Основы технологии производства керамики
Основы технологии производства керамики
Основные этапы производства керамических материалов:
Добыча, транспортировка, обработка сырья;
Подготовка массы;
Формование изделий;
Сушка;
Обжиг;
Контроль качества;
Упаковка готовой продукции.
Карьерная глина, как правило, непригодна для получения керамических изделий. Поэтому проводится её обработка с целью подготовки массы. Подготовку глин ведут сочетанием естественной и механической обработки. Естественная обработка – вылеживание предварительно добытой глины в течение 1-2 лет при периодическом увлажнении осадками или искусственном замачивании и периодическом замораживании и оттаивании. Механическая обработка – проводится с целью разрушения природной структуры глин, удаления и измельчения крупных включений, удаления примесей, измельчения глин и добавок, перемешивания всех компонентов. Для механической обработки используются специализированные машины – глинорыхлители; дезинтеграторы, мельницы, мешалки и т.д. Качественная подготовка сырьевой массы – необходимое условие получения качественных керамических изделий.
В зависимости от вида продукции, вида и свойств сырья изделия формуют по одному из 5-ти способов.
Пластический способ. Влажность теста 18…28%. Наиболее простой, наименее металлоемкий и наиболее распространенный способ. Применяется в случаях использования среднепластичных и умеренно-пластичных, рыхлых и влажных глин с умеренным содержанием посторонних включений. Формование осуществляется на ленточных прессах (шнековых) под давлением 1,6…7 МПа с вакуумированием или подогревом и без них. Производительность до 10 000 штук/час.
|
|
Рис. 5.1. Схема ленточного пресса
Жесткий способ является разновидностью пластического способа. Влажность массы 13…18%. Формование осуществляется на мощных вакуумных и гидравлических прессах под давлением 10…20 МПа. Могут быть использованы менее пластичные глины. Требуются меньшие энергетические затраты на сушку. Сырец имеет повышенную прочность. Пластическим и жестким способами выпускаются полнотелые и пустотелые кирпичи, камни, блоки, панели, черепица.
Полусухой способ менее распространен. Влажность шихты 8…12%. Формование изделий осуществляется в пресс-формах на гидравлических или механических прессах под давлением 15…40 МПа. По сравнению с пластическим способом длительность производственного цикла сокращается в 2 раза, изделия имеют более правильную форму и точные размеры, до 30% сокращается расход топлива. Недостаток способа – металлоемкость (формы) в 3 раза выше по сравнению с пластическим способом. Можно использовать малопластичные тощие глины с большим количеством добавок.
|
|
Сухой способ является разновидностью полусухого способа. Влажность пресс-порошка составляет 2…6%. Устраняется операция сушки. Применяется для изготовления плотных керамических изделий – плитки для полов; клинкерного кирпича; материалов из фаянса и фарфора.
В шликерном (литьевом) способе используется многокомпонентная масса, состоящая из неоднородных и трудноспекающихся глин и добавок. Влажность шликера – до 40%. Способ применятся для изготовления изделий сложной формы (санитарно-технических изделий), облицовочных плиток.
В процессе сушки и обжига сырца происходят следующие приращения:
Сушка изделий(t=100…150°С) служит для удаления свободной воды. Процесс обратим. Изделия необходимо высушить до влажности 5…6 % во избежание неравномерной усадки, искривлений, растрескиваний при обжиге. Продолжительность сушки – до 72 часов. Воздушная усадка составляет 6…10%.
После сушки выполняется операция обжига.
При температуре 500…800°Спроисходит потеря химически связанной воды, выгорание органических примесей. Процесс необратим. Дегидратация глинистых минералов осуществляется по общей схеме:
|
|
При температуре 800…900°С происходит распад метакаолина на оксиды, находящиеся в химически активном состоянии:
При температуре 1000…1100°С происходит образование керамического черепка. Происходит частичное плавление твердой фазы, расплав обволакивает нерасплавившиеся частицы, стягивает их, проводя к уплотнению массы и огневой усадке, которая составляет 2…8%. Образуются различные соединения, в т.ч. основной минерал керамики, придающий ей водостойкость и высокие физико-механические характеристики – муллит – 3Al2O3·2SiO2. В основном керамические изделия обжигают при данной температуре.
При повышении температуры обжига до 1200°Спроисходит усиление спекания, образование плотного керамического черепка. При такой температуре получают изделия с плотным черепком – клинкерный кирпич, плитки для полов, керамогранит и др.
При температуре 1350°Спроисходит плавление сырья, до этой температуры обжиг не доводят.
Дата добавления: 2018-11-24; просмотров: 732; Мы поможем в написании вашей работы! |
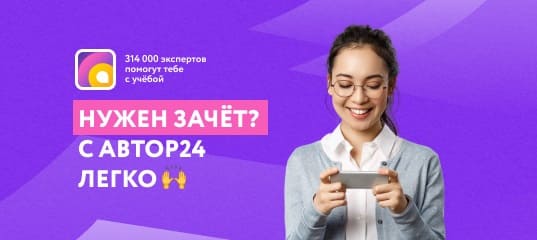
Мы поможем в написании ваших работ!