Оценка качества сухих строительных смесей; условные обозначения
Качество сухих смесей оценивается по совокупности нормируемых характеристик: смесей в сухом состоянии; смесей, затворенных водой и готовых к применению; затвердевшего раствора в проектном возрасте.
К основным показателям качества сухих смесей отнесены: влажность; зерновой состав, задаваемый в виде наибольшей крупности и содержания зерен наибольшей крупности; насыпная плотность (при необходимости). Влажность смесей не должна превышать 0,2 или 0,3 % по массе в зависимости от вида вяжущего.
Основные нормируемые характеристики смесей, готовых для применения: подвижность, водоудерживающая способность, объем вовлеченного воздуха, а также сохраняемость первоначальной подвижности для цементных смесей и время начала схватывания или продолжительность переработки для гипсовых смесей.
В отличие от обычных растворных смесей для оценки подвижности предлагаются не один, а три различных показателя: погружение конуса Пк, см, расплыв конуса РК, мм и расплыв кольца Рк, мм.
Критерий оценки и требуемую подвижность устанавливают в зависимости от назначения и способа применения сухой смеси. Важно, что требуемая подвижность должна быть обеспечена при затворении водой в количестве, установленном производителем и указанном на маркировке.
Водоудерживающая способность смесей должна быть не менее 90 %, а при условии содержания водоудерживающих добавок – не менее 95 %.
|
|
Технические требования к затвердевшим растворам весьма разнообразны и зависят от назначения и условий применения смесей. Для большинства смесей (кроме клеевых) основным показателем качества затвердевшего раствора является прочность на сжатие, по которой устанавливается соответствующая марка из параметрического ряда: М5, М10, …, М200, М250 и М300.
Важнейшим требованием к смесям для отделочных работ является минимально допускаемая прочность сцепления с эталонным бетонным основанием. В соответствии с требованиями ГОСТ 31357 и ГОСТ 31358 прочность сцепления затвердевших цементных растворов должна быть не ниже, МПа: 0,8 – для ремонтных смесей; 0,75 – для напольных; 0,5 – для клеевых; 0,4 – для наружных штукатурных; 0,25 – для внутренних штукатурных.
Для смесей, предназначенных для использования во влажных и мокрых помещениях, а также для наружного применения, нормируются водопоглощение и марка по морозостойкости. Смеси на цементном вяжущем должны иметь водопоглощение растворных образцов при полном погружении в воду на 48 ч не более 8 % по массе. Марки по морозостойкости затвердевших растворов: F15, F25, …, F200, F300 и F400.
Напольные смеси дополнительно должны иметь определенные прочность на растяжение при изгибе, истираемость и деформации усадки; гидроизоляционные – фиксированную марку по водонепроницаемости и т. д.
|
|
В соответствии со стандартными требованиями условное обозначение сухой смеси должно состоять из наименования классификационных признаков согласно ГОСТ 31189, обозначения основных технических показателей и обозначения нормативного документа на данную смесь.
В условном обозначении могут быть опущены: слово "строительная"; слово "цементная" – для сухих смесей на цементном вяжущем; слово "крупнозернистая" – для растворных крупнозернистых сухих смесей; слово "выравниваемая" – для напольных сухих смесей.
Пример условного обозначения сухой штукатурной тяжелой смеси на цементном вяжущем для наружных работ марки по прочности при сжатии М50, марки по морозостойкости F35, механизированного нанесения:
Смесь сухая штукатурная тяжелая для наружных работ, М50, F35 механизированного нанесения ГОСТ 33083-2014.
Особенности производства работ при применении сухих строительных смесей и их технико-экономическая эффективность
Сухие смеси могут упаковываться в полиэтиленовые пакеты вместимостью до 8 кг (для розничной торговли) и многослойные бумажные мешки из крафт-бумаги или с полиэтиленовым вкладышем вместимостью до 50 кг. Для крупных потребителей, применяющих механизированные способы выполнения работ, допускается поставка смесей в мягких контейнерах (биг-бэгах), вмещающих 0,5…1,5 т или специализированными силосными контейнерами большой емкости (3…18 т), обеспечивающими защиту от воздействия осадков.
|
|
Смеси должны храниться в упакованном виде в крытых складских помещениях с влажностью воздуха не более 60 %. Гарантийный срок хранения смесей в неповрежденной упаковке – 6 мес., а смесей, транспортируемых в силосах, - 3 мес. с даты изготовления.
Приготовление растворных смесей с использованием современных сухих смесей очень технологично: нужно только добавить воду в количестве, указанном изготовителем, и тщательно перемешать смесь по рекомендованному режиму. Однако надо иметь в виду, что заявленные изготовителем свойства продукта могут быть достигнуты при неукоснительном выполнении всех требований инструкции по применению. Не допускается вводить в сухую смесь или готовый раствор какие бы то ни было химические добавки, смешивать продукты различного назначения или однотипные, но разных изготовителей. Добавление воды свыше рекомендуемого количества или любых добавок ведет к непрогнозируемому снижению качества материала.
|
|
Особенности приготовления растворных смесей связаны со спецификой диспергирования полимерных порошкообразных модификаторов. Для более быстрого диспергирования рекомендуется энергичное перемешивание, например с помощью профессионального миксера или электродрели с насадкой.
Перемешивают смесь обычно в два приема. Первый – 4…5 мин. Затем для дозревания смеси дают отстояться 5…10 мин. В это время вокруг первичных полимерных частиц формируются водные оболочки, в результате чего модификатор начинает работать в растворной смеси. Затем производится окончательное перемешивание в течение 1-2 мин.
В инструкции по применению любой модифицированной сухой смеси указан интервал рабочих температур, например от +5 до +30° С, в котором данная смесь обеспечивает заявленные свойства. Только при этих температурах полимерный модификатор перейдет в пленочную форму и образует дополнительные связи внутри затвердевшего раствора и на границе отделочного слоя и основания.
При использовании растворной смеси надо строго следовать указаниям изготовителя относительно рекомендуемой и максимальной толщины нанесения состава. Недопустимо нанесение толстым слоем (10 мм и более) смеси с высоким содержанием эфира целлюлозы, предназначенной для тонкослойного использования. В этом случае может проявиться "эффект карамели", когда поверхность слоя отвердевает нормально, а внутри сохраняется незатвердевший раствор.
Расширение производства узкоспециализированных сухих смесей связано с необходимостью увеличить производительность труда строителей, снизить материалоемкость и повысить качество строительных объектов.
С появлением специальных сухих смесей для машинного нанесения и оборудования для их использования стали применяться механизированные технологии строительных и отделочных работ. Полная схема механизации включает доставку смесей на объект и их хранение в силосных контейнерах большой емкости, подачу сыпучего материала к месту работ с использованием пневмотранспортной системы, приготовление и нанесение растворной смеси на основание с помощью мобильной растворосмесительной станции.
Наиболее часто механизированные технологии применяются для штукатурных работ, устройства выравнивающих стяжек и наливных полов, а также при устройстве фасадных систем утепления "мокрого" типа. Производительность труда отделочников при этом повышается в 3…5 раз в зависимости от вида работ и степени механизации. Кроме того, уменьшается себестоимость одного м2 готовой поверхности и сокращаются сроки выполнения отделочных работ.
Благодаря высокой водоудерживающей способности модифицированных сухих смесей появились тонкослойные технологии нанесения растворных смесей: тонкие штукатурки, составы для облицовочных работ и кладки высокоточных стеновых изделий, самовыравнивающиеся стяжки для полов. В этом случае расход основных материалов снижается в 3-4 раза и более.
Применение сухих смесей наряду с повышением производительности труда и снижением расхода растворной смеси обеспечивает получение готовых покрытий высокой долговечности с заданными эксплуатационными свойствами. Повышенная долговечность является одним из решающих факторов экономической эффективности использования модифицированных сухих смесей, в результате чего удлиняется межремонтный период и соответственно снижаются эксплуатационные расходы.
Общие сведения
Органические вяжущие вещества – это высокомолекулярные природные или синтетические вещества, способные:
приобретать жидковязкую консистенцию при нагревании или при действии растворителей или же имеющие жидковязкую консистенцию в исходном состоянии;
с течением времени самопроизвольно или под действием определенных факторов (температуры, УФ-облучения, веществ-отвердителей и др.) переходить в твердое состояние.
При этом как в жидком, так и в твердом состоянии большинство этих веществ имеют хорошую адгезию к другим материалам.
В зависимости от происхождения, химического и вещественного состава органические вяжущие делят на следующие группы:
черные вяжущие (битумы и дегти);
природные смолы, клеи и полимеры;
синтетические полимерные продукты.
Природные высокомолекулярные вещества применяют как в их естественном состоянии, так и после химической модификации, придающей им необходимые свойства. Например, целлюлозу применяют в виде эфиров (нитроцеллюлоза, метилцеллюлоза и т. п.). Битумы также часто подвергают модификации.
Самая обширная группа органических вяжущих – синтетические полимеры. Их получают из низкомолекулярных продуктов (мономеров) полимеризацией и поликонденсацией. Специфическая группа полимеров – каучуки и каучукоподобные полимеры, обладающие высокоэластичными свойствами – способностью к большим упругим деформациям; их также называют эластомерами.
В зависимости от отношения к нагреванию и растворителям органические вяжущие делят на термопластичные и термореактивные.
Термопластичными называют вещества, которые при нагревании переходят из твердого состояния в жидкое (плавятся), а при охлаждении вновь затвердевают; причем такие переходы могут повторяться много раз. Термопластичность объясняется линейным строением молекул и невысоким межмолекулярным взаимодействием. По этой же причине большинство термопластов способно растворяться в соответствующих растворителях. К термопластам относятся битумы, смолы, многие широко распространенные полимеры — полиэтилен, поливинилхлорид, полистирол и др.
Термореактивными называют вещества, у которых переход из жидкого состояния в твердое происходит необратимо. При этом у них меняется молекулярная структура: линейные молекулы соединяются в пространственные сетки – гигантские макромолекулы. Такое необратимое твердение (этот процесс называют также отверждением, сшивкой, вулканизацией) происходит не только под действием нагрева (отсюда пошел термин «термореактивные вещества»), но и под действием веществ отвердителей, УФ и γ–излучения и других факторов. Отвержденные термореактивные полимеры, как правило, более теплостойки, чем термопластичные. К термореактивным органическим вяжущим относятся, например, эпоксидные и полиэфирные олигомеры (смолы), олифы, каучуки в смеси с вулканизаторами и др.
Органические вяжущие существенно отличаются от неорганических (минеральных). Адгезионные свойства многих органических вяжущих значительно выше, чем минеральных. Прочность на сжатие у них сопоставима с прочностью минеральных, а при изгибе и растяжении во много раз выше. У термопластичных вяжущих прочность быстро падает при повышении температуры из – за размягчения полимера. Органические вяжущие характеризуются низкой термостойкостью. В зависимости от состава и строения температура их размягчения составляет 80…250 °С. Все органические вяжущие – горючие вещества.
Большинство органических вяжущих водо- и химически стойки (они хорошо противостоят действию кислот, щелочей и растворов солей). Стоимость органических вяжущих значительно выше, чем минеральных, а объемы их производства – намного ниже.
Из сказанного следует, что отличия органических вяжущих от минеральных носят как положительный, так и отрицательный характер, поэтому каждый вид вяжущих имеет свои рациональные области применения, выбираемые с учетом всех его свойств. В последние годы широко используют модификацию минеральных вяжущих органическими с целью получения композиционных материалов с принципиально новым набором свойств.
Органические вяжущие используют в строительстве для получения клеев, мастик, лакокрасочных материалов, полимерных и полимерцементных растворов и бетонов. Большая же часть синтетических полимеров используется при производстве пластмасс, в состав которых, как правило, входят наполнители и другие компоненты, снижающие стоимость и придающие пластмассам специальные свойства.
Высокая стоимость полимерных вяжущих выдвигает на первый план при их использовании задачу снижения полимероемкости материала, т.е. получения требуемого результата при минимальном расходе полимера. Поэтому полимерные вяжущие применяют в основном для получения тонких облицовочных изделий (плиток, пленок), погонажных изделий, окрасочных и клеящих составов, гидроизоляционных и защитных химически стойких покрытий, а также для изготовления газонаполненных пластмасс – теплоизоляционных материалов с низкой плотностью (10...50 кг/м3).
Битумы и дегти
Первыми органическими вяжущими, которые начали применять в строительстве, были битумы и дегти. Имеются свидетельства применения битумных материалов в I тысячелетии до н.э. в Месопотамии при строительстве «висячих» садов Семирамиды, тоннеля под Евфратом и асфальтированных мостовых. Известно применение битумных материалов и в Древнем Риме.
Хотя битумы и дегти имеют различное происхождение и несколько отличаются составом, оба обладают общими характерными свойствами. При нагревании они обратимо разжижаются и в таком состоянии хорошо смачивают другие материалы, а при охлаждении отвердевают, прочно склеивая смоченные ими материалы. Кроме того, битумы и дегти водостойки и водонепроницаемы, и если ими пропитать или покрыть другие материалы, то приобретают гидрофобные (водоотталкивающие) свойства. Битумы и дегти хорошо растворяются в органических растворителях. Перечисленные свойства предопределили использование битумов и дегтей для получения клеящих и гидроизоляционных материалов, а также для получения специальных дорожных бетонов – асфальтобетонов.
Битумы (от лат. bitumen – смола) – при комнатной температуре вязкопластичные или твердые вещества черного или темно-коричневого цвета, представляющие собой сложную смесь высокомолекулярных углеводородов и их неметаллических производных. В зависимости от происхождения битумы могут быть природные и искусственные (техногенные); источником образования или получения битумов и в том и в другом случае является нефть.
Природные битумы встречаются в виде асфальтовых пород, например, песка, пористого известняка, пропитанных битумом (содержание битума от 5до 20 %). Такие породы встречаются в Венесуэле, Канаде, на острове Тринидад и др. Есть месторождения практически чистых битумов, например битумные озера на Сахалине. Природные битумы образовались при разливе нефти в результате испарения из нее легких фракций и частичного окисления кислородом воздуха. Мировые запасы природного битума — более 500 млрд т.
Искусственные битумы получают как остаток при переработке нефти на нефтеперегонных заводах при получении топлива и смазочных масел. После переработки (перегонке или крекинге) нефти остается густой смолистый остаток, содержащий твердые частицы — гудрон. Выход гудрона из тяжелой нефти 7...8 %, а из легкой – до 1 %. Гудрон подвергается специальной обработке (например, нагреву и продувке воздухом) для получения твердого или полутвердого материала – нефтяного битума.
Элементный состав битумов находится в следующих пределах: углерод С – 70...87 %, водород Н – 8...12 %, сера S – 0,5...7 %. Эти элементы образуют в битуме четыре группы веществ:
нефтяные масла – (молекулярная масса 300...600); алифатические углеводороды (строение молекул линейное); содержание в битуме 30...60 %; придают битуму вязкость и эластичность;
смолы — (молекулярная масса 600...1000), содержание в битуме 20...40 %; состоят из кислорода и серосодержащих полярных соединений, придают битуму высокие адгезионные свойства;
твердые высокомолекулярные вещества – (молекулярная масса 1000...5000); содержание в битуме 10...40 %; к ним относятся асфальтены, карбены и карбоиды; они придают битуму твердость, повышают температуру размягчения;
асфальтогеновые кислоты – содержание до 3 %; выполняют функцию поверхностно-активных веществ и повышают адгезионные свойства битума.
Вещества, составляющие битум, образуют коллоидную систему, в которой масла с растворенными в них смолами являются дисперсионной средой. В ней равномерно распределены мельчайшие твердые частицы (дисперсная фаза). Устойчивость такой системе придают ПАВ – смолы и асфальтогеновые кислоты. При нагреве масла разжижаются и битум переходит в жидковязкое состояние; при охлаждении масла густеют и битум затвердевает, а при дальнейшем охлаждении делается хрупким. Эти превращения битума обратимы, т.е. битум – термопластичный материал.
Битумы делят на три типа по области их применения: дорожные (для асфальтобетонов), кровельные (для мягких кровельных материалов) и строительные (для изготовления мастик, гидроизоляции и др.). Каждый тип битумов в зависимости от состава может иметь различные марки (таблица 9.1).
Таблица 9.1
Марки нефтяных битумов
Марка битума | Температура размягчения,°С, не ниже | Растяжимость при 25 °С, не менее | Глубина проникания иглы при 25 °С, 10-1, мм |
Строительные битумы | |||
БН-50/50 | 50 | 40 | 41…60 |
БН-70/30 | 70 | 3 | 21…40 |
БН-90/10 | 90 | 1 | 5…20 |
Кровельный битум | |||
БНК-45/180 | 40…50 | Не нормируется | 140…220 |
БНК-45/190 | 40…50 | То же | 160…220 |
БНК-90/40 | 85…95 | То же | 35…45 |
БНК-90/30 | 85…95 | То же | 25…35 |
Дорожные битумы | |||
БНД-200/300 | 35 | Не нормируется | 201…300 |
БНД-130/200 | 39 | 65 | 131…200 |
БНД-90/130 | 43 | 60 | 91…130 |
БНД-60/90 | 47 | 50 | 61…90 |
БНД-40/60 | 51 | 40 | 40…60 |
Марки битумов определяют по комплексу показателей, основные из которых: температура размягчения, твердость и растяжимость.
Температуру размягчения определяют на стандартном приборе «Кольцо и шар». Температурой размягчения считается температура, при которой шарик проваливается сквозь битум, заплавленный в кольцо. У битума, как у сложной коллоидной системы, нет определенной температуры плавления: он размягчается постепенно.
Твердость (вязкость) битума определяют на приборе пенетрометр по погружению иглы в образец битума (единица шкалы прибора 0,1 мм) при температуре 25 °С.
Растяжимость битума определяют по абсолютному удлинению (в см) стандартного образца битума, растягиваемого в воде при 25 °С со скоростью 5 см/м.
Транспортируют битумы в фанерных барабанах или бумажных мешках. Хранят в закрытых складах или под навесом таким образом, чтобы на битум не попадали прямые солнечные лучи. Битум – горючее вещество, поэтому при работе с ним, особенно при разогреве битума, следует соблюдать требования пожарной безопасности.
Деготь – продукт сухой (без доступа воздуха) перегонки твердых видов топлива (древесины, угля, горючих сланцев, торфа и т. п.), представляющих собой вязкую темно-бурую жидкость с характерным «дегтярным» запахом.
Деготь, вероятно, один из старейших химических продуктов, получаемых человеком. С древнейших времен на Руси было развито «дегтекурение» — получение дегтя из бересты (тонкой березовой коры). Бересту нагревали без доступа воздуха до 200...300 °С. При этом образовывалась темная вязкая жидкость с сильным запахом. Позже стали вырабатывать деготь из древесины березы и других лиственных пород.
Деготь использовали дня пропитки деревянных сооружений, лодок, рыбацких сетей, смазки сапог и т.п. Такая обработка защищала от гниения, благодаря антисептирующему и гидрофобизирующему действию дегтя. Антисептирующие свойства дегтя используют и в медицине (мазь Вишневского, деггярное мыло и т. п.). Копчение продуктов (рыбы, мяса) также основано на обработке их продуктами сухой перегонки древесины.
В больших масштабах деготь стали производить с конца XIX в., когда стала развиваться металлургия. Деготь является побочным продуктом при коксовании углей (высокотемпературной (1000±50)°С обработки каменных углей без доступа воздуха с целью получения кокса).
Дегти, как и битумы – сложная дисперсная система, состоящая из большого числа (несколько тысяч) различных углеводородов (жидких и твердых) и их неметаллических производных. Но в отличие от битума, где преобладают парафиновые углеводороды, в дегте много ароматических углеводородов и их производных (бензола, толуола, нафталина, фенола и др.). Именно они придают дегтю антисептические свойства.
Сырой деготь практически не применяется. Его разгоняют, получая растворители, различные масла (антраценовое, креозотовое и др.) и твердообразное вещество – пек.
Пек (от голл. pek — смола) – аморфный хрупкий при обычных температурах остаток от перегонки «сырого» дегтя при температуре более 360°С. Он состоит из смолистых веществ, «свободного углерода», антрацена, масел и других слаболетучих соединений. Пеки применяют для получения составного дегтя, сплавлением его с маслами, и пекового лака, растворением его в ароматических растворителях. Составные дегти используют для гидроизоляции и антисептирования древесины.
Дегти менее атмосферостойки, чем битумы. Под действием солнечного излучения и кислорода они окисляются, превращаясь в твердые хрупкие продукты; это объясняется наличием в дегте, в отличие от битума, активных реакционноспособных соединений, в частности, ароматических углеводородов. Дегти и продукты на их основе — канцерогены, поэтому их использование в местах, где возможен их длительный контакт с человеком, запрещено.
При работе с дегтями и пеком следует помнить, что они и их пары могут вызвать воспаление или аллергические реакции при контакте с кожей и в особенности – слизистыми оболочками.
Общий недостаток битумов и дегтей – узкий интервал температур, при которых материалы на их основе обладают прочностью и эластичностью. Так, битумы при понижении температуры до 0...–10°С становятся хрупкими, а при повышении до 40...60°С начинают течь. Для расширения интервала эксплуатационных температур битумы и дегти модифицируют, добавляя термопластичные полимеры и каучуки.
Дата добавления: 2018-11-24; просмотров: 2263; Мы поможем в написании вашей работы! |
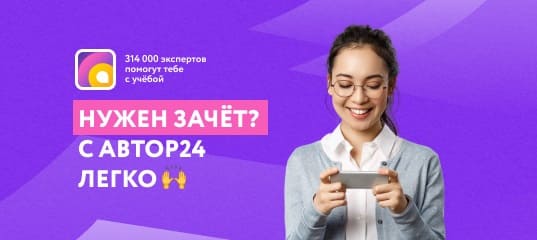
Мы поможем в написании ваших работ!