Магнитные методы контроля сварных соединений
Цель работы : изучение техники выполнения магнитных методов контроля, а так же оборудования для его выполнения.
Оборудование и материалы
- дефектоскоп ГСП ПМД-70 (МД-70ПК-111У);
- дефектоскопы магнитографические МД-11Г и МГК-1.
- контрольный образец;
- намагничивающие устройства типа ПНУ;
- источник питания намагничивающего устройства.
Нормативная и техническая документация
- паспорт и техническое описание дефектоскопа ГСП ПМД-70;
- паспорт и техническое описание дефектоскопа магнитографического МД-11Г;
- паспорт и техническое описание магнитографического дефектоскоп МГК-1;
- ГОСТ 25225-82 Контроль неразрушающий. Швы сварных соединений трубопроводов. Магнитографичский метод;
- ГОСТ 21105-87 Контроль неразрушающий. Магнитопорошковый метод.
Содержание отчета
- цель работы, оборудование и приборы;
- краткое описание сущности магнитных методов контроля;
- описание магнитографического дефектоскопа и его работы;
- эскизы дефектных мест, выявленных магнитопорошковым методом;
- выводы по работе.
Общие положения
Магнитные методы контроля основаны на обнаружении магнитных потоков рассеяния, создаваемых дефектами в намагниченных изделиях из ферромагнитных материалов. Магнитный поток, встречая на своем пути дефект, огибает его, поскольку магнитная проницаемость дефектов на несколько порядков ниже, чем основного материала. В результате этого часть магнитных линий вытесняется на поверхность, образуя местный поток рассеяния (рисунок 16).
|
|
а) б)
Рисунок 16 Распределение магнитного потока по сечению бездефектного шва (а) и шва, содержащего дефект (б).
В зависимости от способа регистрации потока рассеяния магнитные методы контроля подразделяются на магнитопорошковый и магнитографический. В первом случае потоки рассеяния выявляются с помощью магнитного порошка, во втором регистрируются с помощью магнитной ленты.
Сущность магнитопорошкового метода заключается в том, что на поверхность намагниченной детали наносят ферромагнитный порошок в виде суспензии /мокрый метод/ или аэрозоля /сухой метод/. В результате действия местных потоков рассеяния, порошок скапливается над дефектами, указывая их местоположение и форму.
Технология контроля включает в себя следующие операции:
- очистка поверхности от окалины, шлака, загрязнения;
- намагничивание контролируемого изделия;
- нанесение суспензии или порошка на поверхность изделия;
- осмотр изделия и выявление дефектов.
Метод обладает высокой чувствительностью к тонким и мелким трещинам, оперативностью и наглядностью результатов.
|
|
Для приготовления суспензии чаще всего используют масло – керосиновые смеси /соотношение 1:1/, содержащие 50…60г порошка на 1л жидкости. В качестве материала для приготовления порошка используют мелко помолотую окись железа с размером частиц (5…10)мкм, стальные опилки, получающиеся при шлифовании. Для лучшей индикации дефектов применяют цветные порошки, получаемые окрашиванием или отжигом темных порошков.
Сущность магнитографического метода заключается в намагничивании контролируемого изделия с одновременной записью магнитного поля на магнитную пленку (рисунок 17), с последующей расшифровкой полученной информации специальными магнитографическими дефектоскопами.
Рисунок 17 Схема магнитографического контроля: 1 - Обмотка намагничивающего устройства; 2 сварной шов; 3 – дефект шва; 4 – магнитная лента;
Контроль выполняется в следующей последовательности:
Очистка контролируемых соединений от брызг, шлака, и других загрязнений.
Наложение на шов магнитной ленты. Перед началом работы лента, независимо от того новая она или бывшая в употреблении, должна быть размагничена. Прижим ленты ко шву производится эластичными накладками.
|
|
Намагничивание контролируемого изделия.
Расшифровка результатов контроля.
Чувствительность магнитографического контроля W определяется как отношение вертикального размера дефекта ∆S к толщине контролируемого изделия S:
.
Чувствительность магнитографического контроля зависит от глубины залегания, ориентации, формы и размеров дефектов, типа магнитной ленты, параметров дефектоскопа. Этим способом надежно выявляются плоскостные дефекты /трещины, не провары/, а так же протяженные дефекты, ориентированные поперек магнитного потока. Значительно хуже выявляются дефекты, имеющие округлую или овальную форму. Легче выявляются дефекты, расположенные у поверхности метала, тем не менее, современные дефектоскопы надежно обнаруживают дефекты с вертикальным размером 10…15% толщины изделия при глубине залегания (20…25)мм.
На чувствительность сильно влияет форма и высота усиления шва, а так же состояние его поверхности. Для повышения надежности выявления дефектов необходимо, чтобы высота усиления не превышала 25% толщины метала, а переход от наплавленного метала к основному был плавным. Чешуйчатость на поверхности шва должна составлять не более 25…30%, высота усиления не более 1мм. Швы с грубой чешуйчатостью должны подвергаться предварительной зачистке. Наилучшие результаты получаются при контроле швов, выполненных автоматической сваркой.
|
|
Расшифровка результатов контроля производится с помощью магнитографических дефектоскопов. На рисунке 18 приведена схема работы дефектоскопа.
Рисунок 18 Схема работы магнитографического дефектоскопа: 1 – ротор; 2 -магнитные головки; 3 – электродвигатель; 4 – электронный усилитель; 5 – генератор развертки; 6 – блок питания; 7 – электроннолучевая трубка.
Электродвигатель приводит во вращение барабан с несколькими магнитными
головками, которые при этом перемещаются поперек пленки. В головках происходит преобразование записанного магнитного сигнала в электрический сигнал, который, будучи усиленным, подается на отклоняющие пластины ЭЛТ.
Существуют дефектоскопы с импульсной и телевизионной индикацией. При импульсной индикации сигнал, возникающий при прохождении участка пленки, находившегося при намагничивании над дефектом, приводит к появлению на экране ЭЛТ импульса, амплитуда которого характеризует размер дефекта в вертикальном направлении. При телевизионной индикации магнитная запись на пленке преобразуется в телевизионное изображение отдельных участков шва. Совершенные магнитографические дефектоскопы, в их числе и МГК – 1, имеют двойную индикацию.
Намагничивающее устройство, входящее в комплект дефектоскопа, состоит из П – образного магнитного сердечника (см. рис.17) с расположенной на нем обмоткой. Устройство установлено на четырех роликах опорах, что позволяет перемещать устройство вдоль шва.
Обмотка намагничивающего устройства записывается от источников постоянного тока (выпрямителей).
Порядок выполнения работы
1. Изучить конструкцию и правила эксплуатации магнитопорошкового дефектоскопа ПМД-70
2. Изучить требования к выполнению магнитопорошкового контроля по ГОСТ 21105-87.
3. Произвести намагничивание образцов с помощью намагничивающего устройства магнитопорошкового дефектоскопа и произвести испытание контрольного образца.
4. Изучить конструкцию и правила эксплуатации магнитографических дефектоскопов МД-11 и МГК-1;
5. Изучить требования к выполнению магнитографического контроля по ГОСТ ГОСТ 25225-82.
Контрольные вопросы
1. Физическая сущность магнитных методов контроля.
2. Методика выполнения магнитопорошкового и магнитографического методов контроля.
3. Чувствительность магнитных методов контроля.
4. Устройство магнитографических дефектоскопов.
Лабораторная работа №5
Капиллярные методы контроля
Цель работы: изучить методику и освоить технику разновидностей капиллярного метода контроля
Оборудование и материалы
- цветной аэрозольный переносной комплект для цветного контроля;
- источник света – отражательная лампа;
- образцы сварных соединений из различных материалов.
Нормативная и техническая документация
- ГОСТ 18442-80 Контроль неразрушающий. Капиллярные методы. Общие требования;
- ОСТ 36-76-83 Контроль неразрушающий. Сварные соединения трубопроводов и конструкций. Цветной метод;
Содержание отчета
- цель работы и порядок выполнения работы.
- краткое описание капиллярных методов контроля.
- описать технику выполнения разновидностей контроля.
- рисунки дефектных мест выявленных цветным методом контроля.
- выводы по работе.
Общие положения
Капиллярные методы контроля предназначены для обнаружения дефектов – несплошности материала, не видимых не вооруженным глазом. Эти методы основаны на использовании капиллярных свойств жидкостей обладающих высокой проникающей способностью, так называемых пенетрантами.
Дефекты выявляют, обнаруживая либо жидкость, оставшуюся в их полостях после удаления ее с поверхности, либо скопление частиц порошка взвешенного в жидкости и отфильтровавшегося на поверхности детали при заполнении полости дефекта жидкостью. В первом случае оставшуюся в полостях дефектов жидкость обнаруживают чаще всего после внесения проявителя. Он поглощает жидкость, образуя индикаторный рисунок. Во втором случае скопления порошка обнаруживается без применения проявляющего вещества.
Индикаторные рисунки обладают способностью либо люминесцировать в ультрафиолетовых лучах, либо меняют окраску, вызываемую избирательным поглощением (отражением) части падающих на них лучей.
Из существующих разновидностей капиллярной дефектоскопии наибольшее применение получили цветная, люминесцентная и цвета – люминесцентная.
Капиллярная дефектоскопия – простой способ, имеющий высокую чувствительность к поверхностным дефектам.
К преимуществам способа можно отнести высокую чувствительность, разрешающую способность и достоверность контроля, наглядность результатов контроля, возможность контроля деталей различной сложности в один прием, универсальность технологических операций при контроле широкой номенклатуры материалов деталей, а так же низкая стоимость используемых материалов.
К недостаткам метода можно отнести возможность обнаружения только поверхностных дефектов, большая длительность процесса (до 0,5 – 1,5ч) снижение достоверности контроля при отрицательных температурах, необходимость удаления с поверхности лакокрасочных покрытий и тщательной очистки поверхностей, низкая вероятность обнаружения дефектов, покрытых оксидными пленками, тонким слоем деформированного материала или сжатых значительными остаточными или рабочими напряжениями в детали, вредность дефектоскопических материалов, субъективность контроля, ограниченный срок хранения дефектоскопических материалов.
Методы капиллярной дефектоскопии позволяют обнаруживать различные поверхностные дефекты: трещины (шлифовочные, термические, усталостные), закаты волосовины, заковы, растрескивания, пористость, различные виды коррозии на деталях простой и сложной формы, изготовленных из черных и цветных металлов и сплавов, пластмасс и др. материалов.
Высокая чувствительность позволяет определять трещины с шириной раскрытия у входа на поверхность ~0,001мм, глубиной более 0,01мм и длиной болие0,1мм.
При цветной, люминесцентной и цвета – люминесцентной дефектоскопии контроль осуществляется в следующей последовательности:
1. Нанесение проникающей жидкости (пенетранта) на контролируемую поверхности деталей.
2. Выдержка деталей в течение определенного времени 15 – 20 мин (до 1,5 часов).
3. Удаление проникающей жидкости с поверхности.
4. Нанесение проявителя.
5. Проявление дефектов и осмотр детали.
6. Удаление проявителя и следов других дефектоскопических материалов с поверхности годных деталей.
Способы удаления проникающей жидкости с поверхности деталей выбирают, учитывая необходимость ее сохранения в полостях дефектов, а так же ряд других факторов – тип используемой индикаторной проникающей жидкости, шероховатость поверхности, условия контроля (цеховые, полевые или лабораторные), объем работ и требуемую производительность.
Удаление проникающей жидкости производят протиркой, промывкой, обдувкой, гашением люминесценции и цвета, и их комбинации.
Способ нанесения проявителя выбирается с учетом следующих основных факторов – требуемой чувствительности контроля, типа и свойств проявителя, степени сложности формы поверхности детали, объема работ и необходимой производительности труда. Нанесение проявителя осуществляется: нанесением кистью, распылением, электрораспылением, погружением, электроосаждением, обливанием с использованием воздушной взвеси, посыпанием, наложением липких лент.
Проявление дефектов является наиболее важным этапом метода и выполняется: выдержкой детали до полного проявления дефектов (временной), путем прогревания детали (тепловой), ваакумированием пространства над контролируемой поверхностью с постоянной или изменяющимся разряжением, вибрационным воздействием на деталь и их комбинации.
Порядок выполнения работы
1. Нанести на очищенные от загрязнений образцы швов пенетрант.
2. Выдержать в течении 10 – 15 мин, затем удалить пенетрант с помощью растворителя, шов просушить.
3. Нанести на сухой шов слой проявителя.
4. Определить наличие трещин по красным пятнам на белой поверхности проявителя, который адсорбирует пентрант, проникший в трещины.
5. Занести результаты опыта в отчеты и зарисовать картину контролируемых участков швов, обработать результаты ответов и сделать выводы.
Контрольные вопросы
1. Назовите особенности капиллярного метода контроля.
2. Объясните методику люминесцентного контроля.
3. В чем заключается методика цветного контроля?
4. Назовите области применения капиллярных методов контроля.
5. В чем состоят преимущества и недостатки метода?
Лабораторная работа №6
Дата добавления: 2019-01-14; просмотров: 748; Мы поможем в написании вашей работы! |
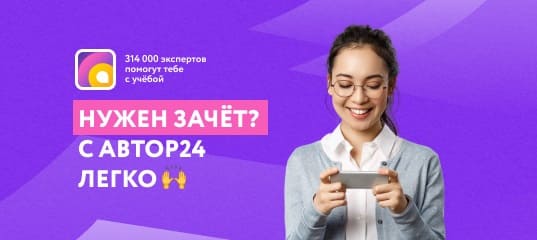
Мы поможем в написании ваших работ!