Рекомендации по выбору метода и способа получения заготовок.
СЕМИНАРЫ
Семинар 1. Заготовительное производство
Производство заготовок для изделий машиностроения
Основные факторы, влияющие на выбор метода и способа получения заготовок
Факторы, влияющие на себестоимость производства в машиностроении, делятся на три группы:
1-я группа – конструктивные факторы, т.е. конструктивное решение самой детали, обеспечивающее приемлемость её для изготовления обработкой давлением, литьем, сваркой; выбор марки материала и технологических условий;
2-я группа – производственные факторы, т.е. характер и культура производства, технологическая оснащенность, организационные и технологические уровни производства;
3-я группа – технологические факторы, характеризующие способ формообразования заготовок, выбор самой заготовки, оборудования и технологического процесса получения детали.
То, насколько полно в заготовке учтено влияние факторов первой и второй групп, позволяет судить о технологичности заготовки.
Под технологичностью заготовки принято понимать, насколько данная заготовка соответствует требованиям производства и обеспечивает долговечность и надежность работы детали при эксплуатации.
Выпуск технологичной заготовки в заданных масштабах производства обеспечивает минимальные производственные затраты, себестоимость, трудоемкость и материалоемкость.
Третья группа факторов важна, когда детали могут быть получены одним или несколькими способами литья или обработки давлением, например, фланцы, тройники, шестерни. Однако при литье структура металла, а следовательно, и механические свойства, ниже, чем при обработке металлов давлением. Также, особенно при литье в кокиль или под давлением, выше вероятность возникновения литейных напряжений и наличия пористости.
|
|
Таким образом, при выборе методов и способов получения заготовки в первую очередь следует учитывать основные факторы - себестоимость и требования к качеству.
В себестоимости изготовления детали значительную долю составляют затраты на материал (около 60 %). Поэтому пути снижения себестоимости целесообразно искать в снижении расхода материала.
Технологичность детали с определенной степенью приближения оценивается следующими показателями:
– коэффициент выхода годного (Квг) ;
– коэффициент весовой точности (Квт) ;
– коэффициент использования металла (Ким).
Квг – характеризует расход металла в заготовительном цехе, размер брака, технологических отходов, определяется по формуле:
Квг = М2/М1
где: М1– масса исходного металла; М2– масса заготавливаемого металла.
Квт – отражает степень приближения формы и размеров заготовки к форме и размерам детали, т.е. характеризует объем механической обработки, определяется по формуле:
|
|
Квт = Мд/М2
где: Мд – масса готовой детали.
Ким – отражает общий расход металла на изготавливаемую деталь, определяется по формуле:
Ким = Квг × Квт
Средние значения КИМ у поковок и штамповок находятся в пределах – 0,5–0,55, а у отливок и сварных заготовок значительно выше – 0,75–0,8.
Экономичность изготовления деталей из различных заготовок можно также оценить и трудоемкостью изготовления (чел.-час/т). Трудоемкость изготовления отливок в большинстве случаев наименьшая 120; у сварных заготовок – 130; у штамповок – 194; у поковок – 245.
Общие принципы выбора метода и способа получения заготовок
Наиболее широко для получения заготовок в машиностроении применяют следующие методы: литье, обработка металла давлением, сварка, а также комбинация этих методов.
Каждый из методов содержит большое число способов получения заготовок.
Метод – это группа технологических процессов, в основе которых лежит единый принцип формообразования.
Литье – получение заготовок в результате заливки расплавленного металла заданного химического состава в литейную форму, полость которой имеет конфигурацию получаемого изделия.
|
|
Методом литья получают заготовки практически любых размеров, как простой, так и очень сложной конфигурации. При этом отливки могут иметь сложные внутренние полости с криволинейными поверхностями, пересекающимися под различными углами. Точность размеров и качество поверхности заготовки зависят от способа литья. Отливки можно изготавливать практически из всех металлов и сплавов.
Обработка давлением – технологические процессы, которые основаны на пластическом формоизменении металла.
Машиностроительные профили изготавливают прокаткой, прессованием и волочением. При этом получают заготовки в виде сортовых профилей, листового проката, труб и периодических профилей. Прокат выпускают горячекатанным и калиброванным. Изделия из калиброванных профилей отличаются высокой точностью размеров и низкой шероховатостью поверхности. Для этих изделий выполняется только отделочная механическая обработка поверхностей заготовок.
Периодические профили имеют изменяющиеся форму и площадь поперечного сечения вдоль оси заготовки. Их применяют как фасонные заготовки для последующей объемной штамповки и механической обработки резанием.
Легкие, но жесткие тонкостенные профили (менее 23 мм) весьма сложной конфигурации и большой длины можно получать профилированием листового материала в холодном состоянии на профилегибочных станах. Гнутые профили применяют при изготовлении изделий для машиностроения, автомобильной и авиационной промышленности, строительных конструкций.
|
|
Для получения заготовок из стали и цветных металлов с деформированной макроструктурой, имеющих форму и размеры близкие к форме деталей машин, целесообразно применять ковку, объемную и листовую штамповку..
Ковку применяют для изготовления заготовок в единичном производстве в результате пластической деформации профилей или слитков. При производстве крупных и уникальных заготовок массой до 250 т ковка единственно возможный способ обработки давлением.
Заготовки, полученные объемной штамповкой, отличаются более высокой точностью размеров и качеством поверхностного слоя по сравнению с коваными поковками. Применение этого способа обработки давлением для получения заготовок деталей машин экономически целесообразно в условиях серийного и массового производств. По точности и шероховатости поверхностей заготовки, получаемые холодной объемной штамповкой, не уступают изделиям, изготавливаемым специальными способами литья. При этом механические свойства поковок выше, чем отливок.
Листовой штамповкой изготавливают самые разнообразные плоские и пространственные изделия массой от долей граммов до десятков килограммов. В качестве заготовок при листовой штамповке используют полученные прокаткой листы, полосы или ленты, толщина которых обычно не превышает 10 мм. При заданной прочности и жесткости этим способом обработки давлением получают изделия минимальной массы с высокой точностью размеров и качеством поверхности. Это позволяет сократить количество отделочных технологические операций механической обработки резанием.
Сварка вряде случаев упрощает изготовление заготовок сложной конфигурации. Проблемным местом сварной заготовки является шов или зона термического влияния. Как правило, их прочность ниже, чем основного металла. Кроме того, неправильная конструкция заготовки или технология сварки могут привести к дефектам (коробление, пористость, трещины), которые трудно исправить последующей обработкой. Заготовки сложной конфигурации дают значительный экономический эффект при изготовлении элементов изделий штамповкой, литьем, прокаткой, с последующим соединением их сваркой. Такие заготовки применяют при изготовлении крупных коленчатых валов, станин кузнечно-прессового оборудования и т.п..
Выбор метода и способа получения заготовки сложная задача.
Метод и способ получения заготовки должен быть экономичным, обеспечивающим высокое качество детали, производительным, нетрудоемким.
Рекомендации по выбору метода и способа получения заготовок.
1. Тип производства .
Для единичного производства характерно использование в качестве заготовок горячекатаного проката, отливок, полученных в песчаных формах, поковок, полученных ковкой.
Это обуславливает большие припуски, значительный объем последующей механической обработки, повышение трудоемкости.
В условиях серийного и массового производств рентабельны следующие способы получения заготовок: горячая объемная штамповка; литье в кокиль, под давлением, в оболочковые формы, по выплавляемым моделям.
Применение этих способов позволяет значительно сократить припуски на механическую обработку, снизить трудоемкость изготовления детали.
Дата добавления: 2019-03-09; просмотров: 257; Мы поможем в написании вашей работы! |
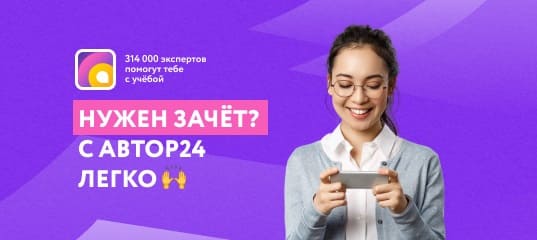
Мы поможем в написании ваших работ!