Техника безопасности при выполнении работ в гальваническом цехе
Всех работающих в цехе необходимо обеспечить соответствующей специальной одеждой: костюмом для защиты от кислот из молескина с кислотозащитной отделкой К20, прорезиненным фартуком, головным убором, резиновыми сапогами, защитными очками, комбинированными рукавицами, резиновыми перчатками, респираторами, противогазом, утепленной курткой.
Рациональное освещение помещений и рабочих мест – один из важнейших элементов благоприятных условий труда.
При правильном освещении повышается производительность труда, улучшаются условия безопасности, снижается утомляемость.
При недостаточном освещении рабочий плохо видит окружающие предметы и плохо ориентируется в производственной обстановке.
Успешное выполнение рабочих операций требует от него дополнительных усилий и большого зрительного напряжения. Неправильное и недостаточное освещение может привести к созданию опасных ситуаций.
1. К самостоятельной работе на операциях нанесения гальванопокрытий допускаются лица:
- достигшие восемнадцатилетнего возраста;
- прошедшие медосмотр и не имеющие противопоказания по результатам осмотра;
- прошедшие производственное обучение с проверкой знаний и имеющие удостоверение на право работы с химическими веществами.
2. Персонал, работающий на операциях по производству покрытий должен знать:
- физические и химические свойства применяемых химических материалов;
|
|
- особенности действия химических материалов на организм человека;
- правила пользования средствами индивидуальной защиты.
3. Требования безопасности перед началом работы:
- проверить наличие и исправность спецодежды;
- общие проходы и подходы к рабочим столам, приборам и оборудованию должны быть свободны;
- рабочая поверхность вытяжных шкафов, предназначенных для работы с концентрированными кислотами и щелочами, должны быть полностью покрыты материалом, устойчивым к воздействию этих веществ;
- вся используемая посуда и тара должна быть подписана, и применяться только по назначению.
4. Требования безопасности во время работы:
- загрузка деталей в ванну должна производиться осторожно во избежание разбрызгивания электролита;
- при выгрузке деталей из ванны необходимо поддерживать их над ней для стекания электролита;
- недопустимо поправлять контакты, находящиеся под напряжением;
- во избежание отравления недопустимо наклоняться над ванной, хранить и принимать пищу на рабочем месте, пользоваться химической посудой для питья
5. Требования безопасности по окончании работы:
- по окончанию работы отключить электрические приборы от сети;
|
|
- привести в порядок рабочее место;
- сообщить сменщику о ходе работы и сдать ему рабочее место;
- сообщить руководителю обо всех отклонениях во время работы и о мерах, принятых к их устранению.
Оказание первой помощи пострадавшему от электрического тока.
1. Оказывающий помощь должен знать:
- основные признаки нарушения жизненно важных функций организма человека;
- общие принципы оказания первой помощи;
- основные способы переноски и эвакуации пострадавших.
2. Последовательность оказания первой помощи:
- устранить воздействие на организм повреждающих факторов, угрожающих здоровью и жизни пострадавшего, оценить состояние пострадавшего;
- выполнить необходимые мероприятия по спасению пострадавшего в порядке срочности (восстановить проходимость дыхательных путей, провести искусственное дыхание, наружный массаж сердца, остановить кровотечение, наложить повязку и т.д.);
- поддержать основные жизненные функции пострадавшего до прибытия медицинского работника;
- вызвать скорую медицинскую помощь.
7.
Изм.
Лист
№ докум.
Подпись
Дата
Лист
1
БГТУ 07. 00. ПЗ
Разраб.
Жилянина А. В.
Провер.
Дроздович В. Б.
Н. Контр.
Утверд.
Дроздович В. Б.
Вопросы экономики, организации, планирования и управления предприятием
Лит.
Листов
9
Вопросы экономики, организации, планирования и управления предприятием БГТУ 41606007, 2010
|
|
Производственная деятельность республиканского унитарного предприятия «Минский завод колесных тягачей» сконцентрирована на изготовлении и продаже потребителям специальной автомобильной техники, поставках ее на экспорт в страны дальнего зарубежья и СНГ, выпуска и реализации запасных частей к автомобилям и плугов для нужд сельского хозяйства.
Основными направлениями производственно-хозяйственной деятельности предприятия являются: выпуск автомобилей и тягачей для газовой и нефтедобывающей промышленности, для перевозки сыпучих грузов по дорогам всех категорий, шасси под монтаж кранового оборудования грузоподъемностью 25–160 тонн, шасси под монтаж оборудования для цементовоза, топливозаправщика, прицепной техники различного назначения, специальных колесных шасси для нужд обороны, выпуск запчастей для своей основной продукции.
|
|
Основной целью деятельности УП «МЗКТ» является выработка стратегии на ближайшую и длительную перспективу развития, основанную на наращивании объемов производства и реализации продукции, как на внутреннем, так и внешнем рынках; техническое перевооружение предприятия; экономическое обоснование оптимального расходования финансовых, материальных и трудовых ресурсов, а также повышение конкурентоспособности выпускаемой продукции на международных рынках.
Достижение определяющей цели планируется осуществить путем решения следующих главных задач:
– технического перевооружения производства, модернизации и обновления необходимого оборудования;
– внедрения новых и высоко-прогрессивных энерго- и ресурсосберегающих технологий;
– наращивания объёмов выпуска специальной автотехники новых моделей;
– сохранения устойчивых позиций на имеющихся рынках сбыта и расширение организация сервисного обслуживания клиентов;
– обеспечения выполнения высоких технико-экономических показателей.
Решение поставленных задач предполагает внесение существенных коррективов в маркетинговую политику предприятия, сочетающую в себе как работу на рынках СНГ и России по существенному увеличению продаж, так и максимальное укрепление позиций на рынках дальнего зарубежья.
УП «МЗКТ» является унитарным предприятием со 100% государственным капиталом Республики Беларусь, созданным на основании приказа Государственного комитета промышленности (Министерства промышленности
Республики Беларусь в настоящее время) от 08.02.1994 года на базе производственной структуры Минского автомобильного завода (МАЗ) «Производство специальных колесных тягачей». Длительное время это производство специализировалось на выпуске автомобильных шасси для мобильных ракетных комплексов.
Завод является самостоятельным субъектом хозяйствования с правом юридического лица и осуществляет свою деятельность в соответствии с Уставом предприятия. Уставный фонд завода на 1 января 2005 года составил 321 млн. руб. Унитарное предприятие создано с целью осуществления хозяйственной деятельности, направленной на получение прибыли.
В соответствии с Указом Президента Республики Беларусь от 30 декабря 2003 года N599 "О создании Государственного военно-промышленного комитета Республики Беларусь" и приказом Госкомвоенпрома N1 от 15.01.2004 года УП "МЗКТ" передан в ведение Государственного военно-промышленного комитета Республики Беларусь.
В структуре предприятия имеется 10 цехов основной деятельности, 3 цеха вспомогательной деятельности, 15 функциональных управлений, 18 отделов, военизированная охрана, экспериментальный цех, исследовательский цех, ремонтно-механический цех.
Предметом деятельности УП "МЗКТ" является производство и реализация автомобильной и автоприцепной техники, в том числе и специального назначения, комплектующих изделий, деталей и запасных частей, а также выполнение гарантийного и сервисного обслуживания произведенной продукции.
УП "МЗКТ" производит и продает, в основной своей части под заказы покупателей, автотранспортные средства высокой проходимости и различной грузоподъемности, которые в зависимости от технических характеристик можно классифицировать как:
По габаритной ширине:
– дорожные (с колесными формулами 6x4, 6x6, 8x4, 8x8);
– внедорожные (с колесными формулами 8x8, 12x12);
По грузоподъемности:
– тяжелые (от 20 до 40 тонн);
– сверхтяжелые (грузоподъемностью от 46 до 75 тонн и в перспективе до 150 тонн).
Основными направлениями МЗКТ по созданию транспортных средств большой грузоподъемности в настоящее время являются:
– многоосные полноприводные шасси под монтаж оборудования народно-хозяйственного назначения (бурового, для ремонта нефтегазовых скважин и т.д.);
– большегрузные автопоезда в составе тягачей 8x8 и полуприцепов (прицепов) к ним грузоподъёмностью 40–75 тонн;
– автомобили и шасси с колёсной формулой 8x4 для перевозок грузов и монтажа специализированного оборудования (самосвалов, топливозаправщиков, бетоносмесителей и бетоновозов, оборудования для контейнерных перевозок);
– специальные полноприводные шасси с колёсной формулой 6x6 и 8x8 под монтаж оборудования для нефтегазового комплекса.
По состоянию на сегодняшний день Минским заводом колесных тягачей разработана и освоена целая гамма автомобильной техники высокой, повышенной проходимости внедорожного класса с колесной формулой 8x8, 12x12 и дорожного габарита с колесной формулой 8x4, 6x4, 6x6, которую условно можно выделить в следующие основные семейства:
– специальные шасси и тягачи для монтажа систем вооружений;
– специальные шасси под монтаж нефтегазового оборудования;
– крановые шасси;
– специальные автомобили и автомобили-самосвалы;
– седельные тягачи;
– прицепы и полуприцепы.
Технические характеристики выпускаемой заводом продукции позволяют применить АТС в различных отраслях экономики, в районах как с развитой, так и не развитой сетью дорог.
Приоритетным направлением, определяющим стратегию развития предприятия, выбрано создание и освоение новой продукции, пользующейся спросом у покупателя.
Так, удельный вес новой продукции в объеме производства в 2004 г. составлял – 35,3%, в 2005г. – 42,4%, в 2006г. – 59,6%%, в 2007г. – 61,2%.
В настоящее время ОАО «МЗКТ» принимает активные меры по завоеванию позиций на рынках стран, в которые несколько лет назад по объективным причинам реализация тяжелой автотранспортной техники была приостановлена. Результаты проводимой маркетинговой стратегии свидетельствуют об эффективности прилагаемых усилий.
Товарные рынки ОАО «МЗКТ» представлены в таблице 7.1.
Реализация на территории Республики Беларусь в 2008 году составила 18,2% общего объема реализованной продукции, в 2007 году – 35,9%, в 2006 году – 58,3%, сокращение объема реализации в Беларуси за анализируемый период составило 40,1%.
Реализация в Российскую Федерацию в 2008 году составила 64,4% общего объема реализованной продукции, в 2007 году – 52,4%, в 2006 году – 39,3%, увеличение объема реализации в Россию за анализируемый период составило 25,1 %.
Реализация для стран дальнего зарубежья в 2007 году составила 11,2% общего объема реализованной продукции, в 2006 году – 11,7%, в 2003 году –1,7%, увеличение объема реализации в данные страны за анализируемый период составило 9,3 % (шасси, самосвалы, тягачи и прицепы).
Реализация в страны СНГ в 2008 году составила 6,2 % общего объема реализованной продукции, в 2007 году – не осуществлялась, в 2006 году – 0,7%, увеличение объема реализации в страны СНГ за анализируемый период составило 5,5% (самосвалы, тягачи, крановые шасси).
Сальдо внешней торговли (разница между суммой экспорта и импорта) в 2007 году составила 20728,8 млн. р. и увеличилось в процентном соотношении на 23,7% по сравнению с 2006 годом.
При этом удельный вес экспорта в общем объеме реализации за период с 2006 по 2008 гг. колебался с 63,0% до 78,1%, что говорит о том, что ОАО «МЗКТ» является экспортоориентированным предприятием.
Таблица 7.1 – Товарные рынки ОАО «МЗКТ»
Основные виды продукции | Рынки сбыта (страны и регионы) | |
Специализация предприятия | Вид продукции | |
Строительные компании | Самосвалы, автокраны, автоопрокидыватели, мусоровозы, асфальтовозы | Страны СНГ: Беларусь, Россия, Украина Страны дальнего зарубежья: страны Прибалтики, Болгария |
Предприятия газо- и нефтепереработки | Внедорожные автомобили высокой проходимости: плетевозы, полноприводные самосвалы, буровые установки, шасси со спецплатформой | Страны СНГ: Россия, Казахстан Страны дальнего зарубежья: Пакистан, ОАЭ, Турция, Сирия |
Лесозаготовительные организации | Лесовоз, пожарные машины | Страны СНГ: Центральный, Северо-Западные районы РФ Страны дальнего зарубежья: страны Прибалтики |
Военно-промышленный комплекс | Автопоезда для перевозки гусеничной техники, неделимых грузов, топлива | Страны СНГ: РФ Страны дальнего зарубежья: Ближний Восток, Юго-Восточная Азия, Юго-Западная Азия, Европа, Северная Африка |
ПДП, ПДС | Спецшасси под экскаваторы, крановые установки | Страны СНГ: Центральный район РФ, Западная и Восточная Сибирь |
Основным рынком экспорта готовой продукции ОАО «МЗКТ» является рынок России, кроме российского рынка предприятие поставляет свою продукцию в Украину, Молдову, Казахстан, страны Средней Азии и страны Балтии, а также в страны дальнего зарубежья: Ближний Восток, Юго-Восточная Азия, Юго-Западная Азия, Европа, Северная Африка.
Производительность линий представлена в таблицах 7.2.
Цены (тарифы) на все виды используемых в данном цехе материалов и энергии, действующие на заводе на момент сбора данных, представлены в таблице 7.3 и 7.4. Численность персонала по профессиям и специальностям с указанием тарифного разряда:
всего 37 человек:
– 32 основной персонал (гальваники);
– 5 вспомогательный персонал (корректировщики).
Гальваники имеют 4 разряд, а корректировщики 5.
Ставка первого разряда на предприятии (на момент прохождения практики) – 164230 руб. Тарифные коэффициенты 4 и 5 разрядов равны 1,57 и 1,73 соответственно.
Таблица 7.2 – Производительность автоматизированных и механизированных линий
Линия | Производительность |
Цинкование на подвесках АЛГ-232 | 4,7 м²/ч |
Цинкование в барабанах АЛГ-35М | 7 м²/ч |
Фосфатирование | 5 м²/ч |
Анодирование | 1,5 м²/ч |
Хромирование | 703,981 м2/год |
Таблица 7.3 – Цены на все виды используемых в данном цехе энергии
Наименование | Цена |
Электроэнергия | 263,2 руб. за 1кВт∙ч |
Теплоэнергия | 130,6 руб. за 1 Гкал |
Вода (канализация) | 580 руб. за 1м³ |
Таблица 7.4 – Цены на все виды используемых в данном цехе материалов
Наименование | Цена, руб./кг |
Амоний сернокислый чистый | 2530 |
Ангидрид хромовый технический | 14450 |
Бихромат натрия кристаллический | 14490 |
Блескообразующая добавка ЩЦ | 7965 |
Известь хлорная | 1734 |
Калий-натрий виннокислый | 11630 |
Калий-железо синеродистое техническое | 10250 |
Кислота азотная | 408 |
Кислота серная техническая | 470 |
Концентрат фосфатирующий | 7950 |
Купорос медный | 9420 |
Натр едкий технический | 2510 |
Натрий азотнокислый технический | 3100 |
Натрий сернокислый | 3670 |
Оксид цинка | 7950 |
Олово (аноды) | 70813 |
Сода кальцинированная | 980 |
Свинец в чушках | 7790 |
Тринатрийфосфат | 2760 |
Фосфатирующий состав | 6950 |
Цинк (аноды) | 9800 |
ОАО "МЗКТ" был создан в 1959 году (в то время Производство специальных колесных тягачей МАЗ) для проектирования и выпуска многоосных колесных полно-приводных тягачей большой грузоподъемности предназначенных для различных систем вооружения.
Технические решения, заложенные в конструкции моделей МАЗ-535 и МАЗ-537, оказались настолько удачными, что привело к созданию семейства специальных шасси МАЗ-543.
Почти на протяжении 30 лет завод серийно выпускал эту технику, доведя объемы продукции до 1200–1300 шасси в год.
В 90-е годы произошло резкое падение объемов производства, упал спрос на ранее выпускавшиеся специальные колесные тягачи для нужд МО СССР.
Из-за недостатка средств было практически прекращено обновление основных фондов.
Создавшаяся ситуация заставила завод искать пути выхода из нее за счет разработки принципиально новых изделий для народного хозяйства, в том числе автомобилей и тягачей для газовой и нефтеперерабатывающей промышленности, шасси под монтаж кранового оборудования, самосвалов для перевозки сыпучих грузов по дорогам всех категорий и других.
Существующие производственные мощности позволяют развиваться заводу и наращивать объемы производства без существенного расширения площадей, но при условии обновления парка физически изношенного оборудования.
В цехах завода эксплуатируется 2786 единиц технологического оборудования. 73% оборудования эксплуатируется более 20 лет, со сроком эксплуатации до 10 лет – 1,5%. Износ составляет 97,4%.
Процент обновления в 2005 году составил 0,25%.
Таблица 7.5 – Производственная мощность участка металлопокрытий
Виды металлопокрытий | Годовой фонд времени работы оборудования в часах | Коэффициент загрузки оборудования |
Хромирование | 4015 | 0,55 |
Фосфатирование | 4015 | 0,22 |
Меднение | 4015 | 0,069 |
Анодирование | 4015 | 0,14 |
Олово-висмут | 4015 | 0,02 |
Цинкование | 4015 | 1 |
Цинкование: | ||
насыпью | 3810 | 0,57 |
подвески | 3810 | 0,2 |
Средний коэффициент загрузки оборудования равен 0,44. Производственная мощность 107% к плану.
График планово-предупредительных ремонтов ведущего оборудования представлен в таблице 7.6.
Таблица 7.6 – График планово-предупредительных ремонтов ведущего оборудования
Наименование оборудования | Виды работ по месяцам | |||||||||||
1 | 2 | 3 | 4 | 5 | 6 | 7 | 8 | 9 | 10 | 11 | 12 | |
Линия автоматическая цинкования | О | М | О | |||||||||
Линия фосфатирования | О | С | О | |||||||||
Линия хромирования | О | О | К | |||||||||
Линия анодирования | О | О | О | |||||||||
Линия никелирования | О | О | М | |||||||||
Примечание: О – осмотр, М – малый ремонт, С – средний ремонт, К – капитальный ремонт. |
Сметы общепроизводственных, общехозяйственных и коммерческих расходов:
1. Содержание аппарата управления:
1.1. Основная и дополнительная заработная плата персонала управления цеха в соответствии с номенклатурой должностей, относящихся к аппарату управления и отчислений на социальное страхование;
1.2. Содержание диспетчерской связи.
2. Содержание прочего цехового персонала:
2.1. Основная и дополнительная заработная плата с отчислениями на социальное страхование мастеров производственных участков цеха, механика, энергетика;
2.2. Основная и дополнительная заработная плата с отчислениями на социальное страхование ИТР и других работников, не относящихся к аппарату управления.
3. Амортизация зданий, сооружений и оборудования;
4. Содержание зданий, сооружений и оборудования цеха:
4.1. Расходы на содержание оборудования (стоимость смазачно-обтирочных материалов, эмульсии для охлаждения и других вспомогательных материалов, необходимых для оборудования и содержанием его в рабочем состоянии);
4.2. Стоимость материалов, израсходованных на хозяйственные нужды цехов, а также на содержание электросети, отопительной сети, водоснабжения и канализации, на содержание в чистоте помещений и другие хозяйственные нужды;
4.3. Стоимость электроэнергии, расходуемой на хозяйственные нужды цеха;
4.4. Стоимость теплоэнергии, расходуемой на хозяйственные нужды цеха;
4.5. Стоимость топлива, воды, пара, сжатого воздуха и других видов энергии,
расходуемой на хозяйственные нужды цеха;
4.6. Основная и дополнительная заработная плата с отчислениями на социальное страхование вспомогательных рабочих, занятых на хозяйственных работах по уборке помещений цеха, протирке, вставке и промазке стекол, очистке дымоходов, крыш от снега, вывозке и выброске мусора, очистке и уборке отнесенных к цеху проездов и тротуаров и других хозяйственных работах;
4.7. Оплата работ и услуг сторонних организаций по текущему ремонту зданий и сооружений;
4.8. Основная и дополнительная заработная плата с отчислениями на социальное страхование вспомогательных рабочих и кладовщиков
службы энергетика;
4.9. Стоимость ремонтно-строительных материалов, израсходованных для ремонта зданий, сооружений хозспособом;
4.10. Основная и дополнительная заработная плата с отчислениями на социальное страхование вспомогательных рабочих, крановщиков службы
механика;
4.11. Оплата работ и услуг сторонних организаций по текущему ремонту машин и оборудования;
4.12. Оплата работы и услуг по капитальному ремонту ОС, МБП цеха сторонним организациям ;
4.13. Затраты на ремонт машин и оборудования хозспособом;
4.14. Стоимость запчастей для ремонта оборудования.
5. Транспортное обслуживание:
5.1. Оплата транспортных услуг сторонних организаций;
5.2. Расходы на содержание и эксплуатацию транспортных средств, занятых внутризаводским перемещением сырья и материалов, инструментов, деталей, заготовок и т.п. с базисного склада в цеха и доставкой готовой продукции на склады хранения; стоимость бланков путевых листов;
5.3. Основная и дополнительная заработная плата с отчислениями на социальное страхование водителей, машинистов, сцепщиков, стропальщиков, крановщиков, вспомогательных рабочих, занятых перемещением, погрузкой или выгрузкой материалов, деталей, готовых изделий, отходов и прочих грузов на складах хранения и в цехах.
6. Расходы по ремонту и восстановлению инструмента:
6.1. Стоимость услуг, оказанных сторонними организациями, по ремонту, восстановлению и заточке инструмента, испытания;
6.2. Затраты по наладке оборудования и инструментария;
6.3. Основная и дополнительная заработная плата с отчислениями на социальное страхование рабочих, занятых ремонтом и восстановлением инструментов слесарей, токарей, фрезеровщиков, бюро инструментальной хозяйственной заточки и других работников.
7. Стоимость спецодежды, обуви и защитных приспособлений, стоимость молока, жиров, мыла, газированной воды, дезинфекция мест общего пользования, спецодежды, детализация, озеленение помещений цехов; содержание и устройство средств по технической безопасности, номенклатурные мероприятия по охране труда;
8. Инструмент:
8.1. Стоимость инструмента;
8.2. Стоимость специнструмента общего назначения;
8.3. Стоимость инвентаря цехов, ремонты и погашение стоимости инвентаря и хозяйства.
9. Расходы на командировки работников цехов;
10. Отчисления на социальное страхование из премии;
11. Междугородние телефонные переговоры, оплата услуг факсимильной и спутниковой связи, интернета, электронной почты;
12. Доплаты:
12.1. Доплата работникам цехов за ночное и вечернее время;
12.2. Сверхурочные выплаты;
12.3. Доплата работникам до среднего заработка;
12.4. Доплата беременным женщинам при переводе на больничный на легкую или менее оплачиваемую работу с отчислениями на социальное страхование;
12.5. Резерв отпускных персонала цехов с отчислениями на социальное страхование.
Непроизводственные расходы:
13. Потери от простоев:
13.1. Стоимость сырья и материалов, топлива и энергии, израсходованных
период простоев по вине цеха;
13.2. Основная и дополнительная заработная плата рабочих за время простоев;
13.3. Доплата рабочим, которые за время простоев были использованы на работах, требующих применение менее квалифицированного труда.
14. Стоимость потерь материальных ценностей в пределах норм естественной убыли при хранении в цеховых кладовых;
15. Расходы по инвентаризации;
16. Канцелярские расходы: стоимость канцелярских и чертежных принадлежностей, стоимость бланков отчетности и документации цехов, стоимость переплетных и типографских работ;
17. Основная и дополнительная заработная плата с отчислениями на социальное страхование вспомогательных рабочих, занятых пошивом спецодежды;
18. Услуги сторонник организаций производственного характера;
19. Расходы, связанные с возмещением ущерба, нанесенного в результате производственных травм, производимые на основании решений, вынесенных в текущем году;
20. Прочие расходы (по договорам сторонних организаций);
21. Стоимость материалов, запчастей израсходованных для ремонта
оргтехники по цехам.
Изм.
Лист
№ докум.
Подпись
Дата
Лист
1
БГТУ 07. 00. ПЗ
Разраб.
Жилянина А. В.
Провер.
Дроздович В. Б.
Н. Контр.
Утверд.
Дроздович В. Б.
Учебное рационализаторское предложение
Лит.
Листов
4
8 Учебное рационализаторское предложение БГТУ 41606007, 2010
Предлагаю изменить технологию производства путем внедрения технологии скоростного хромирования.
Состав электролита, г/дм3:
хромовый ангидрид…………………..60–200
добавка №1………………………………..1–5
добавка №2…………………………..0,05–1,0
Способ приготовления электролита:
1. Рецептурное количество хромового ангидрида около 160 г/дм3 растворяют в рабочей ванне небольшого объема проточной холодной воды. После растворения храмового ангидрида доводят водой уровень рабочей ванны на 2/3–3/4 объема электролита.
2. Растворяют отдельно небольшими порциями в горячей (30–40°С) или холодной воде рецептурное количество вещества, выбранного из группы 1 (около 3 г/дм3), затем добавляют небольшое количеств раствора хромового ангидрида в раствор состоящий из веществ 1 группы до изменения цвета раствора солей 1 группы, затем вводят приготовленный таким образом раствор в рабочую ванну небольшими порциями перемешивая рабочий раствор.
3. Растворяют отдельно рецептурные количества около 0,2–0,5 г/дм3 вещества, выбранные из группы 2 в небольшом количестве горячей воды (температура 80–90°С) и вводят указанный раствор в рабочую ванну, перемешивая рабочий раствор. При введении раствора веществ в группы 2 рабочий раствор может быть или горячим (40–60°С) или холодным. Добавка веществ группы 2 лучше растворяется в горячем растворе.
После введения в рабочий раствор комплексов – веществ группы 2, электролит довести до уровня проточной холодной водой, тщательно перемешать. Электролит выдержать 0,5–3 часа при температуре электролита 10–55°С после чего он готов к работе. Блестящее хромовое покрытие должно сохраняться после нескольких перерывов тока, если блеск не сохраняется, то ванну необходимо проработать в течении 0,5–1 часа до сохранения блеска покрытия после нескольких перерывов тока.
Режим работы электролита скоростного хромирования. Плотность тока 5–150 А/дм2, оптимальная рабочая плотность тока от 10 до 50 А/дм2, температура электролита от 10 до 90°С в зависимости от требуемых свойств хромовых покрытий с максимальной твердостью и износостойкостью температура электролита должна быть 35–60°С. Скорость осаждения покрытий при 30–35 А/дм2 составляет 1–1,2 мкм/мин.
Основные неполадки электролита скоростного хромирования приведены в таблице 8.1.
Таблица 8.1 – Основные неполадки электролита скоростного хромирования
Основные неполадки | Причина | Способ устранения |
Пригар на выступающих частях деталей или отличие цвета на выступающих частях деталей от основного покрытия | 1. Увеличенная плотность тока, малая или большая концентрация хромового ангидрида | 1. Уменьшить плотность тока до 10–40 А/дм2 |
2. Малая концентрация веществ группы 2 | 2. Ввести вещества группы 2 из расчета 0,2–0,3 г/л | |
Желтый налет убираемый протиркой или щелочными растворами в углубленных частях деталей | 1. Малая плотность тока, малая концентрация веществ группы 1, малая концентрация веществ группы 2 | 1. Увеличить плотность тока до 10–40 А/дм2, увеличить концентрацию хромового ангидрида до 150–160 г/дм3. Ввести вещества группы 1 из расчета 0,5–1 г/дм3, ввести вещества группы 2 из расчета 0,1–0,5 г/дм3 (при отсутствии на поверхности электролита пены) |
Ослабление блеска покрытий или покрытия осаждаются напряженными | 1. Малая концентрация веществ группы 2 | 1. Ввести вещества группы 2 из расчета 0,1–0,5 г/дм3 |
Корректировка электролита скоростного хромирования:
1. Корректировка электролита производится на основе химического анализа хромового ангидрида.
Содержания хромового ангидрида определяется по удельному весу электролита или химическими способами, применяемыми в промышленности.
2. Корректировка электролита при работе электролита скоростного хромирования используют аноды применяемые в промышленных способах хромирования – свинцово-сурмянистые, свинцовые, свинцово-оловянные и т.д.
Указанные аноды в электролите скоростного хромирования не разрушаются, чистка анодов не производится.
Соотношение катодной и анодной поверхности 1:1 или 1:2. При длительных перерывах в работе электролита скоростного хромирования необходимо кратковременная проработка электролита для активации анодов (5–15 мин.).
Корректировка электролита скоростного хромирования производить в следующем порядке: хромовый ангидрид, вещества выбранные из группы 1, вещества, выбранные из группы 2.
Указанные вещества можно вводить при любой температуре электролита. Хромовый ангидрид вводится непосредственно в рабочую ванну, размешивается до полного растворения. Вещества группы 1 растворяются в горячей или холодной воде, в полученный раствор вводится небольшая порция электролита из рабочей ванны до изменения цвета раствора веществ группы 1. Полученный таким образом раствор вводится в рабочую ванну небольшими порциями и электролит перемешивается.
Вещества группы 2 растворяются в горячей воде 80–90°С и вводятся в рабочий электролит небольшими порциями, перемешивая электролит.
Вещества группы 2 в электролите скоростного хромирования на ряду с другими свойствами обеспечивают уменьшение выделения хромового ангидрида в рабочую зону и вытяжку, так как обладают поверхностно-активными свойствами. Электролит работает с небольшой пеной.
Агрессивность электролита определена методом погружения образцов в электролит хромирования и выдержки 13 часов при температуре электролита 10–70°С. Агрессивность электролита к стали в г/м2∙час при 20°С составляет 0,06, агрессивность электролита к латуни в г/м2∙час составляет 22,9.
Коррозионная стойкость определялась погружением образцов с хромовым покрытием в коррозионные среды.
Скорость коррозии в г/м2∙час для 1 раствора соляной кислоты составляет 0,247, в 4% растворе фтористого натрия 0,001, в 40% растворе лимонной кислоты 0,002 – изменение цвете покрытий не наблюдается.
Пористость покрытия измерялась методом наложения фильтровальной бумаги через 1 час после осаждения покрытия. Покрытие не имеет практически пор при толщине свыше 3 мкм. Это подтверждается данными электронного растрового микроскопа.
Износостойкость покрытия уменьшается примерно в 2 раза по сравнению с покрытием, осажденным из стандартного электролита хромирования.
Удельные нормы раствора химикатов на 1 м2 хромовых покрытий. Расход
хромового ангидрида рассчитывают по общепринятым методикам с учетом действия поверхностно-активных веществ.
Вещества группы 1 – расход 0,001–0,003 кг/м2. Вещества группы 2 – расход 0,0005–0,001 кг/м2.
Требования безопасности. Технологический процесс хромирования связан с применением хромового ангидрида, относящегося к вредным веществам, поэтому
при работе с ним необходимо соблюдать меры предосторожности, предусмотренные «Правилами безопасности при травлении металлов и нанесении на них гальванических и химических покрытий», утвержденными Министром Здравоохранения СССР и ЦК профсоюза 12 декабря 1968 г. и ГОСТ 12.3.008-75.
Сравнение стоимости компонентов электролитов скоростного хромирования и хромирования из стандартного электролита, применяемого на предприятии.
Таблица 8.2 – Стоимость материалов
Наименование | Стоимость, руб./кг |
Хромовый ангидрид | 5000 |
Н2SO4 | 126,51 |
Добавка №1 | 15050 |
Добавка №2 | 21500 |
Объем ванны равен 950 дм3.
Состав электролита скоростного хромирования:
хромовый ангидрид……………………...150
добавка №1………………………………..1,5
добавка №2………………………………..1,0
Состав электролита хромирования, применяемого на предприятии:
хромовый ангидрид……………………187,5
Н2SO4……………………………………..1,85
Найдем массу компонентов на загрузку одной ванны по формуле:
m = C∙V (8.1)
Для электролита скоростного хромирования:
– количество хромового ангидрида:
mCrO3 = 0,150 ∙ 950 = 142,5 кг
– количество добавки №1:
m = 0,0015 ∙ 950 = 1,35 кг
– количество добавки №2:
m = 0,001 ∙ 950 = 0,95 кг
Для стандартного электролита:
– количество хромового ангидрида:
mCrO3 = 0,1875 ∙ 950 = 177,65 кг
– количество Н2SO4:
mН2SO4 = 0,00185 ∙ 950 = 1,758 кг
Общая стоимость компонентов, которые необходимы для загрузки одной ванны:
– электролит скоростного хромирования:
S1 = 142,5 ∙ 5000 + 1,35 ∙ 15050 + 0,95 ∙ 21500 = 753242,5 руб.
– электролит стандартного хромирования:
S1 = 177,65 ∙ 5000 + 1,758 ∙ 126,51 = 888473 руб.
Изм.
Лист
№ докум.
Подпись
Дата
Лист
1
БГТУ 00. 00. ПЗ
Разраб.
Жилянина А. В.
Провер.
Дроздович В. Б.
Н. Контр.
Утверд.
Дроздович В. Б.
Заключение
Лит.
Листов
1
Заключение БГТУ 41606007, 2010
В данном отчете по технологической практике представлена деятельность ОАО “МЗКТ”. За время прохождения технологической практики были изучены все имеющиеся на предприятии процессы нанесения гальванопокрытий. Одним из ведущих процессов является процесс нанесения хромового покрытия. Также изучено основное и вспомогательное оборудование, экономика производства, вопросы стандартизации, охраны труда, охраны окружающей среды.
Основными проблемами предприятия, на мой взгляд, являются проблемы, связанные с недостатком материальных средств для обеспечения качественного производства продукции. Также несомненной проблемой является техническое перевооружение предприятия и замена устаревшего оборудования.
Высокая степень ручного труда не позволяет значительно повысить производительность и качество выпускаемой продукции, техническое состояние оборудования не соответствующие, из этого можно сделать вывод, что оно требует замены на современное автоматическое оборудование.
Изм.
Лист
№ докум.
Подпись
Дата
Лист
1
БГТУ 00. 00. ПЗ
Разраб.
Жилянина А. В.
Провер.
Дроздович В. Б.
Н. Контр.
Утверд.
Дроздович В. Б.
Список использованных источников
Лит.
Листов
2
Список использованных источников БГТУ 41606007, 2010
1 Электроосаждение металлических покрытий: справочник / М. А. Беленький, А. Ф. Иванов. – М.: Металлургия, 1985. – 288 с.
2 Гальванические покрытия в машиностроении: справочник / под ред. М. А. Шлугера. – М.: Машиностроение, 1985. – 240 с.
3 Ильин, В.А. Краткий справочник гальванотехника. – С.-П.: Палитехника, 1993. – 256 с.
4 Оборудование цехов электрохимических покрытий. / Я. В. Вайнер, М.А. Дасоян. – Л.: Машиностроение, 1971. – 288 с.
5 Оборудование гальванических цехов. / Я. В. Вайнер, Б. П. Кушнарев. – Л.: Машиностроение. – 125 c.
6 Грилихес, С. Я. Обезжиривание, травление и полирование материалов. – М.: Гальванотехника и обработка поверхности, 1994. – 190с.
7 Гамбург, Ю. Д. Мир материалов и технологий: гальванические покрытия. Справочник по приминению. – М.: Техносфера, 2006. – 215 с.
8 Когановский, А. М. Очистка и использование сточных вод в промышленном водоснабжении – М.: Химия, 1983. – 288 с.
9 Комплекс документов на групповой технологический процесс цинкование с бесцветным хроматированием (АГЛ-232).
10 Гибкие автоматизированные гальванические линии: справочник / Под ред. В.Л. Зубченко. – М.: Машиностроение, 1989. – 672 с.
11 Виноградов, С.С. Экологически безопасное гальваническое производство. / Под ред. проф. В. Н. Кудрявцева. – М.: Производственно-издательское предприятие «Глобус», 1998. – 302 с.
12 Единая система защиты от коррозии и старения. Покрытия металлические и неметаллические неорганические. Методы контроля: ГОСТ 9.302–88. – М.: Изд-во стандартов, 1989. – 53 с.
13 Единая система защиты от коррозии и старения. Покрытия металлические и неметаллические неорганические. Общие требования: ГОСТ 9.301–86. – М.: Изд-во стандартов, 1988. – 20 с.
14 Покрытия металлические и неметаллические неорганические. Общие требования и методы контроля: СТП 202-790-2001.
15 Инструкция «МЗКТ» № 52684.54578.00035 по линии «Цинкование с бесцветным хроматированием».
16 Коротин, А.И. Технология нанесения гальванических покрытий: Учеб. пособие для сред. проф.-техн. училищ. – М.: Высш. шк., 1984. – 200с.
17 Прикладная электрохимия / Под ред. А.П. Томилова – М.: Химия, 1984. – 520 с.
18 Основное оборудование электрохимических производств: Учеб. пособие по курсу «Оборудование и основы проектирования электрохимических производств» для студентов специальности 1-48 01 04 «Технология электрохимических производств» / Н. Л. Смоляг, И. М. Жарский. – Минск: БГТУ, 2004. – 83 с.
ПРИЛОЖЕНИЕ Г
1 – ванна обезжиривания, 2 – ванна горячей промывки, 3 – ванна холодной промывки, 4 – ванна хромирования (также в ней производят нагрев и активацию), 5 – ванна холодной промывки, 6 – ванна горячей промывки, 7 – выпрямитель ВАКР 630, 8 – выпрямитель ВАКР 3200, 9 – монтажный стол.
ПРИЛОЖЕНИЕ Б
Детали для нанесения хрома
Рисунок 1.1 – Валик
Рисунок 1.2 – Фланец
Рисунок 1.3 – Стакан
ПРИЛОЖЕНИЕ В
Ванна холодной промывки
ПРИЛОЖЕНИЕ Г
Ванна химического обезжиривания
ПРИЛОЖЕНИЕ Д
Подвеска для нанесения хрома
Дата добавления: 2019-09-13; просмотров: 664; Мы поможем в написании вашей работы! |
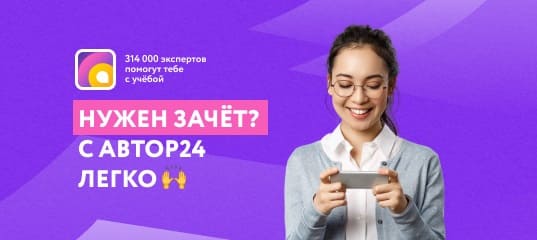
Мы поможем в написании ваших работ!