Измерение твердости вдавливанием алмазной пирамиды (метод Виккерса) (ГОСТ 2999-75).
При измерении твердости по Виккерсу в испытуемый металл вдавливается четырехгранная алмазная пирамида, противоположные грани которой образуют угол 136º (Рис.21.). Выбор такого угла при вершине объясняется тем, что он обеспечивает наилучшее совпадение чисел твердости HV со значениями чисел твердости по Бринеллю HB. Испытания проводят на специальном прессе под нагрузкой от 5 до 100 кг. Твердость определяется при измерении диагонали квадратного отпечатка, оставшегося на поверхности образца или детали, с помощью микроскопа, имеющегося на приборе. Время приложения нагрузки Р для черных металлов 10 сек, для цветных – 30 сек.число твердости по Виккерсу можно определить по формуле
HV = = 1,854
кг/мм2
Где Р – нагрузка на пирамиду, создаваемая прибором, кг;
d – среднее арифметическое длин обеих диагоналей отпечатка после снятия нагрузки, мм.
Преимущество метода Виккерса по сравнению с методом Бринелля заключается в том, что методом Виккерса можно испытывать материалы более высокой твердости из-за применения алмазной пирамиды.
Рис.21.Прибор для испытания на твердость вдавливанием вершины алмазной пирамиды
Для измерения твердости тонких слоев материалов и даже их отдельных структурных составляющих применяют метод микротвердости (ГОСТ 9450-76). Этот метод по существу не отличается от метода Виккерса, однако при этом используются малые нагрузки вдавливания.
|
|
Определение твердости по методу Шора.
При измерении твердости по методу Шора груз вместе с закрепленным на нем индентором (обычно стальной шарик) падает с высоты Нп на образец перпендикулярно его поверхности. Твердость по Шору определяется по высоте отскока шарика Но. шкала твердости разделена на 130 единиц. Она рассчитана таким образом, что твердость закаленной эвтектоидной стали, оказывается равной 100 единицам.
Проба на загиб в холодном и горячем состоянии.
Проба на загиб служит для определения способности металла принимать заданный по размерам и форме загиб. Образцы имеют размер: длину L = 5а + 150 мм и ширину b = 2а, но не менее 10 мм. Образец устанавливается на два опорных ролика и сверху посередине к нему прилагают усилие с помощью пресса или оправки (Рис.25.) .
Рис.25. Проба на загиб.
В зависимости от технических условий могут быть применены три типа загиба:
Рис.26.Загиб до определенного угла;
Рис.27. Загиб до параллельности сторон;
Рис.28. Загиб до соприкосновения сторон образца.
Проба может производиться в холодном или нагретом состоянии. Образец считается выдержавшим пробу, если в нем после загиба отсутствуют трещины, надрывы, расслоения и излом.
|
|
Проба на осадку в холодном состоянии.
При изготовлении из пруткового материала болтов, винтов, заклепок и др. необходима значительная пластичность металла, так как головки болтозаклепочных изделий получаемых из прутка диаметром меньше 30 мм, обычно осаживаются в холодном состоянии.
Форма образца для испытания (Рис.29.) – цилиндр диаметром d и высотой h = 2d . Образцы диаметром до 15 мм осаживаются молотком или кувалдой, а диаметром свыше 15 мм осаживаются под прессом до высоты h1. Признаком того, что образец выдержал пробу, служит отсутствие в нем после осадки трещин, надрывов или излома.
Рис.29. а – образец для испытанБ – вид образца после осадки.
Проба труб на бортование. (Рис.30.а.)
Этот вид испытаний применяется для труб. Качество трубы определяется ее способностью выдерживать без повреждения отгибание борта на 90º. Конец трубы или отрезок длиной не менее 0,5 D отбортовывается с помощью стальной закаленной оправки до получения заданного диаметра борта D.
Проба труб на загиб. (Рис.30.б.)
Применяется для труб с наружным диаметром более 114 мм. Качество металла определяется по способности образца трубы загибаться без повреждения на угол 90º вокруг оправки заданного радиуса любым способом: на станке или вручную, с наполнителем или без наполнителя, с внутренней оправкой или без оправки. Уменьшение наружного диаметра трубы при испытании не должно превышать 15% начальной величины диаметра.
|
|
Рис.30. а – проба труб на бортование;
Б – проба труб на загиб
Проба на искру.
Применяется в тех случаях, когда нужно быстро установить марку стали. Основана эта проба на том, что снимаемая при обработке стали на абразивных кругах стружка, сгорая в воздухе, образует сноп искр. Характер искр, их форма и цвет – от ослепительно белого до темно-красного – различны и зависят от химического состава стали (Рис.31.).
Марки углеродистой стали (в) дают белый пучок искр с отдельными звездочками, причем, чем больше в стали углерода, тем больше звездочек и тем короче пучок искр.
Марганцовистая сталь с содержанием 10 -14 % Мn дает тонкие и длинные светло-желтые линии с крупными звездочками (г), быстрорежущие стали – небольшой пучок искр темно-красного цвета, почти без звездочек (а). Кремнистые стали дают линии с крупными редкими звездочками (б), хромистые стали – искры соломенно-желтого оттенка, прерывистыми линиями, с мелкими частыми звездочками (д).
|
|
Рис.31.Проба стали на искру
Сплавы.
Подавляющее большинство металлических материалов – это не чистые металлы, а сплавы. Для специальных целей приготавливают особо чистые металлы, но даже металлы сомой высокой частоты, представляют собой сплавы. Даже при частоте 99,9999 % (по массе) каждый грамм металла все еще содержит сотни триллионов инородных атомов примесей.
Чистые металлы относительно редко применяют в машиностроении, так как они не обеспечивают необходимого комплекса механических и технологических свойств изготовляемых из них деталей. Широко используют сплавы, состоящие из двух и более элементов. Элементы, входящие в сплав, называются компонентами.
Металлические сплавы, как и чистые металлы, имеют характерную кристаллическую решетку. Следовательно, они являются кристаллическими веществами. Свойства сплавов зависят от содержания в них основных компонентов, а также от концентрации легирующих элементов, которые специально вводят в сплавы для придания им требуемых свойств.
Получение сплава не всегда возможно. Например, железо со свинцом, свинец с цинком не образуют сплава, так как в жидком виде они не дают раствора. Обязательное условие для образования сплава – получение однородного жидкого раствора соединившихся компонентов. При затвердевании сплавы образуют различные типы соединений, определяющих их внутреннее строение. Внутреннее строение сплавов резко отличается от строения металлов, из которых они получены, поэтому и свойства сплавов отличаются от свойств их компонентов.
Существует несколько способов получения металлических и других сплавов: сплавлением, спеканием, электролизом. Наиболее распространенным является способ сплавления входящих в состав сплава компонентов. При этом возможно получение следующих типов сплавов: твердый раствор, механическая смесь и химическое соединение. Указанные виды соединений различаются по структуре и по свойствам. Образование того или иного типа сплава обусловливается поведением атомов составляющих его металлов при охлаждении расплава.
Механические смеси состоят из практически чистых зерен обоих компонентов, сохраняющих присущие им типы кристаллических решеток и прочностные свойства. Образование такого сплава происходит при любом соотношении компонентов. Механические смеси образуют компоненты с большим различием атомных диаметров, не способные к взаимному растворению друг в друге в твердом состоянии и не вступающие в химическую реакцию. Компоненты сплава могут обладать как одинаковыми, так и разными кристаллическими решетками. Механические свойства смесей зависят от количественного соотношения компонентов, от размеров и формы зерен.
Химические соединения, образующиеся при сплавлении двух компонентов имеют строго определенный состав. Они образуются обычно при соединении компонентов, расположенных в периодической системе далеко один от другого и имеющих одинаковые или различные решетки. Химические соединения представляют собой зерна со специфической кристаллической решеткой, отличной от решеток обоих компонентов. Ячейки решеток химических соединений имеют сложное строение. Связь между атомами в них сильнее и жестче металлической. Поэтому они являются очень твердыми и хрупкими веществами.
Если образующиеся в сплавах химические соединения оказываются стойкими веществами, не диссоциирующими при нагреве вплоть до температуры плавления, то их принято рассматривать в качестве самостоятельных компонентов, способных образовывать сплавы с компонентами сплава.
При растворении компонентов друг в друге образуются твердые растворы. Получающийся при этом продукт представляет собой зерна, кристаллическая решетка которых построена из атомов обоих компонентов (при кристаллизации сохраняется решетка только одного компонента – того, который является растворителем). Атомы растворенного компонента находятся в решетке растворителя.
Если атомы растворимого компонента замещают в узлах решетки атомы компонента-растворителя, то образующийся раствор называется раствором замещения(Рис.32.а.). Такие растворы образуют компоненты с аналогичными типами кристаллических решеток при небольшой разнице их параметров. К твердым растворам замещения относятся медноникелевые, железохромистые, железомарганцевые и другие сплавы. Объем новой решетки несколько изменяется в сторону увеличения или уменьшения параметров, в зависимости от размеров атома растворенного компонента. Если растворимый компонент имеет очень малый атомный диаметр, то образуется твердый раствор внедрения (Рис.32.б). В этом случае атомы растворимого компонента размещаются в междоузлии ячейки кристаллической решетки растворителя, не вытесняя атомов растворителя из узлов решетки. Твердые растворы внедрения получаются обычно при соединении металлов с неметаллами. Это объясняется тем, что атомы неметалла – растворенного компонента значительно меньше по размерам, чем атомы растворителя – металла. Компоненты с неограниченной растворимостью образуют только растворы замещения. Ограниченная растворимость наблюдается как у твердых растворов замещения, так и у растворов внедрения. При ограниченной растворимости компонентов за пределами их растворимости образуются или смеси зерен ограниченных твердых растворов обоих компонентов друг в друге (например, компонента А в В и компонента В в А), или смеси зерен ограниченного раствора и химического соединения компонентов.
В твердых растворах замещения преобладающей связью между атомами является металлическая. В растворах внедрения вместе с металлической может возникать и ковалентная связь.
Рис.32.Виды твердых растворов
Дата добавления: 2019-02-26; просмотров: 422; Мы поможем в написании вашей работы! |
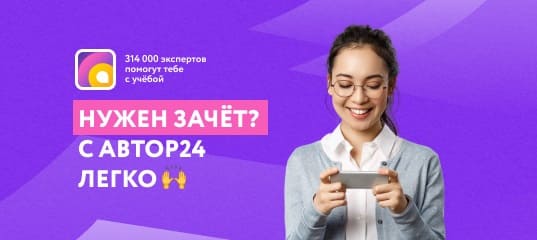
Мы поможем в написании ваших работ!