Исследование процесса индукционного переплава лигатуры Nd-Fe с использованием механически активированных порошков
Как было показано выше, получение магнитов методом порошковой металлургии – это многостадийный процесс. Нами предлагается новая технология их получения, существенно уменьшающая количество операций в технологии получения магнитов и значительно сокращающая количество отходов, т.е. повышающая выход готовой продукции. Принципиальная технологическая схема её представлена на рисунке 70.
Рисунок 70 – Принципиальная технологическая схема получения магнитов
Принципиальные отличия данной схемы от описанной ранее в п.3 состоят в том, что:
- во-первых, полученные слитки тройного и высоконеодимового сплавов по этой схеме подвергаются индукционному переплаву с модификатором для получения мелкокристаллической структуры отливки во всём её объёме;
- во-вторых, при получении сплавов можно использовать металлический неодим, исключив операции фторирования и восстановления;
- в-третьих, непосредственно к порошкам гидридов полученных сплавов можно подшихтовывать до стехиометрии тройного сплава необходимые количества порошков ферробора и металлического железа с последующим их измельчением в шаровых мельницах в процессе твердофазного легирования;
- в-четвёртых, по необходимости, порошки гидридов тройного сплава можно в процессе ТФЛ легировать порошками гидридов сплавов, содержащих диспрозий, тербий и другие металлы.
Если стадии, включающие в себя получение гидридов, достаточно подробно изучены и описаны в данной работе, а последующие операции используются в существующем технологическом цикле получения магнитов, то самые первые операции, индукционный переплав с модификатором, требуют для данной технологии дополнительного изучения. Это связано с тем, что при всех способах получения сплава, его кристаллическая структура не получается мелкокристаллической, состоящей из кристаллов Nd2Fe14В размерами до 10 мкм. Задача получения именно такого типа мелкокристаллической структуры весьма актуальна, это – размеры доменов магнитных материалов. Наши исследования процесса гидрирования высоконеодимовых сплавов (лигатуры Nd-Fe) показали, что этот процесс протекает по границам зёрен, обогащенным неодимом. Образование NdН2 идёт именно по этим границам. Поэтому при смешивании полученных таким образом гидридов с порошкообразным металлическим железом и ферробором произойдёт в процессе ТФЛ последующее спекание и рекомбинация гидридов, и образование кристаллов Nd2Fe14В с размерами доменов 5-10 мкм.
|
|
При получении лигатуры фторидным методом или методом индукционного переплава кристаллизация носит направленный характер от холодных поверхностей футерованного тигля или изложницы соответственно. При этом кристаллы имеют значительный размер. В случае гидрирования такого материала он рассыпался на пластинки и чешуйки, которые необходимо было дополнительно истирать. Известно [139], что для создания мелкокристаллической (5-10 мкм) структуры получаемых сплавов необходимо выполнение одного из следующих условий: скорость охлаждения отливки должна быть не менее 104 К/мин, или процесс кристаллизации должен идти не от стенок, а непосредственно в объёме. Первое условие технологически трудно осуществимо, а для второго был использован зарекомендовавший себя при получении чугунов метод добавки искусственных центров кристаллизации в виде ультрадисперсных механоактивированных порошков[140].
|
|
В данном разделе как раз и приводятся экспериментальные данные по исследованию способа получения магнитного сплава с мелкокристал-лической структурой с использованием модификатора.
Исследования осуществлялись на промышленных установках магнитного участка ХМЗ СХК (г. Северск, Томской области). Переплав магнитных материалов (сплавов и лигатур) проводился на установке УППФ-3М (рисунок 71).
|
|
Рисунок 71 – Установка УППФ-3М
Установка УППФ-3М (рисунок 72) представляет собой двухкамерный агрегат, имеющий камеру плавления 1 и камеру кристаллизации 2. В камере плавления имеется тигель с индуктором 3, снабженные поворотным устройством для слива расплава в кристаллизатор 6. Камера плавления оборудована также устройством 4 для подгрузки кусков чернового материала в тигель. Объем плавильной камеры ~ 2,0 м3, диаметр – 1,5 м. В камере кристаллизации имеется кристаллизатор (медная изложница) 6 и распределительная тарелка (воронка) 5.
Установка УППФ-3М укомплектована вакуумными насосами 8, 9, 10, обеспечивающими получение в объеме камеры остаточного давления газов до 1×10–3 мм рт. ст. Для проведения процесса в инертной среде камера снабжена линией подачи аргона. Контроль температуры процесса можно осуществлять либо с помощью термопар, либо пирометром. Чехлы термопар изготовлены из оксида алюминия.
1 – корпус печи; 2 – камера кристаллизации; 3 – тигель плавильный; 4 – устройство для подгрузки; 5 – воронка; 6 – кристаллизатор; 7 – вакуумный затвор;
8, 9, 10 – насосы вакуумные
Рисунок 72 – Схема установки УППФ-3М
Высокочастотный (ВЧ) генератор мощностью 150 кВт подает питание на индуктор плавильной камеры. Плавильная камера соединена с камерой охлаждения через механизированный вакуумный затвор 7, обеспечивающий сохранение вакуума и возможность проведения процесса расплавления следующей порции сплава во время охлаждения материала с кристалли-затором в отдельной камере.
|
|
Для переплава материалов использовались тигли типа "Крок" (завод Красный Октябрь, г. Москва), изготовленные из корунда (А12О3) различного гранулометрического состава и корундо-муллитовой смеси, и тигли производства ХМЗ СХК, состоящие из корунда с добавкой до 15 % крошки силицированного графита (рисунок 73). Тигель устанавливался в индуктор печи УППФ-3М и закреплялся в опорах с помощью замазки (жидкое стекло, бентонит и электрокорунд фракции (-0,1) мм). Комплект сливного устройства изготавливался на участке керамики цеха 10 ХМЗ СХК из шамота. Сливное устройство предназначено для направления расплавленного металла в шлакоуловитель, а затем через воронку в медный кристаллизатор. Часть шихтового материла загружалась в тигель в виде кусков, а часть в таком же виде размещалась в подгрузочном устройстве.
![]() | ![]() |
Рисунок 73 – Схемы тиглей для индукционного переплава
Медный кристаллизатор был изготовлен из двух частей, которые скреплены установочными болтами. Над кристаллизатором устанавливалась воронка из шамота с покрытием из смеси (Al2O3, бетонит и жидкое стекло), а также шлакоуловитель такой же конструкции, как и воронка. Для уменьшения взаимодействия оксида алюминия с расплавом неодима в состав обмазки вводили до 20-30 % порошка Nd2O3.
После такой подготовки камера плавления изолировалась от камеры охлаждения шибером, вакуумировалась до остаточного давления 1×10-3 мм. рт. ст., включался ВЧ генератор и осуществлялся нагрев шихты (сплава, лигатуры и легирующих добавок) в тигле. При достижении тиглем температуры 900-950 °С из коллектора в плавильную камеру подавался аргон до давления 0,8-0,9 атм и продолжался нагрев тигля до температуры 1300-1500 °С. После расплавления основной массы шихты из дозатора подгружались легирующие металлы, система тигель-расплав металла выдерживалась при этой температуре для усреднения состава в течение 5-7 мин, затем поднимался шибер, тигель поворачивался вокруг оси на 90°, и расплав сливался в кристаллизатор через воронку и шлакоуловитель.
После охлаждения слиток извлекался из кристаллизатора, от него отбиралась проба для анализа, он взвешивался и передавался на склад. Анализ проводился в аналитической лаборатории ХМЗ СХК.
Для того чтобы кристаллизация начиналась одновременно во всём объёме слитого в изложницу металла, непосредственно перед сливом в расплавленный материал вводился механоактивированный модификатор. Он состоял из оксидов РЗЭ, плакированных железом, и, являясь поверхностно – активным веществом, обеспечивал возникновение активных центров кристаллизации во всём объёме застывающего материала. Это позволяло создать одинаковую микроструктуру в объёме слитка, и в дальнейшем, облегчало процесс водородного измельчения, когда гидрирование материала проходило только по границам межзёренного пространства.
Практически это выглядело следующим образом (рисунок 74):
Рисунок 74 – Схема смешивания модификатора с магнитным сплавом
- на край индуктора, куда помещалась шихта, устанавливалась небольшая площадка с модификатором;
- нагревали индуктор и расплавляли исследуемый материал;
- затем индуктор немного наклоняли, не выливая металл, и модификатор по площадке скатывался в расплав;
- проводили выдержку 2-3 минуты для полного растворения и перемешивания модификатора с расплавом с последующим сливом в медную изложницу.
Полученный слиток был раздроблен на прессе и образец из центра слитка был отшлифован по торцу и проанализирован на электронном микроскопе Philips SEM 515 (рисунок 75).
Как видно из микрофотографий, поверхность модифицированной лигатуры выглядит более "рыхлой", с меньшим размером зерен (0,1 – 1,0 мкм). Ожидается, что гидрирование такого материала будет проходить более интенсивно, чем стандартной высоконеодимовой лигатуры.
Рисунок 75 – Микрофотографии скола стандартной высоконеодимовой лигатуры без (а) и с модификатором (б)
При получении из этой лигатуры магнитных сплавов Nd-Fe-B, выплавленных по стандартной технологии, было отмечено увеличение хрупкости полученных слитков при их измельчении, а свойства магнитов, полученных из сплава без добавки, и с добавкой механоактивированного модификатора представлены в таблице 12.
Таблица 12 – Сравнительные характеристики полученных магнитов
Номер слитка | Количество модификатора, %/г | Масса шихты, кг | Время помола, мин | Магнитные характеристики | Примечание | |
Br, Тл | Hcm, кЭ | |||||
233 | Без модификатора | 22,8 | 36 | 1,2 | 5,75 | Изложница горячая |
234 | 0,05 / 11,4 | 22,8 | 30 | 1,19 | 5,75 | Изложница холодная |
36 | 1,19 | 5,75 | ||||
42 | 1,19 | 6,0 | ||||
235 | 0,05 / 11,4 | 22,8 | 30 | 1,25 | 4,0 | Изложница горячая |
36 | 1,25 | 4,0 | ||||
42 | 1,25 | 4,0 |
Из табличных данных видно, что даже небольшая добавка модификатора позволила поднять магнитную индукцию до 1,25 Тл, хотя однозначно, поскольку не найдены оптимальные условия процессов кристаллизации и получения магнитов, говорить об эффективности применения метода объемной кристаллизации при изготовлении магнитных сплавов Nd-Fe-B пока рано. В любом случае, необходимо провести дополнительные исследования предлагаемого метода и использование этого метода в ТФЛ.
Таким образом, в результате применения гидридов для изготовления магнитов установлено, что:
- магниты, изготовленные из сплава, химический состав которого был скорректирован методом ТФЛ с применением гидридов, показали более высокие магнитные характеристики (Br = 1,25 - 1,32 Тл; Hcµ = 7,9 – 8,8 кЭ), по сравнению с магнитами, изготовленными по обычной технологии (Br = 1,02 - 1,18 Тл; Hcµ = 3,4 – 6,0 кЭ);
- предложена и опробована технология получения магнитов, существенно уменьшающая количество операций и значительно сокращающая количество отходов, и, соответственно, повышающая выход готовой продукции.
Дата добавления: 2020-01-07; просмотров: 190; Мы поможем в написании вашей работы! |
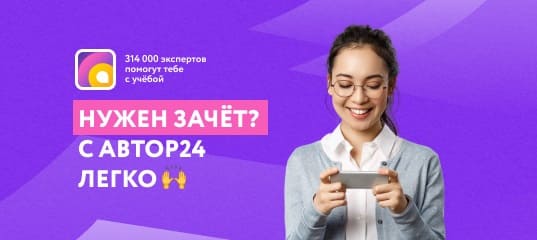
Мы поможем в написании ваших работ!