Измерение твердости вдавливанием стального шарика (метод Бринелля) (ГОСТ 9012-59).
Рис.17. Прибор для испытания металлов на твердость вдавливанием стального шарика.
Измерение твердости по Бринеллю заключается в том, что в поверхность испытуемого металла вдавливается стальной закаленный шарик диаметром 2,5, 5 и 10 мм под действием статической нагрузки Р (Рис.18).
Рис. 18. Схема испытания твердости шариком
Нагрузку на шарик устанавливают пропорционально квадрату диаметру шарика. Для испытания стали и чугуна нагрузка на шарик P = 30D2. Для меди и медных сплавов принята нагрузка
P = 10D2 , а для баббитов и свинцовых бронз P = 2,5D2.
Отношение усилия Р к площади F поверхности полученного отпечатка лунки дает значение твердости, обозначаемое НВ.
НВ = кг/мм2 .
Число твердости, выраженное через диаметр шарика D и диаметр отпечатка – лунки d, характеризуется следующей формулой:
HB = кг/мм2
Диаметр отпечатка измеряется с помощью специальной лупы (Рис.19.).
Рис.19.Измерение диаметра отпечатка
Число твердости по Бринеллю дает представление о другой важной величине, характеризующей металл, - о приделе прочности при растяжении. Для низкоуглеродистой и незакаленной легированной стали предел прочности при испытании на растяжение численно равен 0,36 величины твердости, полученной испытанием по Бринеллю.
Способом Бринелля нельзя пользоваться для определения твердости металлов более 450 НВ, так как под значительной нагрузкой стальной шарик изменяет свою форму, дает неправильный отпечаток и может разрушиться.
|
|
Измерение твердости вдавливанием алмазного конуса (метод Роквелла) (ГОСТ 9013-59).
Измерение твердости по Роквеллу производиться путем вдавливания в испытуемый металл стального шарика диаметром 1,58 мм или алмазного конического наконечника с углом при вершине 120º (Рис.20). В отличие от способа Бринелля, твердость по Роквеллу определяется не по площади отпечатка, а по глубине вдавливания стального шарика или алмазного конического наконечника в изделие. При определении твердости по методу Роквелла вдавливание индентора производится действием двух последовательно прилагаемых нагрузок: предварительной, равной 10 кг, и окончательной, равной 60, 100 и 150 кг.
Рис. 20Схема контроля твердости по способу Роквелла:
Алмазным конусом и стальным шариком.
Если под действием предварительной нагрузки индентор внедрился на глубину h, то под действием окончательной нагрузки он внедрится на глубину h2. разность глубин h1, на которые проникает индентор под действием последовательно приложенных нагрузок, характеризует твердость испытуемого материала. Число твердости, измеренное по методу Роквелла, обозначается HR и выражается в условных единицах.
|
|
На приборе Роквелла измерение глубины вдавливания индентора производится автоматически, и число твердости после измерения отсчитывается на циферблате индикатора. Индикатор стандартного прибора имеет две шкалы: черную шкалу С для испытания алмазным конусом (закаленных сталей) с нагрузкой 150 кг и красную шкалу В для испытания стальным шариком с нагрузкой 100 кг. Каждое деление шкалы соответствует единице твердости и равно глубине вдавливания на 0,002 мм.
Стальной шарик применяется для определения твердости незакаленной стали, бронзы, латуни и других материалов. Испытание очень твердых материалов производиться алмазным коническим наконечником с нагрузкой 60 кг, с отсчетом по черной шкале, обозначаемой буквой А.
При выражении твердости по Роквеллу к знаку твердости HR добавляют индекс, обозначающий шкалу, по которой производилось испытание, например HRC, HRB, HRA.
Дата добавления: 2019-02-26; просмотров: 430; Мы поможем в написании вашей работы! |
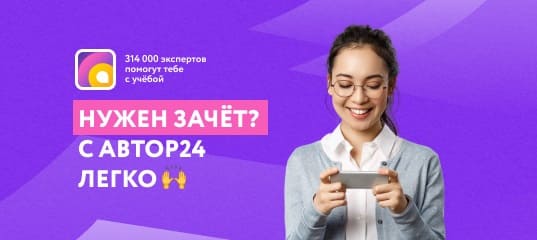
Мы поможем в написании ваших работ!