Практика термической обработки
Для правильного проведения термической обработки необходимо установить:
1) температуру нагрева;
2) время выдержки при данной температуре;
3) скорость охлаждения.
Выбор температуры и времени нагрева
Температуру нагрева стали при термической обработке выбирают согласно диаграмме «железо-углерод» (рис. 3.3).
Рисунок 3.3. - Области температур нагрева при термической обработке сталей: 1 – полный отжиг, нормализация, закалка доэвтектоидной стали; 2- нормализация эвтектоидной и заэвтектоидной стали; 3 – неполный отжиг, закалка заэвтектоидной стали; 4 - высокий отпуск; 5 – средний отпуск; 6 – низкий отпуск; 7 – диффузионный отжиг.
Выдержка при температуре необходима для полного прогрева детали по всему сечению и для выравнивания химического состава аустенитных зерен. Время выдержки при данной температуре зависит от формы и размеров изделия и от состава стали. Чем выше температура нагрева, тем меньше время выдержки. Общее время нагрева tобщ складывается из времени нагрева до заданной температуры (tн) и времени выдержки при этой температуре (tв), следовательно,
tобщ=tн+tв. (*)
Величина tн зависит от нагревающей способности среды, от размеров и формы деталей, от их укладки в печи; tв зависит от скорости фазовых превращений, которая определяется степенью перенагрева выше критической точки и дисперсностью исходной структуры. Практически величина tв может быть принята равной 1 мин для углеродистых и 2 мин для легированных сталей. При нагреве крупных деталей (когда tн значительно больше 1-2 мин) величиной tв можно пренебречь; в случае мелких деталей (диаметром или толщиной менее 1 мм) пренебрегают составляющей tн. Вообще, время нагрева зависит от многих факторов и на практике колеблется от 1 – 2 мин (нагрев мелких деталей в соли) до многих часов (нагрев крупных деталей тяжелого машиностроения в печи). Точно установить время нагрева можно лишь опытным путем для данной детали в данных конкретных условиях, а приближенно – можно подсчитать. Расчет проводят по следующей формуле:
|
|
tн=0,1D1K1K2K3, (**)
где D1 – размерная характеристика изделия (мм) – минимальный размер максимального сечения (для шара и круга – диаметр, квадрата – сторона, в пластине – толщина); K1 – коэффициент среды в которой производят нагрев (для газа - 2, соли - 1, металла - 0,5);К2 – коэффициент формы (для шара – 1, цилиндра – 2, параллелепипеда – 2,5, пластины – 4); К3 – коэффициент равномерности нагрева (всесторонний нагрев – 1, односторонний – 4). Время нагрева стали под закалку складывается из времени нагрева детали до заданной температуры и времени выдержки при температуре закалки. В соответствии с вышеприведенными формулами были получены следующие значения для времени нагрева сталей в электрической печи в воздушной атмосфере (табл. 3.2).
|
|
Таблица 3.2. - Нормы нагрева стали при термической обработке, мин
Форма изделия | Продолжительность нагрева при Температуре (˚ С) | ||||
600 | 700 | 800 | 900 | 1000 | |
Круг (на 1 мм диаметра) | 2 | 1,5 | 1,0 | 0,8 | 0,4 |
Квадрат (на 1 мм ширины) | 3 | 2,2 | 1,5 | 1,2 | 0,6 |
Отжиг и нормализация.
Для доэвтектоидных сталей применяется полный отжиг, который заключается в нагреве выше точки Ас3, а для эвтектоидной и заэвтектоидной стали – неполный отжиг, при котором нагрев проводят выше точки Ас1. Полный отжиг для заэвтектоидных сталей использовать нельзя, вследствие образования цементитной сетки, резко снижающей вязкость стали. Перегрев доэвтектоидной стали при отжиге также не допускается, так как он приводит к образованию крупных зерен. Структуру перегретой стали можно исправить нормальным отжигом или нормализацией.
Закалка и отпуск.
Температуру закалки для доэвтектоидных сталей берут на 30-50˚ выше точки Ас3, а для эвтектоидной и заэвтектоидной сталей – на 30-50˚ выше точки Ас1.
Нагрев заэвтектоидных сталей выше точки Асm (линия SE) вреден, так как приводит к снижению твердости вследствие растворения цементитных частиц, роста зерен и увеличения количества остаточного аустенита. Кроме того, при закалке с высоких температур образуется крупноигольчатый мартенсит, обладающий повышенной хрупкостью.
|
|
Нагрев доэвтектоидной стали под закалку ниже точки Ас3, но выше Ас1 также не допускается, так как не позволяет получить высокую твердость вследствие неполного растворения пластичного мягкого феррита. После такой неполной закалки доэвтектоидная сталь получает структуру мартенсита и феррита.
Скорость охлаждения определяется требуемой структурой и свойствами стали.
Закалочные среды. При закалке стали для переохлаждения аустенита до температуры мартенситного превращения требуется быстрое охлаждение, но не во всем интервале температур (от температуры нагрева до комнатной температуры), а только в пределах 650 – 4000С, т.е. в том интервале температур, в котором аустенит менее всего устойчив. В качестве охлаждающей среды применяют различные жидкости (см. табл. 3.3): воду, водные растворы солей, щелочей, кислот, масло, расплавленные соли и т.д. Следует отметить, что многие легированные стали приобретают мартенситную структуру при охлаждении в холодных или подогретых маслах, а высоколегированные стали закаливаются на мартенсит даже при охлаждении на воздухе.
|
|
Таблица 3.3. - Характеристика закалочных сред.
Закалочная среда | Интервал пузырчатого кипения, 0С | Относительная интенсивность охлаждения в середине стадии пузырчатого кипения |
Вода: | ||
200С | 400-100 | 1 |
400С | 350-100 | 0,7 |
800С | 250-100 | 0,2 |
Раствор в воде, 200С: | ||
1%-ный NaCl | 500-100 | 1,5 |
10%-ный NaCl | 650-100 | 3,0 |
10%-ный NaОН | 650-100 | 2,5 |
Масло минеральное, 20-2000С | 500-250 | 0,3 |
Наиболее распространенные закалочные среды – вода и масло. Механизм действия закалочных сред следующий. В момент погружения изделия в закалочную среду вокруг него образуется пленка перегретого пара, охлаждение происходит через слой этой паровой рубашки, т.е. относительно медленно – стадия пленочного кипения. Когда температура поверхности достигает некоторого значения (определяемого составом закаливающей жидкости), при котором паровая рубашка разрывается, то жидкость начинает кипеть на поверхности детали, и охлаждение происходит быстро – стадия пузырчатого кипения. Когда температура поверхности металла ниже температуры кипения жидкости, жидкость кипеть уже не будет, и охлаждение замедлится – стадия конвективного теплообмена. Закалочная жидкость охлаждает тем Интенсивнее, чем шире интервал стадии пузырчатого кипения. Скорость охлаждения в воде с температурой 18˚ составляет примерно 600˚С/сек, а в масле - 150˚С/сек.
В таблице 3.3 приведены примерные температуры, разграничивающие различные стадии охлаждения, и сравнительная интенсивность действия разных закалочных сред.
Выбор температуры отпуска. Температуру нагрева для отпуска стали определяют в зависимости от требуемых свойств.
Различают три вида отпуска: низкий (160-180˚ С), средний (350-450˚ С) и высокий (500-650˚ С).
Низкий отпуск назначается для снятия внутренних напряжений, некоторого повышения вязкости и пластичности без заметного снижения твердости. Такому отпуску подвергают мерительный и режущий инструмент, детали, прошедшие цементацию, поверхностную закалку.
Среднему отпуску подвергают штампы, пружины и рессоры для получения структуры троостита.
Высокий отпуск применяют для конструкционной стали, чтобы получить структуру сорбита, которая обладает наилучшим сочетанием прочности и пластичности. Закалку с высоким отпуском называют улучшением. Улучшению подвергают ответственные детали, изготовленные из конструкционных сталей с содержанием углерода 0,3-0,5%. Продолжительность отпуска выбирается из расчета получения стабильной структуры и рекомендуется в пределах от 0,5 до 3 часов. В лабораторной работе отпуск можно проводить в течение 30-60 мин. Охлаждать образцы рекомендуется на воздухе.
Порядок выполнения работы
1. Получить 6 образцов стали одного химического состава, оборудование и инструмент.
2. По диаграмме состояния «железо-углерод» найти критические точки для данной стали и установить температуры неполной и полной закалки, отжига и нормализации. Занести данные в табл. 1.
3. Определить для данных образцов время нагрева tн, время выдержки tв при температуре термообработки и общее время нагрева tобщ (по формулам (*) и (**)). Занести данные в табл. 2.
4. Все образцы нагреть до оптимальной температуры закалки.
5. Охладить образцы: три образца – в воде, один образец – в масле, один образец – на воздухе, один образец – вместе с печью до 500˚С, а затем на воздухе. Закалку в воде и масле произвести следующим образом: одной рукой открыть дверцы печи, а другой щипцами взять образец и быстро перенести его в охладитель – воду или масло. Категорически запрещается погружать в масло щипцы во избежание возгорания! В охладителе образец нужно энергично передвигать для повышения интенсивности его охлаждения. Для образца, охлаждаемого с печью, нужно подсчитать фактическую скорость охлаждения, для чего необходимо записать интервал температур и время охлаждения образца с печью.
6. Плоские поверхности образца с двух сторон зачистить на наждаке и шкурке и испытать на твердость. Результаты измерений занести в табл. 2.
7. Построить график зависимости твердости от скорости охлаждения.
8. Три образца, закаленных в воде с оптимальной температуры, подвергнуть отпуску при температурах 180˚С, 350˚С и 650˚С в течение 30 минут.
9. После отпуска измерить твердость образцов. Результаты измерений занести в табл. 3.
10. Построить график зависимости твердости от температуры отпуска.
11. Составить отчет о проделанной работе.
Содержание отчета
1. Название работы.
2. Цель работы.
3. Приборы и принадлежности.
4. Краткие сведения из теории.
4.1. Цели термической обработки.
4.2. Основные виды термической обработки.
4.3. Превращения, происходящие в стали при нагреве и охлаждении.
4.4. Краткие сведения из практики термической обработки.
5. Материал исследования.
Таблица 1. - Материал исследования.
Марка стали | Химический состав, % | Критические точки, 0С | ||||||
Ас1 | Ас3 | |||||||
Краткая характеристика исследуемых сталей (структурный класс, исходная равновесная структура, область применения).
6. Влияние скорости охлаждения на структуру и свойства стали.
Таблица 2. - Протокол испытаний.
Марка стали | Вид обработки | Режим обработки | Твердость, HRC | Предполагаемая структура | ||
tнагр, 0С | tобщ | Vохл | ||||
Отжиг | ||||||
Нормализация | ||||||
Закалка (H2O) | ||||||
Закалка (масло) |
7. График зависимости твердости от скорости охлаждения.
8. Выводы по полученным результатам.
9. Влияние температуры отпуска на структуру и свойства сталей.
Таблица 3. - Протокол испытаний.
Марка стали | ||
Режим обработки | Твердость, HRC | Структура |
Закалка | ||
Закалка + отпуск 1800С | ||
Закалка + отпуск 3500С | ||
Закалка + отпуск 6500С |
10. График зависимости твердости от температуры отпуска.
11. Выводы по полученным результатам и их практическое значение.
12. Общие выводы по работе.
Контрольные вопросы.
1. Диаграмма состояния «железо-цементит» и ее характерные точки.
2. Однофазные структурные составляющие железоуглеродистых сплавов, их характеристика.
3. Двухфазные структурные составляющие железоуглеродистых сплавов, их характеристика.
4. Термическая обработка. Ее виды и цели.
5. Превращения в стали при нагреве.
6. Как получить в стали мелкое зерно аустенита?
7. Перлитное превращение аустенита.
8. Мартенситное превращение аустенита.
9. Чем отличается по структуре и свойствам перлит от сорбита и троостита? Как получить эти структуры?
10. Опишите превращения и структуры, получающиеся в результате отпуска.
11. Укажите критерии выбора температур для того или иного вида термообработки сталей.
12. Установите температуру полного отжига стали, содержащей 0,6 % С. каково назначение отжига?
13. Какую сталь нужно при отжиге охлаждать медленнее – углеродистую или легированную? Почему?
14. На диаграмме изотермического распада переохлажденного аустенита наложите кривые охлаждения для различных способов закалки.
15. Каким требованиям должны удовлетворять закалочные жидкости? Какие применяют жидкости для закалки, каковы их достоинства и недостатки?
Лабораторная работа 4
Дата добавления: 2019-07-17; просмотров: 529; Мы поможем в написании вашей работы! |
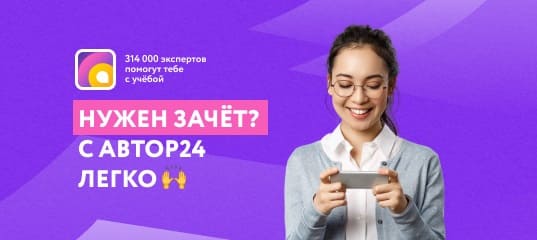
Мы поможем в написании ваших работ!