ТРЕБОВАНИЯ К КАЧЕСТВУ И ПРИЁМКЕ РАБОТ
Материалы, применяемые для изоляции стыков, должны иметь сертификаты, по которым контролируют их соответствие требованиям проекта и нормативным документам.
При входном контроле качества применяемых материалов следует контролировать параметры, указанные в табл. 4.
Таблица 4
Объект контроля | Характеристика | Способ контроля |
1. Внешний вид компонентов праймера | ||
Компонент А Компонент Б | - однородная масса от темно-зеленого до черного цвета - жидкость от оранжевого до темно-коричневого цвета, допускается наличие осадка | Определяют визуально при перемешивании |
2. Манжета | ||
Внешний вид рулона, толщина, геометрические размеры | Визуальным осмотром развернутого на 1-1,5 м полотна. Полотно должно быть двухслойным, без следов недолива, трещин, включений, отверстий, морщин, мест пропуска адгезионного слоя. Толщину манжеты определяют толщиномером по ГОСТ 11358-89 с погрешностью до 0,1 мм или микрометром МК-25 по ГОСТ 6507-90 по поперечному срезу, отступив от края манжеты на расстояние не менее 10 мм. Проверяют по клейму на ярлыке и в паспорте на данную партию манжет. Гарантийный срок хранения манжет и комплектующих изделий – 12 месяцев со дня изготовления. |
Порошок абразивный | ||
Наличие и правильность маркировки | в соответствие с п.4.2 ТУ 3989-003-82101794-2008 | Визуально |
Форма зерен | острая угловатая | Визуально |
Цвет зерен | Черный. Порошок может содержать незначительные включения коричневого, красного, белого цвета, что не влияет на качество. | Визуально |
Фракционный состав | Независимо от марки абразивного порошка содержание гранул заказанной фракции должно составлять не менее 85% от общей массы порошка | Визуально |
Хранение комплектующих изделий производится в соответствии с требованиями технических условий на их изготовление.
|
|
Результаты входного контроля должны быть зафиксированы в Журнале входного контроля и Акте входного контроля, составляемого по результатам контроля партии изоляционных материалов с выдачей заключения комиссии на годность к применению.
При выполнении работ производится операционный и инспекционный контроль работ по изоляции стыков, качества изоляционного покрытия.
Качество очистки изолируемых поверхностей проверяют внешним осмотром. На поверхности не должно быть острых выступов, заусениц, задиров, капель металла, шлака, флюса, копоти, грязи, влаги, масла, ржавчины, окалины. Очищенная поверхность должна иметь серо–стальной цвет.
Степень очистки зоны сварного стыка стальной поверхности труб должна быть не ниже Sa 2½ в соответствии с ИСО 8501-1, шероховатость поверхности Rz должна составлять от 40 до 90 мкм в соответствии с ИСО 8503-1, а запыленность поверхности должна быть не выше эталона 3 по ИСО 8502-3.
|
|
Контроль температуры подогрева производить контактным термометром в нескольких точках: (сверху, снизу, с обеих сторон трубы в близи кольцевого сварного шва и у кромки заводского покрытия).
При нанесении защитных покрытий следует непрерывно проводить визуальный контроль качества работ: очистку изолируемой поверхности труб, установку и усадку термоусаживащихся манжет.
Следует также проводить осмотр готового покрытия с целью контроля его состояния, при этом сформированное покрытие должно отвечать следующим требованиям:
- манжета должна плотно охватывать изолируемую поверхность металла и заводского покрытия трубы и иметь поверхность без пузырей, гофр, складок проколов, задиров, других сквозных дефектов, а также без следов прожига полиэтилена;
- через изоляцию должен проступать профиль сварного стыка трубы, нахлеста манжеты;
- адгезив должен выступать за кромку манжеты на заводском покрытии с обеих сторон от стыка на всем диаметре трубы;
- покрывает заводское покрытие не менее чем на 50 мм с обеих сторон;
- сплошность покрытия должна быть проконтролирована дефектоскопом с напряжением 5 кВ/мм толщины покрытия;
|
|
- нет отслоившихся краев замковой ленты. Запрещается производить нагрев замковой ленты после усадки манжеты;
- адгезия манжеты в нахлесте и к металлу проводить методом отслаивания через 24 часа. Допускается предварительный контроль не ранее чем через 2 часа.
Технические критерии и средства контроля операций приведены в табл. 5.
Таблица 5
Наименование процессов, подлежащих контролю | Предмет контроля | Инструмент и способ контроля | Периодичность контроля | Ответственный контролер | Технические критерии оценки качества | |||
Предварительная очистка поверхности труб | Качество очистки | Визуально | Непрерывно (в процессе работы) | Мастер Лаборант по изоляции | Наличие заусенцев, задиров, брызг металла не допускается | |||
Скос кромок заводского покрытия | Угол скоса | Шаблон | Непрерывно (в процессе работы)100% | Прораб Мастер Прораб | Угол скоса не более 30º | |||
Предварительный прогрев и сушка поверхности сварного стыка труб и прилегающего заводского покрытия | Отсутствие влаги | Контактный термометр | Постоянно Количество точек (4) | Мастер Лаборант по изоляции | Температура подогрева 50-60оС | |||
Финишная очистка поверхности трубы (пескоструйная обработка) и придание шероховатости прилегающей зоне с заводской изоляцией
| Степень очистки | Визуально | Непрерывно (в процессе работы) | Мастер Лаборант по изоляции | Степень очистки зоны сварного стыка стальной поверхности труб должна быть не ниже Sa 2½ в соответствии с ИСО 8501-1, шероховатость поверхности Rz должна составлять от 40 до 90 мкм в соответствии с ИСО 8503-1, а запыленность поверхности должна быть не выше эталона 3 по ИСО 8502-3. После окончания обработки труба должна иметь светло-серый цвет, без следов ржавчины и окалины. (При осмотре невооруженным глазом окалина и ржавчина не обнаруживаются). Равномерный серо–стальной цвет поверхности без темных или рыжих пятен. Шероховатость на заводском покрытии на ширине не менее 200 мм. | |||
Непрерывно (в процессе работы) | Прораб | |||||||
Приготовление праймера | Однородность, температура компонентов | Контактный термометр, пластиковый контейнер, шпатели | Непрерывно (в процессе работы) | Мастер Лаборант по изоляции | Однородный состав приготовленного праймера, отсутствие сгустков, комков и т.п. Температура в пределах 20º±5ºС | |||
Нанесение праймера на подогретую до 105º-110ºС поверхность. | Равномерность нанесения праймера по поверхности поролоно-вым роликом | Визуально | Непрерывно (в процессе работы) | Мастер Лаборант по изоляции | Равномерность нанесения праймера по поверхности открытого металла и отсутствие пропусков и подтеков. Толщина праймера после нанесения должна составлять 100-200 мкм. Праймер не наносится на заводское покрытие | |||
Нагрев заводского покрытия с обеих сторон
| Температура нагрева | Контактный термометр
Линейка | Постоянно Количество точек (4) | Мастер | Температура нагрева заводского покрытия на расстоянии не менее 200 мм от сварного шва 105º-110ºС | |||
Постоянно 100% сварных стыков | Прораб | |||||||
Установка манжеты | Зона нахле-ста краев манжеты при монтаже, обеспеч-ая необходимый провис | Линейка | Непрерывно (в процессе работы). | Мастер Лаборант по изоляции | нахлест ленты должен быть 100±20 мм | |||
Установка замковой ленты | Правильность установки замковой ленты | Визуально | Непрерывно (в процессе работы). | Мастер Лаборант по изоляции | Середина нахлеста проходит по середине замковой ленты. Нет отслаивающихся краёв замковой ленты. | |||
Усадка манжеты | Направление усадки | Визуально | Непрерывно (в процессе работы). | Мастер Лаборант по изоляции | Соответствие п.п.2.11.6. и 2.12 | |||
Контроль качества готового покрытия
Контроль качества готового покрытия
Контроль качества готового покрытия | Ширина нахлеста манжеты после усадки на зав. покрытие | Линейка | Постоянно 100% сварных стыков | Мастер | Ширина нахлеста на заводское покрытие после усадки не менее 50 мм. | |||
Лаборант по изоляции | ||||||||
Положение замка | Визуально | Постоянно 100% сварных стыков Постоянно 100% сварных стыков | Мастер Лаборант по изоляции | Середина пластины замка над линией нахлеста. Наличие отслаивающихся краев на замковой ленте не допускается. Запрещается производить нагрев замковой ленты после усадки манжеты. | ||||
Качество усадки манжеты | Визуально
| Постоянно 100% сварных стыков | Мастер | Соответствие п.2.12 и п.3.8. Отсутствие гофр, воздушных мешков. (Под усаженной манжетой не должно быть воздушных пузырей. Покрытие копирует профиль сварного шва. Виден проступивший адгезив шириной 5-10 мм. Края манжеты должны плотно прилегать к заводскому покрытию и не иметь отслоений. | ||||
Постоянно 100% сварных стыков | Лаборант по изоляции | |||||||
Адгезия покрытия к стали и заводскому покрытию | Адгезиметр типа АМЦ2-20 или его аналог | Контроль адгезии должен осуществляться на трех изолированных сварных стыках в начале проведения работ и не менее чем на одном изолирован- ном сварном стыке из каждых последующих 100. Дополнительный контроль должен производиться по требованию контролирующего персонала в случае возникновения подозрений на низкое качество |
Мастер Прораб Лаборант по изоляции
| Показатель прочности адгезионной связи сформированного покрытия должен составлять к металлу не менее 10 кгс/см (100 Н/см) при температуре (23±20)С | ||||
Сплош- ность изоляционного покрытия | Искровой дефектоскоп типа «Корона–2» | Постоянно 100% контроль поверхности труб | Перед проведением испытаний покрытие проверяют на сплошность искровым дефектоскопом при напряжении 5 кВ/мм + 5 кВ. Измерение электросопротивления проводят при температуре (20±5) °С при напряжении (100±5) В. За результат испытаний принимают показание прибора через (30±5) секунд после начала измерения. | |||||
Прочность при ударе | Приспособление для контроля прочности защитных покрытий при ударе | В местах вызывающих сомнение | ГОСТ Р 51164-98 Приложение А табл.2, п.8 (п.6.2.7.) | |||||
Толщина готового покрытия | Толщиномер по ГОСТ 11358 с точностью ±0,1мм | Не менее чем в 12 точках равномерно распределенных по 4-м продольным образующим пов-ти изолированной зоны стыка | Мастер Прораб Лаборант | 3 мм по п. 5.7.2 . ТУ |
Выявленные дефекты готового изоляционного покрытия, а также повреждения изоляции, произведенные во время проверки ее качества, должны быть устранены.
Выполненные работы по переизоляции и результаты контроля качества оформить в журнале изоляционно-укладочных работ.
Адгезионная прочность проверяется на одной или нескольких усаженных манжетах установочной партии, а также по требованию заказчика или возникновении подозрений на низкое качество изоляции сварного стыка. Адгезия определяется методом отслаивания полосы покрытия под углом 90±10 градусов со скоростью 10±1 мм/мин. Адгезионная прочность покрытия к стали и полиэтиленовому покрытию должна составлять не менее10 кгс/см (100 Н/см) при температуре (23±2) °С согласно ТУ 2245-048-82119587-2014.
При неудовлетворительном качестве изоляции сварного стыка, необходимо произвести его переизоляцию.
При удовлетворительном качестве место проведения испытаний должно быть отремонтировано с применением ремонтных материалов «Терма-Р» и «Терма-РЗ», предназначенных для ремонта повреждений заводского полиэтиленового покрытия и термоусаживающихся манжет.
Ремонту подлежат дефекты термоусаживающейся манжеты площадью не более 100 см. При наличии дефектов в манжете (отслоений, задиров и пр.) площадью более 100 см2 необходимо заново выполнить его изоляцию.
Дата добавления: 2019-02-22; просмотров: 256; Мы поможем в написании вашей работы! |
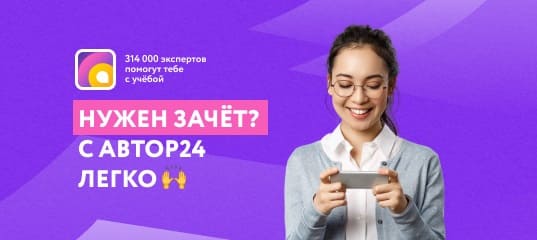
Мы поможем в написании ваших работ!