Перечень тем лабораторных работ
Таблица 1 – Темы лабораторных работ
№ п.п. | Номер темы дисциплины | Наименование темы лабораторной работы |
1 | 1 | Измерение твердости металлов и сплавов |
2 | 2 | Определение микроструктуры Fe-C сплавов |
3 | 4 | Проведение термической обработки сталей |
4 | 4 | Определение влияния термической обработки на структуру и свойства алюминиевых сплавов |
Рекомендации по подготовке и проведению лабораторных работ
Лабораторная работа 1
Измерение твердости металлов и сплавов
Цель работы:
1) ознакомление с методами определения твердости;
2) приобретение практических навыков в работе с приборами для измерения твердости.
Приборы и материалы:
1) твердомер Бринелля, микроскоп МПБ – 3;
2) твердомер Роквелла;
3) образцы.
Краткие сведения из теории
При проектировании и производстве машин, механизмов, инструментов те или иные детали должны обладать определенными механическими свойствами. Механические свойства металлов характеризуют сопротивление материала деформации и разрушению под действием внешних нагрузок. Практически все методы определения механических свойств являются разрушающими. Для проведения испытаний необходимы специальные машины, процессы испытания довольно длительны, особенно если учесть весьма продолжительный процесс изготовления специальных образцов.
Механические свойства и физические свойства зависят от многих факторов: от состава материала, вида обработки (пластической деформации, термической обработки). Поэтому в процессе изготовления тех или иных деталей необходимо контролировать свойства, особенно механические. Как отмечено ранее, обычные методы испытания механических свойств не могут быть использованы на промежуточных стадиях изготовления деталей вследствие длительности и дороговизны изготовления образцов, длительности самого процесса испытания. В этом случае пользуются методами определения твердости.
|
|
Твердостью называют способность тела сопротивляться проникновению в него другого, более твердого тела.
Наибольшее применение получило измерение твердости вдавливанием в поверхность металла наконечника (индентора), изготовленного из малодеформирующегося материала и имеющего форму шарика, конуса, пирамиды. В результате вдавливания достаточно большой нагрузкой поверхностные слои металла, находящиеся под наконечником и вблизи него, пластически деформируются. После снятия нагрузки остается отпечаток. Особенность происходящей при этом деформации заключается в том, что она протекает только в небольшом объеме, окруженном недеформированным металлом. При измерении твердости вдавливанием пластическую деформацию испытывают не только пластичные металлы, но и металлы (например, чугун), которые при обычных механических испытаниях (на растяжение, сжатие, кручение, изгиб) разрушаются хрупко почти без заметной пластической деформации.
|
|
Измерения твердости получили достаточно широкое распространение в силу следующих факторов:
1. Между твердостью пластичных материалов, определяемой способом вдавливания, и другими механическими свойствами (главным образом пределом прочности), существует количественная зависимость. Подобная количественная зависимость не наблюдается для хрупких материалов, которые при испытаниях на растяжение (или сжатие, изгиб, кручение) разрушаются без заметной пластической деформации, а при измерении твердости получают пластическую деформацию. Однако в ряде случаев и для этих металлов (например, серых чугунов) наблюдается качественная зависимость между пределом прочности и твердостью; возрастанию твердости обычно соответствует увеличение предела прочности на сжатие. Кроме того, по значениям твердости можно судить о некоторых пластических свойствах металлов и сплавов. Твердость, определенная вдавливанием, характеризует также предел выносливости некоторых металлов, в частности, меди, дюралюминия и сталей в отожженном состоянии.
|
|
2. Измерение твердости по технике выполнения значительно проще, чем определение прочности, пластичности и вязкости. Измерения твердости выполняются быстро, например, при вдавливании конуса за 30 – 60 с, а при вдавливании шарика за 1–3 мин. Твердость проверяют на отливках, прокате, поковках, штамповках, а также готовых деталях и инструменте как в термически обработанном, так и в необработанном состояниях.
3. Измерение твердости обычно не влечет за собой разрушения проверяемой детали, и после измерения ее можно использовать по своему назначению, в то время как для определения прочности, пластичности и вязкости необходимо изготовление специальных образцов из детали.
4. Твердость можно измерять на деталях небольшой толщины, а также в очень тонких слоях, не превышающих (для некоторых способов измерения твердости) десятых долей миллиметра.
Все известные в настоящее время методы измерения твердости можно разделить на следующие группы:
1. Статические – измерение твердости по методу вдавливания. К таким методам следует отнести метод Бринелля, метод Роквелла, метод Виккерса.
|
|
2. Динамические:
а) динамически-пластический метод, основанный на измерении величины отпечатка, оставленного индентором в результате ударного приложения нагрузки (прибор типа «Польди»);
б) динамически-упругий метод, основанный на измерении высоты упругого отскока индентора (прибор «Шора»).
Наибольшее распространение получили статические методы.
Метод Бринелля
Способ измерения твердости вдавливанием шарика (ГОСТ 9012-59) используется для определения твердости как металлов, так и полимерных материалов. Метод основан на вдавливании стального закаленного шарика диаметром 1 мм, 2,5 мм, 5 мм или 10 мм под определенной нагрузкой P от 62,5 до 3000 кг.
Рисунок 1.1. Схема прибора Бринелля. |
1 – столик для установки измеряемого образца; 2 – маховик; 3 – грузы; |
Испытание твердости по Бринеллю производят на прессах. В некоторых конструкциях давление осуществляется гидравлическим способом, а в других – грузами, передвижение которых осуществляется электродвигателем. Для замера твердости испытуемый образец ставят на столик 1 (рис. 1.1), расположенный на подъемном винте. Подъемным винтом при помощи маховика 2 поднимают столик с образцом до соприкосновения образца с шариком 4 (до отказа), создавая этим предварительную нагрузку. Основная нагрузка на образец через шарик прилагается при помощи рычажной системы, работающей от электромотора 5. На длинном плече рычага имеется подвеска, на которую устанавливают съемные грузы 3. В зависимости от количества этих грузов нагрузка на образец может меняться от 62,5 до 3000 кг. Эта нагрузка действует в течение определенного времени, обычно 10 – 60 с, в зависимости от твердости испытуемого материала, после чего вал двигателя, вращаясь в обратную сторону, соответственно перемещает коромысло и снимает нагрузку. После автоматического выключения двигателя, поворачивая маховик 2 против часовой стрелки, опускают столик прибора и снимают образец. Шарик оставляет на поверхности металла отпечаток, имеющий вид сферической поверхности, по площади которого судят о твердости испытуемого металла. Диаметр отпечатка d измеряют с помощью специальной лупы или микроскопа. На рис.2 дано изображение отпечатка, видимое в микроскоп, с наложенной на него шкалой окуляра. По шкале окуляра определяют диаметр отпечатка в мм. На рисунке 1.2 диаметр отпечатка равен 3,25 мм. Число твердости по Бринеллю (НВ) определяется отношением нагрузки, действующей на шарик, к площади полученного отпечатка:
НВ =
кг/мм2, (1)
где НВ – число твердости по Бринеллю, Р – нагрузка в кг, F – площадь полученного отпечатка, мм2.
Площадь отпечатка может быть выражена через диаметр вдавливаемого шарика D и диаметр отпечатка d:
F = (D -
), мм2. (2)
Полученное число твердости при прочих равных условиях определяется диаметром отпечатка d. Последний тем меньше, чем выше твердость испытуемого металла. Однако при вдавливании шарика на разную глубину, т.е. с разной нагрузкой для одного и того же материала, не соблюдается закон подобия между получаемыми диаметрами отпечатка. Наибольшие отклонения наблюдаются, если шарик вдавливается с малой нагрузкой и оставляет отпечаток небольшого диаметра или вдавливается с очень большой нагрузкой и оставляет отпечаток большого диаметра, приближающегося по величине к диаметру шарика. Поэтому твердость измеряют при постоянном соотношении между величиной нагрузки Р и квадратом диаметра шарика D2. Отношение Р/D2 (Р – нагрузка, кг; D – диаметр шарика, мм) обозначается буквой К и может равняться 30; 10; 2,5. Это соотношение должно быть различным для металлов разной твердости. Перед проведением испытаний на твердость выбирают диаметр шарика в зависимости от толщины испытуемого образца металла и нагрузку в зависимости от твердости металла.
В таблице 1.1 приведены принятые ГОСТом 9012-59 нормы для испытаний по Бринеллю
Таблица 1.1 - Условия испытаний металлов на твердость по Бринеллю (ГОСТ 9012–59)
Металлы | Твердость НВ | Минимальная толщина испытуемого образца, мм | Соотношение между Р и D2 | Диаметр Шарика D, мм | Нагрузка Р, кгс | Выдержка под наг- рузкой, сек | |
Черные |
140-450 | От 6 до 3 |
Р=30 D2 | 10,0 | 3000 |
10 | |
От 4 до 2 | 5,0 | 750 | |||||
Менее 2 | 2,5 | 187,5 | |||||
140 | Более 6 |
Р=10 D2 | 10,0 | 1000 |
10 | ||
От 6 до 3 | 5,0 | 250 | |||||
Менее 3 | 2,5 | 62,5 | |||||
Цветные |
130 | От 6 до 3 |
Р=30 D2 | 10,0 | 3000 |
30 | |
От 4 до 2 | 5,0 | 750 | |||||
Менее 2 | 2,5 | 187,5 | |||||
35-130 | От 9 до 3 |
Р=10 D2 | 10,0 | 1000 |
30 | ||
От 6 до 3 | 5,0 | 250 | |||||
Менее 3 | 2,5 | 62,5 | |||||
8-35 | Более 6 |
Р=2,5 D2 | 10,0 | 250 |
60 | ||
От 6 до 3 | 5,0 | 62,6 | |||||
Менее 3 | 2,5 | 15,6 | |||||
При испытании стали и чугуна Р=30D2, меди, латуни, бронзы Р=10D2, алюминия, подшипниковых сплавов Р=2,5D2.
Следует заметить, что при измерении твердости шариком определенного диаметра и с установленными нагрузками нет необходимости производить расчеты по указанным выше формулам (1) и (2). На практике твердость определяют по таблицам, составленным на основании формул (1) и (2) и указывающим число НВ для разных диаметров отпечатков и нагрузок (табл. 2). Следует учесть, что таблица составлена для К = 30.
По величине твердости можно с некоторым приближением судить о прочности металла при растяжении, так как между числом твердости НВ и пределом прочности σв (МПа) существует следующая зависимость:
Сталь с твердостью НВ: | σв (МПа) |
120 – 175 | σВ»3,4 НВ |
175 – 450 | σВ»3,6 НВ |
Медь, латунь, бронза: | |
Отожженная | σВ»5,5 НВ |
Наклепанная | σВ»4,0 НВ |
Алюминий и алюминиевые сплавы с твердостью НВ: | |
20 – 45 | σВ»(2,3 – 2,6) НВ |
В меньшей степени соблюдается точная количественная зависимость между числами твердости НВ и пластичностью и пределом выносливости материала.
Измерение твердости вдавливанием стального шарика не является универсальным способом. Основной недостаток такого метода определения твердости – невозможность испытывать металлы, имеющие твердость более 450 НВ; измерять твердость тонкого поверхностного слоя (толщиной менее 1 – 2 мм). Чтобы при вдавливании шарика не происходило продавливания материала, толщина его должна быть не менее десятикратной глубины отпечатка.
Преимущества этого метода – простота, достаточная точность, минимальные требования к чистоте поверхности по сравнению с другими методами.
Метод Роквелла
Испытание твердости металлов по способу Роквелла (ГОСТ 9013 – 59) производится вдавливанием в испытуемый образец алмазного конуса с углом при вершине 120˚ или стального закаленного шарика D=1,59 мм под действием двух последовательно прилагаемых нагрузок – предварительной (10 кг) и общей (предварительная + основная) в 60, 100 или 150 кг. Предварительное нагружение проводят для того, чтобы исключить влияние упругой деформации и шероховатости поверхности образца на результаты измерений.
О твердости материала судят не по диаметру отпечатка, а по разности глубин вдавливания, на которые проникает алмазный конус или стальной шарик под действием двух последовательно приложенных нагрузок (предварительной и основной). Эта разность характеризует твердость испытуемого металла по Роквеллу.
Для численной характеристики твердости введена условная шкала с цифрами, нанесенными в порядке, обратном движению в момент приложения нагрузки. Внедрение наконечника на 0,002 мм соответствует перемещению стрелки на одно деление. Число твердости по Роквеллу отвлеченное и выражается в условных единицах HR; после R указывается шкала В, С или А. Например, HRB, HRC или HRA. Числа твердости по Роквеллу, выраженные в условных единицах, связываются с углублением конуса или шарика формулами
HRC = 100 - (для шкалы С),
HRB = 130 - (для шкалы В),
где – соответственно глубина внедрения индентора в испытуемый образец под действием предварительной и общей нагрузки. Следовательно, чем тверже измеряемый материал и, соответственно, меньше h , тем больше должно быть число твердости. Наоборот, чем мягче измеряемый материал и больше величина h, тем меньше число твердости, т.е. числа твердости по Роквеллу возрастают с увеличением твердости материала, что позволяет сравнить числа твердости по Роквеллу с числами Бринелля. Вместе с тем числа твердости по Роквеллу не имеют той размерности и того физического смысла, который имеют числа твердости по Бринеллю. Однако числа твердости по Роквеллу можно пересчитать на числа твердости по Бринеллю с помощью таблицы (табл. 1.2).
На циферблате индикатора прибора имеются две шкалы – красная внутренняя и черная наружная. Красной шкалой пользуются при испытании на твердость шариком: она смещена относительно нулевого положения черной шкалы на 30 делений. Необходимость смещения вызвана тем, что глубина вдавливания при стандартных нагрузках на шарик получается более 100 делений. Черной шкалой пользуются при испытании на твердость алмазным наконечником: ее нулевое положение должно совпадать с начальным положением стрелки.
Твердость на приборе Роквелла можно измерять:
1. Алмазным конусом с нагрузкой 150 кг проводят измерения для закаленной или низкоотпущенной стали с твердостью более 450 НВ; для материалов средней твердости (более 230 НВ) как более быстрый способ определения, оставляющий меньший след на поверхности, чем при испытании по Бринеллю; для определения твердости тонких поверхностных слоев, но толщиной более 0,5 мм (например, цементованного слоя). В этом случае значение твердости характеризуется цифрой, указываемой стрелкой на черной шкале С циферблата и обозначается Н RC.
2. Алмазным конусом с нагрузкой 60 кг применяют для очень твердых металлов (более 70 HRC), например твердых сплавов, когда вдавливание алмазного конуса с большой нагрузкой может вызвать выкрашивание алмаза, а также для измерения твердых поверхностных слоев (0,3 – 0,5 мм) или тонких образцов (пластинок). В этом случае значения твердости также характеризуются цифрой, указываемой стрелкой на черной шкале С циферблата, но обозначаются HRA. Числа HRA можно перевести на числа HRC по следующей формуле HRC =2 HRA – 104.
3. Стальным шариком с общей нагрузкой 100 кг твердость определяют для мягкой (отожженной) стали или отожженных цветных сплавов в деталях или образцах толщиной 0,8 – 2 мм, т.е. в условиях, когда измерение по Бринеллю, выполняемое шариком большого диаметра, может вызвать смятие образца. В этом случае значения твердости характеризуются цифрой, указываемой стрелкой по красной шкале В циферблата и обозначаются HRB.
Определение твердости по Роквеллу очень распространено для контроля качества продукции, так как оно позволяет испытывать как мягкие, так и самые твердые материалы, а также твердые поверхностные слои (например, цементованный слой).
Получающиеся от стального шарика и алмаза отпечатки очень малы и не портят поверхность детали, длительность испытания мала – 40-60 секунд, величина твердости читается прямо на циферблате прибора без дополнительных измерений и пересчетов.
Недостатком этого метода является необходимость соблюдения параллельности проверяемых поверхностей, относительно низкая точность показаний по сравнению с другими методами и необходимость подготовки поверхности.
Метод Виккерса
При испытании твердости по Виккерсу (ГОСТ 2999-75) в испытуемый металл вдавливают четырехгранную алмазную пирамиду с углом при вершине 136˚. Твердость по Виккерсу HV определяют, как удельное давление, приходящееся на единицу площади отпечатка:
кг/мм2,
где Р – нагрузка на пирамиду (кг); α – угол между противоположными гранями пирамиды, α = 136˚; d – среднее арифметическое длины обеих диагоналей отпечатка (мм). Поэтому числа твердости по Бринеллю и Виккерсу имеют одинаковую размерность и для материалов с твердостью до 400 ед. совпадают. Благодаря большому углу в вершине пирамиды, даже малой глубине отпечатка соответствует диагональ отпечатка большой величины. Это увеличивает чувствительность метода и делает его пригодным для изучения свойств тонких поверхностных слоев металла (например, при обезуглероживании, поверхностном наклепе, химико-термической обработке поверхности и тонких листов – до 3 мм и т.п.).
При испытании применяют нагрузки 5,10,20,30,50,100 и 120 кг. При вдавливании пирамиды соотношение между диагоналями получающегося отпечатка при изменении нагрузки остается постоянным, что позволяет изменять ее в широких пределах. Величина нагрузки выбирается в зависимости от целей исследования, толщины и твердости исследуемого металла.
Образцы для испытания на твердость по Виккерсу должны иметь полированную поверхность. Толщина образца должна быть не менее 1,5 диагонали отпечатка. Прибор Виккерса позволяет измерять твердость мягких металлов и очень твердых сплавов. Особенно он удобен при измерении твердости поверхностно-упрочненных деталей, имеющих сложную конфигурацию. Однако каждое определение твердости по Виккерсу занимает много времени и требует тщательной подготовки поверхности испытуемого образца, что является основным недостатком этого метода, препятствующим широкому применению его в цеховых условиях.
Измерение микротвердости
Для изучения свойств и превращений в сплавах необходимо не только знать «усредненную» твердость, представляющую твердость в результате суммарного влияния присутствующих в сплаве фаз и структурных составляющих, но и определять твердость отдельных фаз и структур сплава. В данном случае объем, деформируемый вдавливанием, должен быть меньше объема (площади) измеряемого зерна, поэтому прилагаемая нагрузка выбирается небольшой. Для определения микротвердости (ГОСТ 9450 – 76) наиболее часто применяют алмазный наконечник в виде четырехгранной пирамиды с квадратным основанием и углом между гранями при вершине 1360, т.е. таким же, как и в пирамиде для измерения по Виккерсу (что облегчает пересчет на числа Виккерса). При испытаниях применяют нагрузки от 2 до 200 г. Микротвердость рассчитывается как отношение нагрузки, приложенной к наконечнику к площади поверхности отпечатка:
Н = .
В случае измерений с помощью четырехгранной пирамиды с квадратным основанием микротвердость рассчитывается по формуле:
кг/мм2,
где Р – нагрузка на пирамиду (кг); α – угол между противоположными гранями пирамиды, α = 136˚; d – среднее арифметическое длины обеих диагоналей отпечатка (мм).
Для осуществления измерений поверхность образца шлифуют и полируют, а при необходимости подвергают травлению реактивами, применяемыми для микроанализа соответствующих сплавов.
Таблица 1.2 - Перевод твердости HV в HR и HВ
Твердость по Виккерсу | Твердость по Бринеллю D= 10 мм, Р= 3000 кг | Твердость по Роквеллу При шкале | |||
Диаметр отпечатка, мм | Число Твердости | С 150 кг | В 100 кг | А 60 кг | |
1224 | 2,20 | 780 | 72 | - | 84 |
1116 | 2,25 | 745 | 70 | - | 83 |
1022 | 2,30 | 712 | 68 | - | 82 |
941 | 2,35 | 682 | 66 | - | 81 |
868 | 2,40 | 653 | 64 | - | 80 |
804 | 2,45 | 627 | 62 | - | 79 |
746 | 2,50 | 601 | 60 | - | 78 |
694 | 2,55 | 578 | 58 | - | 78 |
650 | 2,60 | 555 | 56 | - | 77 |
606 | 2,65 | 534 | 54 | - | 76 |
587 | 2,70 | 514 | 52 | - | 75 |
551 | 2,75 | 495 | 50 | - | 74 |
534 | 2,80 | 477 | 49 | - | 74 |
502 | 2,85 | 461 | 48 | - | 73 |
4747 | 2,90 | 444 | 46 | - | 73 |
460 | 2,95 | 429 | 45 | - | 72 |
435 | 3,00 | 415 | 43 | - | 72 |
423 | 3,05 | 401 | 42 | - | 71 |
401 | 3,10 | 388 | 41 | - | 71 |
390 | 3,15 | 375 | 40 | - | 70 |
380 | 3,20 | 363 | 39 | - | 70 |
361 | 3,25 | 352 | 38 | - | 69 |
344 | 3,30 | 341 | 36 | - | 68 |
334 | 3,35 | 331 | 35 | - | 67 |
320 | 3,40 | 321 | 33 | - | 67 |
311 | 3,45 | 311 | 32 | - | 66 |
303 | 3,50 | 302 | 31 | - | 66 |
292 | 3,55 | 293 | 30 | - | 65 |
285 | 3,60 | 285 | 29 | - | 65 |
278 | 3,65 | 277 | 28 | - | 64 |
270 | 3,70 | 269 | 27 | - | 64 |
261 | 3,75 | 262 | 26 | - | 63 |
255 | 3,80 | 255 | 25 | - | 63 |
249 | 3,85 | 248 | 24 | - | 62 |
240 | 3,90 | 241 | 23 | 102 | 62 |
235 | 3,95 | 235 | 21 | 101 | 61 |
Таблица № 1.2. Продолжение.
Твердость по Виккерсу | Твердость по Бринеллю D= 10 мм, Р= 3000 кг | Твердость по Роквеллу При шкале | |||
диаметр отпечатка, мм | число твердости | С 150 кг | В 100 кг | А 60 кг | |
228 | 4,00 | 229 | 20 | 100 | 61 |
222 | 4,05 | 223 | 19 | 99 | 60 |
217 | 4,10 | 217 | 17 | 98 | 60 |
213 | 4,15 | 212 | 15 | 97 | 59 |
208 | 4,20 | 207 | 14 | 95 | 59 |
201 | 4,25 | 201 | 13 | 94 | 58 |
197 | 4,30 | 197 | 12 | 93 | 58 |
192 | 4,35 | 192 | 11 | 92 | 57 |
186 | 4,40 | 187 | 9 | 91 | 57 |
183 | 4,45 | 183 | 8 | 90 | 56 |
178 | 4,50 | 179 | 7 | 90 | 56 |
174 | 4,55 | 174 | 6 | 89 | 55 |
171 | 4,60 | 170 | 4 | 88 | 55 |
166 | 4,65 | 167 | 3 | 87 | 54 |
162 | 4,70 | 163 | 2 | 86 | 53 |
159 | 4,75 | 159 | 1 | 85 | 53 |
155 | 4,80 | 156 | 0 | 84 | 52 |
152 | 4,85 | 152 | - | 83 | - |
149 | 4,90 | 149 | - | 82 | - |
148 | 4,95 | 146 | - | 81 | - |
143 | 5,00 | 143 | - | 80 | - |
140 | 5,05 | 140 | - | 79 | - |
138 | 5,10 | 137 | - | 78 | - |
134 | 5,15 | 134 | - | 77 | - |
131 | 5,20 | 131 | - | 76 | - |
129 | 5,25 | 128 | - | 75 | - |
127 | 5,30 | 126 | - | 74 | - |
123 | 5,35 | 123 | - | 73 | - |
121 | 5,40 | 121 | - | 72 | - |
118 | 5,45 | 118 | - | 71 | - |
116 | 5,50 | 116 | - | 70 | - |
115 | 5,55 | 114 | - | 68 | - |
113 | 5,60 | 111 | - | 67 | - |
110 | 5,65 | 110 | - | 66 | - |
109 | 5,70 | 109 | - | 65 | - |
108 | 5,75 | 107 | - | 64 | - |
Выполнение работы
Задание
Определить твердость образцов углеродистой стали, чугунов и цветных сплавов на приборе Бринелля и Роквелла. Привести все значения твердости исследуемых образцов к числу твердости по Бринеллю. Определить предел прочности испытуемых образцов.
Порядок проведения работы
1.Получить образцы для определения твердости на приборах Бринелля и Роквелла.
2.Определить твердость на прессе Бринелля:
а) найти необходимую величину нагрузки и диаметр шарика в зависимости от вида и толщины испытуемого материала, пользуясь табл.1;
б) установить образец на столике шлифованной поверхностью кверху. Центр отпечатка должен находиться от края образца на расстоянии не менее 2,5 диаметров отпечатка; расстояние между центрами двух смежных отпечатков должно быть не менее четырех диаметров отпечатка;
в) привести образец в соприкосновение с шариком вращением маховика по часовой стрелке до полного упора;
г) включить электродвигатель нажатием кнопки пускателя мотора и проследить за ходом испытания. Выдержка нагрузки на образец, включение мотора и освобождение образца от нагрузки происходят автоматически. Приложение полной нагрузки и выдержка сигнализируются зажиганием сигнальной лампы;
д) опустить стол с испытуемым образцом вращением маховика против часовой стрелки;
е) получить на том же образце еще два отпечатка;
ж) измерить при помощи лупы Бринелля диаметры отпечатков в двух взаимно перпендикулярных направлениях;
з) результаты замеров занести в табл.3;
и) пользуясь табл.2, по диаметру отпечатка определить твердость по Бринеллю;
к) найдя среднее значение диаметра отпечатка во всех трех измерениях, определить твердость, пользуясь формулами 1 и 2.
3.Определить твердость на приборе Роквелла (рис. 1.3):
а) найти необходимую величину нагрузки и вид индентора в зависимости от материала образцов;
б) установить необходимую нагрузку с помощью рукоятки 5 и выбранный индентор 1;
в) установить образец на столик 2 прибора;
г) привести образец в соприкосновение с наконечником при помощи маховика 4;
д) создать предварительную нагрузку в 10 кг, для этого вращением маховика продолжить подъем столика до тех пор, пока малая стрелка индикатора 3 не окажется против отметки на шкале, а большая не станет примерно в вертикальное положение;
е) с помощью ручки 6 вращать шкалу индикатора с циферблатом до тех пор, пока для обоих наконечников – шарика и алмаза, нуль черной шкалы не совпадет с большой стрелкой;
ж) включить основную нагрузку, для чего освободить рукоятку 7 движением вправо. Время приложения основной нагрузки 5-7 сек;
з) снять основную нагрузку, для чего рукоятку 7 плавно вернуть в исходное положение;
и) записать число твердости по Роквеллу, т.е. цифру, на которую указывает на шкале циферблата большая стрелка. Если индентором является шарик, отсчет произвести по красной шкале индикатора, а если алмазный конус – по черной;
к) разгрузить образец полностью, для чего повернуть маховик 4 против часовой стрелки, при этом столик 1 прибора с образцом опустится;
л) испытание повторить на одном образце четыре раза.
За число твердости взять среднее из трех последних значений. Результаты испытаний занести в таблицу № 4.
4.Результаты измерений занести в сводную табл. 5. Пересчитать твердость на предел прочности.
5.Составить отчет по работе.
Для приближенного перевода единиц твердости из одной системы в другую можно воспользоваться таблицей № 2 или следующими формулами:
HB=10 HRC,
HB=2 HRВ,
HВ = HV (до 450 кг/мм2).
Содержание отчета
1. Название работы.
2. Цель работы.
3. Приборы и принадлежности.
4. Краткие сведения из теории.
5. Результаты измерения твердости по Бринеллю:
Таблица 1. - Результаты замера твердости по Бринеллю
№ обр. | Мате- риал | № отпеч. | Нагрузка, кг | D, Мм | d отпечатка, мм | НВ, кг/мм2 | |||||
1 | 2 | среднее | по | по образцу | |||||||
| |||||||||||
6. Результаты вычислений по формулам 1 и 2 для материала:
7. Результаты измерения твердости по Роквеллу:
Таблица 2. - Результаты замера твердости по Роквеллу
№ образ- ца | № отпе- чатка | Мате- риал | Шкала | Нагрузка, кг | Тип индентора | Число твердости | Среднее число HR на образец | Пере- вод на НВ |
8. Представить сводные данные с пересчетом на предел прочности:
Таблица 3. - Результаты замеров с пересчетом на предел прочности
Метод замера | Материал | Число твердости по образцу | Число твердости по Бринеллю HB | Пересчетная формула на прочность | Предел прочности, МПа |
По Бринеллю | |||||
По Роквеллу |
9. Сделать выводы по работе: область применения измерений твердости, связь с другими механическими свойствами материалов.
Контрольные вопросы.
1. Дать определение твердости.
2. Способы измерения твердости и их различия по характеру воздействия наконечника.
3. Измерение твердости вдавливанием: сущность метода и процессы, происходящие с испытуемым материалом.
4. Преимущества измерения твердости.
5. Измерение макротвердости и микротвердости: их основные отличия.
6. Измерение твердости по Бринеллю: вид индентора, схема испытания, подбор нагрузки, времени выдержки под нагрузкой, обозначение твердости.
7. Связь числа твердости НВ с пределом прочности различных металлов.
8. Преимущества и недостатки измерения твердости по Бринеллю.
9. Измерение твердости по Роквеллу: вид индентора, принципиальные отличия от измерения по Бринеллю.
10. Схема испытания, подбор индентора и нагрузки при измерении твердости по Роквеллу, обозначение твердости.
11. Преимущества и недостатки измерения твердости по Роквеллу.
12. Как можно измерить твердость очень тонких слоев металла (толщиной менее 0,3 мм)?
Лабораторная работа 2
Дата добавления: 2019-07-17; просмотров: 187; Мы поможем в написании вашей работы! |
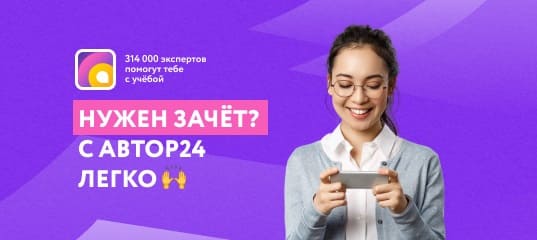
Мы поможем в написании ваших работ!