Кровельные и гидроизоляционные битумные материалы
Основная задача, решаемая с помощью как кровельных, так и гидроизоляционных материалов, – создание водонепроницаемого покрытия, защищающего изолируемую конструкцию и здание в целом от воздействия влаги. Однако условия, в которых работают кровельные материалы, существенно отличаются от условий, в которых работают гидроизоляционные материалы.
Кровельные материалы подвергаются периодическому увлажнению и высушиванию, воздействию прямого солнечного излучения (особенно опасно действие его УФ-составляющей), нагреву, замораживанию, снеговым и ветровым нагрузкам.
Чтобы длительно и успешно работать в таких условиях, кровельные материалы должны быть атмосферостойкими, светостойкими, водо- и морозостойкими и достаточно прочными. В тех же случаях, когда крыша является видимым элементом сооружения (мансардные, двухскатные, вальмовые и т.п. кровли), материал должен отвечать и определенным архитектурно-декоративным требованиям. И, наконец, технологичность и экономичность – общее требование ко всем кровельным материалам.
Гидроизоляционные материалы, в отличие от кровельных, работают в условиях постоянного воздействия влаги или агрессивных водных растворов (часто под давлением). Температурные условия работы гидроизоляционных материалов более стабильны, солнечное облучение отсутствует, но возможно развитие гнилостных процессов.
От гидроизоляционных материалов требуются полная водонепроницаемость, долговечность, базирующаяся на гнилостойкости и коррозионной стойкости, и свойства, обеспечивающие сохранение сплошности материала при различных внешних механических воздействиях. Технологичность и экономичность остаются также непременными требованиями.
|
|
Для получения кровельных и гидроизоляционных материалов и изделий используют разнообразные материалы: природный камень, металлы, керамику, асбестоцемент, полимеры, но самые распространенные кровельные и гидроизоляционные рулонные материалы получают на основе битума и синтетических полимеров.
Материалы на основе битумных, битумно-полимерных и полимерных связующих – главнейший вид кровельных материалов. К ним относятся самые разные по форме, размерам и физическому состоянию материалы:
мембранные – большеразмерные полотнища (площадью до 500 м2);
рулонные – полотнища шириной около 1 метра и длиной 7…20 м, поставляемые на строительную площадку в рулонах;
штучные и листовые – мелкоразмерные полосы и листы;
мастичные – вязкие жидкости, образующие водонепроницаемую пленку после нанесения на изолируемую конструкцию.
Выбор того или иного типа материала зависит от многих факторов:
|
|
конструктивных (угол наклона крыши, материал основания и др.);
технологических (простота устройства покрытия);
архитектурно-декоративных (желаемый цвет и фактура поверхности);
экономичность (стоимость и долговечность).
Рулонные кровельные материалы находят наибольшее применение. Площадь кровель, выполненных из рулонных материалов, составляет почти половину от общей площади кровель в России. Объясняется это, с одной стороны, невысокой стоимостью самих материалов и простотой устройства кровельного покрытия, а с другой стороны – тем, что рулонные материалы – наиболее удобный вид кровельного материала для плоских, в особенности с уклоном вовнутрь, кровель, характерных для типовых многоэтажных панельных, монолитных и кирпичных зданий. Популярны рулонные материалы и для индивидуального строительства в сельских районах. Качество рулонных кровельных и гидроизоляционных материалов регулирует ГОСТ 30547–97 «Материалы рулонные кровельные и гидроизоляционные. Общие технические условия». Методика определения этих показателей регламентирована ГОСТ 2678-94 «Материалы рулонные кровельные и гидроизоляционные. Методы испытаний».
|
|
Первые рулонные материалы, появившиеся в конце XIX века, это толь, пергамин и рубероид. В основе этих материалов лежит кровельный картон, пропитанный черными вяжущими (битумом или дегтем).
Кровельный картон получают из вторичного текстиля, макулатуры и древесного сырья. Картон имеет рыхлую структуру и хорошо впитывает влагу и другие жидкости (в частности, расплавленный битум). При увлажнении, под действием солнечного излучения и в результате гниения картон теряет свои свойства. Пропитка битумом замедляет эти процессы.
Марка картона устанавливается по его поверхностной плотности (масса 1 м2 картона в г); она может быть от 300 до 500. Ширина кровельного картона – 1000, 1025 и 1050 мм.
Толь – картон, пропитанный и покрытый с двух сторон дегтем, в настоящее время практически не применяется.
Пергамин – простейший рулонный материал, получаемый пропиткой кровельного картона расплавленным легкоплавким битумом (например, БНК 45/180). Применяют пергамин для устройства нижних слоев кровельного ковра и для устройства пароизоляционных прокладок в строительных конструкциях. Марки пергамина П-300, П-350 и т.п. (П – пергамин, 300 – марка картона).
Рубероид – многослойный материал, получаемый, как и пергамин, пропиткой кровельного картона легкоплавким битумом и последующего нанесения с обеих сторон слоя тугоплавкого битума, наполненного минеральным порошком. Лицевая сторона рубероида покрывается «бронирующей» посыпкой (песком, слюдой, сланцевой мелочью и т.п.), защищающей материал от УФ-излучения; нижняя сторона – порошком из известняка или талька для защиты от слипания слоев в рулоне. Длина рулона 10…20 м.
|
|
Марки рубероида – РКК-420; РКЧ-350 и т.п. (Р – рубероид; К – кровельный; К и Ч – вид посыпки, соответственно крупнозернистая или чешуйчатая). Для нижних слоев кровельного ковра выпускается рубероид подкладочный с пылеватой посыпкой (П) с обеих сторон (например, РПП-300).
Качество рулонных кровельных материалов оценивается в соответствии со стандартом комплексом показателей:
прочностью, характеризуемой силой, необходимой для разрыва образца материала шириной 5 см, Н;
деформативностью, характеризуемой относительным удлинением материала при разрыве, %;
гибкостью на холоде, характеризуемой минимальной температурой, при которой образец материала не трескается при загибе его вокруг бруса радиусом 25 мм (для материалов с основой) и 5 мм (для безосновных), оС;
теплостойкостью, характеризуемой максимальной температурой, при которой у вертикально подвешенного образца не наблюдается стекания покровной массы, оС;
водопоглощением, %;
водонепроницаемостью, характеризуемой временем, в течение которого образец не пропускает воду при определенном давлении.
Таблица 9.2
Технические характеристики рубероида различных марок
Показатели | Марка рубероида | ||
РКК–400 | РКК–350 | РПП–300 | |
Разрывная сила при растяжении, Н, не менее | 340 | 320 | 220 |
Теплостойкость, °С, не менее | 80 | 80 | 80 |
Гибкость на брусе R = 15 мм, °С, не выше | +5 | +5 | +5 |
Водонепроницаемость при давлении 0,001 МПа в течение, ч | 72 | 72 | 72 |
Кровля из рубероида и пергамина многодельна, так как представляет собой многослойный (3…5 слоев) кровельный ковер. Из-за хрупкости битумного связующего на холоде устройство кровли из рубероида невозможно в зимний период.
Помимо этого, кровли из обычного пергамина и рубероида имеют невысокую долговечность – 5…6 лет. Последнее объясняется низкими значениями прочности и водо- и биостойкостью картонной основы, а также узким интервалом рабочих температур битумного вяжущего: на холоде (около 0оС) он становится хрупким, а при нагреве до 60…80оС размягчается и течет. Кроме того, и битум, и картонная основа быстро стареют под действием солнечного излучения и кислорода воздуха.
Через несколько лет эксплуатации на крыше рубероид становится жестким; кровельный ковер при небольших деформациях (температурных, усадочных и т.п.) трескается и кровля начинает протекать.
Современные рулонные материалы прошли длинный путь совершенствования свойств и мало напоминают традиционный рубероид.
Первым этапом модификации рубероида было упрощение технологии устройства кровельного ковра благодаря внедрению наплавляемого рубероида. Он отличается более толстым слоем битума на нижней стороне материала, где в соответствии со стандартом слой битума должен быть не менее 1500 г/м2. Кровельный ковер из наплавляемого рубероида получают путем подплавления нижней поверхности рубероида газовой горелкой с последующей его прикаткой.
Следующим шагом была замена непрочной и подверженной гниению картонной основы на более прочную и гнилостойкую. Были опробованы асбестокартон и основы на базе стекловолокна и синтетического волокна «полиэстер» в виде тканей, холста и нетканого полотна. В настоящее время предпочтение отдают нетканым основам из полиэстера и стеклохолсту. Стекловолокнистые основы отличаются малым удлинением при разрыве (1,5…3%), у синтетических – оно выше (35…40%).
Производят материалы на основе алюминиевой и медной фольги (например, фольгоизол). Фольга, находящаяся на лицевой стороне материала, придает ему декоративные свойства и защищает от солнечного излучения.
Применение новых прочных и долговечных основ, в свою очередь, потребовало модификации битумного связующего в сторону повышения его долговечности и расширения диапазона рабочих температур. Эта задача была решена путем модификации битума полимерами. Полимерные добавки позволяют расширить интервал рабочих температур битума (снижая температуру хрупкости и повышая температуру размягчения) и обеспечивают сохранение эластичности вяжущего длительное время (то есть повышают долговечность материала). В настоящее время для модификации битума используют, в основном, термоэластопласты, в частности, атактический полипропилен (АПП) – побочный продукт при производстве полипропилена, по внешнему виду и свойствам напоминающий невулканизированный каучук, и синтетические каучуки, например, стирол-бутадиен-стирольный (СБС).
Битумы, модифицированные АПП по сравнению с обычным окисленным битумом, характеризуются высокой теплостойкостью, хорошей гибкостью на холоде (до минус 20оС) и высокой устойчивостью к атмосферным воздействиям. Битумы, модифицированные СБС, характеризуются еще более высокой гибкостью на холоде (до минус 30оС), но они более чувствительны к УФ-облучению, в связи с чем требуют эффективной защиты от солнечного света. Материалы на основе битумов, модифицированных полимерами, имеют расширенный диапазон эксплуатационных температур, повышенную долговечность и позволяют производить работы по устройству кровли из рулонных материалов при отрицательных температурах, то есть практически круглый год.
У современных рулонных битумно-полимерных материалов для защиты от солнечного излучения используют бронирующие посыпки из цветной минеральной (сланцевой, керамической) или полимерной крошки. Такие посыпки более надежны, чем традиционные и придают повышенную декоративность материалу.
Промышленность выпускает большое количество рулонных кровельных материалов на различных основах и с различными модификаторами, при этом каждое предприятие дает свое собственное фирменное название материалу. Однако, все эти материалы в принципе имеют одно и то же строение: многослойный композиционный материал на прочной негниющей основе, на которую с обеих сторон нанесен толстый слой битумно-полимерного или битумного связующего с декоративной посыпкой на лицевой стороне и пленочной защитой от слипания на нижней. Толщина современных рулонных материалов 3…5 мм, что позволяет делать кровельный ковер двухслойным (а не 3…5 слоев) и укладывать его методом наплавления.
Гидроизоляционные материалы предназначены для предохранения строительных конструкций от контакта с водой, поглощения воды или фильтрации воды через них. Влага, контактирующая с материалом и проникающая в него, может пагубно влиять на эксплуатационные показатели материала (прочность, теплоизолирующую способность) или вызывать коррозию материала вплоть до его полного разрушения. В зависимости от физического состояния и соответственно технологии их применения гидроизоляционные материалы можно разделить на жидкие (пропиточные и пленкообразующие), пастообразные пластично-вязкие (мастики) и твердые упруго-пластичные (рулонные). Наиболее востребованы материалы из последней группы.
Упруго-пластичные гидроизоляционные материалы представлены рулонными материалами (безосновными и на различных основах) аналогичны кровельным. Как уже говорилось, в отличие от кровельных, гидроизоляционные материалы не подвергаются солнечному излучению, но постоянно находятся во влажных условиях, где на первое место выходит гнилостойкость.
В современных рулонных гидроизоляционных материалах для повышения долговечности и надежности используют битумные и полимербитумные материалы на негниющих основах.
Гидростеклоизол – битумный гидроизоляционный материал, состоящий из стекловолокнистой основы, на которую с двух сторон нанесен слой битумного вяжущего, состоящего из битума, минерального наполнителя (20 % от массы вяжущего) и пластификатора. Масса битумного вяжущего 3000±300 г/м2. Материал укрепляется на изолируемой поверхности путем оплавления пламенем горелки. Рекомендуемая температура работ при укладке – не ниже 10°С.
Значительно эффективнее битумно-полимерные материалы, имеющие основу из полиэфирного волокна. Эти материалы могут эксплуатироваться в интервале температур от –25°С до +100°С; относительное удлинение при разрыве 35…40%. Материалы обеспечивают водонепроницаемость при давлении 0,2 МПа, применяются для гидроизоляции тоннелей метрополитена, пролетных строений мостов и путепроводов, подвалов, бассейнов и т.п.
Общие сведения
Полимерныминазывают материалы, основными компонентами которых являются полимеры. Другое их название — пластмассы (пластические массы). Это название они получили благодаря способности в процессе переработки принимать требуемую форму и сохранять ее после снятия действующих усилий.
Полимеры (от греч. poli — много, meros — доля, часть) высокомолекулярные соединения, молекулы которых (макромолекулы) состоят из многократно повторяющихся звеньев — одинаковых групп атомов. К высокомолекулярным соединениям относят вещества с молекулярной массой выше 5000. Молекулярная масса низкомолекулярных соединений обычно не превышает 500. Вещества, имеющие промежуточное значение молекулярной массы, называют олигомерами. Большинство полимеров имеют молекулярную массу от 8000…10000 до нескольких миллионов.
По происхождению полимеры подразделяются на природные и искусственные (синтетические). Природные высокомолекулярные соединения: целлюлоза, белки, нуклеиновые кислоты, полисахариды, натуральный каучук, крахмал, янтарь и др.
Для производства строительных материалов применяют синтетические полимеры. Сырьем для их производства являются природные газы, попутные нефтяные газы, газы нефтепереработки, продукты углепереработки, а также продукты переработки других видов твердого топлива (торфа, древесных и растительных материалов и их отходов).
Исходные низкомолекулярные вещества, из которых синтезируют полимеры, называют мономерами. Например, мономером для получения полиэтилена является газ этилен СН2=СН2. Структурной единицей (повторяющимся элементарным звеном) полиэтилена служит бирадикал (двойной радикал) —СН2—СН2—.
Формула полиэтилена имеет вид
[—СН2—СН2—]n,
где n — степень полимеризации (может достигать 70 тыс. и более).
Полимеры могут иметь линейное, разветвленное и пространственное (сетчатое) строение. Если каждое элементарное звено обозначить А, то макромолекула линейного строения будет иметь следующий вид:
…—А—А—А—А—А—…
Макромолекулы разветвленных полимеров имеют боковые сравнительно короткие ответвления. В полимерах пространственного(трехмерного) строения длинные линейные цепи связаны друг с другом в единую сетку более короткими поперечными цепями.
Полимеры, имеющие линейное или разветвленное строение молекул(полиэтилен, поливинилхлорид, полистирол и др.), обладают способностью многократно при нагревании размягчаться, а при охлаждении отвердевать при сохранении основных свойств. Это термопластичные полимеры (термопласты).
Пространственные полимеры (фенолоформальдегидные, карбамидные, полиэфирные и др.) не могут обратимо изменять свои свойства и, будучи отвержденными, при последующем нагревании превращаются в неплавкие и нерастворимые продукты, не способные к повторному формованию. Это связано с разрывом связей между цепями и внутри цепей. Такие полимеры называются термореактивными (реактопласты). Можно сказать, что при нагревании до высоких температур они ведут себя подобно древесине, претерпевают деструкцию (разрушение) и загораются.
Синтетические полимеры получают посредством реакций полимеризации и поликонденсации. Полимеризации подвергаются мономеры, в молекулах которых содержатся кратные двойные связи (или циклические группировки). За счет раскрытия этих связей (или за счет раскрытия цикла) у молекул исходного вещества образуются свободные валентности, которыми они соединяются между собой в макромолекулы. При этом не выделяется побочных продуктов и химический состав полимера и мономера одинаков. Полимеризацией получают полимеры линейного и разветвленного строения.
При поликонденсации макромолекулы образуются в результате химического взаимодействия между функциональными группами, находящимися в молекулах исходных веществ. Это взаимодействие сопровождается выделением побочных продуктов: воды, хлористого водорода, аммиака и других низкомолекулярных веществ. В связи с этим химический состав полимера отличается от состава исходных компонентов. Поликонденсацией получают полимеры пространственного строения.
Полимеры в пластмассах выполняют роль связующего вещества.
Связующие вещества
Связующие вещества
Выбор связующего вещества в значительной мере определяет технические свойства изделий из пластмасс: их теплостойкость, способность сопротивляться воздействию растворов кислот, щелочей и других агрессивных веществ, а также характеристики прочности и деформативности. Связующее вещество — это обычно самый дорогой компонент пластмассы.
Термопластичные полимеры. Свойства термопластичных (полимеризационных) полимеров обусловлены линейным строением их молекул. При нагревании ослабевает взаимодействие между молекулами и полимер размягчается, вплоть до состояния вязкой жидкости. На этом основано формование изделий из этих полимеров, а также их сварка.
Способность термопластичных полимеров набухать и растворяться в некоторых растворителях также объясняется линейным строением молекул. Растворы полимеров даже малой концентрации (2…5%) отличаются высокой вязкостью, что связано с большими размерами макромолекул полимеров по сравнению с молекулами низкомолекулярных веществ. После испарения растворителя полимер вновь отвердевает. На этом основано применение растворов термопластов в качестве клеев и вяжущих в мастиках и строительных растворах.
Полиэтилен — один из наиболее распространенных полимеров, представляющий собой прозрачное роговидное вещество, жирное на ощупь. Плотность его колеблется в пределах от 910 до 970 кг/м3. При нагревании до температуры 85…90°С он размягчается, а при температуре 105…130°С — плавится. При поджигании полиэтилен горит с характерным запахом парафина; практически нерастворим ни в одном из растворителей при комнатной температуре; стоек по отношению к кислотам, щелочам, солям; водостоек; прочность при растяжении — 20…40 МПа; эластичность сохраняется до температуры -70°С.
К недостаткам полиэтилена относятся низкие теплостойкость и твердость, горючесть, слабая адгезия к минеральным материалам, клеям, склонность к старению под действием солнечного света, поражаемость грызунами.
Полипропилен [—СН2—СН(СН3)—]n по свойствам близок к полиэтилену, но превосходит его по теплостойкости (температура перехода в жидкое состояние 170°С) и механическим свойствам.
Полиэтилен и полипропилен применяют для изготовления труб, пленок, листов, пенопластов, погонажных, санитарно-технических и других изделий. Изделия из этих полимеров хорошо свариваются и подвергаются механической обработке.
Полистирол [—СН2—СН(С6Н5)]n — прозрачный жесткий полимер, при комнатной температуре хрупкий. Плотность его 1050…1080 кг/м3, температура размягчения — 80…100°С. Полистирол растворяется в органических растворителях (бензоле, толуоле, сложных эфирах и т.д.). Он хорошо окрашивается и легко перерабатывается в изделия. Полистирол и его растворы горят, давая яркое коптящее пламя и выделяя сладковатый, цветочный запах мономера. Используют его для изготовления пенопластов, облицовочных плиток и других изделий. Раствор полистирола используется в качестве клея.
Поливинилхлорид [—СН2—СНСl—]n — один из самых распространенных полимеров, используемых в строительстве. Он прозрачный, жесткий и прочный. Переходит в вязкотекучее состояние при температуре 180…200°С. Горит, но при удалении из пламени гаснет. При разложении поливинилхлорида выделяется хлористый водород. Пластические массы на основе поливинилхлорида выпускают в виде жестких материалов, не содержащих пластификатора (винипласт), и мягких, содержащих пластификаторы (пластикат); хорошо перерабатывается в различные изделия (линолеум, пленки, трубы, облицовочные материалы). Поливинилхлорид применяется также для получения кровельных материалов, оконных и дверных блоков.
Продукт на основе поливинилхлорида с содержанием хлора до 60…80% называется перхлорвинил. Он легко растворяется в органических растворителях и применяется для изготовления красок.
Поливинилацетат [—СН2—СН(СН3СОО)—]n — прозрачный, бесцветный, при комнатной температуре жесткий полимер. Плотность его 1 190 кг/м3; при нагревании до температуры 130…150°С разлагается с выделением уксусной кислоты; растворяется в некоторых органических растворителях, набухает в воде; не устойчив к действию кислот и щелочей; горюч. Положительное свойство поливинилацетата — высокая адгезия к камню, древесине, стеклу. Поливинилацетат широко применяется в производстве лаков, красок, клеев. В виде водной дисперсии его применяют также для полимерцементных бетонов и растворов, в производстве влагостойких обоев.
Поливинилацетатная дисперсия (ПВАД) — сметанообразная масса белого или светло-кремового цвета, хорошо смешивающаяся с водой. Для стабилизации этой дисперсии (мельчайшие частицы поливинилацетата в воде) служит поливиниловый спирт. Основной вид ПВАД, применяемый в строительстве, — дисперсия поливинилацетатная гомополимерная грубодисперсная. Содержание полимера в ней — около 50%; размер частиц дисперсии — 3 мкм. ПВАД выпускается средней (С), низкой (Н) и высокой (В) вязкости в непластифицированном и пластифицированном (индекс Ф) виде. В качестве пластификатора применяется дибутилфталат. ПВАД разбавляется водой в любом соотношении и хорошо совмещается с цементом и гипсом.
Полиакрилаты — полимеры производных акриловой и метакриловой кислот. В строительстве наибольшее применение находит полимер метакриловой кислоты.
Полиметилметакрилат [—СН2—С(СН3)—СООСН3—]n — известен под названием «органическое стекло». Это прозрачный полимер аморфной структуры, пропускающий свыше 99% солнечного света, в том числе ультрафиолетовые лучи, что выгодно отличает его от обычного силикатного стекла. Другими его преимуществами перед обычным стеклом являются меньшая хрупкость и хорошая обрабатываемость. Плотность его 1180 кг/м3, предел прочности при изгибе — 80…140 МПа. Применяется для остекления зданий, особенно теплиц, оранжерей, плавательных бассейнов, для устройства светопрозрачных ограждений, изготовления труб, в производстве моющихся обоев и в виде эмульсий для красок, лаков, грунтовок.
Полиизобутилен [—СН2—С(СН3)2—]n — мягкий, эластичный, каучукоподобный полимер, но в отличие от каучуков не способен вулканизироваться (превращаться в резину). По химической стойкости и прочности уступает полиэтилену и полипропилену, но превосходит их по эластичности и степени адгезии к бетону и другим материалам. Из полиизобутилена изготовляют герметизирующие мастики, клеи, пленки.
Термореактивные полимеры. Термореактивные (поликонденсационные) полимерные связующие обычно представляют собой вязкие жидкости или высококонцентрированные водные растворы. Не совсем верно их называют смолами. Как правило, это олигомеры, которые в процессе отверждения переходят в высокомолекулярное состояние. В отвержденном виде они превосходят термопластичные полимеры по прочности и теплостойкости.
Фенолоальдегидные полимеры получают путем ступенчатой поликонденсации фенолов с альдегидами. Наиболее распространены фенолоформальдегидные смолы. Формальдегид (СН2О) является простейшим представителем альдегидов. Фенол (С6Н5ОН) — простейший представитель ароматических углеводородов, в молекуле которых имеются гидроксильные группы, связанные с ароматическим кольцом. В зависимости от соотношения фенола и формальдегида получают либо термопластичные (новолачные), либо термореактивные (резольные) полимеры. Для производства строительных материалов более широко применяются резольные олигомеры и полимеры, выпускаемые как в жидком, так и в твердом состоянии. Применяют их в качестве связующего для производства слоистых пластиков, клеев, газонаполненных пластмасс, минераловатных изделий, древесно-стружечных плит, в полимерных бетонах и растворах и т.д.
Аминоальдегидные полимеры получают путем поликонденсации аминов с альдегидами. Амины — производные аммиака NH3, образованные замещением одного или нескольких водородных атомов углеводородными радикалами. Для производства строительных материалов применяют в основном карбамидо- и меламиноформальдегидные полимеры. Их изготавливают в виде водных растворов или эмульсий. Область применения аминоальдегидных полимеров примерно такая же, как у фенолоформальдегидных.
Карбамидоформальдегидные (карбамидные) смолы — олигомерные продукты конденсации мочевины (карбамида) с формальдегидом (другое название — мочевиноформальдегидные). Это наиболее дешевый и доступный вид синтетических смол. Они обладают невысокой прочностью и водостойкостью; содержат 30…40% свободной воды, связывание которой является необходимым условием получения прочного материала. Связывание воды осуществляется введением дополнительных вяжущих — гипса, фосфогипса и других веществ, химически связывающих воду, или цеолитов, впитывающих ее.
Эпоксидные смолы — олигомерные продукты различного состава, содержащие эпоксидные группы. Это вязкие жидкости или твердообразные вещества, растворимые в органических растворителях (реже - в воде) и плавящиеся при нагревании. Они прозрачны, цвет — от светло-желтого до коричневого. Перевод их в нерастворимое и неплавкое состояние достигается с помощью отвердителей при нормальной и повышенной температуре. Плотность эпоксидных смол — 1 100…1 200 кг/м3, температурный предел применения — до 120°С. Отвержденный полимер имеет высокую водостойкость, хорошую адгезию к металлу, дереву, каменным материалам, химическую стойкость. Применяются эпоксидные смолы в качестве универсальных клеев, связующих в стеклопластиках, полимербетонах, для получения лаков и красок.
Полиэфирные смолы — обширная группа полимеров, получаемых поликонденсацией многоатомных спиртов и органических кислот. Различают насыщенные (термопластичные) полиэфиры и ненасыщенные полиэфиры (термореактивные). Ненасыщенные полиэфирные полимеры применяют для изготовления различного рода стеклопластиков и изделий из них (плоских и волнистых листов, санитарно-технических изделий), лаков, красок, клеев, литых изделий, полимербетонов и т.д.
Алкидные полимеры — разновидность полиэфирных полимеров; один из старейших типов полимеров, получивших широкое распространение в лаковой промышленности, в меньшей степени — для производства линолеума. В промышленности строительных материалов из алкидных полимеров применяют глифталевые и пентафталевые полимеры и их модификации. Названия этих полимеров образуются от вида применяемого сырья: глифталевые получают на основе глицерина и фталевого ангидрида, пентафталевые — на основе пентаэритрита и фталевого ангидрида. Модифицированные глифтали и пентафталевые полимеры в основном применяют для изготовления лаков и эмалей холодной и горячей сушки, грунтовок и шпатлевок для внутренней отделки помещений.
Полиуретановые смолы — химически активные олигомеры, легко отверждающиеся водой, гликолями (двухатомные спирты). Обладают высокой прочностью и эластичностью, химической стойкостью, износостойкостью. Их используют для получения искусственных кож, поролона, эффективных теплоизоляционных материалов, лакокрасочных материалов, клеев.
Фурановые полимеры получают из фурфурола, фурилового спирта и ацетона. Они обладают высокой теплостойкостью и применяются для получения полимерных бетонов, защитных лаков, клеев и мастик. Из пресс-материалов изготавливают трубы, арматуру, различные детали.
Кремнийорганические полимеры — представители элементоорганических высокомолекулярных соединений. Мономерами для кремнийорганических полимеров служат соединения, получаемые взаимодействием кремния с хлористым метилом и этилом. Кремнийорганические полимеры характеризуются высокой теплостойкостью (более 400°С), водостойкостью, морозостойкостью, эластичностью, устойчивостью к окислению, гидрофобизующей способностью.
В строительстве широко используют низкомолекулярные кремнийорганические полимеры в виде жидкостей для придания гидрофобных свойств поверхностям различных строительных материалов (бетона, кирпича, асбестоцемента, штукатурки и др.). Гидрофобизирующие кремнийорганические жидкости (ГКЖ) нетоксичны и удобны в обращении. Кремнийорганические полимеры применяют для изготовления пенопластов, пропиточных составов, лаков, эмалей, красок, а также для изготовления слоистых пластиков, стеклопластиков и др.
Полиамиды — содержат в основной цепи макромолекулы повторяющиеся амидные группы —СОNH—. Из полиамидов изготавливают пленки, трубы, различную строительную арматуру. Применяют их также для изготовления лаков и клеев, обладающих хорошей адгезией к бетону, керамике, металлам, пластмассам и др.
Каучукоподобные полимеры и синтетические каучуки. Отдельную группу полимеров, получаемых полимеризацией различных углеводородов, составляют синтетические каучуки. Главная особенность их заключается в том, что они состоят из гибких, как бы свернутых в спираль, макромолекул и обладают эластичностью. При приложении растягивающей силы они могут удлиняться в 2—10 раз, а при прекращении действия силы восстанавливают свои первоначальные размеры.
При обработке серой в условиях повышенного давления и температуры (140…150°С) из смесей каучуков с наполнителями (мел, сажа, каолин) и некоторыми регулирующими добавками получают вулканизированный каучук и резину. При вулканизации (превращении каучука в резину) макромолекулы каучука связываются поперечными связями («мостиками» из серы), что повышает механическую прочность, эластичность и теплостойкость материала. В отличие от каучуков резины не имеют пластических деформаций и не растворяются в органических растворителях.
Название «каучук» произошло от двух индейских слов: «кау» — дерево и «учу» — плакать, течь. Первым каучуком, с которым познакомились люди, был натуральный каучук, получаемый из млечного сока (латекса) бразильской гевеи. Есть и некоторые другие каучуконосные растения. Латекс содержит около 35% природного каучука и до 60% воды. По внешнему виду латекс напоминает молоко. Исследования показали, что натуральный каучук представляет собой изопрен — ненасыщенный ациклический углеводород.
Промышленностью выпускается большое количество синтетических каучуков с самыми разнообразными свойствами, в ряде случаев — более высокими, чем у натурального каучука. Каучуки выпускают в виде твердых эластичных продуктов, вязкой жидкости (жидкие каучуки) и в виде водных дисперсий — каучуковых латексов. Латексы имеют преимущества перед другими формами выпуска синтетических каучуков (СК): они легко совмещаются с другими материалами (цементом, наполнителями), легко распределяются на поверхности материалов тонкой пленкой, не горючи, в них отсутствуют дорогостоящие и токсичные органические растворители.
Каучук и каучукоподобные полимеры используются в строительстве для изготовления эластичных клеев, красок, мастик, для модификации полимерных и битумных материалов, изготовления герметиков, материалов для полов, модификации строительных растворов и бетонов и т.д.
Основной вид каучуков (более половины общего выпуска синтетических каучуков) - бутадиен-стирольные каучуки и бутадиен-стирольные латексы. Другие виды каучуков, достаточно широко применяемых в строительстве, — хлоропреновый (полихлоропреновый) каучук,бутилкаучук, тиоколовые (полисульфидные) каучуки и др.
Модифицированные природные полимеры. Для получения связующих веществ, применяемых в отделочных работах, природные полимеры модифицируют в целях улучшения их свойств.
Целлюлоза(от лат. сellula — клетка) — самый распространенный природный полимер. Для производства модифицированных полимеров целлюлозы используют древесину или хлопок. Из древесины получают так называемую древесную целлюлозу, из хлопка — целлюлозу высшего качества.
Нитроцеллюлозу (НЦ) (азотнокислый эфир целлюлозы) с содержанием азота 10,7…12% называют коллоксилином, а с более высоким содержанием азота — пироксилином. По внешнему виду коллоксилин представляет собой рыхлую волокнистую массу белого цвета, напоминающую исходную целлюлозу. Серьезным недостатком нитроцеллюлозы является легкая воспламеняемость. Применяют нитроцеллюлозу для изготовления шпатлевок, мастик, красок, лаков.
Карбоксиметилцеллюлоза (КМЦ)— порошкообразный или волокнистый продукт белого цвета, хорошо растворяющийся в воде. Образующийся вязкий раствор обладает клеящими свойствами. Карбоксиметилцеллюлозный клей используется для приклеивания обоев, изготовления мастик, шпатлевок, штукатурных смесей. Он не токсичен, биостоек, стоек к действию органических растворителей, жиров, масел. В производстве лаков и красок применяется также метилцеллюлоза (МЦ), этилцеллюлоза (ЭЦ), бензилцеллюлоза (БЦ), оксиэтилцеллюлоза.
Природные смолысодержатся в жидкостях, выделяемых на поверхности коры деревьев самопроизвольно или в результате ее ранения. Они содержат много низкомолекулярных летучих веществ. Ископаемые смолы (янтарь, копалы) представляют собой продукты жизнедеятельности давно погибших деревьев. При переработке смолы хвойных деревьев получают канифоль и скипидар. Скипидар используют в качестве растворителя. Канифоль, растворы которой в органических растворителях обладают клеящими свойствами, применяют в качестве составной части клеящих мастик для улучшения их адгезионных свойств.
Олифы(от греч. a’leipha — мазь, масло) — пленкообразующие вещества на основе растительных масел или алкидных смол. Применяются олифы для приготовления и разбавления масляных красок, для пропитки древесины перед окрашиванием, как вяжущее и пластификатор в мастиках и замазках при облицовочных работах.
Дата добавления: 2018-11-24; просмотров: 687; Мы поможем в написании вашей работы! |
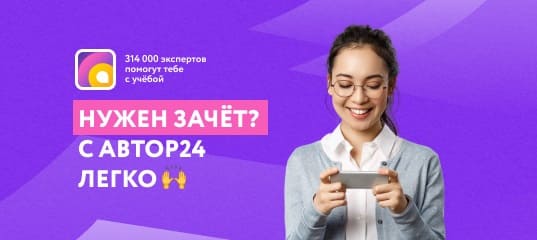
Мы поможем в написании ваших работ!