Контроль сварного соединения ультразвуком
Министерство образования Российской Федерации
Омский государственный технический университет.
МЕТОДИЧЕСКИЕ УКАЗАНИЯ
К ЛАБОРАТОРНЫМ РАБОТАМ ПО КУРСУ
“КОНТРОЛЬ КАЧЕСТВА СВАРНЫХ КОНСТРУКЦИЙ”
Омск – 2011
Составители:
В.А. Соколов, доцент, к.т.н.
Ю.О. Филиппов, ассистент
Аннотация
Методические указания содержат перечни применяемых приборов и нормативных материалов, общие положения по основным способам неразрушающего контроля сварных конструкций, порядок выполнения лабораторных работ, а также контрольные вопросы для проверки полученных знаний.
Методические указания предназначены для студентов бакалаврских направлений 150400. 62. «Технологические машины и оборудование» и 150700.62 «Машиностроение» с профильной подготовкой «Оборудование и технология сварочного производства».
Введение
Обеспечение высокого качества сварочных работ – одна из наиболее важных проблем в области сварки, значение которой все более возрастает по мере усложнения конструкций сварных изделий.
Эта проблема является многогранной и решается в нескольких направлениях. Среди них ответственная роль принадлежит применению современных методов и средств неразрушающего контроля, эффективность которых определяется их достоверностью и производительностью.
Среди методов неразрушающего контроля, применяемых в настоящее время в сварочном производстве, наиболее важное место занимают методы визуально – измерительного контроля, радиографические, ультразвуковые и магнитные методы обнаружения несплошностей, капиллярные методы, а также методы контроля герметичности сварных соединений и конструкций.
|
|
Качество сварных соединений зависит от качества исходных основных и сварочных материалов, качества сборки под сварку, соблюдения технологии сварки и других факторов. Поэтому операции контроля должны начинаться со входного контроля основных и сварочных материалов, выполняться в процессе выполнения отдельных сварных швов и завершаться окончательным контролем готовой сварной конструкции.
В настоящих методических указаниях содержатся сведения об основных методах неразрушающего контроля, применяемых для контроля сварных соединений и конструкций, а также порядок выполнения лабораторных работ с применением соответствующих приборов, их описаний и действующих нормативных документов по контролю.
Лабораторная работа №1
Визуально – измерительный метод контроля
Цель работы: Изучение методики и технологии визуально измерительного контроля сварных швов и применяемых для этого приборов и устройств
|
|
Оборудование и материалы:
- Образцы деталей собранные под сварку
- Сварные образцы стыковых и тавровых соединений, выполненные различными способами сварки.
- лупы измерительные по ГОСТ 25706;
- угольники поверочные 90° лекальные по ГОСТ 3749;
- штангенциркули по ГОСТ 166 и штангенрейсмусы по ГОСТ 164;
- шаблон типа УШС-3 (шаблон сварщика универсальный), модель 00314;
- линейка измерительная металлическая длиной 400мм;
Нормативная и техническая документация
- РД 03-606-03 Инструкция по визуально измерительному контролю;
- Паспорт шаблона УШС 3 00314. 000ПС;
- ГОСТ 5264 – 80 ручная дуговая сварка. Соединения сварные. Основные типы, конструктивные элементы и размеры;
- ГОСТ 16037 – 80 Соединения сварные стальных трубопроводов. Основные типы, конструктивные элементы и размеры;
- ГОСТ 14771 – 76 Дуговая сварка в защитном газе. Соединения сварные. Основные типы, конструктивные элементы и размеры;
- Операционные технологические карты по визуально измерительному контролю.
Содержание отчета:
- название и цель работы;
- описание хода выполнения работы;
- эскизы сварных образцов, с указанием размеров и отклонений, обнаруженных в процессе выполнения работы;
|
|
- заключение о соответствии испытанных образцов требованиям нормативной документации.
Общие положения
Визуальный и измерительный контроль качества сварных соединений (наплавок) в процессе сварки и готового сварного соединения выполняют с целью подтверждения их соответствия требованиям конструкторской документации, производственной и нормативной технической документации.
Визуально измерительному контролю в объеме 100%, подвергаются исходные материалы и детали, подлежащие сварке, собранные под сварку узлы, готовые сварные соединения. Сварные соединения, забракованные при визуально измерительном контроле не подлежат испытаниям физическими методами контроля и механическим испытаниям.
Материал заготовок бракуется при наличии вмятин, заусенцев, окислов, ржавчины, и т.д. Определяют качество подготовки кромок под сварку: очистку поверхностей, правильность разделки кромок. При контроле собранных соединений проверяют качество зачистки кромок, соответствие допустимым значениям зазоров, смещение кромок сопрягаемых поверхностей, перелом осей при сборке трубопроводов. При сборке деталей проверяются также геометрические размеры собранного узла.
|
|
Визуальный и измерительный контроль выполненных сварных соединений (конструкций, узлов) проводят с целью выявления деформаций, поверхностных трещин, подрезов, прожогов, наплывов, кратеров, свищей, пор, раковин и других несплошностей и дефектов формы швов; проверки геометрических размеров сварных швов и допустимости выявленных деформаций, поверхностных несплошностей и дефектов формы сварных швов.
Для контроля применяются специальные шаблоны или универсальный инструмент. Оптические приборы для контроля используют с небольшим увеличением (не более 20 –30 раз), так как с возрастанием их увеличения существенно сокращается поле зрения и глубина резкости, а также снижается производительность и надежность результатов контроля.
Внешний вид шва характерен для каждого способа сварки, пространственного положения шва. Неравномерная ширина и высота шва, неравномерная чешуйчатость указывают на колебания мощности дуги, нестабильность ее горения. При сварке в защитных газах или вакууме внешняя поверхность швов должна быть гладкая, блестящая, без чешуек.
Сварные швы принимают по внешнему виду в сравнении с эталонами. Геометрические характеристики швов замеряют с помощью шаблонов, или измерительных инструментов, сравнивая их с размерами, приведенными в нормативной документации или в технологических картах.
Порядок выполнения работы
1. Подготовить образцы для проведения визуально измерительного контроля.
Требования к выполнению измерительного контроля при подготовке деталей под сварку приведены в таблице 1 и на рисунке 1
Таблица 1 Требования к измерениям размеров подготовки под сварку стыкового соединения стального трубопровода
Контролируемый параметр | Средства измерений | Примечания |
Овальность (наружный диаметр) | рулетка | Измерения в двух взаимно- перпендикулярных сечениях по наибольшему и наименьшему диаметрам |
Геометрические размеры коррозионных и механических дефектов | Шаблон универсальный, штангенциркуль, линейка | Измерения наибольшего и наименьшего размеров и наибольшей глубины |
Угол скоса кромки | Угломер или шаблон универсальный | Измерение в одном месте |
Притупление кромки | Штангенциркуль | Измерения в двух взаимно перпендикулярных сечениях (4 точки) |
Отклонение плоскости торца трубы (детали) от перпендикуляра к образующей | Угольник и линейка | Измерения не менее, чем по трем образующим в зоне максимального отклонения |
Рисунок 1 – Размеры, подлежащие измерительному контролю при подготовке под сварку
а) разделка кромки при толщине стенки до 15 мм включительно;
б) разделка кромки при толщине стенки свыше 15 мм
Требования к выполнению измерительного контроля при сборке сварных соединений под сварку приведены в таблице 2 и на рисунке 2
Таблица 2 Требования к измерениям параметров сборки соединений деталей под сварку.
Контролируемый параметр | Средства измерений | Примечания |
Зазор в соединении | Шаблон универсальный | Не менее чем в трех местах равномерно расположенных по длине стыка |
Смещение кромок с наружной стороны соединения | Шаблон универсальный | В месте наибольшего смещения |
Перелом осей | Линейка (L = 400 мм), рулетка и щуп | Измерение проводится в плоскости, проходящей через оси свариваемых деталей |
Длина прихватки | Линейка или штангенциркуль | Измерение каждой прихватки |
Высота прихватки | Штангенциркуль | Измерение каждой прихватки |
Расстояние между прихватками | Линейка, рулетка | Измерение расстояния между соседними прихватками |
а) б)
Рисунок 2 – Размеры, подлежащие измерительному контролю сборки под сварку
А – зазор в соединении, F, F1 – смещение кромок, δ – угол разделки кромок
а) – стыковое соединение б) –угловое и тавровое соединение
Требования к выполнению измерительного контроля сварных швов приведены в таблице 3 и на рисунке 3.
Таблица 3 Контролируемые параметры и средства измерений сварных швов
Контролируемый параметр | Средства измерений | Примечания |
Высота шва | Штангенциркуль или шаблон | В местах наибольшей и наименьшей высоты шва, но не менее чем в 3 точках по длине шва |
Ширина шва | Штангенциркуль или шаблон | В местах наибольшей и наименьшей ширины шва, но не менее чем в 3 точках по длине шва |
Выпуклость (вогнутость) шва | Штангенциркуль или шаблон | Измерения в 3 местах, выделенных по результатам визуального контроля |
Глубина подреза | Штангенциркуль, шаблон или приспособление для измерения глубины подреза | Измерению подлежит каждый подрез |
Величина смещения кромок | Штангенциркуль или шаблон | Измерение в местах, вызывающих сомнение по результатам визуального контроля, но не менее, чем в 3 точках по длине шва |
Катет углового шва | Штангенциркуль или шаблон | Измерение в местах, вызывающих сомнение по результатам визуального контроля, но не менее, чем в 3 точках по длине шва |
Чешуйчатость шва | Штангенциркуль или шаблон | Измерение в местах, вызывающих сомнение по результатам визуального контроля, но не менее, чем в 3 точках по длине шва |
Глубина западаний между валиками | Штангенциркуль или шаблон | Измерение в местах, вызывающих сомнение по результатам визуального контроля, но не менее, чем в 3 точках по длине шва |
Размеры (диаметр, длина, ширина) одиночных несплошностей | Лупа измерительная | Измерению подлежит каждая несплошность |
а) б)
в) г)
Рисунок 3 - Размеры сварного шва, подлежащие измерениям при ВИК
а) размеры стыкового шва: е, е1 – ширина шва; g,g1 – высота усиления шва
б) размеры дефектов сварного шва: b1 –глубина подреза; b2 – глубина вогнутости (утяжина)
в,г – размеры углового шва: к, к1 –размеры катетов углового шва.
2. Провести внешний осмотр и отметить дефектные места.
3. Произвести замер геометрических параметров сварных швов – высоты и ширины стыковых соединений, катета шва угловых соединений.
4. Дефектные участки швов зарисовать в отчете.
5. Обобщить результаты и сделать выводы по проделанной работе.
Контрольные вопросы
1. Назовите разновидности визуально – измерительного контроля?
2. В каких объемах и кем производится визуально измерительный контроль?
3. Назовите приборы, применяемые для визуально – измерительного контроля?
4. Какие размеры можно проконтролировать с помощью УШС 3?
5. Какие размеры контролируют при подготовке кромок под сварку?
6. Какие размеры контролируют при сборке деталей под сварку?
7. Какие размеры контролируют при контроле сварных швов?
8. Как производится контроль геометрии швов?
9. Что делают со сварными узлами не прошедшими испытания по ВИК?
Лабораторная работа №2
Контроль сварного соединения ультразвуком
Цель работы: Изучить физические основы ультразвукового контроля, схемы контроля, технологию выполнения и оборудование для ультразвуковой дефектоскопии.
Оборудование и материалы:
- образцы контрольных сварных соединений;
- ультразвуковые дефектоскопы УД2-12, ЭВУД ПК;
- стандартные образцы по ГОСТ 14782-86 №1, №2 и №3 для настройки дефектоскопа;
- стандартные образцы предприятия (СОП) по ВСН 012-88;
- минеральное масло, кисточка, ветошь и др. материалы.
Нормативная и техническая документация:
- паспорт и техническое описание дефектоскопа УД2-12;
- паспорт и техническое описание дефектоскопа ЭВУД ПК;
- ГОСТ 14782-86 Контроль неразрушающий. Соединения сварные. Методы ультразвуковые;
- ВСН 012-88 Ведомственные строительные нормы. Строительство магистральных и промысловых трубопроводов. Контроль качества и приемка работ;
- операционные технологические карты ультразвукового контроля сварных соединений.
Содержание отчета
- название и цель работы;
- методы контроля ультразвуком сварных соединений;
- схемы контроля стыковых и угловых швов;
- эскизы сварного соединения с указанием дефектов.
- порядок оформления результатов ультразвукового контроля
Общие положения
Ультразвуковой контроль основан на использовании упругих механических колебаний частотой 0,5 – 10 МГц, распространяющихся в контролируемых изделиях. Механические колебания при ультразвуковой дефектоскопии получают с помощью пъезопреобразователей (ПЭП), представляющих собой пластину из титанита бария или цирконата титаната свинца (ЦТС).
Сущность работы ПЭП заключается в том, что при подаче на пъезопластину переменного электрического напряжения, она изменяет свои геометрические размеры (толщину) с частотой приложенного напряжения, передавая в окружающую среду механические колебания соответствующей частоты. И, наоборот, при падении на поверхность пластины механических волн на торцах пластины возникают импульсы электрического напряжения, которые затем усиливаются и подаются на экран прибора.
Ультразвуковые волны имеют свойства присущие волновым процессам, то есть, их можно описывать такими параметрами как: частота (f), длина волны (λ), скорость ее распространения (С). При распространении в сплошной среде происходит их затухание, а при переходе из одной среды в другую, наблюдается преломление и отражение ультразвуковых волн.
В твердой среде могут распространяться продольные волны, у которых направлений смещений элементарных микрообъемов совпадает с направление распространения волны, и поперечные волны, имеющие смещение перпендикулярное направлению распространения волны, кроме того, имеют место и так называемые, поверхностные волны, распространяющиеся по поверхности раздела сред.
Для обнаружения в контролируемом материале дефектов - несплошностей используют, либо отраженный от дефекта сигнал, при этом метод называют эхо-методом, либо фиксируют снижение уровня сигнала с обратной стороны детали дополнительным искателем – приемником, тогда метод называют теневым.
В практике ультразвукового контроля сварных соединений наиболее широкое распространение нашел эхо – метод и некоторые его разновидности. Метод основан на отражении УЗ - колебаний от границы раздела несплошности (дефекта) со средой, при этом амплитуда эхо – сигнала на экране прибора пропорциональна площади отражательной поверхности дефектного участка, а его положение на горизонтальной развертке пропорционально глубине залегания дефекта по направлению распространения луча.
Аппаратура для ультразвукового контроля состоит из дефектоскопа, комплект искательных головок различных типов и вспомогательных устройств.
Ультразвуковые дефектоскопы, выпускаемые, промышленностью работают в импульсном и непрерывном режимах излучения ультразвуковых колебаний.
При контроле сварных швов используют прямые, распространяющие продольные волны перпендикулярно поверхности ввода, наклонные искатели с вводом чисто поперечных ультразвуковых колебаний под углом к вертикали и раздельно-совмещенные искатели, распространяющие в материале продольные волны под небольшим углом к поверхности (Рисунок 4).
Рис. 4 Различные типы преобразователей а) прямой искатель, б) - наклонный искатель, в – раздельно-совмещенный искатель
1 – пъезопластина, , 2 – демпфер, 3 – корпус, 4 – призма
В наклонных и раздельно – совмещенных искателях пъезоэлемент приклеен к призмам из оргстекла или другой пластмассы, в которых ультразвук распространяется с небольшой скоростью, что позволяет при относительно малых углах падения вводить в контролируемый металл чисто поперечные волны.
Прямые и наклонные искатели работают в основном по совмещенной схеме, т.е. один и тот же пъезоэлемент является излучателем и приемником ультразвука.
В РС – искателях одна пластина пъезопреобразователя является излучателем, другая – приемником и работают они в непрерывном режиме.
Для настройки чувствительности ПЭП и прибора ГОСТ 14782-86 предусматривает несколько типов стандартных образцов.
Рисунок 5 Стандартный образец СО №1
Стандартный образец СО №1 (рисунок 5) применяют для определения условной чувствительности, проверки разрешающей способности и погрешности глубиномера дефектоскопа. Образец СО №1 изготавливается из органического стекла.
Стандартный образец СО №2 (рисунок 6) применяют для определения условной чувствительности, мертвой зоны, погрешности глубиномера, угла a ввода луча, ширины основного лепестка диаграммы направленности, импульсного коэффициента преобразования при контроле соединений из малоуглеродистой и низколегированной сталей, а также для определения предельной чувствительности.
Рисунок 6 Стандартный образец СО №2
Стандартный образец СО № 3 (рисунок 7) следует применять для определения точки выхода 0 ультразвукового луча, стрелы преобразователя.
Рисунок 7 Стандартный образец СО №3
Проверку преобразователей с притертой рабочей поверхностью следует проводить на стандартном образце предприятия (СОП) на примере ВСН 012-88, изображенном на рисунке 8.
а) б)
Рисунок 8 Стандартный образец предприятия для настройки ультразвуковых дефектоскопов по ВСН 012-88
а - с угловыми отражателями; б - с цилиндрическими сверлениями
Для контроля стыковых соединений применяют схемы прозвучивания сварного шва прямым (а) и прямым и обратным лучом (б) (Рисунок 9)
а) б)
Рисунок 9 Схемы прозвучивания стыковых соединений
а) - прямым лучом; б) – обратным лучом
Схемы прозвучивания угловых швов тавровых (а,б) и нахлесточных (в) соединения приведены на рисунке 4
а) б) в)
Рисунок 10 Схемы прозвучивания угловых швов
а) – прямым лучом таврового соединения; б) – обратным лучом таврового соединения; в) – нахлесточного соединения обратным лучом.
Порядок выполнения работы
1. Изучить документацию по устройству и обслуживанию дефектоскопов УД2-12 и ЭВУД ПК А;
2. Используя технологические карты настройки дефектоскопа УД2-12 выполнить:
а) - настройку зоны контроля;
б) - настройку измерителя координат и измерение координат искусственных отражателей в стальных образцах;
в) - проверку и настройку уровней срабатывания индикаторов АСД;
г) - настройку режима ВРЧ.
3. Используя техническое описание ЭВУД ПК А4 произвести контроль сварного соединения.
Контрольные вопросы
1. В чем заключается сущность ультразвукового контроля?
3. Какие существуют методы ультразвукового контроля?
4. Какие существуют типы искательных головок?
5. Объясните принцип работы ультразвукового дефектоскопа?
6. В чем состоит техника выполнения ультразвукового контроля?
7. Объясните принцип действия блоков ВРЧ и АСД
8. Какие схемы прозвучивания применяют для контроля стыковых соединений?
9. Какие стандартные образцы применяются для настройки чувствительности ультразвукового дефектоскопа?
Лабораторная работа №3
Дата добавления: 2019-01-14; просмотров: 429; Мы поможем в написании вашей работы! |
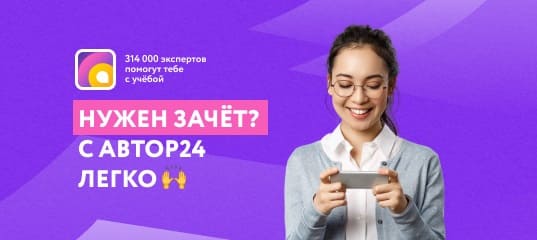
Мы поможем в написании ваших работ!