Газофазный способ получения углеродной матрицы
При получении УУКМ по способу осаждения пироуглерода из газовой фазы газообразный углеводород (метан, бензол, ацетилен и т. д.) или смесь углеводорода и разбавляющего газа (инертный газ или водород) диффундирует через углеволокнистый пористый каркас, где под действием высокой температуры происходит разложение углеводорода на нагретой поверхности волокна. Осаждающийся пироуглерод постепенно создает соединительные мостики между волокнами. Кинетика осаждения и структура получаемого пироуглерода зависят от многих факторов: температуры, скорости потока газа, давления, реакционного объема и др.
При изотермическом методе заготовка находится в равномерно обогреваемой камере. Равномерность обогрева в индукционной печи обеспечивается с помощью тепловыделяющего элемента – сусцептора, изготавливаемого из графита. Углеводородный газ подается через днище печи и диффундирует через реакционный объем и заготовку; газообразные продукты реакции удаляются через выходное отверстие в крышке печи. Процесс производится обычно при температуре 900 – 1150 0С и давлении 130–2000 кПа. Уменьшение температуры приводит к снижению скорости осаждения и чрезмерному удлинению продолжительности процесса. Увеличение температуры ускоряет осаждение пироуглерода, но при этом газ не успевает диффундировать в объем заготовки и происходит поверхностное наслоение пироуглерода. Продолжительность процесса достигает сотен часов. Изотермический метод обычно применяется для изготовления тонкостенных деталей, поскольку в этом случае заполняются преимущественно поры, находящиеся у поверхности изделия [1].
|
|
Метод импульсного осаждения в режиме давление – вакуум
В этом процессе реакционный объем попеременно заполняется углеводородным газом на несколько секунд и вакуумируется, в то время как температура заготовки с помощью индукционного нагрева поднимается от 800 до 1000 0С. Этот метод наиболее выгоден для объемного уплотнения изделий пироуглеродом. Хотя процесс затрудняется поверхностным осаждением пироуглерода, однако путем оптимального выбора температуры и времени осаждения удается достичь глубинного уплотнения углеродного изделия и снизить его газопроницаемость.
Для объемного насыщения пор и получения толстостенных изделий применяется метод температурного градиента, заключающийся в создании в заготовке температурного градиента путем помещения ее на обогреваемую оправку или сердечник или прямым разогревом ее током. Углеводородный газ подается со стороны, имеющей более низкую температуру. Давление в печи обычно равно атмосферному. В результате осаждение пироуглерода происходит в наиболее горячей зоне. Охлаждающее действие газа, протекающего над поверхностью с высокой скоростью, является основным способом достижения температурного градиента. Повышение плотности и теплопроводности композита приводит к перемещению температурного фронта осаждения, что обеспечивает в конечном итоге объемное уплотнение материала и получение изделий с высокой плотностью 1700—1800 кг/м3 [3].
|
|
При осаждении пироуглерода по методу перепада давления газ через заготовку (каркас) пропускается принудительно под давлением. Возникающий по толщине градиент давления зависит от проницаемости каркаса. По мере осаждения пироуглерода проницаемость снижается, что приводит к замедлению инфильтрации газа. Этим методом лучше уплотняются изделия с низкой проницаемостью. Метод технически весьма сложен, а получаемые результаты плохо воспроизводимы, поэтому метод не нашел широкого применения в промышленности.
Высокотемпературная термообработка (графитация) УУКМ
В ходе процесса получения УУКМ в них могут возникать внутренние напряжения, способные привести к деформациям и искажениям структуры изделия при эксплуатации этих материалов при температуре выше температуры карбонизации или осаждения пироуглерода. Поэтому при необходимости получения более термостабильного материала проводят его высокотемпературную обработку. Конечная температура термообработки определяется условиями эксплуатации. Термообработка проводится в индукционных печах или печах сопротивления в неокисляющей среде (графитовая засыпка, вакуум, инертный газ).
|
|
Длительность этих процессов невелика и степень превращения определяется в основном температурой. Поэтому длительность процессов высокотемпературной термообработки значительно меньше, чем в случае карбонизации или осаждения пироуглерода, и составляет обычно несколько часов. При высокотемпературной термообработке карбонизованных пластиков происходят необратимые деформации изделия, постепенное «залечивание» дефектов структуры и удаление гетероатомов. Для хорошо графитируемых материалов на основе пеков при температурах свыше 2200 0С наблюдается интенсивный рост трехмерноупорядоченных углеродных кристаллитов вплоть до перехода к графитовой структуре. В то же время в карбонизованных пластиках на основе плохо графитирующихся полимерных связующих дефекты структуры сохраняются до 3000 0С и материал остается в неграфитированной турбостратной структурной форме.[6]
|
|
Окисление УУКМ
Если в неокисляющей среде механические характеристики УУКМ сохраняются вплоть до 1700 0С и выше, то на воздухе они выдерживают лишь кратковременный высокотемпературный нагрев, при длительном же воздействии вследствие окисления углерода характеристики УУКМ резко снижаются. При выяснении механизма окисления с целью повышения окислительной стойкости УУКМ установлено, что суммарная скорость гетерогенных реакций углерода с газами в отсутствие катализирующих примесей определяется соотношением скоростей следующих стадий процесса:
- диффузией реагирующего газа и продуктов реакции из газового объема к поверхности углерода;
- диффузией реагирующего газа от наружной поверхности к активным участкам внутри образца и переносом продуктов реакции в обратном направлении;
-хемосорбцией молекул реагирующего газа на поверхности и десорбцией продуктов.
Окисление углерода начинается в первую очередь на активных центрах, какими могут являться кромки базисных углеродных слоев, дефекты решетки или дислокации. На процесс окисления большое влияние могут оказать примеси, например следы переходных металлов или их оксидов. Элементы, входящие в состав примесей, могут оказывать как ускоряющее действие на окисление углерода, так и замедляющее [7].
Пористость УУКМ и характер распределения пор также влияют на скорость окисления. Если лимитирующей стадией окисления является диффузия в порах, то с уменьшением соотношения радиуса пор и их длины энергия активации процесса снижается. Высокая пористость способствует ускоренному окислению композита.
Таким образом, повышению окислительной стойкости УУКМ способствуют применение хорошо графитирующейся матрицы, повышение плотности, конечной температуры обработки, снижение содержания катализирующих окислов примесей. Поскольку окисление углерода начинается уже при 350 – 4500С то для увеличения предельной температуры эксплуатации УУКМ в окислительных газовых средах необходимо использовать различные способы защиты композита от окисления. Например, известно, что фосфаты и бораты замедляют процесс окисления искусственных углеродов. Особенно эффективна пропитка фосфатом цинка, который снижает скорость окисления в 20 раз. Антиокислитильное действие фосфатов и боратов связано, возможно, с блокированием ими активных центров на поверхности углерода.
С целью защиты УУКМ от окисления возможно нанесение барьерных защитных покрытий, таких, как карбиды, силициды, а также пироуглерод.
Защитное действие покрытий, например карбида кремния, эффективно лишь на начальной стадии окисления. Если вначале скорость окисления УУКМ с покрытием очень мала по сравнению с немодифицированным УУКМ, то с течением времени она вновь возрастает до значения, характерного для исходного УУКМ. Это связано с возникновением температурных напряжений в слое карбида кремния при нагреве, приводящих к разрыву покрытия и быстрому окислению УУКМ.
Для эффективной защиты УУКМ от окисления покрытия должны удовлетворять следующим требованиям:
-иметь высокую температуру плавления и разложения; низкое давление паров;
- быть по возможности плотными, бес пористыми;
- при окислении образовывать тонкую оксидную пленку, препятствующую дальнейшему проникновению окисляющего газа внутрь изделия;
-не вступать в реакции с углеродом;
- значения температурных коэффициентов линейного расширения защитного слоя и УУКМ не должны сильно отличаться, чтобы не произошло разрыва или смещения покрытия;
- иметь хорошую адгезию к углеродному материалу [8].
Дата добавления: 2019-07-15; просмотров: 1281; Мы поможем в написании вашей работы! |
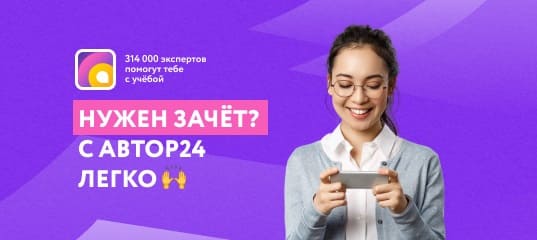
Мы поможем в написании ваших работ!