Операции литья под давлением.
Nbsp;
ТЕХНОЛОГИЧЕСКИЙ ПРОЦЕСС ИЗГОТОВЛЕНИЯ ДЕТАЛЕЙ ИЗ ТЕРМОПЛАСТОВ ЛИТЬЕМ ПОД ДАВЛЕНИЕМ
Подготовка материала.
Понятие подготовки сырья включает в себя вес технологические операции, необходимые для того, чтобы из полимерного сырья получить способный к переработке материал. Изготовители полимерного сырья, предназначенного для переработки в готовое изделие, как правило, поставляют свою продукцию в виде гранулята, легко поддающегося переработке. В таком случае, сырье уже подготовлено на предприятии-производителе. Из-за большого количества рецептур, а также многообразия добавок, подготовку полимера может взять на себя переработчик.
Смешение - процесс механического распределения различных веществ (гранулята с дробленкой, красителей и добавок) за счет взаимного перемещения частиц, осуществляемого до получения заданного соотношения компонентов в любой точке перемешиваемого объема. В зависимости от свойств материалов и требуемого размера зерен используют различные смесительные установки.
Измельчение - это процесс уменьшения размеров частиц твердых тел, преимущественно, за счет механического воздействия. В зависимости от типа вещества при измельчении могут быть использованы различные технологические установки: валковая дробилка, молотковая дробилка, бегуны, дисковая ударно-отражательная мельница, ножевая дробилка, стержневая мельница или вальковая мельница.
|
|
4.1.1. Перед переработкой термопластов следует проводить их подсушку, с целью уменьшения гигроскопической или конденсированной влаги. Сушка гигроскопических материалов (сополимеров стирола, полиамидов, поликарбонатов, ПММА) строго обязательна. Подогрев негигроскопичных термопластов способствует интенсификации литья под давлением. Допустимая остаточная влажность термопластов и их подсушка указана в Приложении №4.
4.1.2. Гранулированные и измельченные термопласты рекомендуется сушить в любых полочных сушильных шкафах на перфорированных полках слоями в 20-30 мм.(время сушки при применении вакуума сокращается в 2-3 раза) или в сушилках с предварительным нагревом воздуха и с последующим его продувом через гранулы. Полки сушилок должны быть короче длины шкафа для обеспечения свободной конвекции горячего воздуха.
4.1.3. Подсушенный термопласт должен храниться в герметично закрывающейся таре.
4.1.4 . В бункер литьевой машины следует загружать термопласт сухим и подогретым. Для термопластов с низкой теплопроводностью (поликарбонат, полиамид, полипропилен), желательно, использовать предварительный подогрев в обогреваемом бункере литьевой машины.
|
|
Литьё под давлением.
Оборудование
Литьевые машины (термопластавтоматы - ТПА) предназначены для формования изделий из термопластов методом литья под давлением. Литьевая машина состоит из трех наиболее важных узлов: узел смыкания, узел пластикации и станина машины с системой привода и системой управления.
Задачи, выполняемые узлом пластикации, состоят в следующем: загрузка, подача, пластикация, дозировка и впрыск (инжекция) термопласта.
Задачи, выполняемые узлом смыкания: контакт с мундштуком, размыкание и смыкание литьевой формы, создание усилия, необходимого для удержания литьевой формы в закрытом состоянии и извлечение изделия из литьевой формы.
Станина служит для размещения на ней отдельных элементов конструкции литьевой машины и их надежного крепления.
Оснастка.
При формовании из термопластов необходимо использовать стационарные литьевые формы. Литьевая форма в основном состоит из неподвижной и подвижной частей, литниковой втулки, литниковой системы, выталкивающего устройства и охлаждающей системы. Конструкция литьевых форм должна отвечать следующим технологическим требованиям:
-одновременное заполнение гнёзд литьевой формы;
|
|
-Равномерное давление впрыска (инжекция) и усилие подпрессовки для многогнёздных форм, чем достигается однородная плотность и размерная точность изделий;
-изменение размеров каждого вводного канала в литьевых формах для изготовления нескольких различных по величине деталей и в литьевых формах с последовательным расположением гнёзд одинакового размера для обеспечения одновременной отливки всех деталей, поскольку длина пути расплава к отдельным деталям различна;
-правильная гидродинамическая конфигурация разводящих литников, так как литник и разводные каналы единое целое с отливкой, литник должен быть коротким, коническим, круглым в сечении и подводиться в центре или в месте наибольшей толщины изделия.
Одногнёздные литьевые формы дают возможность получать детали повышенной точности, улучшают условия наладки работы машины в автоматическом режиме. На литьевую форму оформляется технический паспорт (карта замеров), после чего она запускается в производство. Для повышения производительности, уменьшения отходов и поддержания необходимой температуры переработки расплава применяют горячеканальные литниковые системы (далее ГКС). Особенности конструкции сопла, литников, литьевых форм для различных термопластов указаны в Приложении № 14.
|
|
Операции литья под давлением.
Операция литья под давлением в стационарные формы представляет собой периодический процесс переработки полимеров. Пластмасса пластифицируется в обогреваемом материальном цилиндре узла пластикации, а затем, посредством выступающего в качестве поршня шнека, впрыскивается в формующую полость литьевой формы. В процессе выдержки под давлением в полости формы расплав застывает и, по прошествии определенного времени охлаждения, извлекается в виде готового изделия.
Расчет продолжительности цикла по Приложению № 13.
Дата добавления: 2018-11-24; просмотров: 599; Мы поможем в написании вашей работы! |
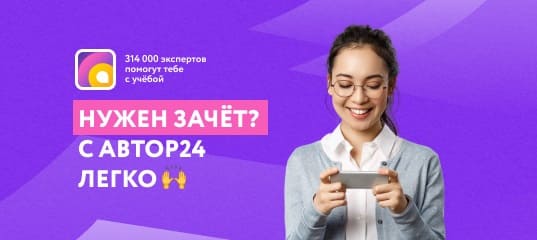
Мы поможем в написании ваших работ!