ГЛАВА 2. ВХОДНЫЕ ДАННЫЕ ДЛЯ СТАТИСТИЧЕСКОГО АНАЛИЗА СТАБИЛЬНОСТИ ТЕХНОЛОГИЧЕСКИХ ПРОЦЕССОВ НА ПРИМЕРЕ ООО «АЖИО»
Краткая характеристика предприятия
Компания «Ажио» была основана в 1998 году и является производителем товаров торговой марки «РУНИТ». С 2000 года является членом Союза Реставраторов Санкт-Петербурга. В 2007 году компания наладила производство известковых красок и декоративных терразитовых штукатурок. В период с 2009 по 2010 гг. проводились новые научные разработки с целью расширения ассортимента ремонтных и гидроизоляционных материалов, предназначенных для реставрации и подземного строительства. В 2010 году стартовало производство новых составов на основе фибробетона «РУНИТ», предназначенных для архитектурных деталей фасадов зданий и являющихся отличной заменой аналогичных элементов на основе гипсовых вяжущих. Фибробетон – композитный строительный материал, который, благодаря наличию в своем составе различных видов фибры, обладает повышенными техническими характеристиками: высокая прочность, ударостойкость, трещиностойкость. С 2014 года ведется разработка элементов навесного фасада из стеклофибробетона, главным компонентом которого, определяющим его уникальные свойства, является стекловолокно [12].
На данный момент компания занимается производством и реализацией широкой номенклатуры продукции:
· ССС и краски, которые включают: штукатурки и шпаклевки для внутренних и наружных работ, декоративные штукатурки, материалы для устройства кладки, гидроизоляционные смеси, силикатные и известковые краски, фибробетонные сухие смеси, клеевые составы и материалы для устройства напольных покрытий;
|
|
· бетонная мозаичная плитка терраццо, обладающая долговечностью, низкой истираемостью и искробезопасностью;
· изделия из стеклофибробетона, используемые в качестве фасадного декора и интерьерного архитектурного декора [13].
Также компания «Ажио», обладая собственными методиками реставрации, оказывает реставрационные услуги по восстановлению и реконструкции зданий. Не последнюю роль в деятельности компании занимает проведение работ по внутренней и внешней гидроизоляции помещений и зданий с применением составов собственного производства.
Кроме того, в состав ООО «Ажио» входит инновационно-испытательный центр «Строительство и реставрация», аккредитованный на проведение контрольных испытаний стройматериалов и сырья для их производства в соответствии с областью аккредитации. Испытательный центр занимается:
· Подбором составов строительных композиционных материалов на основе минеральных вяжущих;
· обследованием зданий и сооружений на предмет технического состояния материалов и изделий (включая рекомендации по восстановлению);
|
|
· разработкой нормативно-технической документации на производство сухих строительных смесей;
· испытанием строительных материалов и конструкций;
· разработкой технологии производства реставрационных работ фасадов и интерьеров зданий и сооружений [14].
Основными этапами при производстве ССС в компании «Ажио» являются:
· Приемка, сушка и транспортировка песка;
· приемка и загрузка добавок;
· приемка и загрузка вяжущих;
· складирование технологических запасов сырья;
· дозирование;
· смешивание;
· упаковочно-погрузочные работы;
· управление производством.
Технологическая схема производства ССС на заводе «Ажио» и спецификация оборудования представлены на рис. 17 и в табл. 6 соответственно.
Сырой песок из карьера доставляется на самосвалах и выгружается на фронтальный погрузчик, при помощи которого попадает в приемный бункер. Затем ленточный питатель, подавая песок из емкости на транспортер ленточного типа, доставляет его в переднюю часть сушильного барабана. После этого песок попадает в разгрузочную камеру и проходит через перфорационные сита, предназначенные для удаления отходов из песка. Очищенный песок подается в емкость насоса, а отходы сбрасываются в карман для отходов.
|
|
Затем при помощи сжатого воздуха песок из пневмокамерного насоса подается по магистрали пневмотранспорта в силос, предназначенный для сухого песка. Проходя через контрольное сито (виброгрохот), отделяющее фракции песка свыше 2,5 мм и влияющее на качество его рассева, песок попадает в смеситель.
Песочная пыль удаляется при помощи вытяжного вентилятора, установленного в ковшовом элеваторе, контрольном сите и емкости для наполнения.
Различные добавки, предназначенные для улучшения физико-механических свойств составов, хранятся на заводском складе. Нужное количество добавок в соответствии с планом производства подготавливается и подается на площадку для перемешивания, а затем на пост смесителя.
Таблица 6 – Спецификация оборудования | |||
№ | Наименование | № | Наименование |
1 | Ленточный питатель | 14 | Лопастной смеситель |
2 | Ленточный транспортер | 15 | Шнек |
3 | Грохот контрольный | 16 | Ковшовый элеватор |
4 | Ленточный транспортер | 17 | Пневмофасовщик |
5 | Загрузочная воронка | 18 | Бункер для раздачи в мешки |
6 | Сушильный барабан | 19 | Ленточный транспортер |
7 | Элеватор | 20 | Дозатор |
8 | Грохот | 21 | Каток для мешков |
9 | Сортирующее сито | 22 | Штамп-машина |
10 | Шнек | 23 | Термоусадочная камера |
11 | Стержневой смеситель | 24 | Рольган съема поддонов |
12 | Шнек | 25 | Вилочный автопогрузчик |
13 | Ковшовый элеватор |
|
|
Цемент, гипс и доломит поступают на завод в автоцистернах. Перегрузка в силосы для вяжущих происходит при помощи пневмонасоса, оборудованного компрессором для нагнетания воздуха.
Емкости для наполнителя, оборудованные уровнемерами, служат для временного хранения фракционного песка. Система аэрации предотвращает возможность образования в емкостях зон со слежавшимся песком.
Известь на завод поступает в полиэтиленовых «биг-бэгах» вместимостью 1 тонна и хранится на складе запасов сырья. Подача извести контролируется весами и происходит автоматически, путем подвешивания мешков на кран.
Емкости для добавок заполняются вручную каждую смену, так как они не предназначены для хранения.
В соответствии с введенной в заводской диспетчерский компьютер рецептурой процессор, управляя автоматическими пневмоклапанами, дозирует все компоненты для необходимого замеса на весы и подает их в смеситель. Также предусмотрена ручная система дозировки.
Система дозировки обеспечивает дозировку с точностью 0,5 %.
Дозированные материалы, перемешиваются в смесителе в соответствии с заданной программой. В программу работы для каждого состава задается время смешивания. Затем состав из смесителя подается в буферную емкость, откуда с помощью фасовочной машины поступает в мешки по 30 кг.
После наполнения мешка готовой продукцией он подается по конвейеру к посту складирования, где проставляется дата изготовления продукции. Мешки укладываются согласно схеме, исходя из количества мешков в партии и их размера на деревянные поддоны. После чего поддоны с мешками упаковываются в термоусадочную пленку и отвозятся вилочным погрузчиком на склад или к месту погрузки в автотранспорт.
На заводе установлены диспетчерский и производственный компьютеры, центральный процессор, локальные логистические системы. Диспетчерский компьютер осуществляет контроль за точностью соблюдения составов, очередностью выполнения заказов, подает команды производственному компьютеру.
Центральный производственный компьютер управляет процессом сушки, транспортировки и сортировки песка, дозировки наполнителя, вяжущих и добавок, смешивания, подачи готовой продукции к упаковочно-погрузочным линиям, обеспечивает контроль за техническими и технологическими параметрами производства.
Дата добавления: 2019-07-15; просмотров: 134; Мы поможем в написании вашей работы! |
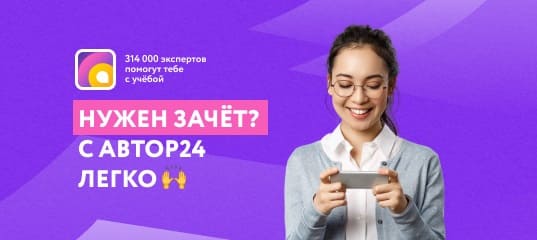
Мы поможем в написании ваших работ!