Расчет величины партий запуска-выпуска
Размер партии деталей – основной календарно-плановый норматив
в серийном производстве. Он определяет все остальные нормативы (периодичность запуска-выпуска, длительность цикла изготовления и т.п.)
и влияет на технико-экономические показатели работы участка.
Расчет минимального размера партии (nmin) основан на экономически рациональном использовании оборудования. Расчет ведется по формуле
где tпз – норма подготовительно-заключительного времени на наиболее трудоемкую операцию, мин;
tш – штучное время на эту операцию, мин;
α– коэффициент, учитывающий допустимые потери времени на переналадку, принимаем α = 0,12.
Минимальный размер партии (для каждой детали) определяется по наиболее загруженной группе оборудования или по самой трудоемкой операции, для которой справедливо соотношение tпзi/tшi = max, данные расчетов приведены в таблице 3.
Таблица 3- Данные расчетов штучно-калькуляционного времени
№ п/п | Наименование и содержание операций | Норма времени, мин. | |||
Подготовительно-заключительного tпз | Штучного, tшт. | Штучно-калькуляционное tштк | tпз / tшт. | ||
1. | Отрезная | 3 | 4 | 7 | 0,75 |
2. | Токарная | 10 | 44 | 54 | 0,23 |
3. | Разметочная | – | 32 | 32 | - |
4. | Фрезерная | 12 | 78 | 90 | 0,15 |
5. | Долбежная | 15 | 18 | 33 | 0,83 |
6. | Слесарная | – | 16 | 16 | - |
7. | Внутришлифовальная | 10 | 10 | 20 | 1 |
8. | Круглошлифовальная | 12 | 9,5 | 21,5 | 1,26 |
Итого: | 62 | 211,5 | 273,5 | 4,22 |
Операцией с наибольшим значением отношения Тпз/Тшт.в данном варианте является операция 040 Круглошлифовальная
|
|
= 0,29
= 62/211,5=0,29
Для нашего варианта:
n min = 9,3 шт., принимаем 9 шт.
Расчет периодичности (ритма запуска-выпуска) партии деталей
Периодичность (ритм запуска) характеризуется отрезком времени между двумя следующими друг за другом запусками партий деталей одного наименования:
где Т n – продолжительность планово-отчетного периода, сут;
nmin – минимальный размер партии деталей, шт.;
N – программа выпуска деталей на данный планово-отчетный период.
Расчёт количества оборудования и коэффициента его загрузки
Потребное количество станков рассчитывается для каждой операции отдельно, исходя из годовой трудоемкости работ участка и действительного годового фонда времени работы единицы оборудования.
Количество оборудования на i-ой операции определяется
следующим образом:
принимаем 1 станок
принимаем 5 станков
принимаем 3 станка
принимаем 8 станков
принимаем 3 станка
принимаем 2 станка
принимаем 2 станка
принимаем 2 станка
где n – количество типоразмеров деталей;
|
|
– годовая программа j-ой детали;
– трудоемкость j-ой детали, мин.;
=
+
.
– коэффициент выполнения норм,
, принимаем
= 1.
– действительный (эффективный)годовой рабочий фонд времени работы
оборудования, час.
Расчетное значение округляется до ближайшего целого числа в меньшую сторону (в большую сторону округление допускается при превышении расчетного значения над принятым не более 5-8 %).
ср1 = 0,61 принимаем спр1 =1
ср2 = 4,74 принимаем спр2 =3
ср3 = 2,8 принимаем спр3 =3
ср4 = 7,9 принимаем спр4 =8
ср5 = 2,9 принимаем спр5 =3
ср6 = 1,4 принимаем спр6 =2
ср7 = 1,75 принимаем спр7 =2
ср8 = 1,93 принимаем спр8 =2
И так далее по всем операциям.
Загрузка оборудования определяется по каждой операции:
Этот коэффициент не должен быть ≥1, т.к. в этом случае имеется «узкое» место, оборудование перегружено, что ставит под угрозу выполнение запланированного объема работ. Для мелкосерийного производства Кзагр = 0,65 -0,75 для среднесерийного производства Кзагр = 0,7-0,9; для крупносерийного и массового производства Кзагр= 08-0,96.Средний коэффициент загрузки оборудования по участку определяется по формуле:
|
|
Результаты расчетов сводятся в таблицу 4.
Таблица 4 – Расчет коэффициента загрузки оборудования
№ | Наименование операции | Оборудование | Расчетное количество | Принятое количество | Коэффициент загрузки |
1. | Отрезная | пила 862 | 0,61 | 1 | 0,61 |
2. | Токарная | 1К62 | 4,74 | 5 | 0,94 |
3. | Разметочная | стол | 2,80 | 3 | 0,93 |
4. | Фрезерная | 6Н12П | 7,90 | 8 | 0,98 |
5. | Долбежная | 7417 | 2,90 | 3 | 0,96 |
6. | Слесарная | верстак | 1,40 | 2 | 0,70 |
7. | Внутришлифовальная | 5822 | 1,75 | 2 | 0,88 |
8. | Круглошлифовальная | 3161 | 1,93 | 2 | 0,97 |
Итого | 24,03 | 26 | 6,97 |
Построение графика загрузки оборудования
На основании данных таблицы 4 строится график загрузки оборудования и составляется таблица 5.
Таблица 5 – Сводная ведомость состава оборудования участка
№ опер. | Тип и модель станка | Принятое количе-ство станков, шт. | Коэффициент загрузки станков | Балансовая стоимость, тыс.руб. | Габаритные размеры станков, мм | |
одного станка | всех станков | |||||
1. 1 | 2. | 3. | 4. | 5. | 6. | 7. |
1 | Отрезная | 1 | 0,61 | 117 | 90 | |||
2 | Токарная | 5 | 0,94 | 1014 | 3900 | |||
3 | Разметочная | 3 | 0,93 | 26 | 60 | |||
4 | Фрезерная | 8 | 0,98 | 1170 | 7200 | |||
5 | Долбежная | 3 | 0,96 | 325 | 750 | |||
6 | Слесарная | 2 | 0,7 | 26 | 40 | |||
7 | Внутришлифовальная | 2 | 0,88 | 1196 | 1840 | |||
8 | Круглошлифовальная | 2 | 0,97 | 1196 | 1840 | |||
Итого:
| 26 | 6,97 | 5070 | 15720 |
Балансовая стоимость одного станка (графа 5) определяется путем умножения стоимости единицы оборудования на коэффициент, учитывающий стоимость затрат на транспортировку и монтаж оборудования (принимаем 1,3)
Ориентировочная стоимость единицы оборудования приведена в таблице 6. ( таблица 6 заполняется по данным Приложения Д).
Таблица 6 – Стоимость единицы оборудования
Дата добавления: 2018-11-24; просмотров: 1368; Мы поможем в написании вашей работы! |
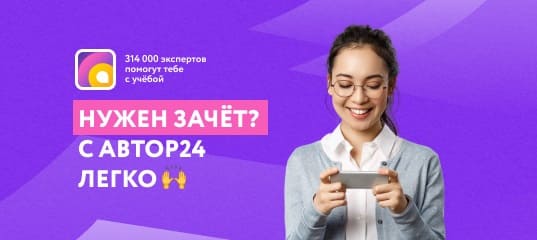
Мы поможем в написании ваших работ!