СИСТЕМЫ ДИАГНОСТИРОВАНИЯПРИМЕНЯЕМЫЕ В ЛОКОМОТИВНОМ
ХОЗЯЙСТВЕ ЖЕЛЕЗНЫХ ДОРОГ
5.1. Приборы, регистрирующие сигналыакустической эмиссии (ИРП-12, Contest )
Сигналы акустической эмиссии возникают в металлических деталях при пластических деформация металла.5.2. Индикатор ресурса подшипника ИРП-12(ЗАО МЕТАКОМ)
Назначение: контроль технического состояния подшипника качения на основе акустической эмиссии в диапазоне ультразвуковых частот 20-300 кГц работающего подшипника.
Минимальное число оборотов 5 об/мин, максимальное - не ограничено.Время диагностирования одного узла до 1 мин.
Основные источники формирования акустико-эмиссионного сигнала в ультразвуковом диапазоне частот эксплуатируемого подшипникового узла:
- упругие волны от нормальных и касательных напряжений пятен контакта в поверхностных
слоях тел и дорожек качения при вращении от действующих нагрузок и чисел оборотов;
- микроудары вследствие шероховатости поверхности тел и дорожек качения, усиливающиеся из-за коксования масла и наличия продуктов износа;
- гидродинамические эффекты от смазки в зоне контактных напряжений тел качения с дорожками качения;
- импульсивный сигнал от образования трещин в металле тел качения;
- микроудары и удары от перекатывания дефектных поверхностей (шелушение, развитие трещин, сколы, раковины);
- микротрещины наружного кольца в гнезде корпуса;
- износ посадочных мест подшипника, сопровождаемый скользящими перемещениями поверхности колец относительно посадочных
мест;
|
|
- проскальзывание тел качения по дорожкам качёния. Наиболее информативный диапазон частот акустико-эмиссионного сигнала 30-300 кГц. На этих частотах влияние импульсов от работающих узлов минимально, что позволяет осуществлять диагностику с надёжностью более 0,9. Амплитуды сигнала возрастают с увеличением нагрузок и числа оборотов механизма.
Влияние незакоксованной смазки на амплитуду сигнала двояко:
- отсутствие смазки увеличивает амплитуду;
- «подбивка» консистентной смазки или восстановление режима жидкой смазки уменьшает
амплитуду.
Зависимость между техническим состоянием и показанием дисплея D прибора от времени работы при номинальной нагрузке подшипника
На рисунке:
Ах - подшипник собран с соблюдением технологии сборки;
А2 - Необходимо проверить сборку;
А3- решение принимается комиссионно.
Если дефекты смазки и монтажа отсутствуют, то точки тренда соответствуют следующим состояниям подшипника: , Dm
Качество монтажа и конструктивных элементов подшипникового узла Dm =6,3-0,4Da.
А.
Накопление усталостных микротрещин в поверхностном и приповерхностном слоях тел и дорожек качения приводят к появлению микровыкрашиваний. W' Участок А-В.
|
|
Развитие поверхностных трещин, мелких выкрашиваний, зарождение пятен выкрашивания на телах и дорожках качения.
Участок В-С.
Развитие трещин на телах и дорожках качения, приводящих в дальнейшем к выкрашиванию металла с образованием раковин, начало интенсивного износа сепаратора, рост пятен выкрашивания.
Участок C-D.
Образование мелких раковин, возможен усталостный износ сепаратора с появлением в нём, в зависимости от материала и конструкции, небольших трещин.
Участок D-E.
Образование значительных и крупных раковин, развитие на кольцах подшипника трещин до сквозных.
Далее Е.
Работа подшипника с крупными раковинами, трещинами, генерация значительной вибрации, до заклинивания с большим тепловыделением.
В точке D имеется вероятность разрушения сепаратора.
В зависимости от норм отбраковки подшипников в каждой отрасли устанавливается по тренду предельное показание дисплея D.
Техническое состояние подшипникового узла на участке тренда:
Dm-A - характеризуется устойчивой работой (зелёная зона);
А-С - допустимая эксплуатация (жёлтая зона);
С-У - недопустимая эксплуатация (красная зона).
|
|
Оценка спектра акустико-эмиссионного от диагностируемого подшипникового узла позволяющая оценить его состояние, высвечивается на дисплее в цифровой форме.
Для конструктивно подобранных узлов и постоянной точке размещения датчика показания дисплея Da определяются функциональной зависимостью диаметра посадочного отверстия эксплуатируемого подшипника — d, числа оборотов вала — п(об/мин); коэффициента нагрузки Кп: Da = f ( d , n , Kn ).
Это подтверждается накопленными экспериментальными данными, что позволяет надёжно определять значения зон технического состояния подшипника:
- хорошая;
- допустимая;
- недопустимая.
Для подшипников КМБ локомотивов и подвижного состава рекомендуется замену подшипников производить на уровне (0,9-1,0)Ьс (конец жёлтой зоны) имея резерв времени по остаточному ресурсу работы до точки D, при значениях сигнала более 1,0-Dc производит* ремонт узла.
Съём и сравнение показателей Dm с различных точек корпуса, крышек, болтов крепления крышек в затянутом и ослабленном состоянии подшипникового узла дозволяют выявить и устранить дефект монтажа подшипникового узла, доведя значение ниже 0,3-0,4 Da для новых и ниже 0,6 Da для ремонтного подшипника. Тщательный подбор элементов ремонтного подшипника, правильный монтаж и смазка позволяют добиться значений Dm<0,3-0,4 Da. Уменьшение параметра Dm, как параметра качества сборки и произведённого ремонта увеличивает долговечность подшипникового узла.
|
|
Такие нарушения в работе оборудования как расцентровка валов, дисбаланс, дефекты крепежа - отрицательно влияют на работу подшипника и могут давать прибора до значений De.
Разброс показаний и максимальное значение сигнала «Р» несут дополнительные диагностические признаки дефектов подшипникового узла: дефекты смазки, недостаток или отсутствие смазки, наличие продуктов износа или коксования смазки, потеря смазочных свойств - увеличивают среднее значение, разброс показаний, максимальное значение «Р». Состав прибора
1. Пьезокерамический датчик.
2. Кабель датчика.
3. Измерительный блок.
4. Гнездо подключения кабеля датчика.
5. Кнопка питания прибора «Вкл/Выкл».
6. Кнопка «ПИК» при нажатии и удержании показывает пиковые значения числа «Р».
7. Окно дисплея.
8. Крышка с уплотнителем аккумуляторного отсека (аккумуляторы А - 1,2 В, время работы
прибора - 22 часа).
Устройство и принцип работы
Подготовка прибора к работе:
1. Кнопкой 5 включить прибор, при появлении показания ВАТТ или отсутствия показаний зарядить аккумуляторы или заменитьих.
2. После включения прибора на дисплее должны появиться цифры от 00.0 до 00.3 (при
t°=20°C, при t°=O°C цифры будут больше).Прибор готов к работе.
3. Датчик прижимают к поверхности с усилием 3-5 кг, при этом поверхность должна
быть ровной, очищенной от грязи и смазанной консистентной смазкой для уменьшения акустического сопротивления сигналу.
Примечание: верхний ряд показателей состояния для подшипников тягового двигателя - для болтов расположенных ближе к валу, нижний - для болтов на крышке.
Расчёт зоны технического состояния N с частотой вращения колёсной пары на момент диагностики п от 100 до 200 об/мин производится по формуле
N=T-K,
где N - определяемое значение конца зоны технического состояния, Т - табличное значение конца зоны, К -коэффициент пересчёта, определяемый как
где п - частота вращения колёсной пары на момент диагностики по условиям, имеющимся в депо.
Значение зоны технического состояния с частотой вращения колёсной пары на момент диагностики п от 200 до 300 об/мин производится по формуле
где N - определяемое значение конца зоны технического состояния, Т - табличное значение конца зоны технического состояния, К - коэффициент пересчёта, определяемый как
Примечание: верхний ряд показателей состояния для подшипников тягового двигателя - для болтов расположенных ближе к валу, нижний - для болтов подшипникового щита.
Диагностирование производится по циклам ремонта ТО5, ТОЗ, ТР1, ТР2 - для буксовых узлов.
Производится запись в бортовой журнал локомотива ТУ 152 при значении показаний ниже «С».
Результаты диагностирования прибором ИРП-12 заносятся в журнал формы №1, который является вкладышем ТУ-28.
Подобный прибор выпускается фирмой CONTEST.
Прибор представляет собой переносную конструкцию с пьезодатчиком, на конце которого имеется щуп. На лицевой панели имеется два индикатора, показывающих среднеквадратическое значение и максимальное значение ускорений. Имеется механический калькулятор с тремя зонами (допустимая, недопустимая, аварийная), по которому в зависимости от диаметра и скорости вращения и показаний прибора можно определить зону технического состояния подшипника.
Прибор также построен на принципе регистрации сигналов акустической эмиссии. По показаниям двух параметров можно оценивать характер повреждений подшипника.
Дата добавления: 2019-09-13; просмотров: 398; Мы поможем в написании вашей работы! |
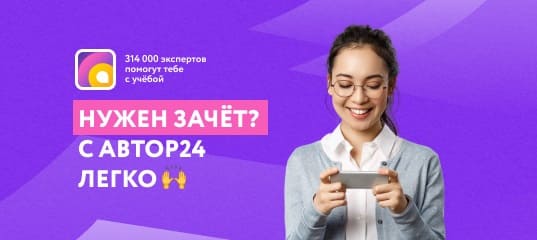
Мы поможем в написании ваших работ!