Выполнение индивидуального задания
· ЛАБОРАТОРНАЯ РАБОТА №5
ОБРАБОТКА МЕТАЛЛОВ РЕЗАНИЕМ
Цель работы
1. Ознакомиться с параметрами режима резания, геометрией режущего инструмента, устройством и назначением некоторых металлорежущих станков.
2. Изучить технологические процессы обработки деталей машин точением, фрезерованием, строганием.
3. Освоить основные приемы работы на токарных, фрезерных и строгальных станках.
Материалы и оборудование
1. Токарные, фрезерные, строгальные станки.
2. Металлорежущий и мерительный инструмент.
3. Заготовки для изготовления деталей.
Основные положения
Обработка металлов резанием – это процесс срезания режущим инструментом слоя металла с поверхности заготовки в виде стружки для получения необходимой геометрической формы, точности размеров, взаиморасположения и шероховатости поверхностей детали.
Режим резания
Движениями резания называют движения, которые сообщаются инструменту и заготовке для срезания слоя металла
Главное движение резания Dr – скорость деформирования и отделения стружки
Движение подачи D s – обеспечивает непрерывность процесса резания
Скорость главного движения резания v (м/мин.) – это скорость перемещения точки режущей кромки инструмента относительно обрабатываемой поверхности в направлении главного движения.
При обработке цилиндрической поверхности скорость определяется как
|
|
v = v= p·Dзаг.·n·10-3, м/мин.
Скорость движения подачи v s – это скорость рассматриваемой точки режущей кромки в направлении движения подачи.
Подача s (мм/об; мм/дв. ход) – это перемещение инструмента в направлении движения подачи за один оборот, либо двойной ход заготовки или инструмента.
Глубина резания t (мм) – это расстояние между обрабатываемой и обработанной поверхностями, измеренное перпендикулярно к последней, пройденное за один проход инструмента.
При обработке цилиндрической поверхности глубина резания
t = 0,5·(Dзаг. − d), мм.
Параметрами режима резания являются скорость главного движения резания v, подача s и глубина резания t характеризуют напряженность процесса обработки
Геометрия инструмента
Токарный проходной резец состоит из стержня, при помощи которого он закрепляется на станке, и рабочей части.
Элементы рабочей части резца показаны на рис. 1:
1. передняя поверхность 1, по которой сходит стружка;
2. поверхности, называемые задними, которые обращены: главная задняя 2 – к поверхности резания,
3. вспомогательная задняя 4 – к обработанной поверхности;
4. главная 3
5. вспомогательная 6 режущая кромка; 6. вершина резца 5.
Рис. 1
Расположение поверхностей режущей части инструмента регламентируется углами, для определения которых введены координатные плоскости (см. рис. 2).
|
|
Основная плоскость - плоскость, параллельная направлениям продольной и поперечной подач и проходящая через вершину резца
Плоскость резания проходит через главную режущую кромку перпендикулярно к основной плоскости.
Главная секущая плоскость проходит перпендикулярно к проекции главной режущей кромки на основную плоскость.
Главные углы резца:
Передний угол gпроходит перпендикулярно к проекции главной режущей кромки на основную плоскость.
Главный задний угол aглавной задней поверхностью и поверхностью резания.
Угол заострения bзаключен между передней и задней поверх ностями.
Вспомогательный задний угол a 1 измеряют во вспомогательной секущей плоскости (рис. 2, в), перпендикулярной проекции вспомогательной режущей кромки на основную плоскость .
Главный угол в плане j образуется проекцией главной режущей кромки на основную плоскость и направлением движения подачи .
Вспомогательный угол в плане j1 проекцией вспомогательной режущей кромки на эту плоскость и направлением, противоположным движению подачи (рис. 2, а).
|
|
Угол в плане при вершине резца e измеряют между проекциями режущих кромок на основную плоскость.
Дата добавления: 2019-07-15; просмотров: 173; Мы поможем в написании вашей работы! |
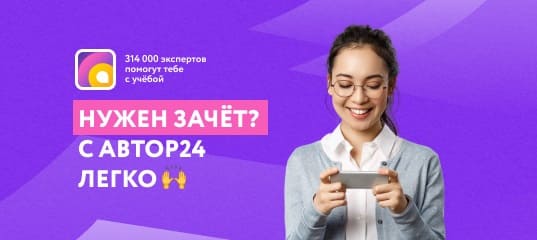
Мы поможем в написании ваших работ!