КОМПОЗИЦИОННЫЕ МАТЕРИАЛЫ СИСТЕМЫ УГЛЕРОД-УГЛЕРОД. История создания
Министерство образования и науки Российской Федерации
федеральное государственное бюджетное образовательное учреждение
высшего образования
«Санкт-Петербургский государственный университет промышленных технологий и дизайна»
Институт прикладной химии и экологии |
Кафедра: | Наноструктурных, волокнистых композиционных материалов |
Направление подготовки: (специальность) | 18.03.01 Химическая технология |
Профиль подготовки: (специализация) | 24.02.01 Технология и оборудование производства химических волокон и композиционных материалов на их основе |
КУРСОВАЯ РАБОТА по учебно-исследовательской работе |
на тему: “Получение исследование свойств углерод-углеродных композиционных материалов” |
Руководитель: | д-р технич. наук, проф. Лысенко В.А. | |||||||
(должность, ученая степень / звание, Ф.И.О.) | (подпись) | |||||||
Обучающийся: | Шлемин Е.Н. | |||||||
(Ф.И.О.) | (подпись) | |||||||
Курс | 4 | Учебная группа: | 4-ХДА-3 | |||||
Санкт-Петербург
2019
СОДЕРЖАНИЕ
Углерод-углеродные композиционные материалы.. 3
КОМПОЗИЦИОННЫЕ МАТЕРИАЛЫ СИСТЕМЫ УГЛЕРОД-УГЛЕРОД. История создания 12
Углеродная матрица и способы ее получения. 13
Жидкофазный способ получения углеродной матрицы.. 15
|
|
Газофазный способ получения углеродной матрицы.. 17
Метод импульсного осаждения в режиме давление – вакуум.. 18
Высокотемпературная термообработка (графитация) УУКМ... 19
Окисление УУКМ... 20
Влияние состава УУКМ на его структуру и свойства. 22
Влияние расположения углеродных волокон в объеме на механические свойства УУКМ... 23
Усталость и сохраняемость. 24
Свойства и области применения УУКМ... 24
Применение УУКМ в химических источниках тока. 28
Материалы газодиффузионных подложек. 31
Промышленное производство газодиффузионных подложек на основе углерод-углеродных композитов. 34
Список использованных источников. 39
1.Углерод-углеродные композиционные материалы
Углерод-углеродные композиционные материалы - такие материалы, матрица и наполнитель которых состоят из углерода. В качестве наполнителя применяют углеродные волокна, ленты и ткани; углеродными матрицами могут быть коксы пеков, синтетические смолы, пироуглерод. [1]
Углеродные волокна (УВ) это волокна, состоящие на 95 - 98 % из углерода. Углеродные волокна обычно получают термической обработкой химических или природных органических волокон (прекурсоров), при которой в материале волокна остаются главным образом атомы углерода. Помимо обычных органических волокон (чаще всего вискозных и полиакрилонитрильных), для получения углеродных волокон могут быть использованы специальные волокна из фенольных смол, лигнина, каменноугольных и нефтяных пеков [2].
|
|
На рисунке 1 представлена схема получения углеродных волокон.
Рисунок. 1. Схема получения УУКМ
В Таблице. 1 представлена эффективность карбонизации основных полимерных волокон-прекурсоров
Таблица 1. Эффективность карбонизации полимерных волокон-прекурсоров
Полимер ные волокна | Содержа ние углерода по данным элементного анализа | Выход карбонизованного остатка, % | Особенности технологии | |
Без использова-ния специаль ных приемов | С использова нием добавок и дополнительных обработок | |||
ПАН (сополи-меры) | 63–65 | 48–52, после термо-стабилиза ции | 57–60, фосфорсодержа щие соединения | Требуется предокисле ние, обработка NaOH, радиационное облучение |
ГЦВ | 42–44 | 18–22 | 35–40, добавки пиролиза | Не нуждается в предокисле нии |
ПЕК | 75–88 | 58–60 | Неизвестно | Требуется окислитель ная стабилизация |
ФФС (Kynol) | 78–80 | 58–60 | 60–65, использование фосфорорганиче ских соединений | Требуется предваритель-ная полимериза ция |
Лигнин | 65–67 | 45-50 | Специальные добавки и условия | Предокисле ние |
Физико-механические и химические свойства углеродных волокон определяются видом исходного сырья, условиями получения, температурой и средой термообработки и другими факторами.
|
|
По мере развития исследований и технологии производства были получены и выделились в отдельную группу весьма важные для современной техники более высокопрочные и высокомодульные углеродные волокна, и была использована их классификация, основанная на физико-механических свойствах, приведенных в таблице 2.
Таблица 2. – Характеристики углеродных волокон по современной классификации
Тип УВ | Модуль упругос ти, ГПА | Прочность на разрыв, ГПа | Термо-провод ность, Вт/м·К | Удельное сопротивле ние, мОм·см | Стои мость, USD/кг |
УВ из ПАН | |||||
Промышленные | 230 | 0,380 | 20 | 1,65 | 18 - 24 |
Стандартные с модулем упругости | 220-241 | 3,5-3,8 | 20 | 1,65 | 36 - 44 |
Среднемодуль ные | 290-300 | 3,5-6,2 | 20 | 1,65 | 65 - 73 |
Высокомодуль ные | 350-450 | 3,5-5,5 | 20 | 1,45 | 100 - 150 |
Сверхвысокомо-дульные | 500-950 | — | 80 | 0,90 | 250 - 1900 |
УВ из пеков | |||||
Низкомодульные | 170-240 | 1,4-3,1 | — | 1,30 | 100-160 |
Высокомодульные | 380-620 | 1,9-2,7 | — | 0,90 | 1700 |
Сверх.выс.модульн. | 690-970 | 2,4 | 400 - 1100 | 0,13 | 3600 |
|
|
В основе производственного процесса изготовления УУКМ находятся технологии создания армирующих каркасов и насыщения их матричным материалом. Из существующих систем структур армирования УУКМ в практике получили наибольшее распространение системы двух, трёх, четырёх и реже n нитей. Изменяя соотношение армирования в разных направлениях, создают материалы с заданными свойствами. Подробный анализ сравнительных преимуществ материалов, образованных системой трех нитей, и многомерных композиционных материалов выполнен в работах [3].
Методы изготовления армирующих каркасов УУКМ различны, среди них ткачество сухих нитей, прошивка тканей, сборка жестких стержней, изготовленных из углеродных нитей методом пултрузии, намотка нитью, плетение, а также комбинация этих методов.
Одной из основных составных частей УУКМ является углеродная матрица. Она объединяет в одно целое армирующие элементы в композиционном материале, позволяет материалу наилучшим образом воспринимать различного рода нагрузки, принимает участие в создании несущей способности композита [2].
Определяющими факторами при выборе исходного материала матрицы, как правило, являются его состав, вязкость, выход и структура кокса.
Наиболее часто в качестве матрицы применяют пироуглерод и кокс синтетических или природных связующих.
Пиролитический углерод — продукт разложения углесодержащих соединений на горячих поверхностях, который получается методом осаждения из нагретых гомогенно, гетерогенно или гомогенно-гетерогенно, разлагающихся газов и паров или твердых веществ. Источником паров, газов, твердых веществ, являются природные газы, например метан, продукты их первичного пиролиза, пропан-бутановые смеси, пары жидких углеводородов: бензола, ацетилена, хлорсодержащие углероды и их производные, каменные и бурые угли. Вся эта группа химических соединений, называется традиционным углеводородным сырьем, которая применяется для получения пиролитического углерода. В зависимости от температурных режимов нагрева углеводородного сырья, большинство исследователей пиролитический углерод называют: полукокс (температура нагрева 400 - 600 °С), кокс (температура нагрева 600 - 950 °С), пиролитический графит (температура нагрева 950 - 1300 °С). Скорость образования пиролитического углерода и его структура зависят от используемого углеводородного сырья [1]. Наибольший выход пиролитического углерода получается из метана, имеющего наименьшую из указанных соединений относительную молекулярную массу, в то время как у углеводородов с большой молекулярной массой наблюдается повышенный выход сажи.
В качестве матричных материалов УУКМ при жидкофазном способе используют термореактивные и термопластичные связующие. Большинство термореактивных связующих в качестве основных компонентов состава содержат смолы. Термопласты в качестве связующего используют редко, из-за малой величины коксового остатка после карбонизации. Исключение составляют каменноугольные и нефтяные пеки, в которых изначально содержится до 90 – 95 % углерода и много его остается в коксовом остатке. В таблице 3 приведены данные по выходу углеродного остатка при карбонизации ряда исходных материалов.
Таблица 3. Выход углеродного остатка для различных материалов
Исходный материал | Углеродный остаток, % мас. |
Полиэфиры | 2–18 |
Эпоксидные смолы | 7–25 |
ПВС | 25 |
Полифениленовая смола | 71 |
Полибензимидазоловая смола | 73 |
Полиимидная смола | 60 |
Фенолформальдегидная смола | 60–65 |
Смола на основе фурфуриловых эфиров | 63 |
Пек | 70–80 |
Выбор связующего для получения УУКМ осуществляется по следующим критериям: высокий выход карбонизованного остатка, технологичность при изготовлении композитов, стоимость.
Основными исходными материалами для матрицы УУКМ являются термореактивные фенольные и фурфуриловые смолы и пек из смолы каменного угля и нефти.
При выборе метода пропитки должны быть рассмотрены ряд факторов, одним из которых является эффективность пропитки, которая тесно связана со стоимостью производства и механическими свойствами композита.
При использовании метода пропитки в виде окунания в пропиточную ванну, эффективность пропитки может ограничиваться.
УУКМ относится низкая пористость, низкий коэффициент термического расширения, сохранение стабильной структуры и свойств, а также размеров изделий при нагревах до 2000 °С и охлаждении, высокие механические свойства, а также хорошая электропроводность.[2]
Предельные температуры эксплуатации металлических сплавов составляют: сплавы алюминия – 160 °С (кратковременно до 500 °С), сплавы титана до 400 °С (кратковременно до 850 - 1000 °С), сплавы бериллия – 450 °С , сплавы магния – 180 °С (до 300 °С), сталь 30 ХГС – 400 - 500 °С (кратковременно до 900 °С), никелевые сплавы – 815 - 1035 °С, никель- хромовые сплавы – 750 °С, коррозионностойкие стали – 500 °С, кобальтовые сплавы – 870 - 1205 °С медноникелевые сплавы – 300 °С, бронза – 200 – 400 °С. Углерод углеродные композиционные материалы (УУКМ), углеродкерамические УУКМ и их модификации сочетают высокие упругоустойчивые свойства с высокой термостойкостью – при 20 °С – 340 Мпа, при 2200 °С – 240 МПа. Графически температуры эксплуатации представлены на рисунке 3.
Рисунок. 2.Зависимость удельной прочности при растяжении σ/р конструкционных материалов от температуры [3]: 1 – алюминиевые сплавы; 2 – МКМ AL/B; 3 – нержавеющая сталь; 4 – титановые сплавы, 5 – эпоксидные углеволокниты; 6 – малеинимидные углеволокниты; 7 — полиимидные углеволокниты; 8,9— УУКМ различных типов и структуры; 10 — МКМ Ti/SiC (Ti 2124 + 15 % м. волокон SiC)
Изменения удельной прочности некоторых материалов от температуры в диапазоне от 0 до 1600 °С представлены на рис. 2. Как видно из рис. 2 предельные температуры эксплуатации алюминиевых, титановых сплавов, а также стали находятся в области до 430 °С, в то же время УУКМ различных типов сохраняют наибольшую удельную прочность при таких температурах, а как сказано выше, имеют температуру эксплуатации значительно превышающую 430 °С.
Основное применение УУКМ находят в изделиях, которые работают при температурах выше 1200 °С [3].
Перечисленные преимущества КМУУ позволили успешно их применять в качестве тормозных дисков в авиационных тормозах, соплах ракетных двигателей, в защитных накладках крыльев космических челноков, пресс-формах, тиглях, роторов турбин, труб высокого давления, для подшипников скольжения, уплотнений и т. д. Особо надо отметить повышающийся интерес на использование КМУУ в электротехнике [3].
Отрасли применения УУКМ рассмотрены на рисунке 3.
Рисунок. 3. Области применения УУКМ [3]: 1 — фрикционные диски узлов торможения самолетов СУ-ЗОМ, ТУ-154, ТУ-160, ИЛ-96; 2 — неохлаждаемые сопла ЖРД; 3 — внешняя переизлучающая многоразовая теплозащита — ВКС и МАКС; 4 —сопла РДТТ установок залпового огня систем «Ураган», «Град»; 5 — сопла РДТТ зенитных комплексов «Игла», С-300, С-400 «Триумф»; 6 — сопла РДТТ СС-20, СС-24, СС-25, «Тополь»; 7 — первая стенка «Токамака»; 8 — Перспективные РДТТ; 9 — ГЧ БРДЦ, детали двигательных установок ядерных РД.
КОМПОЗИЦИОННЫЕ МАТЕРИАЛЫ СИСТЕМЫ УГЛЕРОД-УГЛЕРОД. История создания
Композиционные материалы системы углерод-углерод впервые были созданы в начале 60-х годов прошлого столетия одновременно с появлением высокопрочных углеродных волокон. Способ получения волокон из углерода – неплавкого и нерастворимого вещества – подсказан впервые Эдисоном и Сваном [1]. Им удалось, нагревая органические волокна в определенных условиях, не разрушать их, а превращать в углеродные. Этот же принцип был использован в конце пятидесятых годов прошлого века, когда независимо друг от руга, в СССР, США и Японии развернулись исследования, положившие начало созданию промышленности углеродных волокнистых материалов (УВМ) [2]. За прошедшие годы в качестве исходного сырья для этих целей были испробованы практически все промышленные, а так же ряд специально полученных волокон. Однако большинство из них не удовлетворяло предъявленным требованиям, основные из которых – неплавкость или легкость ее придания, выход готового волокна и его высокие показатели.
Углерод-углеродные композиционные материалы (УУКМ) содержат углеродный армирующий элемент в виде дискретных волокон, непрерывных нитей или жгутов, войлоков, лент, тканей с плоским и объемным плетением, объемных каркасных структур. Волокна располагаются хаотически, одно-, двух- и трехнаправленно, принципиальные схемы расположения волокон в УУКМ представлены на рисунке. 4.
Углеродная матрица объединяет в одно целое армирующие элементы в композите, что позволяет наилучшим образом воспринимать различные внешние нагрузки. Определяющими факторами при выборе материала матрицы являются состав, структура и свойства кокса.
К числу специальных свойств КМУУ относится низкая пористость, низкий коэффициент термического расширения, сохранение стабильной структуры и свойств, а также размеров изделий при нагревах до 2000 °С и охлаждении, высокие механические свойства (таблица 3, рисунок 5), а также хорошая электропроводность. Основное применение КМУУ находят в изделиях, которые работают при температурах выше 1200° с
Перечисленные преимущества КМУУ позволили успешно их применять в качестве тормозных дисков в авиационных тормозах, соплах ракетных двигателей, в защитных накладках крыльев космических челноков, пресс-формах, тиглях, роторов турбин, труб высокого давления, для подшипников скольжения, уплотнений и т.д. Особо надо отметить повышающийся интерес на использование КМУУ в электротехнике.
Дата добавления: 2019-07-15; просмотров: 3183; Мы поможем в написании вашей работы! |
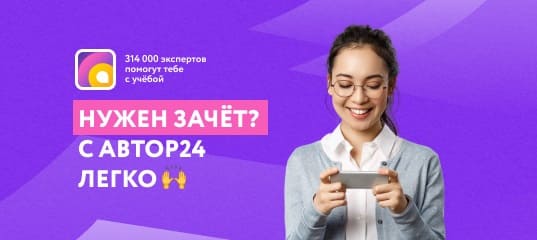
Мы поможем в написании ваших работ!