Анализ причин брака и контроль качества продукции
Контроль деталей после нанесения покрытия:
– контроль внешнего вида (контролируются 100% деталей);
– контроль размера (контролируются 100% деталей микрометром ГОСТ 6507-90);
– контроль толщины покрытия производится на 3–4 деталях от партии магнитным толщиномером марки МТ-41НЦ;
– контроль прочности сцепления производится методом нагрева 1 раз в неделю на 1–2 деталях в камере обезводораживания. Параметры процесса: Т = 200˚С, τ = 90–120 мин.
Получение доброкачественного хромового покрытия зависит от правильности выполнения подготовки поверхности перед покрытием, расположения деталей и анодов в ванне, соблюдения режима электролиза и сохранения в процессе электролиза заданного состава электролита. Виды брака, которые могут возникнуть при нанесении хромового покрытия на сталь, представлены в таблице 1.4.
Таблица 1.4 – Основные неполадки при хромировании
Характерные дефекты | Причина дефекта | Способ устранения | ||
Хром не осаждается на детали | 1. Плохой контакт детали с подвеской | 1. Улучшить контакт | ||
2. Детали экранируют друг друга | 2. Изменить расположение деталей | |||
3. Мала плотность тока | 3. Увеличить силу тока | |||
4. Высокая температура электролита | 4. Снизить температуру электролита | |||
Хром не осаждается даже в малых углублениях | 1. Избыток Н2SO4 | 1. Ввести в электролит BaSO4 | ||
2. Наличие в электролите железа более 8% | 2. Заменить электролит | |||
Неравномерное покрытие (подгар) на одних частях и отсутствие покрытия на других | 1. Образование пленки хроматов свинца на отдельных анодах | 1. Очистить аноды стальной щеткой или погрузить аноды в раствор, содержащий 100 г/дм3 сегнетовой соли и 80 г/дм3 NaOH | ||
Покрытие матовое, трудно полируется
| 1. Недостаток хромового ангидрида | 1. Добавить хромовый ангидрид | ||
2. Велика плотность тока | 2. Снизить плотность тока | |||
На покрытии коричневые пятна | 1. Недостаток Н2SO4 | 1. Добавить Н2SO4 | ||
2. Избыток трехвалентного хрома | 2. Проработать электролит при большей анодной поверхности | |||
Отслаивание покрытия | 1. Значительное наводораживание или плохая подготовка поверхности | 1. Улучшить поверхностную подготовку | ||
2. Перерыв в подаче тока | 2. Исключить перерывы тока | |||
3. Детали изготовлены из сплавов с большим содержанием хрома | 3. Заменить детали | |||
4. Недостаточность обезжиривания и декапирования | 4. Удалить старое покрытие | |||
Покрытие пятнистое | 1. Окисление никелевого подслоя | 1. Декапировать детали в 51% растворе НCl | ||
2. Изделие плохо прогрето в электролите | 2. Выдержать детали в электролите без тока | |||
3. Перерыв тока в процессе хромирования | 3. Устранить перерыв в работе | |||
На выступающих частях изделия утолщение покрытия | 1. Недостаточное ( или отсутствие) экранирования | 1. Усилить экранирование деталей | ||
Непокрытие хромом внутренней поверхности деталей | 1. Неправильно смонтированы дополнительные аноды | 1. Устранить дефекты монтажа деталей на приспособлении | ||
Крупные поры в покрытии | 1. Раковины и поры в основном металле | 1. повысить качество механической подготовки поверхности (шлифования) |
Детали с некачественным покрытием отправляются на переделку.
|
|
Обоснование расхода материалов и энергоресурсов
При нанесении покрытия расходуются аноды и химикаты, составляющие электролиты. Удельные нормы расхода растворимых анодов рассчитывается на 1 м2 покрываемой поверхности при толщине покрытия 1 мкм. Расход химикатов в гальванических ваннах связан с уносом электролита при загрузки и выгрузке деталей, потерями при фильтрации, уносом вентиляцией. Удельные нормы расхода химикатов рассчитываются независимо от толщины покрытия. При расчете норм расхода материала на покрытие мелких деталей в барабанах, удельные нормы расхода следует увеличить в 1,5–2 раза. Нормы расхода химикатов на автоматических линиях устанавливаются опытным путем. Расходы вспомогательных материалов устанавливаются в зависимости от специфики производства.
|
|
Нормы расхода материалов на подготовительные (обезжиривание, травление) и специальные операции (осветление, пассивирование, оплавление и др.) рассчитывают только на 1 м2 обрабатываемой поверхности изделий.
Нормы расхода анодного металла (сплава) устанавливают исходя из толщины слоя покрытия (1 мкм) с учетом технологических отходов и потерь.
В случае механической и электрохимической полировки слоев при нанесении многослойных покрытий следует учитывать увеличение толщины каждого покрытия на 2–3 мкм.
Нормы расхода материалов для деталей простой и сложной формы рассчитывают отдельно. К деталям сложной конфигурации относятся детали с глухими отверстиями, вытяжкой, с внутренней резьбой, а также детали типа стаканов, коробок, муфт и т. д.
Расход материалов определяется исходя из норм расхода материалов на операции гальванопокрытий, представленных в таблице 1.5.
Таблица 1.5 – Удельные нормы расхода материалов на линии хромирования стали
Материал | Норма расхода, г/м2 | Расход, кг | ||
NaOH | 12 | 0,053 | ||
Na2CO3 | 12 | 0,053 | ||
Na3PO4 | 12 | 0,053 | ||
CrO3 | 348 | 1,54 | ||
H2SO4 | 0,5 | 0,002 | ||
Аноды свинцовые | 35 | 0,1561 | ||
Примечание – Расход (кг) рассчитан на одну деталь с поверхностной площадью равной 0,42 м2
|
Изм.
Лист
№ докум.
Подпись
Дата
Лист
1
БГТУ 02. 00. ПЗ
Разраб.
Жилянина А. В.
Провер.
Дроздович В. Б.
Н. Контр.
Утверд.
Дроздович В. Б.
Характеристика основного и вспомогательного оборудования
Лит.
Листов
10
2 Характеристика основного и вспомогательного оборудования БГТУ 41606007, 2010
Для подготовки поверхности применяется оборудование для механической, химической и электрохимической обработки.
Применение средств автоматизации в гальванических цехах приводит к значительному снижению трудоемкости работ по нанесению покрытий и резкому повышению производительности труда, а также значительному улучшению качества гальванических покрытий. Автоматические линии оснащаются приборами контроля, управления и регулирования процессов осаждения металлов, управления источниками тока, выпрямителями и др.
Все оборудование гальваноцехов можно разделить на основное и вспомогательное. К основному относятся гальваническое оборудование, непосредственно проводящее обработку деталей. К вспомогательному оборудованию относят фильтрпрессы, насосы, вентиляторы, емкости для приготовления и хранения электролитов.
Основное оборудование
Ванны – емкости, содержащие рабочие растворы, в которых выполняются подготовительные, основные (процессы покрытия) и заключительные операции химической или гальванической (электрохимической) обработки поверхности деталей, являются основным видом оборудования гальванических цехов и участков.
Применяемые в гальванических цехах ванны принято разделять по способу загрузки на два вида:
– ванны ручной загрузки (стационарные);
– ванны с механизированной загрузкой.
Ванны представляют собой сварные прямоугольные емкости, футерованные для большинства сред и снабженные опорами-ловителями. Футеровка внутренних поверхностей металлических корпусов гальванических ванн химически стойкими материалами выполняет двоякую роль: защищает стенки ванн от разрушения при воздействии растворов и препятствует прохождению тока по корпусу ванны.
Для этой цели применяют винипласт, пластикат. Лучшим футерующим материалом является винипласт. Он обладает высокой химической стойкостью к электролитам и имеет высокую механическую прочность. Футеровку винипластом производят различными приемами: сваривают листы непосредственно в ванне или делают сварную футеровку вне ванны. Последний способ наиболее надежен. Пластикат обладает почти такой же химической стойкостью, что и винипласт, однако он отличается от винипласта пластичностью и более низкими механическими свойствами.
Пластикат прилегает к металлической поверхности ванны лучше, чем винипласт, поэтому во многих случаях целесообразнее использовать именно его. Футерованные ванны установлены для подготовительных операций (травление, обезжиривание, пассивация) и для основных процессов (осаждение покрытия).
Конкретный состав узлов ванны зависит от ее назначения. Все ванны снабжены штуцерами для залива и слива электролита, карманами для слива загрязненных растворов, при необходимости – системой вентиляции, нагревательные приборы, устройства для перемешивания. Ванны устанавливают на кислотостойкую плитку, которая является изолятором.
Длина ванны должна быть с небольшим припуском на интервалы между подвесками. Длина всех ванн длительной обработки одной линии должна быть одинаковой. В зависимости от назначения ванн применяются различные типы корпусов. Корпуса ванн, предназначенных для холодной и горячей промывки, химического и электрохимического обезжиривания изготавливают с карманом (служит для слива верхнего сильно загрязненного слоя жидкости).
Сталь является наиболее распространенным материалом для изготовления ванн. Для изготовления корпусов ванн холодной промывки, активации, хромирования, улавливания, осветления применяют сталь марки Ст-3. Внутренние стенки футеруют винипластом или пластиком. В процессах электрохимического и химического полирования в концентрированных кислотах ванны изготавливают из коррозионностойкой хромоникелевой стали марки Х18Н8 или Х18Н10.
К ваннам предъявляется ряд общих требований: герметичность, отсутствие химического взаимодействия раствора с корпусом ванны, поддержание теплового режима, удобство и безопасность обслуживания и др.
Внутренние размеры ванн зависят от размеров покрываемых деталей, требуемой производительности гальванической линии. На выбор внутренних размеров ванн также оказывает влияние число электродных рядов и расстояние между ними. На практике наибольшее распространение получили электролитические ванны с тремя или пятью электродными рядами, имеющие соответственно 2 анодные и 1 катодную или 3 анодные и 2 катодные штанги. От расстояния покрываемой детали до анода зависит качество и толщина покрытия. [5]
Ванна для элекрохимического обезжиривания имеет стальной корпус с теплоизоляцией. Внутри ванны установлены змеевик, преднозначенный для подогрева раствора паром. Ванна имеет карман, предназначенный для слива раствора в процессе обезжирования деталей. Загрязненный раствор из кармана самотеком поступает в емкость, где электролит хранится до поступления на очистку. Для полного опорожнения ванны в нижней ее части имеется сливной штуцер, в сторону которого днище имеет уклон.
На бортах ванны по центру закреплены две токовые опоры для установки латунной штанги с обрабатываемой деталью и четыре опоры по краям ванны для установки двух анодных медных штанг, смонтированными на бортах ванны. Штанги устанавливаются на изоляторах. Опоры подключаются к выпрямительному агрегату.
Ванна для химического обезжиривания имеет стальной корпус, футированный внутри пластиком. Внутри ванны установлены змеевик, служащий для подогрева раствора паром. Для полного опорожнения ванны в нижней части ее имеется сливной штуцер, в сторону которого днище имеет уклон. На бортах ванны закреплены две опоры для установки штанги с обрабатываемой деталью.
Для травления поверхности деталей используют стационарные ванны с кислотостойкой футеровкой стенок, дна. Эти ванны в зависимости от состава раствора изготавливаются из низкоуглеродистой или коррозионно-стойкой стали.
Ванны травления имеют, как правило, одну штангу, на которую устанавливают приспособления с деталями.
Ванна для тепловой промывки имеет стальной корпус. В ванне имеется змеевик для подогрева воды паром, водоподвод холодной воды. Для полного опорожнения ванны в нижней части ее имеется сливной штуцер, в сторону которого днище имеет уклон. Для слива воды в процессе мойки в ванне имеется карман со штуцером. На бортах ванны закреплены две опоры для установки штанги с обрабатываемой деталью.
Ванна для холодной промывки имеет стальной корпус. Ванна имеет водоподвод для подвода холодной воды. Для слива воды в процессе мойки в ванне имеется карман со штуцером. Для полного опорожнения ванны в нижней части ее имеется сливной штуцер, в сторону которого днище имеет уклон. На бортах ванны закреплены две опоры для установки штанги с обрабатываемой деталью. Эскиз ванны приведен в приложении Б.
В процессе нанесения покрытий предусматривается промывка деталей после каждой операции для удаления с их поверхности переносимого раствора. Лучший результат достигается применением перемешивания воды (на заводе перемешивание осуществляется вручную веслом или путем качания подвески с изделиями в ванне). Таким образом можно промывать детали, имеющие пазы, щели, углубления.
На заводе используется объемный способ промывки, а именно прямоточная промывка с параллельной подачей воды (одноступенчатая). Достоинства этого способа: высокая эффективность и низвая потребность в высококвалифицированном персонале и автоматизаци производства. Недостатки: большой расход воды и низкая концентрация компонентов в стоках.
Ванна для электрохимической обработки имеет стальной корпус. Для нагрева раствора на боковой стенке смонтирован змеевик. Внутри ванна футерована винипластом. На бортах ванны установлены две анодные штанги. В нижней части ванны имеется сливной штуцер, в сторону которого днище имеет уклон, для полного опорожнения ванны. На бортах ванны установлены две токовые опоры. Анодные штанги и токовые опоры подключаются к выпрямительному агрегату. Эскиз ванны приведен в приложении В.
Сушка после процесса хромирования осуществляется естественным путем на монтажном столе цехового изготовления.
Автоматические гальванические линии. Выделяют следующие виды автоматических линий:
– Кареточные автоматические линии с жёстким циклом
Кареточные линии состоят из ванн, расположенных в порядке выполнения операций технологического процесса и, как правило, в два ряда по овалу, а также из сушильной камеры. Вертикальное перемещение каретки производится путем подъёма и опускания подъемного моста, а горизонтальное перемещение тележек – толкающими штангами или цепью механизма горизонтальною перемещения.
– Автооператорные автоматические линии с программным управлением
В автооператорных линиях маршрут переноса деталей и длительность их пребывания на каждой позиции задаются технологически, однако перемещение самого автооператора не совпадает с последовательностью технологических операций и носит челночный характер. В зависимости от требуемой производительности в составе линии может быть несколько автооператоров, имеющих свои зоны обслуживания. Зоны обслуживания автооператоров перекрываются на одну, реже на несколько позиций. Каждый автооператор обслуживает не более 7–8 ванн. Перенос подвески с деталями производится по заданной технологической схеме в соответствии с программой при помощи сигналов, поступающих от системы управления. В большинстве автоматических линий с программным управлением предусмотрена система ручного управления процессом, в этом случае автоматическая линия превращается в механизированную линию.
Отличительными особенностями автооператорных линий являются:
– движение деталей в процессе обработки, как в прямом, так и обратном направлениях;
– ванны и другие позиции обработки могут располагаться не в последовательности выполнения технологических операций;
– возможность осуществления нескольких одноименных операций на одной технологической позиции;
– наличие независимых транспортирующих органов с индивидуальными приводами перемещения и подъема-опускания;
– отсутствие жесткой связи между грузозахватным элементом транспортирующего органа (автооператора) и подвеской с обрабатываемыми деталями;
– наличие устройства программного управления.
Автоматическая гальваническая линия АЛГ-35М предназначена для цинкования стальных деталей в барабанах. Принцип действия линии состоит в следующем. Над ваннами, расположенными согласно циклограмме, по рельсовому пути перемещаются два оператора портального типа, которые транспортируют барабаны с позиции на позицию согласно технологическому процессу. Управление автооператорами автоматическое, осуществляется с пульта управления. В период наладки при необходимости возможно ручное управление. Загрузка и выгрузка производится с одного конца линии.
Автоматическая линия представляет собой однорядно расположенные ванны, установленные на бетонное основание, и состоит из технологических ванн, загрузочной стойки, сушильной камеры, буферных и запасной емкости, командоаппарата, двух автооператоров и площадки обслуживания. [5]
Автооператоры. Перенос деталей из одной ванны в другую осуществляется с помощью автооператоров, которые оснащены автономными системами и которые могут располагаться как сверху, так и сбоку от гальванической линии. Однако помимо подъема-опускания и переноса груза автооператор выполняет следующие функции:
– многократное окунание обрабатываемых деталей;
– передача силового тока к приводам барабанных электролизеров для их вращения в момент подъема и нахождения над технологическими позициями;
– извлечение и транспортировка анодов для чистки;
– встряхивание груза для удаления с его поверхности остатков раствора.
Автооператоры бывают расцепляемые и нерасцепляемые. Расцепляемые автооператоры могут отделяться от штанги, несущей технологические спутники, и при этом переместиться на другие позиции для выполнения определенных операций. Нерасцепляемые автооператоры целесообразно использовать тогда, когда продолжительность процесса невелика, т.е. времени, необходимого для совершения автооператором других действий, недостаточно.
По способу транспортировки технологических спутников автооператоры делятся на несколько групп: консольные, подвесные, портальные.
Консольные автооператоры устанавливаются сбоку от гальванической линии, что не допускает попадания в ванны смазки, используемой для улучшения работы автооператора. Достоинствами таких автооператоров является:
– надежность,
– удобство монтажа и эксплуатации,
– возможность их установки в помещениях с низкими потолками.
К недостаткам относится:
– низкая грузоподъемность (не выше 200 кг);
– свободное обслуживание ванн только с одной стороны;
– нечёткая стабилизация груза при перемещении;
– длина ванн не больше 1,6 м.
Использование подвесного автооператора обеспечивает свободный доступ к ваннам и трубопроводной аппаратуре, такие линии занимают небольшие производственные площади. Но использование подвесного автооператора связано с большой высотой линии, необходимостью устанавливать специальные площадки обслуживания автооператора, с большой металлоемкостью линии в целом за счет необходимости подвески ходовых путей.
Портальные автооператоры, перемещающиеся по направляющей, расположенной по обе стороны ванн и закрепленных на стойках, обладают:
– повышенной устойчивостью вследствие жесткости конструкции;
– большой грузоподъемностью;
– малой высотой линии;
– удобством в обслуживании автооператора.
Главные недостатки линии с портальным автооператором:
– затруднённость обслуживания ванн;
– необходимость частичного или полного демонтажа рельсовых путей при извлечении ванн для ремонта;
– затрудненный подход трубопроводной аппаратуре;
– дополнительное усложнение конструкции линии из-за введения устройств, обеспечивающих безопасность обслуживающего персонала;
– более быстрое коррозионное разрушение автооператоров вследствие близости их к зеркалу растворов;
– усложнение конструкций приводов горизонтального передвижения автооператоров.
Автомат портального типа представляет собой модель с потолочным транспортером, где рабочие шины крепятся к каркасу портального типа. Транспортеры осуществляют транспортировку оборудования для выкладки изделий через отдельные технологические ступени в соответствии с используемой технологией. В качестве устройств для выкладки изделий могут служить каркасы, барабаны или корзины. Автомат выполнен как автомат с одинарной линией. Загрузка и выгрузка осуществляется совместно с торцевой стороны автомата. Используемые аппараты имеют внутреннюю облицовку в соответствии с используемым по технологии раствором, специальная система окраски предохраняет внешнюю сторону от коррозии. Подвод питания к автооператору осуществляется через гибкий кабель, проложенный в металлорукаве.
Штанга для электрохимической обработки предназначена для транспортирования подвесок с обрабатываемыми деталями. Штанга состоит из двух шин, двух цапф, которыми штанга ложится на опоры, установленные на бортах ванн и трех кронштейнов, с помощью которых транспортируют штангу.
Козырек изготовлен из винипласта и предназначен для закрытия промежутка между ваннами с целью исключения попадания растворов на пол.
Площадка обслуживания состоит из отдельных секций и лестниц, изготовленных из уголков и облицованных сверху рифленым железом, а сбоку листами из тонколистовой стали. Секции и лестницы скреплены между собой болтами. Для удобства обслуживания и монтажа трубопроводов и арматуры, размещенных под настилом, верхние листы сделаны на петлях и открываются, а боковые снимаются.
В соответствии с требованиями правил техники безопасности площадка обслуживания с внешней стороны имеет перила, изготовленные из труб.
Разводка трубопроводов предназначена для обеспечения технологических режимов и поддержания стабильности технологических параметров воды и растворов в ваннах.
Разводка трубопроводовсостоит из магистральных, подводящих, отводящих трубопроводов воды, пара, воздуха, конденсата, а также из канализации, запорной и регулирующей трубопроводной арматуры, насосов. Магистральные трубопроводы расположены на крюках под площадкой обслуживания вдоль всей линии. Один конец магистральных трубопроводов заглушен, на другом установлены запорные вентили, необходимые для перекрытия подачи воды, пара, воздуха в случае ремонта или временной остановки линии.
На магистральном трубопроводе воздуха, кроме вентиля, установлен регулятор для понижения давления до 0,05–0,1 МПа. Запорная и регулирующая арматура смонтирована на трубопроводах под площадкой обслуживания. Из магистрального трубопровода вода подается ко всем ваннам. К промывочным ваннам подвод воды осуществляется с помощью наливных труб. Это дает возможность промывать детали в более чистой воде, так как свежая вода непрерывно подается в нижнюю зону ванны, а загрязненная удаляется сверху через сливной карман в канализацию. К остальным ваннам подвод воды осуществляется через борт (с помощью индивидуального трубопровода). Регулирование расхода воды осуществляется автоматически. [8]
Вспомогательное оборудование
К вспомогательному оборудованию относятся: источники питания, технологические спутники, устройства нагрева, перемешивания, насосы, вентиляторы, установки и емкости для приготовления или регенерации электролитов, устройства загрузки-разгруки, бортовые отсосы.
Технологические спутники – устройства, в которых закрепляются обрабатываемые детали, последовательно перемещаемые с помощью автооператора или иного транспортирующего устройства по позициям гальванической линии или загружаемые в автономные гальванические модули. В качестве таких устройств могут использоваться подвески, барабаны, колокола, корзины, кассеты и т. д.
Назначение подвесочных приспособлений заключается как в завешивании деталей в ванне, так и в подводе к ним тока.
Корзины применяются в случае необходимости обработки большого количества мелких деталей. Они засыпаются в навал и занимают приблизительно половину объема емкости. Изготавливаются корзины из железной сетки, проволоки, в отдельных случаях из кислотостойких материалов.
В современном электрохимическом производстве применяются два типа подвешивания достаточно крупных деталей: «елочка», «рамка».
«Елочка» представляет собой вертикальный стержень с подвесным крюком, которым она навешивается на штангу ванны. Характерными особенностями «елочки» являются:
– детали одного «этажа» расположены под разным углом к плоскости анода или катода;
– ограниченность размера деталей, висящих на боковых контактах.
«Рамка» представляет собой прямоугольник, вертикальные боковые стороны которого образованы стержнями подвесных крюков. При конструировании такой подвески возможно два варианта расположения стержней внутри рамы – вертикальное и горизонтальное, что определяется в значительной мере условиями монтажа детали. С точки зрения скорости стекания жидкости более выгодно использовать вертикальное расположение. При горизонтальном расположении стержней их лучше изготавливать наклонными в сторону краев подвески, что не только ускорит стекание жидкости и уменьшит ее вынос подвеской, но и позволит избежать падения капель растворов с верхней зоны подвески на детали, находящиеся ниже. Характерными особенностями «рамки» являются:
– все висящие на рамке детали одинаково ориентированы по отношению к анодам;
– возможность сделать ее более вместительной по количеству и площади умещающихся на них деталей.
При выборе конструктивного исполнения подвесочного приспособления и определении оптимального размещения деталей на подвеске необходимо обеспечить:
– максимально возможное число деталей на единице площади подвески с учетом ее веса с деталями и токовой нагрузки на токопроводящие элементы подвески;
– наиболее оптимальный вариант размещения деталей в электрическом поле с точки зрения равномерного распределения плотности тока, создание хорошего контакта с покрываемой деталью и токоподводящей штангой;
– наилучшее расположение деталей и элементов подвески с целью уменьшения переноса жидкостей из ванны в ванну и исключения экранирования мест, подлежащих покрытию. [5]
Некоторые подвески, используемые для хромирования, приведены в приложении Г.
Барабан представляет собой шестигранную винипластовую перфорированную емкость, закрываемую винипластовой крышкой. На каркасе, закрытым винипластовым кожухом, установлен привод вращения барабана. При подъеме барабана автооператором ток для питания электродвигателя привода вращения подается через гибкий кабель от автооператора. Барабан состоит из сварной рамы с цапфами для укладки в ловители ванн и захватов, с помощью которых осуществляется взаимодействие с грузозахватами автооператора. К раме крепятся несущие щеки (неметаллические или металлические с антикоррозионной изоляцией) с фторопластовыми подшипниками, в которых устанавливается вращающаяся шестигранный перфорированный барабан с крышкой и токоподвод. Привод барабана применен в виде индивидуального мотора-редуктора. Для передачи технологического тока обрабатываемым изделиям предусмотрен катодный токоподвод, который связан с источником питания через пластины и втулки на цапфах и далее через опоры-ловители. Для снижения коррозионного воздействия агрессивной среды предусмотрен защитный кожух.
Насосы предназначены для перемещения электролитов. В связи тем что, на линии нанесения покрытия используются агрессивные среды (концентрированные кислоты и щёлочи), то к оборудованию для перекачивания электролитов выдвигаются особые эксплуатационные свойства. Поэтому в данном процессе использую мембранные (диафрагмовые) насосы, которые удовлетворяют этим требованиям. В насосе такого типа имеется мембрана, которая предотвращает соприкосновение агрессивного электролита с плунжером.
Выпрямитель состоит из трансформатора, преобразующего ток высокого напряжения (220 или 380 В) и малой силы в ток низкого напряжения и большой силы, и электрических вентилей, главным образом, на основе тиристоров (селеновых, кремниевых или германиевых), преобразующих переменный ток в постоянный. Выпрямители с селеновыми вентилями имеют большие габариты; германиевые выпрямители вдвое меньше и вдвое легче, но они боятся перегрузок; кремниевые имеют малые размеры и меньше боятся перегрузок. Пробивное напряжение кремниевых вентилей 200–1000 В, тогда как селеновые пробиваются уже при 17 В.
Ванны (кроме ванны хромирования) оснащены источниками постоянного тока ВАКГ-1600, источники тока отдалены от ванн и расположены в конце линии. Охлаждение выпрямителей производится питьевой водой по системе оборотного водоснабжения. Для контроля силы тока и напряжения на ванне на источниках тока имеются амперметр класс точности 2,5 с пределом измерения от 0 до 750 А ГОСТ 8711-93 и вольтметр класс точности 2,5 с пределом измерения от 0 до 30 В ГОСТ 8711-93.
Ванна хромирования оснащена источником постоянного тока ВАКГ-3200. Охлаждение выпрямителей производится питьевой водой по системе оборотного водоснабжения. Для контроля силы тока и напряжения на ванне на выпрямителях установлены амперметр класса точности 1,5 с пределом измерения от 0 до 7,5 кА ГОСТ 8711-93 и вольтметр класс точности 1,5 с пределом измерения от 0 до 30 В ГОСТ 8711-93.
Вентиляция может быть общеобменной, местной и смешанной.
Общеобменная вентиляция обеспечивает компенсацию оттока воздуха, уходящего в вытяжную вентиляцию, и приток свежего воздуха.
Местная вентиляция на гальванических ваннах осуществляется при помощи бортовых и панельных отсосов, а также других устройств, обеспечивающих отвод вредных веществ с зеркала ванны.
Смешанная вентиляция состоит из приточно-вытяжной общеобменной и местной непосредственно в ваннах или установках предварительной подготовки деталей перед покрытием.
Вентиляционные отсосы предназначены для удаления вредных выделений из ванн. Существуют следующие типы местных вентиляционных отсосов: с горизонтальной щелью всасывания, вертикальной щелью всасывания, фильтрующие. Каждый из этих типов подразделяется на двубортовые и однобортовые. В зависимости от агрессивности среды применяются отсосы из винипласта и полипропилена.
Бортовые отсосы с горизонтальной щелью всасывания предназначены для локализации и удаления вредных испарений из электролита при более низких энергетических затратах на вентиляцию.
Фильтрующие бортовые отсосы предназначены не только для удаления вредных испарений, но и одновременной очистки удаляемого воздуха. В качестве фильтрующего материала для улавливания хромового ангидрида используется полипропиленовое волокно, для улавливания серной кислоты – сетку из винипласта.
Для обслуживания линии используются газопылеуловливающая установка АУ-237 типа циклон-промыватель СИОТ №6, газоочистная установка типа фильтр ПГП-И №12.
Нагревательные приборы. Часто для создания оптимального режима протекания процесса необходимо нагревание электролита, что осуществляется с помощью специальных устройств. К ним относятся рубашки, змеевики, тены. Применение рубашек и других нагревательных элементов, находящихся под ванной часто нецелесообразно из-за футеровки ванн различными изоляционными материалами. Однако в условиях повышенной температуры и агрессивности среды нагрев электролита проводят именно с помощью этих устройств.
На предприятии обогрев ведется паром через свинцовый змеевик, расположенный по дну и боковым стенкам ванны.
Изм.
Лист
№ докум.
Подпись
Дата
Лист
1
БГТУ 03. 00. ПЗ
Разраб.
Жилянина А. В.
Провер.
Дроздович В. Б.
Н. Контр.
Утверд.
Дроздович В. Б.
.
Охрана окружающей среды
Лит.
Листов
2
3 Охрана окружающей среды БГТУ 41606007, 2010
Важнейшим мероприятием по защите окружающей среды при производстве гальванопокрытий является очистка сточных вод от химически вредных взвешанных веществ. Очистка стоков обязательна и производится в соответствии с «Правилами охраны поверхностных вод от загрязнения сточными водами». Сточные воды гальванического производства различают по составу загрязнений, режиму сброса и концентрации. Стоки принято разделять на:
– концентрированные;
– низкоконцентрированные.
Содержание вредных веществ должно быть понижено до значения ПДК. Для возможного дальнейшего сброса сточных вод без ущерба для окружающей среды. Для шламов устанавливаются ограничения по степени влажности.
Стоки от гальванического производства принято разделять на три группы:
– кислотно-щелочные (образуются в результате процессов цинкования, никелирования, обезжиривания и т.д.);
– хромосодержащие сточные воды (образуются в результате процессов хроматирования, электрополирования, оксидирования алюминия, пассивирования цинка и т.д.);
– цианосодержащие сточные воды (образуются в результате процессов обезжиривания изделий с одновременным их меднением, а также цанистые ванны нанесения покрытия).
По режиму сброса и концентрации сточные воды делятся на постоянно поступающие разбавленные воды после промывки деталей и периодически сбрасываемые из основных ванн отработанные концентрированные электролиты. Концентрация загрязняющих веществ в отработанных электролитах в 100-1000 раз больше, чем в разбавленных промывных водах, а объемы во много раз меньше.
Основными компонентами загрязнения сточных вод являются высокотоксичные соединения тяжелых металлов и цианиды. Около 40% стоков гальванического производства составляют хромсодержащие сточные воды.
На МЗКТ очистные сооружения находятся в стадии проектирования. Очистные сооружения в термическом цехе должны обеспечивать необходимую степень очистки сточных вод гальванического производства и маслоэмульсионных стоков.
При проектировании очистных сооружений должны учитываться возможные изменения норм ПДК хрома. В проекте должны быть предусмотрены дополнительные финишные фильтры, которые обеспечат необходимую степень очистки, т.е. очистные сооружения должны быть рассчитаны на любые ПДК.
В ближайшие годы ПДК хрома и других веществ значительно не изменятся.
Состав сточных вод гальванического производства, поступающих в городскую канализационную сеть должны соответствовать таблице 3.1.
Таблица 3.1 – Предельно-допустимые концентрации веществ, поступающих в канализационную сеть
Наименование загрязнения | Концентрация, мг/ ![]() |
Взвешенные вещества | 300 |
Сухой остаток | 1000 |
Хлориды | 350 |
Сульфаты | 500 |
Нефтепродукты | 0,9–1,2 |
![]() | 2 |
![]() | 0,4 |
![]() | 0,1 |
![]() | 1 |
![]() | 2 |
![]() | 1 |
Цианиды | Отсутствуют на предприятии |
Свинец | 0,5 |
Hg | 0,5 |
Изм.
Лист
№ докум.
Подпись
Дата
Лист
1
БГТУ 04. 00. ПЗ
Разраб.
Жилянина А. В.
Провер.
Дроздович В. Б.
Н. Контр.
Утверд.
Дроздович В. Б.
Автоматизация и механизация технологических процессов
Лит.
Листов
2
4 Автоматизация и механизация технологических процессов БГТУ 41606007, 2010
Основное направление решения производственных задач является внедрение средств автоматизации. Это необходимо для обеспечения необходимого качества покрытия, а также для уменьшения доли ручного труда в управлении процессом на ваннах. Внедрение автоматизированной системы управления процессом позволяет снизить себестоимости продукции. Улучшение этого экономического показателя чаще всего достигается за счет уменьшения расхода сырья, материалов и энергии на единицу продукции благодаря повышению качества продукции, увеличению производительности оборудования за счет сокращения потерь рабочего времени из-за неплановых остановок процесса, вызванных ошибками управления, более точному поддержанию оптимального технологического режима за счет регулирования основных технологических параметров.
Автоматизированному контролю подвергаются различные параметры технологического процесса: температура, уровень растворов, кислотность.
На качество покрытия влияет точность времени нахождения деталей на каждой операции. Это достигается за счет применения в работе линии автооператора, работающего по циклограмме, построенной в соответствии с технологическим процессом.
Из технологического процесса следует, что необходимо контролировать и регулировать температуру в ванне промывки, электрохимического обезжиривания, хромирования. В ваннах промывки, обезжиривания, активации, хромирования необходимо регулировать и контролировать уровень жидкости.
В ваннах каскадной промывки необходимо регулировать и контролировать расход воды.
В практике регулирования температуры в гальванических линиях находят применение следующие датчики температуры: термопреобразователи сопротивления и электрические, контактные термометры, манометрические термометры.
Наибольшее применение для измерения небольшого диапазона температур (0–100ºС) нашли термометры сопротивления.
В рабочих ваннах необходимо поддерживать такой уровень электролита, чтобы подвеска с деталями всегда была покрыта слоем электролита постоянной толщины, так как изменение этого параметра может влиять на распределение электрических полей в объеме электролита. Точность поддержания уровня составляет, как правило, ± 5 мм.
Причины, вызывающие изменение уровня следующие: вынос электролита с деталями, вынос электролита в бортовые отсосы и его испарение. Для контроля уровня применяют следующие методы: электроконтактный, поплавковый, ультразвуковой, высокочастотный резонансный, емкостной, гидростатический.
Для контроля расхода воды возможно применение ультразвукового расходомера 2WR5.
Изм.
Лист
№ докум.
Подпись
Дата
Лист
1
БГТУ 05. 00. ПЗ
Разраб.
Жилянина А. В.
Провер.
Дроздович В. Б.
Н. Контр.
Утверд.
Дроздович В. Б.
Стандартизация и контроль качества продукции
Лит.
Листов
4
5 Стандартизация и контроль качества продукции БГТУ 41606007, 2010
Стандартизация, контроль и управление качеством покрытий осуществляется в соответствие с ЕСЗКС – единой системой защиты от коррозии и старения.
ЕСЗКС – комплекс взаимосвязанных государственных стандартов, устанавливающий общие для всех видов материалов и изделий требования, правила, нормы и методы по обеспечению защиты от коррозии, старения и биоповреждений на стадиях разработки, производства и эксплуатации.
ГОСТ 9.303-84. Настоящий стандарт устанавливает общие требования к выбору металлических и неметаллических неорганических покрытий деталей и сборочных единиц, наносимых химическими и электрохимическими способами.
ГОСТ 9.301-86. Настоящий стандарт распространяется на металлические и неметаллические неорганические покрытия, полученные электрохимическими и химическими способами, и устанавливает общие требования к поверхности основного металла и покрытиям в процессе их производства и контролю качества основного металла и покрытий.
ГОСТ 9.305-84. Настоящий стандарт устанавливает параметры операций, входящих в технологические процессы получения покрытий, кроме операций подготовки поверхности основного металла и обработки покрытий, производимых механическими способами. Стандарт распространяется на металлические и неметаллические неорганические покрытия, наносимые химическими и электрохимическими способами на детали и сборочные единицы, за исключением деталей из высокопрочных сталей и магнитных сплавов.
ГОСТ 9.101-78. Единая система защиты изделий от коррозии и старения. Основные положения. Настоящий стандарт устанавливает определения, назначение, структуру и состав единой системы защиты изделий и материалов от коррозии, старения и повреждений, правила наименования и обозначения стандартов системы. Устанавливает общие для всех видов материалов и изделий требования, правила и методы по обеспечению защиты от коррозии, старения на стадиях разработки, производства и хранения.
ГОСТ 9.008-82. Единая система защиты от коррозии и старения. Покрытия металлические и неметаллические неорганические. Термины и определения. Настоящий стандарт устанавливает применение в науке, технике и производстве термины и определения основных носителей в области металлических и неметаллических неорганических покрытий, полученных на металле или сплаве. Термины, установленные стандартом, обязательны для применения в документации всех видов, научно-технической, учебной, справочной литературе.
Стандарты на реактивы, используемые на производстве, приведены в таблице 5.1.
Таблица 5.1 – Стандарты на реактивы, используемые в производстве
Амоний сернокислый чистый | ГОСТ 3769-69 |
Ангидрид хромовый технический | ГОСТ 2548-77 |
Бихромат натрия кристаллический | ГОСТ 2651-78 |
Блескообразующая добавка ЩЦ | ТУ РБ 100375899.009-2001 |
Висмут сернокислый | ТУ 6-09-4218-81 |
Калий двухромовокислый | ГОСТ 2652-78 |
Кислота серная аккумуляторная | ГОСТ 667-73 |
Кислота серная техническая | ГОСТ 2184-77 |
Купорос медный | ГОСТ 2142-68 |
Монофосфат цинка | ГОСТ 16992-78 |
Натр едкий технический | ГОСТ 2263-79 |
Натрий азотнокислый технический | ГОСТ 829-77 |
Натрий сернокислый | ГОСТ 6318-77 |
Натрий хлористый | ГОСТ 4233-77 |
Оксид цинка | ГОСТ 20262-73 |
Олово сернокислое | ТУ 6-09-1502-75 |
Препарат ОС-20 | ГОСТ 10730-82 |
Сода кальцинированная | ГОСТ 5100-85 |
Тринатрийфосфат | ГОСТ 201-76 |
Хромин | ТУ 6-02-788-77 |
Этилендиамин технический | ТУ 3494-59 |
Производится контроль внешнего вида покрытия 100 % деталей от партии.
Требования к внешнему виду покрытия. Поверхность полированного покрытия должна быть однородной, блестящей или зеркальной. На механически полированной поверхности покрытия, кроме зеркальной, не являются браковочными признаками единичные волосовидные царапины или точки от полировочных паст и рихтовочного инструмента в количестве не более 5 шт на 100 , заполировка кромок. На поверхности покрытий, если нет специальных указаний вконструкторской документации, не являются браковочными следующие признаки;
– следы механической обработки и другие отклонения, допускаемые нормативно-технической документацией на основной металл;
– незначительная волнистость поверхности покрытия после вытяжки, выявляющаяся после травления;
– темные или светлые полосы или пятна в труднодоступных для зачистки отверстиях и пазах, на внутренних поверхностях и вогнутых участках деталей сложной конфигурации, местах coпряжения неразъемных сборочных единиц в сварных, паяных швах, околошовной зоне.
– неравномерность блеска и неоднотонность цвета;
– следы от потеков воды, хроматирующих и фосфатирующих растворов без остатков солей;
– блестящие точки и штрихи, образовавшиеся от соприкосновения с измерительным инструментом, приспособлениями и от соударения деталей в процессе нанесения покрытий в барабанах;
– изменение интенсивности цвета или потемнение после нагрева с целью обезводороживания и проверки прочности сцепления, снятия изоляции и пропитки.
При осаждении на поверхности детали рядом двух покрытий без изоляции или с применением изоляции, а также при осаждении местных покрытий, если это не влияет на работоспособность изделия, не являются браковочными следующие признаки:
– смещение границ покрытий до 2 мм;
– отдельные точечные включения одного покрытия на поверхности другого; точечные включения металла покрытия на изолируемой поверхности;
– потемнение металла на границе покрытий;
– цвета побежалости на непокрываемых поверхностях. [12]
Требования к толщине покрытия. Превышение максимальной толщины покрытия не является браковочным признаком, если это не влияет на сборку и работоспособность изделия. В отверстиях, пазах, вырезах, на вогнутых участках сложнопрофилированных деталей, на внутренних поверхностях и местах сопряжения неразъемных сборочных единиц допускается уменьшение толщины покрытия до 50%, а для хромовых покрытий – отсутствие, если нет других требовании в конструкторской документации к толщине покрытия на указанных участках. В глухих гладких и резьбовых отверстиях и пазах диаметром (или шириной) до 12 мм и в сквозных гладких и резьбовых отверстиях и пазах диаметром (или шириной) до 6 мм толщина покрытия на глубине более одного диаметра (или одной ширины) не нормируется; допускается отсутствие покрытия, если в конструкторской документации не указаны требования к толщине покрытия на этих участках.
Контроль толщины хромового покрытия на Минском заводе колесных тягачей выполняется методом прямого измерения, который заключается в определении размеров детали до и после нанесения покрытия. Для измерений используют микрометр. Микрометр позволяет измерять только значительные толщины покрытий, т.к. погрешность измерений достигает ±10 мкм.
Остальные покрытия контролируются капельным методом. На испытуемый участок покрытой детали наносят с помощью пипетки капли растворителя, выдерживая каждую определенное время (0,5–1 мин), с определенной скоростью и падающего на поверхность покрытия под углом 45°. При определении капельным методом толщина покрытия рассчитывается исходя из количества капель, нанесенных на одно и то же место, до обнажения основного металла при данной температуре. Предварительно устанавливается толщина слоя, растворяемого одной каплей в течение 0,5 или 1 мин в зависимости от температуры.
Покрытие должно быть прочно сцепленным с основным металлом. Контролируется методом нанесения сетки царапин. Используется для определения прочности сцепления покрытий толщиной до 20 мкм. На поверхность контролируемого покрытия острием наносят 4–6 параллельных линий глубиной до основного металла на расстоянии 2–3 мм друг от друга и столько же линий, перпендикулярных к ним. Линии проводят в одном направлении. [10]
Изм.
Лист
№ докум.
Подпись
Дата
Лист
1
БГТУ 06. 00. ПЗ
Разраб.
Жилянина А. В.
Провер.
Дроздович В. Б.
Н. Контр.
Утверд.
Дроздович В. Б.
.
Техника безопасности и охрана труда
Лит.
Листов
5
6 Техника безопасности и охрана труда БГТУ 41606007, 2010
Все работающие в гальванических цехах в большей или меньшей степени имеют дело с применением многочисленных веществ, которые при вдыхании или попадании на участки кожи причиняют отравления, ожоги и различные травмы. Большое количество промывочных ванн с горячей и холодной водой создаёт в помещениях повышенную влажность.
Операции механической подготовки поверхности характеризуются повышенной запыленностью металлической пылью, повышенным уровнем вибрации и шума. При химических методах подготовки поверхности применяются различные растворители, горячие щелочные растворы.
Процессы приготовления электролитов, нанесения и обработки хромовых покрытий также характеризуются широкой гаммой применяемых химикатов. Это хромовый ангидрид, щелочи, кислоты, и другие вредные вещества, воздействие которых на организм человека может привести к отравлениям и профессиональным заболеваниям. Воздействие химических веществ на работающих зависит от физико-химических свойств, агрегатного состояния, класса опасности веществ, а также от времени и характера их воздействия и путей поступления в организм.
Наряду с химическими опасными и вредными факторами технологический процесс нанесения гальванопокрытий характеризуется наличием физических вредных факторов (шум, вибрация, ультразвук, электрический ток), пожаро- и взрывоопасности.
Участок гальваники характеризуется повышенной опасностью поражения электрическим током, получения ожогов от концентрированных кислот, а также получения травм от движущихся механизмов.
Химически опасные и вредные вещества, используемые в цехе, по степени воздействия на организм человека подразделяются на три класса:
Первый класс – вещества чрезвычайно опасные (хромовый ангидрид);
Второй класс – вещества высокоопасные (серная кислота, азотная кислота, ортофосфорная кислота, натр едкий);
Третий класс – вещества умеренно опасные (окись цинка);
Четвертый класс – вещества малоопасные (окись углерода, аммиак 25% водный раствор).
Хромовый ангидрид пожаро- и взрывоопасен, токсичен, гидроскопичен (увлажняется на открытом воздухе). При соприкосновении с горючими веществами может вызвать загорание и взрыв, поэтому транспортирование и хранение с легковоспламеняющимися и горючими веществами не допускается. Хромовый ангидрид вредно действует на органы дыхания, зрения и кожные покровы. Хранить его следует в изолированном отделении огнестойкого склада.
Серная кислота обугливает органические вещества, разъедает кожу, оказывает коррозионное действие на металлы. Перевозят серную кислоту со склада в цех в закрытой металлической емкости из нержавеющей стали, которая должна полностью закрываться и исключать расплескивание кислоты при перевозке, должно иметь удобный слив кислоты. Содержат серную кислоту в стеклянных бутылях с плотно закрытыми стеклянными притертыми пробками в изолированном отделении огнестойкого склада в месте с другими кислотами.
Азотная кислота и ее пары ядовиты, оказывают вредное действие на органы дыхания, зрения и кожные покровы. Азотная кислота является окислителем, при попадании на упаковочный материал – деревянную стружку, опилки или солому может вызвать воспламенение. Оказывает коррозионное действие на металлы. Азотная кислота для транспортирования и хранения помещается в стеклянные бутыли, на которые наносят несмываемой краской обозначения: «Огнеопасно», «Едкая жидкость». Хранят также в изолированном отделении огнестойкого склада вместе с другими минеральными кислотами.
Ортофосфорная кислота является едким веществом, при попадании на кожу вызывает химические ожоги. При работе с кислотой следует беречь глаза, кожу, и органы пищеварения от попадания кислоты. Кислоту хранят в проветриваемом закрытом помещении склада отдельно от аммиака.
Едкий натр представляет собой едкое вещество, которое, попадая на кожу, вызывает химические ожоги. При систематическом воздействии на кожу вызывает образование язв и экзем. Едкий натр требует осторожного обращения и применения, санитарных мер защиты органов дыхания, зрения и кожных покровов. Технический едкий натр твердый упаковывают в барабаны из черной кровельной стали, которые герметично закрывают крышкой с резиновыми прокладками. Едкий натр хранят в общих складских помещениях с естественной вентиляцией в условиях, исключающих попадания на тару влаги.
Не допускается попадание оксида цинка внутрь организма. Оксид цинка упаковывают в трехслойные бумажные пакеты и хранят в крытых складских помещениях.
В гальванических цехах при наличии высокой влажности паров кислот и щелочей происходит ускоренное старение изоляции электропроводов, что может вызвать короткое замыкание и загорание проводов, поэтому в установленные сроки следует производить профилактический ремонт всего электрооборудования цеха.
Воздействие опасных и вредных химических веществ на работающих зависит от физико-химических свойств вещества, времени и характера воздействия и путей поступления в организм. Предельно допустимые концентрации (ПДК) вредных веществ в воздухе рабочей зоны приведены в таблице 4.1.
При одновременном выделении паров нескольких вредных веществ их суммарная концентрация не должна превышать концентрации наиболее вредного газа.
Основными мероприятиями по предотвращению воздействия вредных факторов являются автоматизация и герметизация процессов источников вредных и опасных производственных факторов, механизация и автоматизация производства с ручным трудом, замена токсичных горючих веществ менее токсичными и негорючими веществами.
Таблица 4.1 – Предельно допустимые концентрации паров, газов и ядовитых пылей в воздухе рабочей зоны.
Вредные вещества | ПДК, мг/ ![]() | Агрегатное состояние |
Аммиак | 20 | П |
Ацетон | 200 | П |
Одноокись углерода | 20 | П |
Окислы азота (в пересчете на NO) | 5 | П |
Окись цинка | 6 | А |
Серная кислота | 1 | А |
Сернистый ангидрид | 10 | П |
Сероводород | 10 | П |
Сероуглерод | 10 | П |
Формальдегид | 0,5 | П |
Фосген | 0,5 | П |
Фтористый водород | 0,5 | П |
Хлористый водород | 5 | П |
Хромовый ангидрид | 0,01 | А |
Цианистый водород | 0,3 | П |
Этиловый спирт | 1000 | П |
Примечание: А – аэрозоли, П – пары или газы. |
Полностью исключить воздействие вредных факторов на работающих не представляется возможным, так как технический уровень современного производства для этого недостаточно высок. Но ограничить их до допустимых уровней возможно. Это достигается за счет внедрения различных видов защиты, устройства и реконструкции установок различного назначения.
Для обеспечения безопасности труда работающих на гальваническом участке предусмотрен ряд мероприятий – это система электробезопасности, ограждений, защитных кожухов, средств пожаротушения. Кроме этого, основным мероприятием является автоматизация процесса, что исключает контакт рабочего с зонами повышенной опасности, а также с вредными производственными факторами.
Одним из опасных факторов при электрохимическом производстве является электрический ток. Поражение электрическим током характеризуется потерей сознания, мгновенным появлением судорог, ослабленной или полной остановкой сердечной деятельности и дыхания. Наиболее опасным для человека считается переменный ток частотой 50–60 Гц, силой 0,1 А и напряжением свыше 250 В. С целью исключения поражения человека электрическим током оборудование цех должно быть изолировано от других металлических конструкций, изолированы катодные и анодные токоподводы, электропроводящие шины должны быть расположены в местах, недоступных для случайного прикосновения и покрыты устойчивым лаком или краской. Кроме того, все токоведущие части электрических приборов обязательно заземляются, а при работе с электрооборудованием не допускать, чтобы рабочий стоял на влажном или металлическом полу. Производственные помещения снабжаются песком, огнетушителями, шерстяные и асбестовые одеяла.
При возникновении пожара необходимо помнить, что установки под напряжением разрешается тушить углекислым огнетушителем ОУ-5 и запрещается тушить огнетушителем ОХВП-10.
Дата добавления: 2019-09-13; просмотров: 234; Мы поможем в написании вашей работы! |
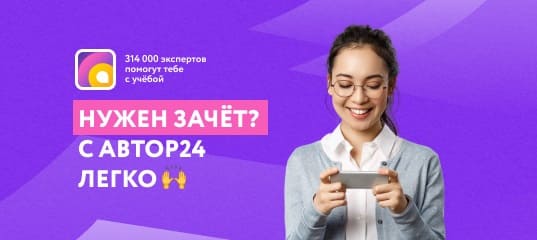
Мы поможем в написании ваших работ!