Меры борьбы с коррозией металлов.
металлические покрытия –это нанесение на металле тонкого слоя другого металла, обладающего большой антикоррозионной стойкостью. Металлические покрытия наносят следующими способами: горячим, гальваническим, диффузионным, металлизацией и д.р.
При горячем способе изделие погружают в ванну с расплавленным металлом: цинком (цинкование), оловом (лужение), свинцом (свинцование).
Гальванический способ заключается в том, что на поверхность изделия наносят тонкий слой (от 0,005 до 0,03мм) металла при электролизе раствора солей цинка, олова, никеля, хрома и д.р.
Диффузионный способ состоит в поглощении поверхностью металла защитного металла, проникающего в него при высоких температурах.
Металлизация(распыление) – нанесение тонкого слоя расплавленного металла на изделие специальным пистолетом – электрометаллизатором.
Плакирование –покрытие листов металлав процессе прокатки тонким слоем другого металла, более устойчивого в отношении коррозии.
Химические покрытия(оксидирование или фосфотирование) заключаются в том, что на поверхности металла искусственно создают оксидные плотные пленки, хорошо сопротивляющиеся коррозии, с последующим покрытием маслами или красками.
Окраска(покрытие красками, лаками и эмалями) – самый простой и распространенный способ предохранения изделий от коррозии.
Смазкапредохраняет металлические изделия от коррозии. Смазку маслом широко применяют для защиты от коррозии вращающихся и движущихся частей станков и машин.
|
|
Электрохимическая защита(Рис.14.)(катодная защита). Коррозионная защита одного металла при помощи «жертвенного» анода-протектора из другого металла (основана на положении металла в электрохимическом ряду напряжения металлов).
Рис.14.Методы катодной защиты от коррозии: с «жертвенным» анодом – протектором (а); с вспомогательным анодом и внешним источником тока (б).
Механические свойства металлов.
Механические свойства характеризуют поведение металлов при воздействии на них внешних сил в процессе изготовления из него заготовок или изделий либо при эксплуатации деталей в рабочих условиях, т. е. прочность, твердость (предел прочности), упругость (предел упругости), пластичность, ударная вязкость и т.д.
Прочностью называется способность металлов сопротивляться деформациям (действию внешних сил), не разрушаясь.
Пределом прочностиназывается максимальная величина нагрузки, отнесенная к исходной площади сечения образца, при которой начинается разрушение металла.
Твердостью называютсвойство металла (сплава) сопротивляться внедрению (вдавливанию) в его поверхность более твердого постороннего тела.
|
|
Упругость –свойство металла сопротивляться прилагаемой внешней нагрузке без заметного относительного смещения атомов.
Пластичность –способность металла к остаточной (остающейся после удаления нагрузки) деформации без разрушения.
Ударной вязкостью называют способность металла (сплава) противостоять разрушению под действием ударной нагрузки.
Ползучесть - свойство металла медленно деформироваться (удлиняться) при высокой температуре под действием постоянной растягивающей нагрузки, которая создает напряжение, ниже предела упругости для данного металла.
Пределом ползучести– называется напряжение, которое вызывает заданное удлинение образца на протяжении определенного времени, например, 1% за 10000 ч при данной температуре.
Усталость металла –явление разрушения металла при его многократном нагружении.
Пределом выносливостиметалла называется такое наибольшее напряжение, которое металл может выдержать без признаков разрушения после заданного количества нагружений знакопеременным изгибом или другим видом деформации при закреплении испытуемого образца одним концом.
Механические свойства материалов определяют на специальных образцах. В зависимости от условий приложения нагрузки различают статические и динамические испытания. При статических испытаниях нагрузка прилагается медленно и плавно возрастает. При динамических испытаниях нагрузка прилагается с высокой скоростью.
|
|
Дата добавления: 2019-02-26; просмотров: 267; Мы поможем в написании вашей работы! |
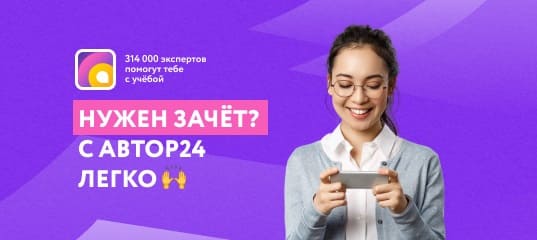
Мы поможем в написании ваших работ!