫВОДЫ
|
|
Опробован в лабораторных и опытно промышленных условиях метод твердофазного легирования магнитных сплавов порошками гидридов для улучшения свойств получаемых из них магнитов на основе Nd-Fe-B.
Проведенный литературный анализ рынка и технологий производства магнитных материалов показал, что рост производства магнитных материалов в мире составляет более 1500 тонн в год. При этом, как у российских, так и у зарубежных производителей имеет место определенный процент некондиции в виде магнитных сплавов с нарушением химического состава, магнитов с низкими магнитными характеристиками и т.д. Количество такого материала (имеются в виду материалы на основе Nd-Fe-B) по оценкам автора составляет в разных случаях от 5 до 15 % от выпуска готовой продукции. Состав таких материалов может быть скорректирован твердофазным легированием порошками гидридов высоконеодимовых сплавов, что дешевле, чем повторный переплав.
В настоящей работе предложен и исследован способ получения порошков гидридов высоконеодимовых лигатур для использования их в технологии получения магнитных материалов.
Предложенный способ измельчения высоконеодимовой лигатуры Nd-Fe, позволяет получать химически достаточно устойчивые порошки гидридов, пригодные для твердофазного легирования некондиционных магнитных сплавов. Способ включает получение лигатур любым известным способом, гидрирование при комнатной температуре и давлении 0,2-0,3 МПа, усреднение и герметичную упаковку полученных порошков.
|
|
Проведенный термодинамический анализ процесса гидрирования высоконеодимовых сплавов показал, что процесс гидрирования вероятен при температурах до 875 К, а увеличение давления водорода ведет к смещению равновесия в сторону образования гидридов. В целом же термодинамика процесса гидрирования РЗМ-содержащих магнитных сплавов (в том числе магнитных Nd-Fe-B) достаточно хорошо освящена в литературе и гидрирование высоконеодимовых лигатур будет подчиняться тем же закономерностям. Исследование кинетических параметров гидрирования высоконеодимовых лигатур напротив показало, что процесс гидрирования лигатур протекает по межфазовым, богатым РЗМ границам, не затрагивая зерен Fe-РЗМ. Процесс гидрирования с высокой достоверностью (коэффициент корреляции 0,98-0,99) описывается уравнением сокращающейся сферы 1-(1-α)1/3 = (0,18±0,01)е-5000/RT×τ. Кажущаяся энергия активации процесса составила 5 кДж/моль.
Было установлено, что:
- скорость гидрирования лигатуры увеличивается при возрастании давления водорода;
- температура в диапазоне 25-300оС оказывает влияние преимущественно на продолжительность индукционного периода;
- избыток водорода неоднозначно влияет на степень гидрирования, максимум последней наблюдается при 100%-ном избытке водорода;
- в состав получаемых гидридов (по данным РФА) входят преимущественно следующие кристаллические фазы - Nd2Fe14H2,5, Nd2H5;
- увеличение массы навески (сотни грамм – килограммы) приводит к возрастанию скорости гидрирования и исчезновению индукционного периода;
Исследование коррозионной активности порошков гидридов показало, что порошки гидридов химически достаточно устойчивые соединения и работать с ними можно на открытом воздухе в условиях сухого помещения. Однако при длительном хранении во влажной атмосфере происходит частичное окисление гидридов до Nd(OH)3, по реакции:
NdH3 + 3H2O = Nd(OH)3+ 3H2.
Хранить порошки гидридов следует в сухой, изолированной или инертной атмосфере, или в герметичной таре в воздушной атмосфере, или в атмосфере водорода.
Опытно-промышленные испытания предлагаемого метода измельчения показали возможность получения порошков гидридов в промышленных условиях и использования их в дальнейшем для коррекции свойств некондиционных магнитов методом твердофазного легирования.
Установлены оптимальные условия получения порошков гидридов лигатуры: давление 1,5-3 атмосферы, температура 25-50оС, средний размер кусков лигатуры 15-25 мм;
Полученные в опытно-промышленных условиях порошки гидридов (30 кг) были использованы для получения магнитов методом ТФЛ. Установлено, что твердофазное легирование порошками гидридов высоконеодимовых сплавов Nd (75%) Fe (25 %) магнитных сплавов (в том числе и некондиционных) позволяет значительно поднять характеристики, изготовленных из них по штатной технологии магнитов. Так, серийные магниты, изготовленные из тройных сплавов с содержанием неодима до 33 – 34 % мас., полученные по внепечной фторидной технологи, имели относительно низкую коэрцитивную силу и значения остаточной магнитной индукции на уровне 1,08-1,10 Тл. Тогда как свойства магнитов полученных твердофазным легированием аналогичных магнитных сплавов с добавками до стехиометрического состава порошков гидридов высоконеодимовых сплавов Nd-Fe значительно повысились и находились в пределах: коэрцитивная сила 7,0 – 9,0 кЭ, магнитная индукция - 1,25 – 1,32 Тл.
Проведенный экономический анализ показал возможность создания производства порошков гидридов лигатур непосредственно на магнитном участке ХМЗ СХК. Себестоимость операции гидрирования (без стоимости лигатуры) не будет превышать 34 руб/кг. Поэтому, создание такого передела и внедрение гидрирования в магнитное производство является достаточно выгодным вариантом не только для исправления и корректировки химического состава некондиционных магнитных сплавов, но и для создания принципиально новой технологии ТФЛ для получения магнитов с улучшенными магнитными характеристиками.
* * *
В заключении выражаю глубокую благодарность за постановку задач исследований по данной теме, научному сопровождению выполнения исследований и помощь в обсуждении результатов работы моему научному руководителю – доценту, к.т.н. Макасееву А.Ю. (СГТА, г. Северск). Выражаю искреннюю признательность за участие и помощь в обсуждении результатов работы – профессору кафедры ХиТМСЭ, д.т.н. Буйновскому А.С. и профессору кафедры МАХП, д.т.н. Софронову В.Л. За оказание помощи в проведении исследовательских работ – Генеральному директору ООО "ПОЗ-ПРОГРЕСС" г. Верхняя Пышма Свердловской области к.ф.м.н. Москалёву В.Н. Выражаю признательность д.х.н. Полубоярову В.А. (ИХТТиМХ СО РАН, г. Новосибирск) за предоставленную возможность в проведении рентгеноструктурных и микроскопических исследований, а также за своевременные квалифицированные консультации.
Благодарю руководство Химико-металлургического завода ФГУП СХК в лице главного инженера Скрипникова В.В. и зам. главного инженера Шадрина Г.Г., а также коллектив магнитного участка 3-го цеха за понимание и оказанную помощь при проведении экспериментов.
Выражаю искреннюю благодарность всем сотрудникам кафедры ХиТМСЭ СГТА (г.Северск) за сотрудничество и моральную поддержку при подготовке и выполнении научно–исследовательской работы.
СПИСОК ЛИТЕРАТУРЫ
1. Trout S.R., Rare earth magnet industry in the USA: current status and future trends. XVII Rare Earth magnet workshop, august 18-22, Newark, DE, USA, 2002.
2. Masato Sagawa, 20 YEARS OF NdFeB. Proceedings of the 18th International Workshop on High Performance Magnets and their Applications, HPMA-04, Annecy (France) 29 August - 2 September 2004.
3. Цыганкова Г.В., Пасечник О.Ю., Смирнова Н.Н. Анализ зарубежного опыта производства и использования высокочистых редкоземельных и тугоплавких редких металлов // Высокочистые вещества.–1991. N2. – С. 43-61.
4. Цыганкова Г.В. Переработка сырья и производство основных видов редкометаллической продукции // Обз. информация. ЦНИИ цветмет. экономики и информации. – 1988. № 3. – С. 1-66.
5. Елютин А.В., Пасечник О.Ю., Цыганкова Г.В. Требования к чистоте и качеству редкоземельных металлов и сплавов с магнитными и магнитострикционными свойствами // Высокочистые вещества. – 1991. №3. – С. 7-13.
6. Тулупов И.Ф. Постоянные магниты // Обз. информация по зарубежным материалам. ЦНИИ патентной информации, ТЭИ и Госкомитет по делам изобретений и открытий. – М.: 1977. – С. 1-48.
7. Обухова В.Ю. Магнитотвердые материалы Nd-Fe-B. Химический состав, легирующие добавки и заменители // Реферативный обзор НПО "Магнетон". – Владимир: 1989. – 112 с.
8. Обухова В.Ю. Современный уровень производства постоянных магнитов Fe-Nd-B // Аналитическая справка. НПО "Магнетон". – Владимир: 1989. – 91 с.
9. Шульгач Н.И. Современный уровень производства и перспективы развития постоянных магнитов // Аналитический обзор. НПО "Магнетон". – Владимир: 1992. – 216 с.
10. Nard W.G. The Present Status and Future Cutlook for Nd-Fe-B mаgnets in the U.S. // Proc. of the 3 Jnt. Conf. and Exibition in the Jmpact of Nd-Fe-B Materials on Magnet Producers. San Diego. Calif. USA., 1991. – 300 p.
11. Шереметьевский Н.М., Стома С.А., Сергеев В.В. Высокоэнергетические постоянные магниты в электромеханике // Электротехника. – 1989. № 11. – С.2-9.
12. Rare earth metalls. Jnd Rare Metals., 1988. № 95. – Р. 62-63.
13. Сергеев В.В., Кононенко В.С. Анализ тенденций в развитии и потреблении постоянных магнитов. Разработка рекомендаций по выбору номенклатуры магнитов, сплавов и способов их получения // Обзор ВНИИЭМ. – М.: 1992. – 40 с.
14. Sagawa M. New materials for permanent magnets on the base of Nd-Fe // J. Appr. Phys. – 1983. – V 55, № 6. – Р. 2083-2087.
15. Hadjipanayis G., Hagelton R. Permanent magnet materials // Appe. Phys. Lett.– 1983. – V 43, № 8. – Р.797-799.
16. Пат. 47-50489 Япония, МКИ 55 0 С22С 1/02. Способ получения постоянных магнитов. – 1972.
17. Пат. 3652343 США, МКИ5 С22С 1/02. Способ получения постоянных магнитов. – 1972.
18. Сергеев В.В., Кононенко В.С. Анализ тенденций в развитии и потреблении постоянных магнитов. Разработка рекомендаций по выбору номенклатуры магнитов, сплавов и способов их получения // Обзор ВНИИЭМ. – М.: 1992. – 40 с.
19. G.W Jewell. High performance electrical machines proceedings of the 18th International Workshop on High Performance Magnets and their Applications, HPMA'04, Annecy (France) 29 August - 2 September 2004.
20. Информационный бюллетень конференции по постоянным магнитам на основе Nd-Fe-B. – Сан-Франциско.: 1999. – 4 с.
21. William G. Hart the global permanent magnet industry 1993 to 2000 // XI. Всес. конф. по пост. магнитам. Суздаль: 10-14 октября 1994. Тез. докл. – М.: 1994. – С. 4.
22. Tourre J.M. // 13 the Jut. Workshop on RE magnets and Their Appl., 1994. – P. 381-390.
23. "Magnetocaloric effect and magnetic refrigeration," V. K. Pecharsky and K. A. Gschneidner, Jr., Journal of Magnetism and Magnetic Materials, Vol. 200, 44 (October 1999)
24. Соколова Т.Л., Соколов А.А. Перспективы применения быстрозакаленных магнитотвердых сплавов системы Nd-Fe-B в промышленности. Проблемы теории и практики в инженерных исследованиях.: Тр. 33-й научной конф. Рос. ун-та дружбы народов (РУДН) – М.: 1997. – С. 261-262.
25. Сергеев В.В., Кононенко В.С. Анализ тенденций в развитии и потреблении постоянных магнитов. Разработка рекомендаций по выбору номенклатуры магнитов, сплавов и способов их получения // Обзор ВНИИЭМ. – М.: 1992. – 40 с.
26. Robbins J. Permanent Magnets. Material Edge, 1987. – Р.17-31.
27. Hadfield D. The Present Statusand Puture Outlook for Nd-Fe-B Magnets in Europe // Proc. of the 3 Intern.Conf. 18-26 Осt. 1987. San Diego, 1987. – Р. 5-49.
28. Шульгач Н.И. Новые тенденции в производстве постоянных магнитов и их применении // XI Всес. конф. по пост. магнитам. Суздаль: 10-14.X.1994. Тез. докл. – М.: 1994. – С. 7-9.
29. Шульгач Н.И. Современный уровень производства и перспективы развития постоянных магнитов // Аналитический обзор. Фонд АО "Магнeтон". – Владимир, 1993. – 217 с.
30. Шульгач Н.И. Последние достижения в производстве магнитотвердых материалов. Новые тенденции в применении постоянных магнитов и магнитных систем // Аналитический обзор. Фонд АО "Магнетон". – Владимир, 1994. – 75 с.
31. Tourre J.M. Rare Earths, 1994 "The Raw Deal" // 13th Int. Workshop on RE Magnets and their Appl., 1994. – P. 381-390.
32. Nagel H. and Krounert W.A Techno-Economic Analysisof Nd-Fe-B Processing / /13th Int. Workshop on RE Magnets and their Appl., 1994. – P. 391-396.
33. Luo Y. The Place of the Chinese Nd-Fe-B Magnets Industry in the World // 13th Int. Workshop on RE Magnetsandtheir Appl., 994. – P. 608-620.
34. Hard W.G. Trends and Structure of Bonded Magnets / Докл. XIII Межд. конф. по пост. Магнитам. Суздаль: 24-28.10.2000. – М.: 2000. – 22 с.
35. Кононенко А.С. Технико-экономическое обоснование развития производства магнитов Nd-Fe-B. – M.: ВНИИЭМ, 1990. – 119 с.
36. Тарасов Е.Н., Башков Ю.Ф., Миляев О.А. и др. Разработка магнитотвердых порошков для магнитопластов // XI Всес. конф. по пост. магнитам. Суздаль: 10-14.X.1994. Тез. докл. – М.: 1994. – С. 94.
37. Сеин В.А., Немчикова Т.В., Сафронов Б.В. МТМ на основе БЗС Fe-Nd-B // XI Всес. конф. по пост. магнитам. Суздаль: 10-14.X.1994. Тез. докл. – М.: 1994. – С. 104.
38. Глебов В.А., Кучумов В.А., Шингарев Э.Н. и др. Методика сертификации магнитных сплавов системы Nd-Fe-B // XI Всес. конф. по пост. магнитам. Суздаль:10-14.X.1994.Тез. докл. – М.: 1994. – С.109.
39. William G. Hart The global permanent magnet industry 1993 to 2003 // XI Всес. конф. по пост. магнитам. Суздаль: 10-14.X.1994. Тез. докл. – М.: 1994. – С.4.
40. Софронов В.Л., Макасеев Ю.Н., Буйновский П.А. и др. Разработка технологии изготовления кольцевых магнитов с радиальным намагничиванием // XI Всес. конф. по пост. магнитам. Суздаль: 10-14.X.1994. Тез. докл. – М.: 1994. – С.80.
41. Софронов В.Л., Кондаков В.М., Кобзарь Ю.Ф. и др. Фторидная технология получения магнитных материалов и магнитов на основе Nd-Fe-B // XI Всес. конф. по пост. магнитам. Суздаль: 10-14.X.1994. Тез. докл. – М.: 1994. – С.81.
42. Софронов В.Л., Анисимов Л.Д., Буйновский П.А. и др. Исследование магнитных свойств магнитов, полученных по фторидной технологии // XI Всес. конф. по пост. магнитам. Суздаль: 10-14.X.1994. Тез. докл. – М.: 1994. – С.82-83.
43. Сергеев В.В. Магнитотвердые материалы. – М.: Энергия, 1980. – 190 с.
44. Кекало И.Б., Самарин Б.А. Физическое металловедение прецизионных сплавов, сплавы с особыми магнитными свойствами. – М.: Металлургия, 1989. – 496 с.
45. Yang LKO Rare Earth Permanents Magnets in China: Production and Raw Materials. Beijing. Конференция по магнитам на основе Nd-Fe-B. Сан-Франциско: 1998. – 15 с.
46. Hard W.G. The Present status and Future Outlook for Nd-Fe-B magnets in the U.S. // Proc. of the 3 Intern Conf. and Exhibition in the Impact of Nd-Fe-B Materials on Magnet Producers. San Diogo. Galif. USA, Oсt. 1987. – Р. 18-20.
47. Башкевич В.В. Изучение процессов плавки магнитных сплавов в плазменно-индукционной печи // Тез. докл. 55-й НТ конф. – Белорусский техн. инст. – Минск, 1990. – С. 105-106.
48. Tang N. Magnetic Properties of Nd-Fe-Co-B-V // The Proc. of the XI Intern. Workshop on Rare Earth Magnets. Pennsylvania, USA, 21-24.X.1990. V1.– P. 408-417.
49. Пат. 294974 ФРГ, МКИ5 С22С 1/02. Способ приготовления сплавов. – 1992.
50. Пат. 5014769 США, МКИ5 B22G 23/00 В 22 G 45/00. Способ бестигельной индукционной плавки. – 1992.
51. Пат. 294736 ФРГ, МКИ5 С22С 1/02, С22С 28/00. Способ пирометаллургического производства сплавов РЗМ.-1992.
52. Пат. 62-146290 Япония, МКИ5 С25С 3/34, С25С 3/36. Способ и устройство для получения сплавов Dy-Fe. – 1989.
53. Пат. 4747240 США, МКИ4, C25G 17/00, С25С 3/36. Способ и устройство для получения Nd-Fe сплава. – 1989.
54. Пат. 62-146291 Япония, МКИ4, С25Е 3/34, С25Е 3/36. Способ электролитического получения сплавов РЗМ. – 1989.
55. Пат.3733180 ФРГ, МКИ5 С22С 1/02, 1/03. Способ изготовления сплавов системы Fe-Nd-Dy-B. – 1990. – 1Е283П.
56. Данилов М.А. Исследование процесса кальциетермического получения магнитных сплавов системы Nd-Fe-B // IX Всес. конф. по пост. магнитам – Суздаль, 20-23.1Х.1988.Тез.докл.- М.: Инф-ро, 1988. – С. 50.
57. Растегаев B.C. Создание новых марок РЗМ и лигатур для производства ВЭПМ РЗМ-Fe-B // Х Всес. конф. по пост. магн. Суздаль, 14-18.Х. 1991 Тез.докл. – М.: Инф-ро, 1991. – С. 105-107.
58. Верклов М.М., Косынкин В.Д. и др. Исследования различных вариантов Са-термического метода получения лигатур дидим-Со // Х Всес. конф. по пост. магнитам. Суздаль,14-18.Х.1991. Тез. докл. – М.: Инф-ро, 1991.– С. 107-109.
59. Лебедев Г.А. Совместное карботермическое восстановление сплавов Nd-Fe-В // Х Всес. конф. по постоянным магнитам.- Суздаль, 14-18.X.1991. Тез. докл. - М.: Инф-ро, 1991. – С. 104-105.
60. Chin C.J. The Effect of Nd Amount on the Characteristics of Nd-Fe-B Alloys by Reduction – Diffusion Process // Proc. of the XI Intern. Workshop on Rare Earth Magnets. Pennsylvanis, USA, 21-24.X. 1990. VI. – P. 351-358.
61. Скороваров Д.И., Косынкин В.Д. Извлечение РЗМ из фосфоритов в СССР // E.J. Alloys and comp. – 1992. – V.180. – P. 71-76.
62. Химия и технология редких и рассеянных элементов, ч. II. / Под ред. К.А. Большакова – М.: Высшая школа,1976. – 360 с.
63. Спеддинг Р.Х., РЗМ. – М.: Металлургия, 1965. – 256 с.
64. Пат. 2574434 Франция, МКИ С25С 1/22, 7/00. Электролитический способ производства РЗМ и их сплавов и устройство для его осуществления. – 1987
65. Herget. Metallurgical Ways to Nd-Fe-B alloys.// 8th Intern. Workshop on Raie Earth Magnets and their Appl. – Dayton, Ohio, 1985. – P. 5519-5521.
66. Пат. 62-44501 Япония, МКИ4 B22F 1/00, С22С 1/04. Способ получения порошка сплава, содержащего РЗЭ. – 1988.
67. Пат. 61-106735 Япония, МКИ4 С22С 1/04, 19/07. Способ получения сплава для постоянного магнита. – 1987.
68. Пат. 60-100638 Япония, МКИ4 С22С 1/04, B22F 1/00. Способ получения сплава для постоянного магнита. – 1986.
69. Пат. 60-125338 Япония, МКИ4 С22С 1/04, B22F 1/00 Способ получения сплава для постоянного магнита. – 1986.
70. Пат. 02375587 ЕПВ, МКИ5 С22В 5/04, 59/00, B22F 9/20, HF 1/04. Способ получения сплава РЗМ. – 1988.
71. Исследование процесса получения сплавов Fe-Nd, Fe-Sm, Co-Nd и Co-Sm методом восстановления и диффузии // O. Guojnnetal Mater Trans / SIM, 1990. – 31, N6. – P. 463-470.
72. Влияние замены Nd2O3 на NdF3 или NdCl3 в восстановительно-диффузионном процессе получения порошков Nd-Fe-B // J. Appl. Phys, 1991. № 10. – P. 2-12.
73. Пат. 4769063 США, МКИ4 С22С 1/04. Способ получения РЗМ сплавов. – 1989.
74. Guangfei S. The syntesis of Nd-Fe-B by reduction-diffusion. J.A.P., 1988, V.64 -P.5512-5521.
75. Пат. 2551769 Франция, МКИ3 С22С 28/00, 1/00. С22В 5/04. Сплавы неодима и процесс их получения. – 1986.
76. Пат. 4992096 США, МКИ5 С22С 26/22, С22В 59/00. Металлотермический способ восстановления РЗМ. – 1992.
77. Пат. 60-82628 Япония, МКИ4 С22С 1/02, С22С 28/00. Получение неодимового сплава. –1989.
78. Пат. 8616948 Франция, МКИ С22С 23/06.Способ получения сплавов на основе РЗМ и переходных металлов.-1989.
79. Пат. 4612047 США, МКИ4 С22С 33/00. Металлотермический способ получения редкоземельных сплавов с Fe. – 1987.
80. Исследование процесса и разработка технологии получения магнитных сплавов и лигатур на основе РЗМ Са-термическим восстановлением фторидов металлов. / Отчет о НИР ТПИ-1 и СХК. Руководители: Буйновский А.С., Софронов В.Л., Чижиков B.C. // Инв. N 14/140, Е-75003. – Томск: 1991. – 121 с.
81. Пат. 60-77943 Япония, МКИ5 С22С 1/02, С22С 28/00. Способ получения сплава на основе РЗМ для магнитов. – 1986.
82. Пат. 61-157646 Япония, МКИ3 С22С 1/00, С22В 59/00. Получение сплавов редкоземельных металлов. – 1987.
83. Harris I.R., Hydrogen: its use in the processing of Nd-Fe-B type magnets and in the characterizations of Nd-Fe-B – type alloys and magnets / Proc.of the 11th Intern. Workshop on Rare Earth Magnets and their Appl // Pittsburgh, Ponnsilvania, USA, 1990. V1.– P. 29-48.
84. Пат. 3912554 США, МКИ4 С22С 23/06. Способ получения сплавов на основе РЗМ. – 1975.
85. Moosa I.S. Microstructure and magnetic domains inSintered Nd-Fe-B magnets made by hydrogen decrepitation // J. Less Common Metalls, 1990, 167, № 1. – P. 153-160.
86. Яртысь В.А., Растегаев В.С. Исследования свойств магнитов, изготовленных из сплавов с применением гидридного диспергирования // Электротехника, 1989. № 11. – С. 31-32.
87. Сеин В.А., Немчикова Т.В., Сафронов Б.В. МТМ на основе БЗС Fe-Nd-B // XI Всес. конф. по пост. магнитам. Суздаль: 10-14.X.1994. Тез. докл. – М.: 1994. – С. 104.
88. Кособудский И.Д. Структура, магнитные свойства порошков МТМ типа Nd-Fe-B, Sm-Co, полученных с помощью современных методов дробления и размола // X Всес. конф. по пост. магнитам. Суздаль, 14-18.X.1991. Тез. докл. – М.: Инф-ро, 1991. – С. 110.
89. Кособудский М.Д. Структура и магнитные свойства спеченных магнитов из сплавов Nd-Fe-B в зависимости от некоторых режимов изготовления // Х Всес. конф. по пост. магнитам. Суздаль: 20-23.IX.1988. Тез. докл. – М.: Инф-ро, 1991. – С. 49.
90. Накачава Д. Способ получения магнита из сплава с редкоземельными элементами // Кокай Токке,1989,Т.14.-С.59-63. Опубл. ВИНИТИ 22.02.89 г. Рег. N 6447813.
91. Пат. 63-157829 Япония, МКИ4 С22С 1/02, С22В 59/00. Получение сплавов РЗМ. – 1989.
92. Брехаря Г.П. Влияние термической обработки на структуру и свойства магнитов Nd-Fe-B // Х Всес. конф. по пост. магн. Суздаль, 14-18.X.1991. Тез. докл. – М.: 1991. – С. 34-35.
93. Groat J.J. Pr-Fe and Nd-Fe – based materials are a new class of high-performance permanent magnets // J. Appl. Phys, 1984. V.55, N 6. – P. 2078-2082.
94. Пат. 4881986 США, МКИ 54 0 В22F 3/12. Способ получения сплавов РЗМ. – 1987.
95. Schults L., Wecker J. Hard magnetic properties of Nd-Fe-B formed by mechanical alloying and solid state reaction // Mater. Sci. and Eng., 1988, 99. – P. 127-130.
96. Hozieres J.P. A new process for Fe-Nd-B permanentmagnet preparation // J. de Phusigue, Dec. 1988. 49. – P. 667-668.
97. Верклов М.М., Цветков В.Ю., Мельников С.А. и др. Магниты из сплавов Pr-Fe-B-Co, полученные горячей прокаткой// XI Всес. конф. по пост. магнитам. Суздаль: 10-14.X.1994. Тез. докл. – М.: 1994. – С.90.
98. Савченко А.Г. Способ получения магнитов / Свойства БЗС лент сплавов Nd-Fe-B и способы получения постоянных магнитов на их основе // Обз. Сб. Новости НиТ. Сер. Новые материалы, их производство и обработка. Вып.4. – М.: 1990. – С. 1-40.
Дата добавления: 2020-01-07; просмотров: 208; Мы поможем в написании вашей работы! |
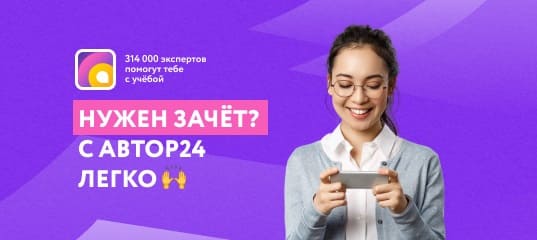
Мы поможем в написании ваших работ!