Жидкости для гидравлических систем.
Предыдущая43444546474849505152535455565758Следующая
Жидкости для гидравлических систем должны удовлетворять следующим требованиям:
· иметь хорошие вязкостно-температурные свойства, обеспечивающие высокую подвижность при низких температурах окружающего воздуха и отсутствие подтеканий в жаркий период;
· не разрушать металлических и резиновых деталей;
· обладать высокой химической и физической стабильностью, не расслаиваться, не выделять каких либо осадков, не вспениваться;
· обладать хорошими противоизносными свойствами и обеспечивать уменьшение интенсивности износа трущихся пар и уплотнителей;
· быть пожаро - и взрывобезопасными, нетоксичными и недефицитными.
Тормозные жидкости.
БСК(касторовая жидкость) состоит из 50 % бутилового спирта и 50 % касторового масла. Жидкость БСК обладает весьма хорошими смазывающими свойствами, но недостаточно высокими вязкостно-температурными свойствами, физической и химической стабильностью. Работоспособна до температуры -20º С. Для сохранения работоспособности при более низких температурах жидкость разбавляют этиловым или бутиловым спиртом. При повышенных температурах происходит испарение спирта, из-за чего увеличивается вязкость и повышается температура замерзания жидкости. Не пригодна для использования на автомобилях с дисковыми тормозами. Огнеопасна.
Кроме БСК, могут применяться спиртокасторовые жидкости, состоящие из смеси касторового масла с изоамиловым (АСК) или этиловым (ЭСК) спиртами.
|
|
Спиртокасторовые жидкости плохо смешиваются с водой, при ее попадании они расслаиваются, становятся физически нестабильными и непригодными к применению.
Гликолевая тормозная жидкость ГТЖ-22М – смесь гликолей, воды и противокоррозионной присадки. Она работоспособна в интервале температур от +50 до -50º С, закипает при температуре +140º С, поэтому непригодна для автомобилей с дисковыми тормозами, хорошо растворима в воде, смешивается с тормозной жидкостью «Нева». Жидкость ядовита.
Жидкость «Нева» состоит из 41 – 59 % этилкарбитоля, 31 -34 % диолов, 5 % эфиров карбитола и 13 – 14 % смесей гликолей с добавками загустителей и противокоррозионных присадок. Работоспособна в широком диапазоне температур от –50 до +50º С, закипает при +190º С. Огнеопасна и ядовита.
Так же выпускается тормозная жидкость «Томь», превосходящая «Неву» по низкотемпературным свойствам. Выпускаемая в России тормозная жидкость «Роса» соответствует мировым стандартам (dot-3; dot-4).
Амортизационные жидкости.
В качестве жидкости для заполнения гидравлических систем используют маловязкие нефтяные масла или их смеси с добавлением вязкостных и других присадок. Амортизационная жидкость должна обладать определенной вязкостью. Высокая вязкость жидкости вызывает жесткость амортизатора, а слишком низкая приводит к бездействию амортизатора вследствие чрезмерно мягкой работы и служит причиной утечки жидкости через уплотнители.
|
|
Для телескопических и рычажно-кулачковых амортизаторов выпускается всесезонная амортизационная жидкость АЖ-12Т, которая состоит из трансформаторного масла и кремнийорганической жидкости с добавлением противоизносной присадки и антиокислителей. Жидкость работоспособна при давлении до 12 МПа и температуре от -50 до +140º С.
Для заполнения гидрообъемных передач и системы гидроусиления руля применяют масло марки Р, которое содержит противоизносную, антиокислительную, моющую и антипенную присадки и поэтому способно работать при тяжелых эксплуатационных режимах.
Для автомобилей эксплуатируемых в районах с температурой ниже -40ºС, в качестве амортизационной жидкости применяют приборное масло МВП, имеющее температуру застывания не ниже -60º С. Масло МВП используется для заполнения гидравлических домкратов. Для заполнения подъемных механизмов автомобилей-самосвалов в летних условиях используется индустриальное масло 20 (веретенное 3) с температурой застывания не выше -20º С , в зимних условиях индустриальное масло 12 (веретенное 2) с температурой застывания не выше -30º С.
|
|
Электролит.
Электролит для кислотных аккумуляторных батарей представляет собой раствор аккумуляторной серной кислоты в дистиллированной воде. Аккумуляторная серная кислота имеет плотность 1,83 г/см3, а плотность электролита зависит от климатической зоны и колеблется от 1,24 до 1, 31 г/см3. Электролит плотностью 1,31 г/см3не замерзает даже при температуре -60º С, а при плотности 1, 15 г/см3 замерзает уже при температуре -14º С.
При приготовлении электролита аккумуляторную кислоту тонкой струей льют в воду. Если делать наоборот возможен выброс кислоты, которая может повредить кожу и одежду работающего. При разведении кислота разогревается. Для определения плотности электролита используют денсиметр (ареометр). При понижении уровня электролита в аккумуляторную батарею добавляют дистиллированную воду или электролит плотностью 1400 кг/м3 (50 %воды и 50 % серной кислоты по массе).
Пусковые жидкости.
Для пуска карбюраторных и дизельных двигателей при низких температурах используются пусковые жидкости «Холод Д-40» и «Арктика», состоящие в основном из этилового спирта и различных присадок. Для применения пусковых жидкостей на автомобиль монтируются специальные пусковые приспособления двух моделей 5ПП-40 и 6ПП-40. Жидкости выпускаются в запаянных ампулах.
|
|
Специальные способы литья
Предыдущая44454647484950515253545556575859Следующая
Литье в металлические формы
При литье в металлические формы (кокили) резко увеличивается производительность труда, снижается брак, возрастает механическая прочность отливок, улучшается их поверхность, уменьшаются припуски на механическую обработку. Литьё металлов в кокиль — наиболее качественный способ. Изготавливается кокиль — разборная форма (чаще всего металлическая), в которую производится литьё. После застывания и охлаждения, кокиль раскрывается и из него извлекается изделие. Затем кокиль можно повторно использовать для отливки такой же детали.
Кокили изготовляют из чугуна или стали и собирают обычно из нескольких частей. Для увеличения стойкости на внутреннюю поверхность металлической формы, предварительно подогретой до 200—250°С, наносят огнеупорную обмазку.
Рис. 83.Схема литья в кокиль:
1-стержень; 2-кокиль; 3-деталь.
Центробежное литье
Методом центробежного литья лучше всего получать отливки, имеющие форму тел вращения. При этом литье жидкий металл поступает во внутреннюю полость быстро вращающейся металлической формы, а затем под действием центробежных сил отбрасывается к ее стенкам и затвердевает в виде пустотелой отливки.
Для вращения форм применяют центробежные машины с вертикальной или горизонтальной осью вращения. Детали небольшой длины, например бронзовые втулки, червячные шестерни, обычно отливают на машинах с вертикальной осью вращения. Детали большой длины, например чугунные водопроводные и канализационные трубы, стальные стволы орудий и другие, отливают на центробежных машинах с горизонтальной осью вращения.
Рис. 84. Схема получения отливок способом центробежного литья на машинах с вертикальной (а) и горизонтальной (б) осями вращения: 1-ковш; 2-желоб; 3-форма; 4-отливка; 5-шпиндель.
Полученные отливки имеют более высокую плотность, отличаются мелкозернистой структурой и высокой прочностью. Отсутствие литников и выпоров, малые припуски на механическую обработку, небольшой брак и высокая производительность — преимущества центробежного способа литья.
Применяют центробежные машины нескольких типов, конструкция которых определяется размерами отливок и их назначением.
Литье под давлением
Предыдущая45464748495051525354555657585960Следующая
Литье под давлением позволяет получить очень точные и вместе с тем сложные по конфигурации отливки. Сущность процесса заключается в том, что расплавленный металл выдавливается в стальные формы под некоторым давлением.
В настоящее время под давлением отливают детали из цинковых, алюминиевых, магниевых и медных сплавов.
Пресс-форма (рис.85, а) состоит из неподвижной матрицы 1 и подвижной матрицы 3. для образования полостей и отверстий в отливке используются только металлические стержни, которые находятся обычно в подвижной полуформе, как, например, стержень 2. Пресс-форма имеет каналы 6 для водяного охлаждения. Для извлечения отливки из формы предусматриваются толкатели 5, закрепленные на плите толкателей 4.
Пресс-форму монтируют на машине, механизмы которой закрывают и запирают пресс-формы под высоким давлением во избежание прорыва металла по плоскости разъема, запрессовывают жидкий металл, раскрывают пресс-формы и выталкивают отливки
Рис. 85. Схема литья под давлением на машинах:
а — с холодной горизонтальной камерой; б — с холодной вертикальной камерой; в — с горячей вертикальной камерой
.
Машины для литья под давлением делятся на поршневые и компрессорные. Наибольшее распространение получили поршневые машины с холодной и горячей камерой прессования.
Поршневые машины с холодной камерой прессования подразделяются на машины с горизонтальной (рис. 85, а) и вертикальной (рис. 85, б) камерой.
Перед заливкой пресс-форму подогревают и наносят смазку на ее рабочие поверхности, камеры прессования 7 и пресс-поршня 8 (рис. 85, а). В камеру прессования (позиция 1) заливают мерную порцию сплава 9. Пресс-поршень 8 перекрывает заливочное отверстие, создает давление в камере прессования и сплав с большой скоростью заполняет полость формы 10. После затвердевания сплава пресс-форма раскрывается — отходит подвижная часть формы вместе с отливкой, плунжер возвращается в исходное положение. Плита толкателей перемещается вместе с пресс-формой до упора 12 (позиция 11). При дальнейшем движении пресс-формы толкатели «снимают» отливку 11 со стержня 2 и она поступает в контейнер. Пресс-форму обдувают сжатым воздухом, смазывают, закрывают и процесс повторяется.
На машине с вертикальной камерой прессования 1 (рис. 85, б) плунжер 2 давит на залитый металл 3 и перемещает вниз пяту 4. При этом открывается отверстие 5 литника, металл заполняет форму, пята 4 поднимается, отрезает и выталкивает пресс-остаток металла.
Поршневые машины с холодной камерой прессования применяют для получения отливок из медных, алюминиевых, магниевых и других цветных сплавов, а также стальных отливок.
В отечественном литейном производстве все большее распространение получают машины с горизонтальной камерой прессования. Они более производительны и проще в обслуживании.
Машины с горячей камерой прессования (рис. 85, в) имеют печь с тиглем 1, в котором образована камера прессования 2. При верхнем положении плунжера 3 металл заполняет камеру через отверстия 4. При движении плунжера вниз он перекрывает эти отверстия, и сплав под давлением заполняет полость пресс-формы 5.
Такие машины имеют высокую производительность, так как не нужно производить операцию заливки сплава — металл сам. заливается в камеру при обратном ходе плунжера. Поэтому большинство машин работает в автоматическом режиме. Производительность может достигать до 3000 и более отливок в час. Машины с горячей камерой прессования используют в основном для литья легкоплавких сплавов (цинковых, свинцово-сурьмянистых и др.).
Применение металлической формы и давления на заливаемый металл позволяет получить сложные отливки высокой точности, с чистой поверхностью и минимальными припусками на механическую обработку. Благодаря давлению возможно получение отливок со стенками толщиной 1—1,5 мм. Прочность отливок выше, чем при литье в песчаные формы. Но пластические свойства отливок снижаются из-за образующейся пористости (при мгновенном заполнении формы воздух и газы не успевают выходить).
Литье под давлением является наиболее прогрессивным и производительным способам для получения отливок из цветных сплавов в массовом производстве.
Дата добавления: 2019-02-26; просмотров: 226; Мы поможем в написании вашей работы! |
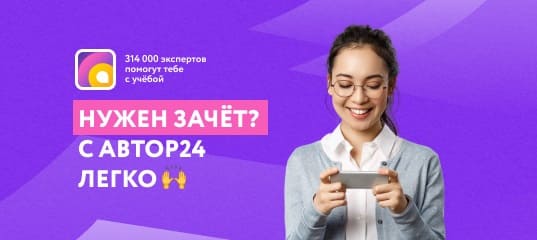
Мы поможем в написании ваших работ!