Индустриальные масла. Марки, отличительные особенности, область применения. Браковочные показатели.
Индустриальные масла применяются на ремонтных предприятиях водного транспорта и на судах для смазки вспомогательного оборудования.
В соответствие с условиями применения, индустриальные масла разделяют на масла для малонагруженных механизмов (И-5А, И-8А), средненагруженных механизмов и машин (И-40А, и-50А) и высоконагруженных машин (цилиндровое 24 и 52).
Характеристики и назначение индустриальных масел зарубежного производства рассмотрим на примере минеральных масел семейства MEROPA и синтетического масла PINNACLE MARINE GEAR 220 фирмы TEXACO
Масла семейства MEROPA предназначены для смазки зубчатых передач, цепных передач, антифрикционных подшипников, гибких муфт. Они обладают высокой несущей способностью, термической стабильностью, совместимы и защищают от коррозии следующие металлы: сталь, медь, бронзу, баббит. Отличаются высокой деэмульгирующей способностью. Высокий индекс вязкости позволяет достичь малого измерения вязкости при колебаниях температур. Отвечают требованиям стандартов US STEEL 224,AGMA 250.04;DAWID BROWN ET 33/80; DIN 51517/3.
Синтетическое индустриальное масло PINNACLE MARINE GEAR 220 предназначено для смазки подшипников и зубчатых передач при высоких температурах. Специально рекомендуется применять для зубчатых зацеплений судовых сепараторов (топливных и масляных). Полностью совместимо с материалами, применяемыми для изготовления красок, уплотнений, прокладок, шлангов и т.д.
|
|
Вопрос 87
Оценка технического состояния цилиндрово - поршневой группы дизеля с использованием пневмоиндикатора. Методика оценки и условия применения пневмоиндикатора.
Оценка технического состояния с помощью пневмоиндикатора ПИ-2М. Нормы плотности цилиндра дизелей представлены на рис.
Нормы плотности цилиндра дизеля при использовании пневмоиндикатора ПИ-2М для перепада давления воздуха на расходомерном устройстве ΔР=0,15 Мпа в зависимости от диаметра цилиндра.
ΔР=Р1-Р2=0,15 МПа
хор.состояние
удовлетворительное
неудовлетворительное
В процессе определения плотности цилиндра следует учитывать следующие обстоятельства: показания прибора в значительной степени зависят от состояния индикаторного канала, поэтому перед выполнением измерений он должен быть чистым и полностью открыт, утечки через неплотности прибора и индикаторного клапана должны отсутствовать.
Определение плотности цилиндров дизелей (например диаметром более 500 мм) осуществляется с помощью мановакуумметра или пневмоиндикатора ПИ-2М. Они устанавливаются на индикаторном кране. В качестве показателя плотности используется величина максимального давления. Проверка производится в процессе проворачивания валоповоротного устройства. Для определения значения норм максимального давления РМАХ в зависимости от категорий ТС могут быть использованы выражения:
|
|
- категория ТС «хорошо»
РМАХ≥41,1 VР0,478 τ -2,22;
- категория ТС «удовлетворительно»
РМАХ≥21,761 VР0,923 τ -2,3Vр0,23 ;
VР=πD2S/4 –рабочий объем цилиндра, м3.
Вопрос 86
Методы ремонта судовых технических средств. Ремонт трубопроводов систем, деталей цилиндрово - поршневой группы дизеля.
Ремонт поршней
Методы ремонта поршней зависят от материала, из которого они изготовлены, а также от вида дефекта.
Наиболее часто встречающимися дефектами, устраняемыми при ремонте поршней, являются чрезмерные зазоры между поршнем и цилиндровой втулкой, образовавшиеся из-за износа и расточки последней. Чугунные и алюминиевые поршни в таких случаях приходится изготовлять заново. Для чугунных поршней применяют чугун марки СЧ28-48 с поверхностной твердостью 171—241 НВ. При отливке головки поршней или не охлаждаемых монолитных поршней чугун легируют хромом и молибденом. Поршни отливают днищем вниз, предусматривая с противоположной стороны, обращенной кверху, прибыль, благодаря чему материал днища приобретает повышенную плотность.
|
|
При обработке поршней выполняют обычно следующие операции (по ходу технологического процесса): разметку и центровку на плите; сверление центрирующих отверстий на радиально-сверлильном станке; черновую обработку с припуском 2,5 мм на сторону; термическую обработку при 450—500° Сс выдержкой при этой температуре в течение 4—6 ч и с последующим охлаждением вместе с печью до 200° С, а затем на воздухе; чистовую обработку на токарном станке; разметку отверстия под поршневой палец на плите; предварительное растачивание отверстия под палец на горизонтально-расточном станке; шлифование наружной поверхности в центрах токарного станка и снятие карманов; чистовое растачивание отверстия под палец; сверление отверс-тий и нарезание резьбы при помощи кондукторов и оправок; гидравлическое испытание по Правилам Регистра СССР.
У составных поршней д. в. с. направляющую часть — тронк (юбку) — изготовляют из чугуна марок СЧ 28-48 и СЧ 24-44; отливают и обрабатывают примерно так же, как целый поршень, Обработанные тронки и тронковые поршни можно хранить только в вертикальном положении, чтобы они не деформировались.
Стальные головки поршней исправляют электронаплавкой. Для этого канавки и наружную поверхность протачивают на 2 мм; затем канавки полностью заваривают, а наружную поверхность наплавляют слоем толщиной 8—10 мм. В качестве электродов применяют электроды с легирующими обмазками марок УОНИ-13/45, УОНИ-13/55, УОНИ-13/65. После электронаплавки поршень подвергают высокому отпуску при 600—650° С для снятия внутренних напряжений. Потом наружную поверхность поршня протачивают, вытачивают канавки согласно построечному чертежу и проверяют торцевые поверхности. После механической обработки производят гидравлические испытания по Правилам Регистра СССР. В случае необходимости стальные поршни отливают из стали 35Л или стали 35, легированной молибденом. Алюминиевые поршни отливают из сплава АЛ25 или АЛЗО и АЛ1, если они ненапряженные.
|
|
Как при изготовлении новых, так и при ремонте старых поршней восстанавливают нормальные зазоры между поршнем и цилиндром. Если нет инструкции завода-строителя, размеры зазоров в миллиметрах определяют из следующих выражений:
а) между головкой поршня и цилиндром
Д, = (0,0065 -:- 0,0075) D мм ;
б) между тронком поршня и цилиндром (для двигателей с тронками или нормальными поршнями)
А, = (0,0010 -f-0,0011)D мм;
в) между поршнем и цилиндром (для двигателей с укороченными поршнями)
Д,= (0,0012 -0,0013) D мм
(D — внутренний диаметр цилиндровой втулки, мм).
В приведенных выражениях большие значения берут для цилиндров меньших размеров, а меньшие — для больших.
Чугунные поршни с трещинами или обгоревшими и прогоревшими днищами заменяют новыми. Стальные поршни с такими дефектами восстанавливают электросваркой и электронаплавкой с последующей термической и механической обработкой. У составных поршней головку и юбку перед сборкой шабрят по плоскости разъема по плите и пригоняют друг к другу на краску с точностью не менее двух пятен на 1 см-. Дефектные шпильки заменяют новыми. Все резьбовые отверстия проверяют метчиком, а после сборки головки с юбкой тщательно шплинтуют.
Если в поршне поверхность отверстия для пальца имеет задиры или отклонение от цилиндрической формы на 0,10—0,15 мм, ее растачивают, а затем шлифуют или расшабривают. При этом одновременно изготовляют новый или наращивают старый палец. В тех случаях, когда отверстие под палец имеет небольшое отклонение от цилиндрической формы, его исправляют шабровкой на краску по калибру. Отверстия считаются исправными, если овальность и конусность не превышает 0,02 мм.
Ремонт и изготовление труб и компенсаторов
Во время ремонта труб и компенсаторов выполняют перечисленные ниже работы.
1. Заварка электродуговым или газовым способом коррозионных поражений (раковин), свищей, трещин и других местных повреждений. Заплавлять зачищенные раковины металлом электрода допускается только в том случае, если толщина оставшейся стенки составляет не менее 2 мм. На места, проржавевшие насквозь, приваривают накладки. Свищи и трещины на красномедных трубах устраняют газосваркой или горячей пайкой (припоем с посыпкой в качестве флюса бурой). После сварки или пайки красномедные трубы отжигают при 630—650° Сс последующим охлаждением водой. На стальных трубах и компенсаторах, работающих под высоким давлением, участки со сквозными и несквозными трещинами или с кавернами (более 3—4 каверн на площади до 10 см2) заменяют. Негодный участок трубы вырезают, а новый приваривают встык к годной части трубы.
2. Замена фланца или заварка на нем небольших трещин с последующей механической обработкой.
3. Проточка и шабровка привалочных плоскостей фланцев. На трубах и компенсаторах высокого давления шабровку фланцев выполняют с точностью 5—6 пятен на 1 см2.
4. Замена и восстановление изоляции, перед постановкой изоляции наружную поверхность труб зачищают и окрашивают суриком, а трубы высокого давления сурмином.
5.Негодные трубы и компенсаторы заменяют новыми. При этом приходится выполнять работы по гибке и нарезанию труб, а также изготовлять соединительные детали.
1. Основные требования при подготовке дизельной установки к действию
2. Основные требования к подготовке и действию системы ГД .
3. Порядок проворачивания, пробных пусков и пусков ГД.
4. Топливные системы. .
6. Системы сжатого воздуха. .
7. Системы отвода газа.
8. Масляные системы.
9. Системы охлаждения.
10. Режимы работы СЭУ и их сущность.
11. Оптимальные режимы работы СЭУ.
12. Работа ГД и гребных винтов на швартовном режиме.
13. Характерные особенности парциальных режимов ГД и гребных винтов.
14. Работа ГД и гребных винтов в режиме буксирования судном воза.
15. Характеристика работы гребного винта при плавании судна в штормовую погоду.
16. Мощностные характеристики ГД и гребного винта при плавании судна на мелководье.
17. Режимы работы ГД при плавании судна во льдах и узкостях. .
18. Влияние изменения температуры наружного воздуха на режим работы ГТУ.
19. Отличительные особенности работы комплекса ГД - гребной винт в период старта судна.
20. Цель подготовительных операций при вводе в действие ДЭУ и их продолжительность. .
21. Особенности обслуживания при работе ДЭУ на переходных и нерасчетных режима
22. Фактор, ограничивающий возможность работы дизеля на перегрузочном режиме. .
23. Основные причины повышения температуры охлаждающей воды на выходе из дизеля и отходящего масла. .
24. Роль соединительной муфты при работе многомашинных установок на ВРШ.
25. Требования Регистра, предъявляемые к дизелям, работающим на винт через муфту
26. Порядок действия механика при отказе, когда при пуске двигатель останавливается при переводе на топливо.
27. Порядок действия механика при неполадках в работе дизеля в частности:
- при пуске подрываются предохранительные клапана;
28. Причины заниженной или (завышенной) по сравнению с заданной частотой вращения дизеля в следующих условиях:
- дизель не развивает оборотов при номинальном положении топливной рейки;
29. Причины и принимаемые меры при отклонениях в работе дизеля в таких случаях:
- повышена температура газов одного цилиндра;
30. Причины и принимаемые меры при отклонениях в работе дизеля в следующих ситуациях:
- стук в одном цилиндре;
31. Причины и принимаемые меры при отклонениях в работе дизеля, когда происходит:
- интенсивный износ цилиндро-поршневой группы;
32. Причины и принимаемые меры при неисправностях систем в следующих ситуациях:
- циркуляционный насос масла не создает требуемого давления;
33. Подготовка к действию котла и его систем в холодном состоянии: разводка огня и подъем пара в котле, включение его в работу.
34. Обслуживание котла и его систем в действии. Прекращение работы котла. Хранение бездействующего котла.
35. Основные мероприятия технического обслуживания котла.
36. Причины упуска воды в котле, действия обслуживающего персонала при упуске воды и после него.
37. Причины и источники вибрации на судне на ходовом режиме работы СЭУ
38. Виды шумов
39. Источники загрязнения мирового океана.
40. Условия допустимости слива нефтесодержащих вод с судов
41. Судовые холодильные установки: подготовка к пуску, ввод в действие, признаки нормальной работы.
42. Регулирование режима работы, обслуживание во время работы, остановка судовой холодильной установки
43. Техническое обслуживание холодильных установок:- удаление хладона из системы;
44. Заполнение систем холодильной установки маслом.
45. Эксплуатация приборов автоматического управления и контроля судовой холодильной установки
46. Борьба за живучесть судна. Борьба с водой, борьба с пожарами, выбор огнегасительных сред.
47. Тушение пожаров в помповых отделениях, жидкого топлива, в жилых, .
48. Борьба с паром, дымом и защита от воздействия высоких температур.
49. Характерные дефекты распылителей форсунок.
50. Характерные причины отказов соплового аппарата ГТН.
51. Основные причины отказов насосов
52. Элементы, определяющие работоспособность компрессоров.
53. Элементы, определяющие работоспособность топливных сепараторов.
54. Контроль плотности цилиндров при работе дизелей
55. Интегральный показатель ухудшения технического состояния топливной аппаратуры
56. Признаки неисправного состояния всасывающих и выпускных клапанов.
57. Основная характеристика работы поршневых компрессоров.
58. Параметры, определяющие степень загрязнения котлов.
59. Контролируемые параметры при определении категории технического состояния газотурбокомпрессоров
60. Способы оценки технического состояния насосов.
61. Способы контроля технического состояния вентиляторов
62. Показатели, оценивающие качество работы топливных сепараторов.
63. Параметры, характеризующие степень загрязнения поверхностей теплообмена теплообменных аппаратов
64. Контролируемые параметры гидравлических систем и агрегатов.
65. Показатели, определяющие износ блоков цилиндров аксиально-поршневых гидроагрегатов, поршней гидроцилиндров
66. Способы контроля технического состояния дейдвудных устройств
67. Способы контроля технического состояния рулевых устройств и машин
68. Причины повышения вязкости моторного масла при длительной работе дизеля.
69. Щелочное число. Характерные значения для судовых масел.
70. Причины попадания в смазочные масла частиц Аl и Si
71. Классификация дефектов судовых технических средств.
72. Основные дефекты дисков, диафрагм, лопаточного аппарата турбин и компрессоров.
73. Способы определения упругого изгиба коленчатых валов
74. Этапы разборки механизма. Подготовительные работы
75. Судовой комплект универсальных переносных диагностических средств.
76. Оценка технического состояния судовых технических средств по уровню вибрации и ударных импульсов. .
77. Основные функции моющих присадок.
78. Антикоррозионные и депрессантные присадки.
79. Противопенные, вязкостные присадки и многофункциональные присадки. .
80. Признаки классификации смазочных материалов по назначению, химическому составу.
81. Основные группы отечественных моторных масел. Функции смазочного масла в ДВС.
82. Основные функции турбинных масел. Предъявляемые требования.
83. Компрессорные масла. Марки отечественного и зарубежного производства.
84. Требования, предъявляемые к гидравлическим маслам.
85. Индустриальные масла. Марки, отличительные особенности, область применения
86. Методы ремонта судовых технических средств.
87. Оценка технического состояния цилиндро-поршневой группы дизеля с использованием пневмоиндикатора.
Дата добавления: 2019-07-15; просмотров: 228; Мы поможем в написании вашей работы! |
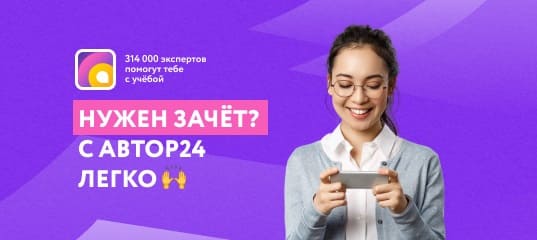
Мы поможем в написании ваших работ!