Термообработка инструмента, втулок полуосей легковых автомобилей
Восстановление постановкой дополнительных ремонтных деталей; Если износилась концевая шейка вала, то ее обрабатывают под меньший размер и напрессовывают ремонтную втулку, изготовленную из того же материала, что и вал. После напрессовки втулку (по наружному диаметру) обрабатывают. под номинальный размер концевой шейки вала. Толщина втулки, изготовленной из стали, не менее 2,0— 2,5 мм.
Чтобы втулка не провертывалась на валу, ее по торцу раскернивают или засверливают и приваривают точечной дуговой сваркой. При необходимости повысить твердость перед напрессовкой втулку подвергают термической обработке.
Если значительно износилось отверстие (в картере коробки передач, ступице колеса и т. д.), его обрабатывают под больший размер и запрессовывают втулку. Толщина стальной втулки не менее 2,0—2,5 мм, чугунной — примерно в два раза больше. Для повышения твердости втулку термически обрабатывают. Внутренний диаметр втулки обрабатывают под номинальный размер отверстия детали. Запрессованную втулку рекомендуется застопорить винтами или штифтами.
Резьбовое отверстие (отверстие для свечи зажигания в головке цилиндров и др.), если его стенки имеют достаточную толщину, восстанавливают постановкой ввертыша. Для этого отверстие с изношенной резьбой рассверливают сверлом диаметром на 5—6 мм больше наружного диаметра резьбы.
В новом отверстии нарезают резьбу и в него ввертывают ввертыш — резьбовую втулку. Выступающую часть ввертыша запиливают и зачищают. В центре ввертыша выполняют резьбовое отверстие с номинальной резьбой. Для предотвращения провертывания ввертыш можно раскернить, приварить, застопорить штифтом или винтом.
|
|
У деталей, имеющих несколько рабочих поверхностей, подверженных разной степени износа, возможна замена части детали. Например, у полуоси сильно изнашиваются шлицы по толщине. В таком случае шлицевой конец полуоси отрезают и изготовляют новый конец (из той же стали, что и полуось).
Изготовленный конец приваривают стыковой сваркой к полуоси, полуось правят, обрабатывают приваренный конец, нарезают на нем шлицы и термически обрабатывают.
Восстановление деталей слесарно-механической обработкой. В практике ремонта автомобилей слесарно-механическую обработку применяют для устранения раковин, образующихся на рабочей поверхности седел клапанов (шлифование, притирка или фрезерование), заделки трещин на стенках рубашки охлаждения и пробоин (штифтовка, постановка заплат), подгонки внутренних отверстий втулок (развертывание), восстановления изношенной резьбы на болтах, шпильках, в гайках (прогонка резьбы метчиками и плашками) и т. д.
|
|
Оснастка, гибка, пробивка, прошивка металла при изготовлении инструмента, приспособлений и изделий
Деформация – изменение формы и размеров твердого тела под воздействием приложенных к нему нагрузок. Различают деформацию упругую (обратимую) и пластическую (необратимую)
Упругой деформацией называют такую, которая исчезает после снятия нагрузок, т.е. тело восстанавливает свою первоначальную форму. Пластическая деформация остается после снятия внешней нагрузке, (тело не восстанавливает первоначальную форму и размеры).
Пластическая деформация сопровождается смещением одной части кристалла относительно другой на расстояние, значительно превышающие расстояния между атомами в кристаллической решетке металлов и сплавов.
Величина пластической деформации не безгранична, при определенных ее значениях может начинаться разрушение металла.
В зависимости от температурно-скоростных условий деформирования различают холодную и горячую деформацию.
Холодная деформация характеризуется изменением формы зерен, которые вытягиваются в направлении наиболее интенсивного течения металла. При холодной деформации формоизменение сопровождается изменением механических и физико-химических свойств металла. Это явление называют упрочнением (наклепом). Изменение механических свойств состоит в том, что при холодной пластической деформации по мере ее увеличения возрастают характеристики прочности, а характеристики снижаются. Металл становится более твердым, но мене пластичным. Упрочнение возникает вследствие поворота плоскостей скольжения, увеличение искажений кристаллической решетки в процессе холодного деформирования(накопление дислокаций у границы зерен).
|
|
Изменение, внесенные холодной деформацией в структуру и свойства металла не обратимы. Они могут быть устранены, например с помощью термической обработки (отжигом).
В этом случае происходит перестройка, при которой за счет дополнительной тепловой энергии, увеличивается подвижность атомов и в твердом металле без фазовых превращений из множества центров растут новый зерна заменяющие собой вытянутые “деформированные зерна”.
Явление зарождения и роста, новых равнооснах зерен взамен деформированных, вытянутых, происходящее при определенных температурах, называется рекристаллизацией. Для чистых металлов рекристаллизация начинается при абсолютной температуре, равной 0,4 абсолютной температуре плавления металла.
|
|
Горячая обработка металлов давлением производится при температурах, значительно превышающих температуру их рекристаллизации, когда скорость процесса упрочнения, вызванного деформацией. При этом микроструктура металла после обработки давлением оказывается равноосной, без следов упрочнения. Зерна в металле получаются тем мельче, чем больше степень деформации.
Перед горячей обработкой давлением металлы и стали нагревают до определенной температуры (начало горячей обработки давлением) для повышения их пластичности и уменьшения сопротивления деформации. Однако в процессе обработки температура металла понижается. Минимальная температура, при которой можно производить обработку, называется температурой окончания обработки давлением. Область температуры между началом и окончанием, в которой металл или сплав обладает наилучшей пластичностью, наименьшей склонностью к росту зерна и минимальным сопротивлением деформированию, называют температурным интервалов горячей обработки давлением.
При этом температура нагрева металла выбирается такой, чтобы не возник, пережег либо перегрев. Пережег, характеризуется окислением металла на границе зерен, в результате чего он становится хрупким и при ударе разрушается. Перегрев сопровождается резким ростом размеров зерен, вследствие чего ухудшаются механические свойства.
Каждый металл и сплав имеет свой строго определенный температурный интервал горячей обработки давлением. Например, алюминиевый сплав АК4 – 470-350С; медный сплав БрАЖМц – 900-750С; титановый сплав Вт8 -1100-900С; сталь 45 – 1200-750С.
Заготовка должна быть равномерно нагрета по всему объему до требуемой температуры. Нагрев осуществляется в различных печах и нагревательных устройствах. Выбор способа нагрева заготовок определяется технико-экономических соображениями.
Способы обработки металлов давлением
К основным способам обработки металлов давлением относятся процессы прокатки, волочения, прессования (выдавливания), свободной ковки, горячей и холодной объемной штамповки, а также листовой или холодной штамповки.
Гибка – образование или изменение углов между частями заготовки или придание ей криволинейной формы.
Рисунок 14. Гибка
Гибка листового металла осуществляется в результате упруго-пластической деформации. При гибке происходит растяжение наружных и сжатие внутренних слоев материала изгибаемой детали. После гибки растянутые и сжатые слои стремятся возвратиться в исходное положение под действием упругих сил. В следствие этого форма детали после гибки не будет соответствовать форме штампа на некоторый угол за счет упругости, что необходимо учитывать при изготовлении инструмента.
Дата добавления: 2018-09-23; просмотров: 751; Мы поможем в написании вашей работы! |
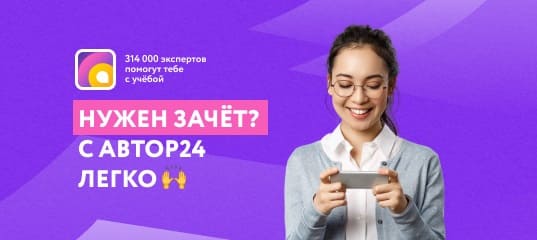
Мы поможем в написании ваших работ!