Проектирование монтажного стыка главной балки
По условиям перевозки (ограничение массы и габаритов) балка расчленяется по возможности на одинаковые отправочные элементы (марки). В разрезной балке ее элементы (стенка и пояса) стыкуются в одном сечении (универсальный стык). В зависимости от пролета и грузоподъемности транспортных средств главная балка может быть разбита на два или три отправочных элемента (рис. 5.12).
Монтажные стыки выполняются сварными или на высокопрочных болтах. В курсовой работе необходимо рассмотреть оба варианта стыка. Чертеж монтажного стыка на болтах можно отобразить только в пояснительной записке.
а) б)
Рис. 5.12. Возможное деление главной балки на отправочные элементы
При выполнении стыка в середине пролета изгибающий момент максимальный и соответственно максимальные нормальные напряжения σ близки к расчетному сопротивлению основного металла R y. При расположении стыка в 1/3 пролета (изгибающий момент Mmax к опоре уменьшается) нормальные напряжения σ могут оказаться меньше 0,85R y.
Монтажный стык на сварке
Стык элементов балки осуществляется стыковыми швами (рис. 5.13). Расчетные сопротивления сварных соединений для любого вида сварки принимаются (см. табл. 2.6): при сжатии соединения независимо от методов контроля качества швов R wy = R y; при растяжении и изгибе с физическим контролем качества швов R wy = R y и R wy = 0,85R y, если физические методы контроля не используются.
|
|
На монтаже применение физических способов контроля затруднено, поэтому расчет растянутого стыкового соединения производится по его пониженному расчетному сопротивлению. Сжатый верхний пояс и стенка соединяются прямым швом, растянутый пояс – косым швом для увеличения длины шва, так как действительное напряжение в поясе σ превышает R wy.
Для обеспечения равнопрочности сварного стыка и основного сечения нижнего пояса достаточен его скос с наклоном реза 2:1.
Монтажный стык выполняется ручной сваркой, материалы для сварки выбираются по табл. 2.5. Для сварки монтажного стыка применяют электроды с индексом А (Э42А), обеспечивающие повышенную пластичность наплавленного металла.
Рис. 5.13. Монтажный стык главной балки на сварке
Для обеспечения качественного соединения при ручной сварке элементов толщиной более 8 – 10 мм производится V-образная разделка кромок, начало и конец шва выводятся на специальные технологические планки.
Для уменьшения сварочных напряжений соблюдается определенный порядок сварки (на рис. 5.13 показан цифрами): сначала сваривают поперечные стыковые швы стенки 1, поясов 2 и 3, имеющие наибольшую поперечную усадку, последними заваривают угловые швы 4 и 5, имеющие небольшую продольную усадку. Оставленные незаверенными на заводе участки поясных швов длиной около 500 мм дают возможность поясным листам несколько вытянуться при усадке швов 2 и 3. Это также позволяет при монтаже совместить торцы свариваемых элементов отправочных марок, имеющих отклонение размеров в пределах технологических допусков.
|
|
Монтажный стык на высокопрочных болтах
Монтажные стыки на высокопрочных болтах выполняются с накладками (по три на каждом поясе и по две на стенке (рис. 5.14).
Усилие с одного элемента на другой передается за счет сил трения, возникающих между соприкасающимися плоскостями, стянутыми высокопрочными болтами. Площади сечения накладок должны быть не меньше площади сечения перекрываемого ими элемента. Наиболее применяемые в конструкциях средней мощности диаметры высокопрочных болтов и их площади сечения приведены в табл. 5.11.
Рис. 5.14. Монтажный стык главной балки на высокопрочных болтах
Таблица 5.11
Площади сечения болтов
d, мм | 16 | (18) | 20 | (22) | 24 | (27) | 30 | 36 | 42 |
A b, см2 | 2,01 | 2,54 | 3,14 | 3,80 | 4,52 | 5,72 | 7,06 | 10,17 | 13,85 |
A bn, см2 | 1,57 | 1,92 | 2,45 | 3,03 | 3,53 | 4,59 | 5,61 | 8,16 | 11,20 |
П р и м е ч а н и е. Размеры, заключенные в скобках, не рекомендуется применять в конструкциях.
|
|
Диаметры болтов во фрикционном соединении рекомендуется принимать не менее толщины наиболее толстого из соединяемых элементов. При большом количестве болтов в соединении их диаметр назначают возможно большим.
При выполнении стыка на высокопрочных болтах рекомендуется принимать один диаметр болтов для поясов и стенки.
Принимаем болты d b = 24 мм. Диаметр отверстия d под болт делается на 1 – 4 мм больше d b. Назначаем отверстие d = 26 мм.
Размещение болтов производится согласно требованиям, приведенным в табл. 3.9.
Минимальное расстояние между центрами болтов (шаг болтов) в расчетных соединениях определяется условиями прочности основного металла и принимается в любом направлении равным amin = 2,5d = 2,5 · 26 = 65 мм.
Принимаем а = 70 мм.
Максимальное расстояние между болтами определяется устойчивостью сжатых частей элементов в промежутках между болтами (в крайних рядах при отсутствии окаймляющих уголков amax ≤ 12tmin = 12 · 10 = 120 мм, где tmin– толщина наиболее тонкого наружного элемента) и обеспечением плотности соединения:
Минимальное расстояние от центра болта до края элемента для высокопрочных болтов в любом направлении усилия
|
|
сmin ≥ 1,3d = 1,3 · 26 = 33,8 мм.
Принимаем с = 50 мм. Ширина верхней накладки пояса принимается равной ширине пояса балки b nf = b f = 450 мм.
Ширина каждой нижней накладки пояса определяется:
b ′ nf = [b f – (t w + 2k f + 2Δ)] / 2 = [450 – (12 + 2 ∙ 7 + 2 ∙ 10)] / 2 = 202 мм,
где Δ = 10 – 15 мм – конструктивный зазор.
Толщина каждой накладки пояса
t nf = t f /2 + 2 = 25 / 2 + 2 = 14,5 мм.
Принимаем верхнюю накладку из листа 450´14 мм с площадью сечения А nf = 63 см2 и две нижних накладки из листа 200´14 мм с площадью сечения А ′ nf = 28 см2.
Суммарная площадь накладок
А n = А nf + 2А ′ nf = 63 + 2 ∙ 28 = 119 см2 > А f = 112,5 см2.
Горизонтальные болты располагаем в 4 ряда на одной полунакладке.
Определяем длину двух вертикальных накладок:
l nw = h w – 2(t nf + Δ) = 1500 – 2 (14 + 10) = 1450 мм.
Ширина вертикальных накладок
b nw = 2а + δ + 4c = 2 · 70 + 10 + 4 · 50 = 350 мм,
где δ = 10 мм – зазор между элементами.
Толщину каждой вертикальной накладки t nw принимаем равной толщине стенки t w за вычетом 2 – 4 мм, но не менее 6 мм (t nw = 10 мм).
Минимальное количество вертикальных рядов принимается равным двум. Расстояния между вертикальными рядами болтов принимаются минимальными, между горизонтальными – близкими к максимальным, количество горизонтальных рядов рекомендуется назначать четным.
Максимальное расстояние между крайними горизонтальными рядами болтов (с учетом расстояния до края элемента с = 50 мм)
а1= 1450 – 2 ∙ 50 = 1350 мм.
Таблица 5.12
Дата добавления: 2018-10-27; просмотров: 1473; Мы поможем в написании вашей работы! |
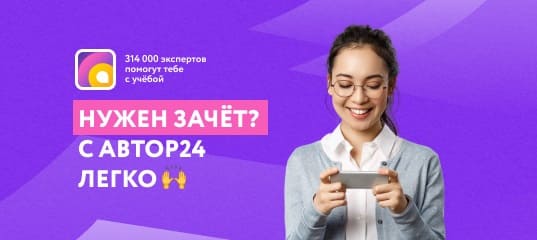
Мы поможем в написании ваших работ!