Узел смыкания (фиксирования).
Узел смыкания предназначен для: контакта с мундштуком, - размыкания и смыкания литьевой формы, - создания усилия смыкания литьевой формы, - извлечения изделия из литьевой формы. Различают механические (коленчато-рычажный) и гидравлические системы смыкания.
Усилие смыкания литьевой формы, пропорциональное площади отливки и удельному давлению литья, должно быть не менее расчётного:
Р=р о * S /1000, где
Р - усилие смыкания, тс;
Р 0 - удельное давления впрыска, л/см 2
S - площадь отливки, см 2
Для расчёта минимального давления смыкания в формулу следует подставить вместо удельного давления впрыскивания, значение распределённого в литьевой форме давления, принимаемое для полистирола, полиэтилена равным 250-350 кг/см 2.
При расчёте усилий смыкания литьевых форм необходимо учитывать особенности переработки отдельных термопластов:
-формирование деталей из стеклонаполненных полиамидов следует проводить в режиме со сбросом давления впрыска до вторичного регулируемого давления формирования;
-формирование деталей из полипропилена следует проводить с длительной выдержкой при высоком давлении в форме для предупреждения образования пустот и вмятин.
Запирание форм при формовании деталей из полипропилена, поликарбоната, стеклонаполненных термопластов, полиформальдегида и его сополимеров должно осуществляться механически. Чисто гидравлический механизм не обеспечит достаточно прочного запирания.
|
|
При расчёте усилия смыкания форм необходимо учитывать конструкцию формуемой детали. Для деталей типа глубоких тонкостенных коробок требуется в 1,5-2 раза Больше усилия смыкания, чем для плоских деталей с той же площадью формирования.
Расчётное усилие смыкания литьевой формы следует сравнивать с паспортной характеристикой термопластавтомата, предлагаемого для использования.
При литье изделий большой площади, когда усилия, возникающие в литьевой форме могут превысить усилия смыкания, целесообразно сбрасывать давление в момент заполнения формы, согласно технологическим режимам работы гидравлических систем, указанных в паспорте термопластавтомата. При этом уменьшаются внутренние напряжения в изделиях, так как облегчается протекание релаксационных процессов.
При недостаточном усилии смыкания, на деталях в плоскости разъёма литьевой формы образуется облой.
Впрыск (инжекция).
Давление литья (Рл)- давление, развиваемое в гидроцилиндре литьевой машины, На современных машинах -60-200МПа. Рл=Рр*Дц*Дц/ Дш*Дш, где Рр-давление рабочей жидкости в гидроцилиндре по манометру, МПа; Дц- диаметр гидроцилиндра, м; Дш - диаметр шнека, м.
|
|
Давление впрыска(Рм)-давление подачи расплава в литниковую систему, необходимое для заполнения литниковой системы и формы. Рм= Рл-Рм, МПа, где Рм- падение давления в гидроцилиндре и сопле=0,1 Рл. За счет осевого перемещения шнека в направлении мундштука расплав полимера впрыскивается в формующую полость литьевой формы. Во время впрыска шнек действует аналогично поршню.
Давление впрыскивания термопласта в литьевую форму зависит от времени и объёмной скорости впрыскивания. Скорость впрыска при литье должна быть оптимальной, чтобы во время заполнения литьевой формы термопласт не затвердевал, но и не произошла механодеструкция полимера. Повышение давления следует применять:
-для увеличения скорости заполнения формы;
-для улучшения качества деталей аморфных полимеров;
-для уменьшения усадки полимеров за счёт более плотной упаковки макромолекул;
-для литья тонкостенных деталей с толщи ной стенки менее 1.5 мм; для литья деталей большой площади;
-для переработки литьём под давлением термопластов с небольшой вязкостью расплава (наполненных полимеров, полиформальдегида и его сополимеров).
Ориентировочные давления впрыскивания и скорость инжекции термопластов на; литьевых машинах указаны в Приложении №7.
|
|
Выдержка расплава в форме.
Давление в форме.
Давление в форме (Рф) равно давлению впрыска с учетом падения давления в литниковой системе. Среднее давление в форме можно приблизительно определить, но формуле:
Рф.ср.= КРм, где К коэффициент, зависящий от геометрических размеров изделия и перерабатываемого материала, обычно равен 0,5-0,7;
Рм- давление впрыска.
При заполнении формы расплавом и выдержке его в форме давление формования претерпевает следующие этапы:
-максимальное давление впрыска при движении расплава до поступления в литьевую форму;
-снижение давления литья за счёт встречных сопротивлений при наполнении литьевой формы расплавом;
-давление возрастает до максимального при уплотнении расплава и для большинства деталей из полистиролов, полиэтилена распределённое давление составляет от 250 до 350 кг/см 2 ;
-выдержка расплава в литьевой форме при максимальном давлении ( подпитка);
-давление гидравлической системы вызывает переход из материального цилиндра в литьевую форму некоторого количества расплава для пополнения объёма формы;
-давление в литьевой форме падает из-за частичного вытекания незастывшего расплава из литьевых каналов формы, период заканчивается закупоркой литьевых каналов отвердевшей массой;
|
|
-давление закупорки литьевых каналов является давлением отключения;
-в момент раскрытия литьевой формы термопласт находится под остаточным давлением.
Изменение выдержки под давлением приводит к изменению давления отключения, при увеличении выдержки под давлением увеличивается плотность отливки, уменьшается усадка. Увеличение остаточного давления может быть причиной трудного извлечения детали из формы вследствие плотно прикасающихся поверхностей изделия и формы при значительных остаточных давлениях. Время выдержки под охлаждением рассчитывается согласно стандартам или техническим условиям на данный материал.
Температура формы.
При формовании деталей из термопластов необходимо поддерживать оптимальную температуру формы. Перепад температур расплава и литьевой формы для различных термопластов должен быть в пределах 100-160 °С.
Перепад температур отдельных точек формы не должен превышать 5-6 єС.
Для поддержания оптимальной температуры литьевой формы следует использовать охлаждение проточной водой или подогрев от термостатирующих устройств. Нагревать обе половинки литьевой формы и регулировать их температуру следует раздельно. Система каналов охлаждения (подогрева) литьевых форм может иметь различное конструктивное оформление:
-для полиэтилена высокой плотности место входа воды в литьевую форму следует располагать рядом с литниковыми каналами, место выхода - дальше от них;
-центральные литниковые каналы большого диаметра охватить специальным охлаждающим каналом;
-в формах для пропилена следует предусмотреть быстрое охлаждение по спиральным каналам с подачей холодной воды в центре.
Подогреваемые литьевые формы следует применять при формовании деталей из поликарбоната, полиформальдегида и его сополимеров, полиамидов с целью снятия внутренних напряжений; деталей, отличающихся разнотолщинностью конструкции, при этом литьевая форма должна иметь подвод широкого литьевого канала к массивным частям отливки во избежание образования пустот при резком остывании наружных слоев в толстых частях детали.
4.2.1 0. По окончанию цикла литья раскрыть форму, сдвинуть ограждение, извлечь детали. Вывернуть резьбовые знаки при формовании деталей с резьбой. Литники необходимо выталкивать из литьевой формы одновременно с деталью. Форма должна обеспечить автоматический сброс отливки, по возможности, отрыв литника от детали без дополнительной механической обработки.
4.2.11. Раскрытую литьевую форму чистить от остатков материала латунным ножом и, по необходимости, смазать, используя при этом: кислоту олеиновую техническую ГОСТ 7580; силиконовую смазку.
Дата добавления: 2018-11-24; просмотров: 558; Мы поможем в написании вашей работы! |
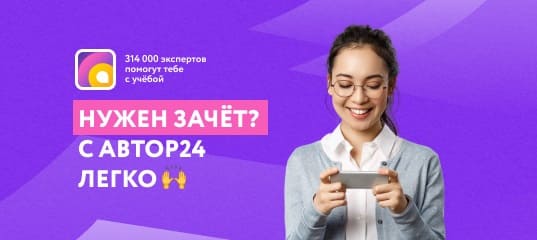
Мы поможем в написании ваших работ!