Углеродная матрица и способы ее получения
Технология получения УВМ, используемых для армирования композитов, различного текстильного ассортимента предусматривает две схемы: при первой текстильная структура готовится из вискозной технической нити перед тепловой обработкой, при второй – непосредственно из углеродных нитей.
Углеродная матрица, подобная по физико-химическим свойствам углеродному волокну, обеспечивает термостойкость УУКМ и позволяет наиболее полно реализовать в композите уникальные свойства углеродного волокна. Углеродная матрица в композите выполняет следующие функции: передает усилие на волокна; защищает волокна от воздействия внешней среды; изолирует отдельные волокна друг от друга, препятствует их взаимному сдвигу [3].
Метод получения углеродной матрицы определяет ее структуру и свойства (таблице 4), а также характеристики УУКМ. Существует три основных способа получения углеродной матрицы (рисунок 6):
- жидкофазный – пропитка КМ смолой или пеком с последующей карбонизацией и графитацией;
- газофазный – насыщение КМ пироуглеродом;
-
комбинированный (гибридный) – насыщение КМ двумя типами углеродной матрицы, состоящей из углеродного кокса полимерных смол или пека с последующим газофазным доуплотнением пористой структуры матрицы пироуглеродом.[4]
Жидкофазный способ получения углеродной матрицы
Процесс карбонизации представляет собой высокотемпературную обработку изделия из углепластика до температуры 800 0С в неокисляющей среде (инертный газ, угольная засыпка и т. д.). Цель термообработки – перевод связующего в кокс. В процессе карбонизации происходит термодеструкция матрицы, сопровождающаяся потерей массы, усадкой, образованием большого числа пор и снижением вследствие этого физико-механических свойств композита.
|
|
Процесс сопровождается удалением испаряющихся смолистых соединений и газообразных продуктов и образованием твердого кокса, обогащающегося атомами углерода. Поэтому в процессе карбонизации ключевым моментом является выбор температурно-временного режима, который должен обеспечивать максимальное образование коксового остатка из связующего, поскольку механическая прочность карбонизованного композита зависит, помимо прочего, от количества образовавшегося кокса.
Наиболее медленный подъем температуры должен происходить в интервале протекания глубоких пирогенетических изменений связующего, содействующих образованию кокса, а затем скорость нагрева может быть значительно увеличена. Скорость нагрева (и охлаждения) определяет также распространение температуры в изделии. Разница температур в объёме изделия вызывает неравномерность протекания пирогенных процессов и объемных изменений, создает опасные внутренние напряжения, приводящие к деформации и растрескиванию изделия. Поэтому, чем больше габариты изделия, тем продолжительнее должен быть процесс карбонизации. Скорость подъема температуры при карбонизации – от нескольких градусов до нескольких десятков градусов в час, продолжительность процесса карбонизации 300 ч и более. Карбонизация заканчивается обычно в интервале температур 800–1500 0С, но при необходимости УУКМ могут нагреваться до более высоких температур, соответствующих температурному интервалу перехода углерода в графит.
|
|
Свойства УУКМ в значительной мере зависят от вида исходного связующего, в качестве которого применяются синтетические органические смолы, дающие высокий коксовый остаток. Чаще всего для этой цели применяют фенолформальдегидные смолы вследствие их технологичности, доступности низкой стоимости, образовавшийся в этом процессе кокс обладает высокой прочностью. Пропитку углеродного материала можно осуществлять готовым связующим или же производить полимеризационное или поликонденсационное наполнение, когда в качестве исходных реагентов используются полимерные порошки [2] или олигомеры смол. Так в работе [2] было исследовано влияние углеродного волокна на ход реакции поликонденсации резольного фенолформальдегидного олигомера.
|
|
Весьма перспективны для получения углеродной матрицы каменноугольные и нефтяные пеки вследствие большого содержания углерода (до 92 – 95 %) и высокого коксового числа. Преимуществами пеков перед другими связующими являются доступность и низкая стоимость, исключение растворителя из технологического процесса, хорошая графитируемость кокса и его высокая плотность. Однако вследствие неоднородности состава пеков, представляющих смесь индивидуальных органических соединений, при карбонизации пеков происходит дистилляция низкомолекулярных компонентов и образование значительной пористости. К недостаткам пеков можно отнести также термопластичность, приводящую к миграции связующего при термообработке и деформации изделия, наличие в их составе канцерогенных соединений, что требует дополнительных мер безопасности.
Вследствие выделения летучих соединений при термодеструкции смолы в карбонизованном пластике возникает значительная пористость, снижающая физико-механические свойства УУКМ. Поэтому стадией карбонизации углепластика завершается процесс получения лишь пористых материалов, для которых не требуется высокая прочность, например, низкоплотных УУКМ теплоизоляционного назначения. Обычно для устранения пористости и повышения плотности карбонизованный материал вновь пропитывается связующим и карбонизуется (этот цикл может повторяться неоднократно). Повторная пропитка производится в автоклавах в режиме «вакуум – давление», т. е. сначала заготовка нагревается в вакууме, после чего подается связующее и создается избыточное давление до 0,6—1,0 МПа. При пропитке используются растворы и расплавы связующих, причем пористость композита с каждым циклом уменьшается, поэтому необходимо использовать связующие с пониженной вязкостью. Степень уплотнения при повторной пропитке зависит от типа связующего, коксового числа, пористости изделия и степени заполнения пор. С ростом плотности при повторной пропитке повышается и прочность материала. Этим методом можно получать УУКМ с плотностью до 1800 кг/м3 и выше. Метод карбонизации углепластика сравнительно прост, он не требует сложной аппаратуры, обеспечивает хорошую воспроизводимость свойств материала получаемых изделий. Однако необходимость многократного проведения операций уплотнения значительно удлиняет и удорожает процесс получения изделий из УУКМ, что является серьезным недостатком указанного метода.[5]
|
|
Дата добавления: 2019-07-15; просмотров: 1410; Мы поможем в написании вашей работы! |
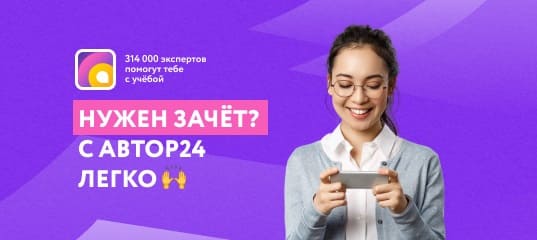
Мы поможем в написании ваших работ!