Краткие сведения о металлографическом анализе
Для изучения внутреннего строения металла применяют металлографический анализ, который широко используется в промышленности для контроля структуры металла полуфабрикатов или готовых деталей с целью обеспечения их качества. Металлографический анализ нашел широкое применение в промышленности при разработке технологии литья, ковки, штамповки, сварки, при исследовании новых сплавов и новых методов обработки, при контроле качества металлических конструкций, а также при установлении причин аварии деталей. Металлографический метод контроля качества введен в ряд действующих стандартов. Так по микроструктуре контролируют величину действительного или природного зерна стали (ГОСТ 5639), загрязненность стали неметаллическими включениями (ГОСТ 1778), степень полосчатости малоуглеродистой стали (ГОСТ 5640), структуру инструментальных сталей в состоянии поставки и ее карбидную неоднородность (ГОСТ 5950).
Металлографический метод исследования включает макроструктурный и микроструктурный анализ.
Макроструктурный анализ проводят визуально (невооруженным глазом) или с помощью лупы с кратностью увеличения изображения до 30 раз.
Микроскопический анализ заключается в исследовании структуры материалов при больших увеличениях с помощью микроскопа. Наблюдаемая структура называется микроструктурой. В зависимости от требуемого увеличения для четкого наблюдения всех присутствующих фаз, их количества, формы и распределения, т.е. структуры в целом, в микроскопах используют:
|
|
· белый свет и обычные оптические системы, являющиеся комбинацией стеклянных линз и призм (оптическая микроскопия с увеличением от 50 до 1500 раз);
· электронные лучи или точнее поток электронов, для создания оптических систем, для которых необходимо применять электромагнитные или электростатические линзы (электронная микроскопия с увеличением от 5000 до 60000 раз).
Применение различного излучения и различных конструкций микроскопов (оптических и электронных) требует различной специальной подготовки объектов и особых методов расшифровки наблюдаемых изображений.
Микроструктурный анализ
Микроструктурным анализом выявляют структурные составляющие, их величину, форму и расположение, неметаллические включения, окисление по границам зерен, глубину обезуглероженного слоя с поверхности, микротрещины, характер и глубину поверхностного насыщения стальных изделий углеродом, азотом и другими элементами. С помощью металлографического микроскопа можно наблюдать структуру металла при общем увеличении от нескольких десятков до 2000 – 3000 раз. Однако полезное увеличение, определяемое условиями дифракции света, не может быть выше 1500 раз. При таком увеличении можно обнаружить раздельно элементы структуры размером не менее 0,2 мкм, что в большинстве случаев достаточно для определения размеров многих фаз, присутствующих в сплавах. Выбор увеличения в пределах, допускаемых оптическим микроскопом, решается в зависимости от конкретной структуры сплавов. Как правило, микроанализ проводят сначала при небольшом увеличении, а затем, в зависимости от строения обнаруживаемой структуры и целей исследования, при больших увеличениях, просматривая в каждом случае ряд участков шлифа.
|
|
Методика проведения микроструктурного анализа
Изучение структуры металла с помощью микроскопа возможно лишь при достаточно интенсивном отражении световых лучей от исследуемой поверхности. Поэтому поверхность образца должна быть специально подготовлена. Для изготовления микрошлифа необходимо вырезать образец из исследуемого материала и получить на нем плоскую блестящую поверхность.
Вырезка образца из исследуемого материала. Детали или образцы небольших размеров и массы после получения требуемой поверхности можно непосредственно установить на столике микроскопа. Если размер или масса детали значительны или если трудно получить на детали плоскую поверхность вследствие сложной конфигурации, необходимо вырезать образец небольших размеров (величиной примерно 10х10х12 мм) и приготовить из него микрошлиф. При вырезании образца необходимо следить за тем, чтобы материал при этом не разогревался, так как значительный нагрев может вызвать изменения в структуре.
|
|
Что касается выбора места, из которого вырезать образец, то здесь можно дать следующие рекомендации:
а) микроструктуру литых материалов и сплавов проверяют в различных сечениях отливки – от самых больших до минимальных. Для изучения микроструктуры слитка вырезают ряд образцов таким образом, чтобы можно было определить изменение структуры по ряду его поперечных сечений;
б) при исследовании влияния пластической деформации на структуру металла место вырезки образца лучше определить после выполнения макроанализа и выявления направления пластической деформации и наиболее характерных участков данной детали. Если деталь подвергали ковке или штамповке, важно изучить участки, где, например, имела место наиболее сложная гибка или большая вытяжка, а также объемы металла на которые не распространялась деформация;
|
|
в) структуру сплавов, подвергающихся термической обработке, проверяют в поверхностных, а также более глубоких слоях детали.
Получение плоской поверхности образца и шлифование плоскости образца. Для получения приблизительно плоской поверхности образцы обрабатывают на токарном или фрезерном станках или на абразивном круге.
После получения приблизительно плоской поверхности образец шлифуют бумажной шкуркой разных номеров. Шлифование производят вручную или на шлифовальном станке, начиная с самой грубой бумаги № 60 и переходя последовательно к шлифованию на бумаге с более мелким абразивным зерном. При переходе с одного номера бумаги на другой необходимо шлифовать в направлении, перпендикулярном к рискам, оставшимся после шлифования на бумаге предыдущего номера, пока эти риски не будут выведены. Также для уменьшения деформации поверхностного слоя надо снижать усилие прижима образца к поверхности шкурки.
Полирование плоскости образца. После окончания шлифования образец промывают для удаления частиц абразивного материала, а затем полируют. Полированием удаляют оставшиеся после тонкого шлифования мелкие дефекты поверхности, риски и т.п. Применяют механический, химикомеханический и электрохимический способы полировки. Механическое полирование проводят на полировальном станке с плоским кругом, обтянутым фетром или сукном, которые смачивают водой с мельчайшим порошком окиси металлов (AI2O3, Fe2O3). Полировать шлиф следует до выведения рисок и получения зеркальной поверхности. Готовый полированный шлиф последовательно промывают водой, спиртом и сушат фильтровальной бумагой.
Изучение микроструктуры. Изучение микроструктуры целесообразно начинать с рассмотрения микрошлифа в нетравленом виде (обычно при увеличении 100х), т.е. непосредственно после полирования, промывки и высушивания. Под микроскопом такой шлиф имеет вид светлого круга, на котором часто можно видеть участки различного цвета (обычно темные), большей частью небольших размеров. Эти участки являются неметаллическими включениями (сульфиды, оксиды, нитриды, графит и др.), образовавшимися в металле в процессе его производства.
Вследствие хрупкости неметаллические включения и часть металлической основы могут полностью выкрашиваться при шлифовании и неосторожном полировании. При осторожном полировании происходит лишь незначительное выкрашивание или несколько более заметное истирание неметаллических включений, что достаточно для обнаружения их под микроскопом вследствие иной отражающей способности, чем у металлической основы. При рассмотрении нетравленого микрошлифа обнаруживают также микропористость – дефект, встречающийся чаще всего в отливках и влияющий на свойства металла.
После просмотра нетравленого шлифа для более полного изучения структуры шлиф травят.
Травление микрошлифов методом избирательного растворения фаз. Для травления микрошлифов в зависимости от химического состава, способа обработки, а также цели исследования применяют различные реактивы. Чаще всего используют слабые спиртовые и водные растворы кислот и щелочей, а также смеси различных кислот. Метод основан на различии физико-химических свойств отдельных фаз и пограничных участков зерен. Любой металл или сплав является поликристаллическим телом, т.е. состоит из большого числа различно ориентированных зерен. Поэтому на приготовленной плоскости микрошлифа находятся зерна, срезанные по разным кристаллографическим плоскостям и имеющие по этим плоскостям неодинаковые свойства. Поэтому степень травимости отдельных зерен на поверхности микрошлифа оказывается различной. Кроме того, на границе зерен обычно располагаются различные примеси; граница зерен имеет более искаженное кристаллическое строение, чем тело зерна. Под действием травления вследствие различных потенциалов зерна и его границы или различных структурных составляющих образуются микроскопические гальванические пары. Границы зерен, а также структурные составляющие с более низким потенциалом будут растворяться быстрее, чем тело зерна или структуры с более высоким потенциалом. В результате неодинакового травления структурных составляющих на поверхности шлифа появляется микрорельеф. Световой поток, направленный на микрошлиф, отразится различно от разных зерен. Благодаря этому микрошлиф при рассмотрении в металлографическом микроскопе выглядит как сочетание светлых (более сильно отражающих свет) и темных (сильнее рассеивающих свет) областей. На рис. 2.2 приведена схема, поясняющая образование изображения в микроскопе. В таблице 2.1 приведены составы и назначения некоторых реактивов. Для травления микрошлиф погружают полированной поверхностью в раствор выбранного состава и через некоторое время (продолжительность травления зависит от состава изучаемого сплава и состава раствора и легко устанавливается экспериментально) вынимают; если полированная поверхность станет слегка матовой, травление считается законченным и шлиф сразу же промывают водой, затем спиртом и высушивают фильтровальной бумагой.
Таблица 2.1. - Реактивы для микроисследования структуры железа и его сплавов
Наименование реактива | Состав реактива | Назначение и особенности применения |
1. Для травления углеродистых, низколегированных сталей и чугуна | ||
1. Спиртовой раствор азотной кислоты (реактив Ржешотарского) | Азотная кислота 1-5 мл, этиловый или метиловый спирт 100 мл. | Реактивы окрашивают перлит в темный цвет, выявляют границы зерен феррита, структуру мартенсита и продуктов отпуска. |
2. Спиртовой раствор пикриновой кислоты (реактив Ижевского) | Пикриновая к-та (кристаллическая) 3-5 г, этиловый или метиловый спирт 100 мл. | |
3. Раствор азотной и соляной кислот | Азотная к-та 25 мл, соляная к-та 50 мл, двухромовокислый калий 12 г, вода 25 мл. | Для выявления величины зерен в закаленной стали. |
2. Для травления высоколегированных сталей | ||
4. Раствор азотной и соляной кислот в глицерине | Азотная к-та 10 мл, соляная к-та 20–30 мл, глицерин 30 мл. | |
5. Царская водка | Соляная кислота 3 ч, азотная кислота 1 ч. | Для выявления структуры нержавеющих сталей и сплавов. Перед употреблением реактив необходимо выдержать 20 – 30 ч. |
6. Солянокислый раствор хлорного железа | Хлорное железо 5 г, соляная кислота 50 мл, вода 100 мл. | Для исследования структуры высоконикелевой нержавеющей аустенитной стали. |
3. Для выявления карбидов, фосфидов, вольфрамидов | ||
7. Щелочной раствор пикрата натрия | Пикриновая кислота 2 г, едкий натр 25 г, вода 100 мл. | Цементит окрашивается в темный цвет; карбиды хрома и вольфрама не окрашиваются. Применяется в кипящем состоянии. |
Металлографические микроскопы. После травления шлиф исследуют с помощью металлографического микроскопа. Микроскопы, позволяющие рассматривать непрозрачные тела в отраженном свете, называются металлографическими или металломикроскопами. Они состоят из оптической системы, осветительной системы с фотографической аппаратурой и механической системы.
Оптическая система металлографического микроскопа включает в себя объектив, окуляр и ряд вспомогательных оптических элементов: зеркала, призмы и т.п. (рис. 2.3).
Объектив дает действительное, увеличенное, обратное изображение шлифа и представляет сложное сочетание линз, располагающихся в одной общей оправке и находящихся в непосредственной близости к шлифу. Объектив имеет фронтальную плоско – выпуклую линзу, определяющую возможное увеличение и ряд так называемых коррекционных линз, предназначенных для устранения нежелательных эффектов – хроматической и сферической аберраций, возникающих при прохождении лучей через фронтальную линзу. Окуляром называется лин
за, обращенная к глазу. Окуляры дают не только мнимое увеличение (т.е. увеличение промежуточного изображения), но и исправляют оптические дефекты, которые полностью не устраняются даже в объективах сложной конструкции. В металлографических микроскопах применяют окуляры трех типов: обычные (Гюйгенса), компенсационные и проекционные. Увеличение окуляра меньше, чем объектива, и подбирается таким образом, чтобы можно было достаточно четко рассмотреть изображение, создаваемое объективом. Если увеличение окуляра слишком мало, детали структуры, имеющиеся в изображении, полученном объективом, не будут выявлены; в то же время при слишком большом увеличении окуляра ухудшается четкость изображения и уменьшается поле зрения. Общее увеличение, которое дает микроскоп, можно принять равным произведению увеличений окуляра и объектива.
Максимальное полезное увеличение микроскопа определяется по формуле:
М max = ,
где d1 – максимальная разрешающая способность человеческого глаза, равная 0,3 мм; d – максимальная разрешающая способность оптической системы микроскопа.
Максимальная разрешающая способность оптической системы определяется из условий дифракции согласно уравнению d = l /(2 n sin ( a /2)), где l - длина волны света (для белого света 600 нм); n – коэффициент преломления; a /2 - половина угла раскрытия входящего светового пучка. Величина n sin ( a /2) называется числовой апертурой, которая всегда указывается наряду с увеличением объектива на его оправе.
Для четкого изображения объекта надо, чтобы общее увеличение не превосходило полезное увеличение системы. Полезное увеличение в данной оптической системе для видимого света можно принять равным 500 – 1000 апертур взятого объектива. Так, для объектива с апертурой 0,65 максимальное полезное увеличение оптической системы равно 650. Поскольку этот объектив дает увеличение в 40 раз, то увеличение окуляра не должно быть больше 15 раз.
Осветительная система микроскопа состоит из источника света, серии линз, светофильтров и диафрагм. В качестве источников света используют низковольтные электрические лампы накаливания, галогенные лампы.
Для уменьшения рассеяния световых лучей и повышения четкости изображения в осветительную систему введены дополнительные линза и конденсор, концентрирующие пучок лучей на рассматриваемом участке микрошлифа. Диафрагмы ограничивают сечение светового пучка, а светофильтры (цветные, матовые или дымчатые стеклянные пластинки) отбирают лучи определенной длины волны и позволяют установить нужную интенсивность освещения с тем, чтобы избежать излишнего утомления глаз наблюдателя. Наибольшей чувствительностью человеческий глаз обладает к желто-зеленым цветам, поэтому применение желто-зеленого светофильтра позволяет более четко наблюдать особенности структуры.
При микроанализе для большинства металлов и других непрозрачных материалов и сплавов применяют наблюдение в светлом поле, т.е. при вертикальном освещении, когда световые лучи попадают на микрошлиф через объектив, который собирает их на поверхности шлифа.
Разновидностью освещения является косое освещение. Оно достигается смещением апертурной диафрагмы или включением между объективом и полупрозрачной пластинкой призмы косого освещения. При таком освещении еще больше возрастает контрастность изображения.
Механическая система микроскопа имеет штатив, тубус и предметный столик. Микрошлиф устанавливается на предметном горизонтальном столике вниз поверхностью, подготовленной для исследования. Столик может перемещаться в двух взаимно перпендикулярных горизонтальных плоскостях с помощью специальных винтов. Это позволяет перемещать шлиф на нужное расстояние и просматривать структуру в различных участках, без изменения выбранного фокусного расстояния.
Для получения четкого изображения микрошлиф после установки его на столике наводят на фокус. Для этого в штативе микроскопа имеется макрометрический винт, вращением которого перемещают столик в вертикальном направлении, обеспечивая приблизительное фокусирование. Точное фокусирование достигается микрометрическим винтом один оборот которого смещает объектив к шлифу на доли миллиметра. Чем больше увеличение объектива, тем меньше должно быть расстояние между шлифом и объективом.
По устройству различают микроскопы вертикальные и горизонтальные. Наиболее широко применяются вертикальные микроскопы МИМ-6, МИМ-7, ММР – 4, ММР – 2Р. При непосредственном визуальном наблюдении эти микроскопы имеют полезное увеличение до 950 раз, а при фотографировании – до 1416 раз.
При металлографическом анализе структуры ее можно оценить одним из трех способов: описательным, полуколичественным (балловая оценка) или количественным.
Описательный способ требует лишь перечисления структурных составляющих; полуколичественный – оценивает примерное содержание тех или иных структурных составляющих путем сопоставления реальной микроструктуры с эталонными структурами, приведенными в ГОСТах; количественный анализ предусматривает измерение достаточно большого количества структурных элементов с последующей статистической обработкой результатов измерения.
Для проведения количественного анализа применяется окуляр-микрометр, т.е. окуляр, в который вставлена стеклянная пластинка, разделенная на некоторое количество частей, обычно через 0,1 мм. Цена деления шкалы окуляр-микрометра зависит от применяемого объектива. Для определения цены деления окуляр-микрометра существует объект-микрометр. Он представляет из себя шлиф с линейкой на которой нанесен 1 мм, разделенный на 100 частей. Для определения цены деления окуляр-микрометра помещают перед объективом вместо шлифа объект-микрометр; в окуляре при этом отчетливо видна сетка делений объект-микрометра. Далее, окуляр-микрометр вращают таким образом, чтобы его шкала совпала со шкалой объект-микрометра. Затем, вращая винты предметного столика, совмещают какие-либо деления этих шкал и принимают их в качестве нулевых; подсчитывают число делений на определенном участке (желательно наибольшем) до совпадения конечных делений этих шкал. В этом случае цена одного деления окуляр-микрометра dок определяется по формуле:
doк= Dоб*M/N,
где Dоб =0,01 мм – цена деления шкалы объект-микрометра; M – число делений шкалы объект-микрометра от начальных до конечных взаимно совмещенных делений; N – число делений шкалы окуляр-микрометра от начальных до конечных взаимно совмещенных делений.
Зная увеличение всей оптической системы (т.е. увеличение объектива и окуляр-микрометра), можно с помощью окуляр-микрометра зрительно определить протяженность какой-либо резко отличающейся структурной области, что необходимо, например, при исследовании или контроле химико-термической обработки стали (цементации, азотирования и т.д.) и определении глубины насыщенного поверхностного слоя.
Порядок выполнения работы
1. Получить образец металла для изготовления микрошлифа.
2. Заторцевать поверхность шлифа, подлежащую исследованию на наждачном круге (постараться получить плоскую поверхность).
3. Произвести шлифовку образца на наждачной бумаге. Для этого образец прижать рукой к наждачной бумаге заторцованной стороной так, чтобы направление шлифования было перпендикулярно рискам, оставшимся от предыдущей обработки. Шлифовать до тех пор, пока старые риски не исчезнут. Шлиф обтереть ватой от приставшей наждачной пыли и продолжать шлифование на бумаге следующего номера, переходя постепенно на бумагу все более мелких номеров. После шлифовки на бумаге последнего номера поверхность микрошлифа должна иметь мелкие риски в одном направлении.
4. Произвести полирование поверхности шлифа. Полирование производится на станке с вращающимся плоским кругом, покрытым сукном. В процессе полирования образец нужно прижимать к поверхности круга всей плоскостью шлифа и перемещать от центра круга к периферии или «восьмеркой». Полирование производить до тех пор, пока не будут выведены все риски, и поверхность шлифа не станет зеркальной. После полирования шлиф промыть водой, затем спиртом и, не задевая поверхности шлифа пальцами, просушить, прикладывая к фильтровальной бумаге.
5. Рассмотреть шлиф до травления. Для этого выполнить следующее:
5.1. Внимательно изучить инструкцию по эксплуатации микроскопа, на котором предстоит работать.
5.2. Подобрать объектив и окуляр так, чтобы установить увеличение порядка 500 – 600 раз.
5.3. Зарисовать видимое в окуляре изображение.
6. Произвести травление шлифа. Для этого погрузить шлиф на время от 30-40 секунд до 1,5-2 минут в реактив или ватным тампоном, смоченным реактивом – травителем, протирать шлиф до тех пор, пока поверхность его не станет матовой. Протравленный шлиф промыть спиртом, а затем просушить фильтровальной бумагой.
7. Рассмотреть протравленный шлиф под микроскопом. Определить структурные составляющие. Результаты занести в таблицу 1.
8. Получить подготовленные микрошлифы разных марок чугуна.
9. Рассмотреть нетравленую часть поверхности шлифа. Результаты занести в таблицу 2.
10. Рассмотреть травленую часть поверхности шлифа. Определить структурные составляющие. Результаты занести в таблицу 2.
Содержание отчета
1. Название работы.
2. Цель работы.
3. Приборы и принадлежности.
4. Краткие сведения из теории.
4.1. Задачи металлографического анализа.
4.2. Описание методики изготовления и травления микрошлифа.
4.3. Описание устройства и принципа действия металлографического микроскопа.
5. Результаты исследования структуры сталей:
Таблица 1.
Дата добавления: 2019-07-17; просмотров: 823; Мы поможем в написании вашей работы! |
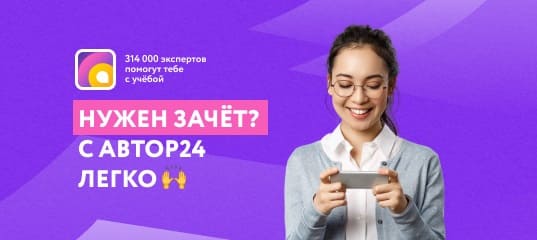
Мы поможем в написании ваших работ!