Специальные требования по отдельным технологическим процессам.
Литьё полиформальдегида и его сополимеров.
При литье под давлением необходимо выполнять специальные требования по отдельным технологическим процессам.
Ограниченная термостабильность полиформальдегида и его сополимеров требует строго контролировать температурный режим литья и избегать появления застойных зон в цилиндре. При увеличении времени выдержки при повышенной температуре материала изменяется его окраска, а затем выделяются пары формальдегида, что обнаруживается по неприятному запаху и пузырькам газа. Перед началом переработки формальдегида и его сополимеров температура загрузочной зоны цилиндра не должна превышать 150-155 °С.
В передней части цилиндра и в сопле устанавливают температуру 165-175 °С. При этой температуре материал в цилиндре следует выдерживать в течении 20-30 мин. Затем температуру цилиндра в первой зоне и температуру сопла повысить до температуры переработки и включить обогрев второй и третьей зоны. Начать вращение шнека со скоростью примерно 4 об/мин. Открыть загрузочное отверстие цилиндра для поступления материала из бункера в цилиндр. Далее отверстие плотно закрыть. При появлении из сопла первой порции расплава скорость вращения повысить до необходимой (от 60 до 80 об/мин). Первая порция расплава может быть бесцветной, разложившейся с сильным запахом формальдегида. Первую партию прогоняемого материала опускать в воду.
|
|
В процессе работы слабый запах формальдегида указывает на неправильный температурный режим (перегрев материала). Для удаления формальдегида отвести форму и продавить перегретую массу. Продавленную массу погрузить в сосуд с холодной водой и затем снизить температуру по зонам обогрева.
При литье внимательно следить за чистотой поверхности отливок. При появлении коричневой окраски на поверхности деталей снизить температуру зон обогрева и выдавить перегретую массу.
При изготовлении деталей из полиформальдегидов и его сополимеров литьём под давлением необходимо соблюдать следующие правила:
-перерабатывать формальдегид и его сополимеры при температуре расплава на 5-10 °С выше температуры плавления материала;
-работу производить на партиях, имеющих период индукции не менее 25 мин, период индукции указывается в паспорте на материал;
-масса отливки должна составлять для машин со шнековой пластикацией не более 75-90% номинальной массы, допускаемой мощностью литьевой машины;
-при работе очистка цилиндра от высокоплавкого материала (полиамида, капрона, поливинилхлорида) должна производиться посредством литья переходного материала-полиэтилена высокого давления;
|
|
-недопустимо наличие медных, бронзовых или латунных предметов соприкасающихся с расплавом, так как они ускоряют деструкцию полимера.
Перед началом работы с полиформальдегидами и его сополимерами все контрольные приборы тщательно проверить. При проверке установить поправочный коэффициент между показателями приборов (терморегуляторами) по всем зонам и температурой расплава. Ориентировочно, этот поправочный коэффициент возможно определять по полиэтилену высокого давления и окончательно уточнить при работе на полиформальдегиде с установившимся технологическим режимом. Температуру расплава замерить термопарой или термометром при продавливании массы через сопло.
При работе с полиформальдегидом, в случае остановки машины, обогрев шнека и рабочего цилиндра отключить. По окончании работы полиформальдегид и его сополимеры доработать из шнека и рабочего цилиндра и загрузить термопластавтомат ПЭВД. Вес работы, связанные с переработкой полиформальдегидов и его сополимеров, следует производить при наличии местной вытяжной вентиляции. Запрещается использовать для литья полиформальдегида цилиндр с остатками поливинилхлорида, так как при этом происходит каталитическое разложение полимера.
|
|
4.2.12.2. Литьё поликарбоната .
При переработке литьём под давлением поликарбоната для инжекционного цилиндра и сопла необходима точность систем нагрева, контроля и регулирования. В бункер термопластавтомата загружать подогретый и только просушенный материал, пары влаги вызывают активную деструкцию материала. При изготовлении из поликарбоната деталей технического назначения следует производить процесс литья при минимальной температуре расплава и повышенной температуре формы (80-100° С).
Температура переработки поликарбоната может быть снижена введением небольших количеств добавок (2-3%) дисульфида молибдена, гидрида бора. При этом теплостойкость, твёрдость и износостойкость деталей повышаются. При прерывании процесса литья не рекомендуется выключать обогрев цилиндра, необходимо поддерживать её в пределах 150-160 °С.
При литье поликарбоната специальная смазка не требуется, деталь должна легко извлекаться из формы. Возможные трудности при съёме деталей вызываются перегрузкой формы, недостаточной конусностью, малым наклоном поверхности съёма, плохим качеством полировки формы, малым количеством и слабостью толкателей, недостаточностью воздушных зазоров.
|
|
Поверхность формы и литниковых каналов должна быть хорошо отполирована.
После окончания работы цилиндр следует очистить от поликарбоната во избежание разрушения цилиндра из-за большой адгезии поликарбоната к металлу. Нельзя механически отделять охлажденный и застывший поликарбонат от стенок цилиндра во избежание их повреждения. Тонкие слои поликарбоната могут быть сняты растворением его в метиленхлоридс. Очистку цилиндра рекомендуется производить в электрическом шкафу, выдержав цилиндр в течении нескольких часов при температуре 400°С. При этом поликарбонат разрушается. Цилиндр может быть демонтирован, разобран и механически очищен от расплава медным резцом при температуре переработки. Оставшийся материал можно удалить при 200°С с помощью щётки из латунной проволоки.
Литьё пластиков АБС.
При переработке пластиков АБС нельзя перегревать инжекционный цилиндр, так как при температуре свыше 270°С возможно образование продуктов разложения (в продуктах разложения возможно присутствие мономеров стирола, альфаметилстирола). Температура воспламенения пластиков АБС-290°С.
4.2.12.4. Литье полиоксифенилена, композиции АБС + ПК, полибутадиентерефталата, полиэтиленгерефталата, этролы, поливинилхлорида и термопластичного полиуретана.
Перед остановкой литьевой машины произвести несколько раз пластификацию без противодавления, затем промывку ПЭВД или ПЭНД.
Обработка деталей.
Механическая обработка.
В зависимости от способа получения и конструкции пресс формы готовые изделия могут требовать доработки в целях окончательного придания им потребительских свойств.
Детали, получаемые литьём под давлением, обрабатываются механическим путём (обрезка, откусывание литников, излишков материала по линии разъема формы, образующихся вследствие затекания расплава в неплотности сопряжений элементов пресс формы (облой), каплевидных наплывов на поверхности деталей (грат)) с помощью станков, приспособлений и инструмента, указанных в технологической карте обработки и упаковки (Приложение №18). Кроме того, к доработке относятся раскрытие недооформленных отверстий, накатка резьбы и другие.
Термическая обработка.
Термическую обработку деталей из термопластов следует применять для стабилизации размеров и уменьшения внутренних напряжений, для получения изделий с мелкокристаллической структурой. В зависимости от среды термообработки применять термошкафы с регулятором температуры до 200°С или специальные ванны. При термообработке деталей из термопластов рекомендуется соблюдать режимы, указанные в Приложение №8. Необходимость проведения термической стабилизации деталей из пластмасс должна быть указана в чертеже.
Дата добавления: 2018-11-24; просмотров: 369; Мы поможем в написании вашей работы! |
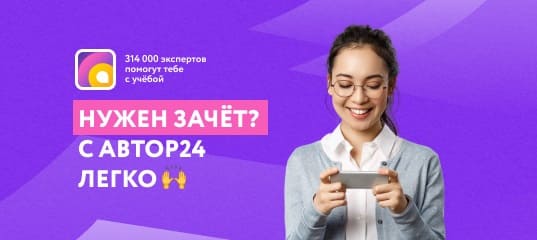
Мы поможем в написании ваших работ!