Глава 2. Требования по охране труда перед началом работы
11. Организация рабочего места должна обеспечивать безопасность выполнения работ.
12. При перемещении грузов на тележках или в контейнерах прилагаемое усилие не должно превышать 10 кг.
13. Тележки, грузовые тележки с подъемными устройствами должны эксплуатироваться в соответствии с требованиями эксплуатационных документов организаций – изготовителей тележек.
14. Грузовые тележки с подъемными устройствами, не прошедшие ежегодное техническое освидетельствование, считаются неисправными, их эксплуатация не допускается.
15. Перед началом работы с применением грузовых тележек работник должен:
надеть средства индивидуальной защиты, соответствующие выполняемой работе;
осмотреть рабочее место, привести его в порядок: убрать посторонние предметы, освободить подходы к нему, очистить их от мусора, в зимнее время – от снега и льда, при необходимости посыпать песком или другими противоскользящими материалами;
устранить наличие на полу влаги, масла и т.п.;
убедиться в исправности тележки, неисправной тележкой пользоваться запрещается.
16. Перед производством работ необходимо проверить:
устойчивость, управляемость тележки, наличие поручней и ручек для удобства их передвижения вручную, а также соответствие виду перевозимых грузов и возможность надежного закрепления и фиксации грузов;
наличие на тележках отчетливо видимых и легко читаемых надписей (табличек) с указанием грузоподъемности, инвентарного номера, наименование структурного подразделения организации;
|
|
наличие предупредительной окраски на выступающих частях тележек, которые могут оказаться опасными при эксплуатации;
наличие стоек, упоров и других устройств, предохраняющих грузы от падения и самопроизвольного смещения на платформе тележки.
17. Тележки-медведки для перемещения бочек должны иметь предохранительные скобы на концах рукояток и иметь приспособления для защиты рук в случае падения или смещения груза с тележки.
18. Работник должен осмотреть грузовую тележку и убедиться в том, что:
колеса вращаются свободно, без заедания, поворотные каретки колес поворачиваются легко, обеспечивая хорошую маневренность тележек;
ручки для передвижения и поручни исправны и надежно закреплены;
подъемные механизмы гидравлических тележек исправны и обеспечивают надежное фиксирование грузовых площадок на необходимой высоте.
19. Рабочий должен осмотреть грузовые тележки с подъемными устройствами на наличие повреждений, утечки рабочей жидкости. Тележки, не прошедшие периодическое техническое освидетельствование, к эксплуатации не допускаются.
20. Работники не должны приступать к выполнению работ при:
|
|
загромождении рабочего места и подходов к нему;
недостаточной освещенности;
неисправностях грузовых тележек, других нарушениях требований по охране труда.
21. Обнаруженные нарушения требований по охране труда должны быть устранены работником до начала работ, при невозможности сделать это работник обязан сообщить о недостатках в обеспечении охраны труда руководителю работ и до их устранения к работе не приступать.
Глава 3. Требования по охране труда при выполнении работы
22. Во время работы работник обязан следить:
за исправностью и надежностью закрепления поручней и колес тележки;
за исправностью, устойчивостью платформ (стеллажей).
23. Укладывать груз на платформы тележек ровными и плотными рядами одинаковой высоты так, чтобы они не выступали за габариты платформы.
24. Во время перемещения тележки держать только за предназначенные для транспортировки поручни или ручки.
25. При перемещении грузов в ящиках и тому подобном для предотвращения ранения рук, выступающие гвозди и концы железобетонной обвязки необходимо загибать.
26. При выполнении работ с использованием инструмента ударного действия для защиты глаз от отлетающих осколков применять защитные очки.
|
|
27. При перевозке грузов не загромождать проходы, проезды.
28. При установке на тележку контейнера необходимо следить за тем, чтобы исключалось ее опрокидывание.
29. При необходимости остановку гидравлической тележки производить опусканием груза. При перемещении груза, уложенного в высокий штабель, привлекать второго работника для поддержания штабеля.
30. При перемещении товаров, грузов на ручной грузовой тележке необходимо:
товары, грузы размещать так, чтобы они не выступали за пределы ее платформы;
не перемещать груз, масса которого превышает установленную грузоподъемность тележки;
не превышать скорость перемещения тележки более 5 км/ч;
при перемещении тележки вниз по наклонному полу находиться позади тележки.
31. При работе с гидравлической вилочной тележкой не допускается:
эксплуатация тележки необученными и посторонними лицами;
оставлять груз в поднятом положении без присмотра;
перевозить на ней людей;
перегружать тележку;
распределять груз по длине вил не равномерно;
нагружать тележку при поднятых вилах;
прикасаться к движущимся частям;
оставлять тележку с поднятыми вилами на неровной поверхности.
|
|
32. При движении тележки необходимо предупреждать людей находящихся в непосредственной близости от места ее эксплуатации об опасности травмирования.
33. При перевозке грузов на тележке необходимо соблюдать следующие требования:
груз на платформе тележки должен размещаться равномерно, занимать устойчивое положение, исключающее его падение при передвижении;
тележка должна нагружаться не более ее грузоподъемности;
борта тележки должны быть закрыты, стойки установлены в гнезда;
работник, сопровождающий тележку, не должен находиться сбоку тележки (чтобы не получить травму при движении тележки в узких местах и воротах, дверных проемах).
34. Не допускается:
нагружать тележки грузом выше уровня глаз транспортирующего тележку. При передвижении тележки груз не должен мешать обзору;
работать с неисправными тележками (не вращается или отсутствует колесо, перекошена платформа и т.п.) и при явных дефектах в покрытии пола (ямы, щели, выступы);
находиться впереди тележки при спуске по наклонной плоскости;
подставлять ноги под колеса для остановки тележки;
открывать двери в проездах ударом об них тележкой;
садиться на тележки во время движения и кататься на них;
поднимать, перемещать груз, превышающий грузоподъемность тележки;
пользоваться неисправными поддонами и тарой.
24. Опишите неразъемные соединения: сварные, паяные и клеевые. Сравнительная характеристика, свойства, применение .
Неразъемными соединениями называются такие, повторная сборка и разборка которых невозможна без повреждения деталей. К ним относятся соединения сварные, паяные, соединения, получаемые склеиванием, соединения заклепками и т.д.
Сварка — это процесс получения неразъемного соединения путем сплавления металлов деталей и сварочного электрода. При сплавлении образуется сварной шов.
Различают термическую, термомеханическую и механическую сварки. Наиболее распространенными видами сварки являются электродуговая, электронно-лучевая, газовая (термические); контактная и термокомпрессионная (термомеханические); трением, холодная и ультразвуковая (механические).
При электродуговой сварке электрической дугой в месте контакта электрода и соединяемых деталей расплавляется металл деталей и электрода и образуется прочный шов (см. рисунок).
При газовой сварке для нагрева и плавления металлов используют теплоту газового пламени при сжигании ацетилена в кислороде. Такую сварку часто применяют для тонкостенных и легко окисляющихся деталей из металлов, обладающих различными температурами плавления, в частности, для сварки деталей из конструкционных сталей толщиной до 2 мм, меди – до 4 мм. Газовая сварка вызывает небольшие деформации и структурные изменения.
Электронно-лучевую (лазерную) сварку производят потоком электронов (частиц света) большой энергии. Этим способом обычно сваривают тугоплавкие и сильно окисляющиеся металлы и сплавы. Сварку производят в вакууме или в атмосфере аргона.
Контактная сварка – самый производительный способ сварки в массовом производстве.
Различают точечную, стыковую и роликовую (шовную) контактные сварки.
При точечной сварке тонкостенные детали соединяют внахлестку. Под действием давления электродов, проводящих ток к месту сварки, образуются точечные сварные соединения. Так как высокие температуры действуют на небольших участках (точках), отсутствует коробление соединяемых деталей. Точечную сварку используют при изготовлении кожухов, панелей, шасси, стоек и других деталей.
При стыковой сварке соединяемые детали сжимают и в зоне контакта при прохождении электрического тока выделяется большое количество теплоты. Стыковой сваркой соединяют детали различных форм и сечений (круг, квадрат, труба, уголок и т.д.).
Шовную сварку осуществляют вращающимися дисковыми электродами. При этом получается непрерывный сварной шов, обеспечивающий герметичное соединение тонкостенных деталей.
Разновидностью контактной сварки является конденсаторная сварка – ток к месту сварки подается в виде короткого импульса при разряде конденсаторов. Контактная сварка позволяет сваривать разнородные материалы, детали малых толщин и сечений (сварка в «шарик» монтажных приводов) и детали различных сечений.
Термокомпрессионная сварка – это сварка под давлением с местным нагревом участка соединения за счет теплопередачи от нагретого электрода.
Применяется для присоединения металлических проводников толщиной в десятки микрон к полупроводниковым кристаллам, к напыленным пленкам, т.е. при монтаже элементов микросхем.
При сварке трением нагрев в месте соединения осуществляется за счет теплоты, выделяемой в месте контакта прижатых друг к другу и вращающихся по отношению друг к другу деталей.
Холодная сварка осуществляется без нагрева соединяемых деталей за счет их сжатия с помощью механических и гидравлических прессов до появления пластических деформаций. Холодной сваркой сваривают металлы с хорошими пластическими свойствами – алюминий и его сплавы, медь и ее некоторые сплавы; никель; олово; серебро; разнородные металлы, например, алюминий и медь.
Для получения прочных и плотных швов необходимо предварительно очистить поверхности контакта от окислов. Прочность соединения при точечной холодной сварке может быть выше, чем при точечной контактной сварке, но при этом значительно хуже внешний вид соединения из-за вмятин и пластической деформации.
Ультразвуковая сварка основана на создании в месте соединения деталей переменных напряжений сдвига с частотой ультразвуковых генераторов, преобразующих колебания электрических величин в механические колебания. Ультразвуковая сварка позволяет сваривать металлы с различными, в том числе неметаллическими покрытиями, пластмассы.
В зависимости от выбранного вида сварки и требований, предъявляемых к соединению, применяют различные виды соединений.
В зависимости от взаимного расположения соединяемых элементов различают следующие виды сварных соединений: стыковые, нахлесточные, угловые и тавровые.
Достоинства сварных соединений:
· невысокая стоимость соединения благодаря малой трудоёмкости сварки и простоте конструкции сварного шва;
· сравнительно небольшая масса конструкции (на 15-25% меньше массы клёпаной):
o из-за отсутствия отверстий под заклёпки требуется меньшая площадь свариваемых деталей;
o соединение деталей может выполняться без накладок;
o отсутствуют выступающие массивные головки заклёпок;
· герметичность и плотность соединения;
· возможность автоматизации процесса сварки;
· возможность сварки толстых профилей.
Недостатки сварных соединений:
· прочность сварного шва зависит от квалификации сварщика (устраняется применением автоматической сварки);
· коробление деталей из-за неравномерности нагрева в процессе сварки;
· недостаточная надёжность при значительных вибрационных и ударных нагрузках.
Сварные соединения (швы) делятся на следующие виды:
· стыковое, обозначаемое буквой С (Рисунок 6.1, а-е);
· угловое, обозначаемое буквой У (Рисунок 6.1, ж);
· тавровое, обозначаемое буквой Т (Рисунок 6.1, з, и);
· нахлесточное, обозначаемое буквой Н (Рисунок 6.1, к, л);
Рисунок 6.1 — Виды сварных швов
Свойство материалов образовывать сварные соединения, отвечающие требованиям конструкции и условиям эксплуатации, оценивается свариваемостью. Из материалов и их сплавов свариваются хорошо, без применения особых методов малоуглеродистые конструкционные и низколегированные стали (Ст0…Ст3, 08…25, 15Х, 15Г и др.), алюминий и его сплавы (Д1, Д16, АМц, АМг3, АЛ2, АЛ4), медь и ее сплавы (М3, ЛС59-1, Л63, БрАЖ9-4, БрОФ10-1, БрОЦ4-3 и др.); свариваются ограниченно только специальными методами или при определенных режимах сварки среднеуглеродистые стали(30 … 45, 30Г, 30ХГС и др.); свариваются плохо высокоуглеродистые и высоколегированные стали65Г, У8, У10, чугуны.
Из неметаллических материалов сварке подвергаются только термопластические пластмассы (полиэтилен, полистирол, полипропилен и др.), при этом кромки деталей разогреваются до пластического вязкотекучего состояния, а затем подвергаются сжатию. В качестве присадочного материала применяют пруток из той же пластмассы, что и свариваемые детали.
Известны следующие способы сварки пластмасс: ультразвуком, токами высокой частоты, трением, газовыми теплоносителями и нагретыми инструментами.
Соединения пайкой
Пайкой называют процесс соединения металлических или металлизированных деталей с помощью дополнительного связующего материала – припоя, температура плавления которого ниже температуры плавления материала соединяемых деталей.
В расплавленном состоянии припой смачивает поверхности соединяемых деталей. Соединение происходит путем межатомного сцепления, растворения и диффузии материала деталей и припоя. В отличие от сварки пайка сохраняет неизменными структуру, механические свойства и состав материала деталей, вызывает значительно меньшие остаточные напряжения. Прочность паяного соединения определяется прочностью припоя и сцепления припоя с поверхностями соединяемых деталей.
В качестве припоя применяют как чистые металлы, так и сплавы. В зависимости от температуры плавления припои бывают легкоплавкие (мягкие) и среднетугоплавкие (твердые). К легкоплавким мягким припоям с температурой плавления до 450 °С относятся оловянисто-свинцовые сплавы с содержанием олова от 18 до 90%, например ПОС-61 (61% олова). Для понижения температуры плавления в эти сплавы вводят висмут и кадмий, а для увеличения прочности – сурьму.
Твердые припои содержат в своем составе медь, цинк, никель, серебро и имеют температуру плавления выше 500 °С.
Мягкие припои применяют для получения главным образом надежных электрических контактов при пайке и герметичных соединений.
Твердые припои обеспечивают достаточную прочность шва при температуре свыше 100 °С, устойчивы к вибрациям, ударам и агрессивным средам.
Хорошее соединение пайкой можно получить только при чистых поверхностях спаиваемых деталей, свободных от окислов и загрязнений и при заполнении зазора между деталями припоем. Для очистки и защиты соединяемых поверхностей и припоя от окисления, улучшения смачиваемости и лучшего растекания припоя применяют флюсы. Они способствуют очищению поверхностей от загрязнений, растворяют окисные пленки, улучшают смачиваемость поверхностей припоем, обеспечивают лучшее затекание припоя в зазоры между спаиваемыми деталями.
Флюсы делятся на химически активные (бура, хлористый цинк и др.) и химически неактивные(канифоль и спиртовые растворы). Применение первых требует тщательной промывки деталей после пайки.
Соединения пайкой могут выполняться при различных способах нагрева деталей и припоя. Наиболее распространенными видами пайки являются пайка паяльником, газовой горелкой, в печи, индукционная, пайка в жидких средах, ультразвуковая, волной припоя, лазером, электронным лучом и другие. Способ нагрева зависит от конструкции соединения, материала соединяемых деталей, требуемого количества теплоты и температуры нагрева.
Качество соединения определяется величиной зазора и плотностью его заполнения припоем, прочностью припоя и прочностью связи припоя с поверхностями соединяемых деталей.
Достоинствами пайки являются простота и дешевизна технологического процесса, широкие возможности его механизации и автоматизации, возможность соединения всех металлов и разнородных материалов (металл с керамикой, стеклом, резиной), малые остаточные температурные напряжения и деформации, малое электросопротивление мест соединения.
Так как непосредственная пайка при соединении металлов с неметаллами невозможна, то на поверхности неметаллических материалов создают промежуточный слой из меди, никеля, серебра, который хорошо сцепляется с поверхностью этих материалов и обеспечивает качественную пайку с металлом.
Недостатком соединений пайкой является их невысокая механическая и термическая прочность.
Различают паяные соединения внахлестку и встык. Наибольшую прочность имеет соединение внахлестку, но при этом увеличиваются габариты соединения. Соединение встык имеет малые габариты, но невысокую прочность.
Склеивание.
Одним из старейших способов получения неразъемных соединений является склеивание, т. е. соединение с помощью клея. В последнее время он получает все большее распространение благодаря совершенствованию качеств клеев. Клей представляет собой вязкое вещество, обладающее склеивающей способностью. Клеевые соединения обеспечивают высокую прочность, позволяют соединять тонкие детали. Склеивать можно как металлы, так и неметаллы.
Клеи подразделяются на белковые, или растительные (крахмал, декстрин, резиновый), и животные (костяной, казеиновый, мездровый, или столярный).
В машиностроении используются клеи различных видов. Эпоксидный клей, состоящий из эпоксидной смолы, наполнителя и отвердителя, служит для склеивания однородных и разнородных материалов. Фенольные клеи БФ-2, БФ-4 применяют для склеивания металлов, пластмасс и некоторых других материалов, БФ-6 — для склеивания текстильных материалов. В соединениях деталей, которые не подвергаются ударным нагрузкам, применяют карбинольный клей (смесь карбинола и перекиси бензоила).
К основным характеристикам клеевых соединений относят: предел прочности при сдвиге, равномерном и неравномерном отрыве; предел выносливости при сдвиге, изгибе и длительную прочность при постоянной статической нагрузке; стойкость к нагреву, охлаждению, воздействию влаги и различных сред (масел, топлива и т.п.).
К преимуществам клеевых соединений следует отнести: возможность соединения разнородных материалов; равномерность распределения напряжений в соединении (повышается сопротивление вибрациям); уменьшение объема механической обработки (отпадает надобность сверления отверстий для крепежа); герметичность и коррозионную стойкость соединения; в ряде случаев уменьшение массы и себестоимости изготовления изделия.
Недостатками клеевых соединений являются: низкая прочность на отрыв; «старение» некоторых клеев с течением времени, меньшая долговечность по сравнению со сварными и клепаными соединениями, длительный срок полимеризации (у ряда клеев) и незначительная тепловая стойкость.
Существует большое разнообразие марок клеев. Их делят на две группы: конструкционные (жесткие) и неконструкционные (эластичные). Конструкционные клеи обеспечивают высокую прочность (на сдвиг до 50…55 МПа, на отдир до 2,5…2,7 МПа). Неконструкционные клеи менее прочны (на сдвиг до 5 МПа, на отдир до 0,7 МПа), но более дешевы. Кроме того, клеи подразделяют на жидкие, пастообразные, пленочные и порошкообразные.
Для правильного выбора клея при проектировании определенного изделия необходимо учитывать условия эксплуатации клеевого соединения, физико-механические и технологические свойства клея.
Большое значение для обеспечения прочности имеет толщина клеевой прослойки, причем увеличение слоя клея снижает прочность соединения. Оптимальные толщины лежат в пределах 0,10…0,15 мм. Не менее важна равномерность толщины клеевого слоя, обусловленная точностью взаимного расположения сопрягаемых поверхностей.
Качество клеевого соединения зависит также от подготовки поверхностей деталей под склеивание. Оптимальные физико-механические свойства поверхностей обеспечивают различными способами физико-механической (дробеструйная, ультразвуковая, газопламенная) и химической (обезжиривание, травление, фосфотирование) обработки. Клей в зависимости от его консистенции наносят кистью, пульверизатором, шпателем, роликом или шприцем.
25. Опишите назначение натяжных устройств, применяемых в механических передачах и конвейерах.
Натяжное устройство любого типа состоит из поворотного устройства 1, которое огибает тяговый элемент 2, подвижных башмаков или тележки 4 (на которых закрепляется ось 3 поворотного устройства) и натяжного механизма 5, который перемещая ползуны или тележку натягивает тяговый элемент. Поворотное устройство может состоять из барабана (для ленты), одного или двух блоков (для каната) или звездочек (для цепей). В конвейерах с тяговым элементом установка натяжного устройства обязательна.
Натяжные устройства служат для создания первоначального (минимального) натяжения тягового элемента, необходимого для обеспечения тяговой способности фрикционного привода, ограничения стрелы провисания ленты между ролико-опорами и компенсации ее вытяжки под нагрузкой в процессе ее эксплуатации, а также уменьшения динамических процессов, особенно у цепных конвейеров.
а — винтовое; б — пружинно-винтовое; в — грузовое тележечное; г — пневматическое (гидравлическое); д - грузовое вертикальное; е - лебедочное
Рисунок - Схемы натяжных устройств
Первоначальное натяжение должно обеспечивать определенное минимальное натяжение тягового органа, необходимое для нормальной работы конвейера. Минимальное натяжение различно и зависит от типа конвейера и его привода. Например, для скребковых и подвесных толкающих конвейеров натяжение должно обеспечивать устойчивое положение скребка или толкателя; у конвейеров с фрикционным приводом первоначальное натяжение ветви должно быть значительным для создания достаточной силы трения между барабаном и лентой для передачи потребного тягового усилия; у конвейеров с передачей тягового усилия зацеплением, первоначальное натяжение цепи необходимо для обеспечения правильного схода цепи с приводной звездочки, оно обычно составляет 5-10% от Smax.
По конструкции и способу действия натяжные устройства делятся на механические, грузовые, гидравлические, пневматические и комбинированные (грузо-лебедочные).
К механическим натяжным устройствам относятся винтовые, пружинно-винтовые и лебедочные. В механических устройствах натяжение производится вручную или при помощи лебедки, приводимой электро- или гидроприводом. Здесь натяжение не остается постоянным, уменьшается в процессе работы из-за вытяжки тягового элемента, требуется периодическая подтяжка - это недостатки механических натяжных устройств.
Преимущества - простота конструкции, малые габаритные размеры, компактность, небольшой вес и большая сила натяжения. Применяются на горизонтальных и наклонных цепных и ленточных (длинной до 60 м) конвейерах с простой конфигурации трассы.
На тяжелых и длинных цепных конвейерах устанавливаются, как правило, пружинно-винтовые натяжные устройства.
Лебедочные приводятся в действие электро- или гидродвигателем, обеспечивая большую силу натяжения и большой ход.
На мощных ленточных конвейерах большой протяженности (500 и более метров) устанавливают комбинированные (грузолебедочные и лебедочно-пружинные) натяжные устройства. Натяжное усилие 100... 150 кН.
Гидравлические и пневматические натяжные устройства имеют малые габаритные размеры, но требуют специального приспособления, обеспечивающего постоянство давления воздуха или масла.
Грузовые натяжные устройства бывают вертикального и горизонтального исполнения на тележках и рамные, приводятся в действие свободно висячим грузом, автоматически обеспечивая постоянное натяжение тягового элемента, компенсируют его удлинение в том числе и от температуры и уменьшают пиковые нагрузки при случайных перегрузках, что является их большим преимуществом.
К недостаткам грузовых натяжных устройств относятся большие габаритные размеры, неудобство применения в передвижных машинах из-за большой массы груза, особенно в мощных и длинных ленточных конвейерах. Для уменьшения массы груза применяют передачу усилия натяжение через полиспасты и рычаги, используют приводные лебедки. Существенным недостатком таких натяжных устройств являются большие сопротивления в полиспастах, которые препятствуют автоматичности действия грузовых натяжных устройств. Грузовые натяжные устройства устанавливают на ленточных (длинной 60-500 м), канатных и пространственных подвесных и цепетянущих конвейерах.
По расположению на трассе конвейера, грузовые натяжные устройства бывают размещенные в хвостовой его части и промежуточные. При расположении грузового натяжного устройства в хвостовой части, из-за динамических нагрузок, натяжение холостой ветви может быть ниже допустимого [Smin].
При размещении грузового натяжного устройства около приводной звездочки динамические нагрузки, возникающие в тяговом элементе при пуске конвейера, не снижают натяжения в холостой ветви ниже Smin, т.к. в этом случае Smin определяется массой натяжного груза, расположенного непосредственно в зоне действия Smin. Поэтому грузовое натяжное устройство цепных конвейеров целесообразно располагать вблизи привода. Кроме того, такое размещение обеспечивает постоянство натяжения тягового элемента.
26. Опишите двухпозиционные переключатели, которые используются для изменения направления муки при перемещении ее сжатым воздухом. Поясните устройство и принцип действия.
Внутрипроизводственное транспортирование муки и других сыпучих компонентов может осуществляться пневматическим, механическим или смешанным транспортом.
Все системы пневмотранспорта можно условно свести к трем видам: низкого, среднего и высокого давления. Пневмотранспорт высокого и среднего давления (более 0,15 мПа) принято называть аэрозольтранспортом. Пневмотранспорт представляет возможность доставки муки практически в любую точку предприятия, сокращает распыл сырья и соответственно потери. Применение пневмотранспорта предпочтительно с точки зрения биотехнологии, поскольку известен эффект ускоренного созревания муки и улучшение её хлебопекарных свойств, когда она находится во взвешенном состоянии в среде нагретого воздуха.
Для изменения направления движущегося потока аэросмеси в мукопроводах предназначены переключатели: двухпозиционные, например, Ш2-ХМБ, многопозиционные М-130 и др. Очистка аэрозольной смеси от транспортирующего воздуха осуществляется с помощью самовстряхивающихся фильтров ХЕ-161 для складских бункеров и силосов, ХЕ-162 для производственных бункеров и фильтр-разгрузитель М-104 для просеивателя.
Дата добавления: 2018-11-24; просмотров: 437; Мы поможем в написании вашей работы! |
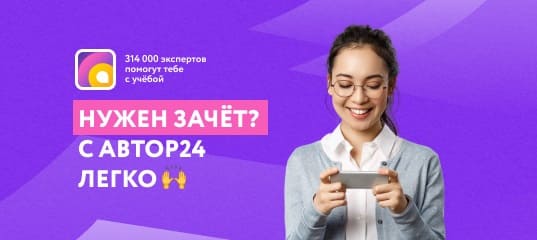
Мы поможем в написании ваших работ!