Современное представление об образовании Н и Г.
При нагревании сопропеловых сланцев до 150-170 С начинается слабое термическое разложение органического вещества, о чем свидетельствует повышение выхода экстактивных веществ. При 200 С образовывается больше экстрактивных веществ, при 370-400С после нагревании в течении 1ч до 60-80% органического вещества переходит в растворимое состояние, образуется асфальто-смолистые вещества, содержащие все основные классы УВ, а так же газы СО2, СН4, Н2S и пирогенетическую воду. В принципе такой же процесс термического либо термокаталического разложения происходит и в природных условиях при погружении отложений, содержащих сопропелевое органическое вещество, под накаплившимися над ними более молодыми осадки. В отличии от лабораторных условий в природных условиях процесс протекает крайне медленно со скоростью погружения осадков обычно от 50-100м/1 млн. лет. Опускание на глубину 2-3 км, где расположена большая часть залежей Н и где t=150-160С процесс осуществляется за 10-60 млн лет. Главная фаза нефтеобразования успевает реализоваться даже в «молодых» осадках с возрастом 10-20 млн лет и тем более он реализуется в более древних отложениях. Процесс образования Н в природных условиях в масштабе геологического времени реализуется при t в 2-2,5 раза более низкой, чем в лабораторных условиях.
Термический крекинг тяжелых нефтяных фракций.
Процесс термического крекинга применяется в промышленности с 1912 г. Он предназначается для получения автомобильного бензина. В настоящее время термический крекинг тяжелых остатков переработки нефти проводят с целью получения вакуумного газолья, а также мазута. Вариант термического крекинга, направленый на снижение вязкости кательного топлива получил название висбрекинг. Его осуществляют при t =450-480С и под Р = 2-5 МПа. Сырьем служат нефтяные остатки: полугудроны, гудруны, тяжелые газойли. Основные продукты висбрекинга: СО2, крекинговый бензин, крекинговый остаток. Газ термического крекинга содержит С1-С3. СО2 применяют как топливо. Бензин содержит много алкенов, поэтому он характеризуются низкой стабильностью (60-66 по моторному методу). Керосино газойливая фракция 200-250С явл-ся ценным компонентом флотского мазута, после гидроочистки его применяют как компонент дизельного топлива. Термогазойль t кип= 350С. Для получения маловязкого котельного топлива в крекинг-остатке оставляют количество низкомалекулярных газойливых фракций. При изменении технологии висбрекинга можно понизить t застывания крекинг-остатка. Включение этого процесса в схему переработки Н позволяет увеличить отбор газойля и получить топливо.
|
|
Пиролиз.
|
|
Основное назначение процесса пиролиза углеводородного сырья – это получение низкомолекулярных алкенов (непредельных углеводородов). Процесс проводят при t=800 – 9000С и при давлении близким к атмосферному. При снижении парциального давления углеводородов сырьё обычно разбавляют водяным паром. Оптимальным сырьём при производстве этилена является этан. Выход этилена при этом достигает 80% . Значительный выход этилена наблюдается также при пиролизе алканов нормального строения. Из пропана получают до 48% этилена, из бутана до 45%. При пиролизе разветвлённых алканов образуется преимущественно Алкены С3-С4, а также алкодиены. Выход низкомолекулярных алкенов при пиролизе циклоалканов и аренов незначительно. В России основную часть этилена получают пиролизом прямогонных бензинов и газойлей. При пиролизе керосино – газойльных фракций выход этилена составляет 16-23%, выход пропилена около 15%, в жидких продуктах около 50%. Жидкие продукты содержат алкены, циклоалканы, алкадиены, арены и другие компоненты. В связи с непредельным ростом цен на прямогонные бензины и их недостаточными ресурсами всё более широкое применение, как сырьё пиролиза находит вторичные продукты пиролиза. В балансе сырья производства этилена и пропилена ожидается увеличение доли природного и попутного газа, а также бензиновых фракций, выделившихся из газа конденсатов.
|
|
38) Коксование.
Назначение процесса коксования – это получение нефтяного кокса и дистиллята, имеющего широкий фракционный состав. В качестве сырья нефтяного кокса наиболее используются отбензиненная нефть, остатки первичной переработки (мазуты, полугудроны), продукты вторичной переработки, тяжёлые газойли каталитического крекинга, смолы пиролиза, природного асфальта. Существуют несколько модифицирующих процессов, а именно процесс коксования в кубах, замедленное коксование в необогреваемых камерах и коксование в псевдосжиженом слое порошкообразногоо кокса. Наиболее широкое распространение получил полунепредельный процесс в установках замедленного коксования. Замедление коксования нефтяных остатков протекает при t =490-505С, и давлении = 0,2-0,3МПа. В результате коксования, кроме нефтяного кокса получают газ, бензин, а также средние и тяжёлые коксованные дистилляты. Выход продуктов и их количество зависит от химического и фракционного состава сырья и от условий коксований. Выход кокса из остатков первичной переработки нефтяного состава 15-25%, а из вторичных 30-35%. Вместе с коксом образуется значительное количество целых жидких и газообразных продуктов. Свойства этих продуктов близки к характерным продуктам термического крекинга. Суммарный выход жидких и газообразных продуктов достигает 70% в расчете на исходное сырьё. Коксование тяжёлых нефтяных остатков является одним из наиболее экономичных способов их превращения в дистиллятное сырьё. Наибольшая экономичность и эффективность процесса коксования наблюдается при квалифицированном использовании всех образующихся продуктов.
|
|
Каталитический крекинг.
Это процесс каталитического деструктивного превращения тяжёлых дистиллятных нефтяных фракций в моторные топлива и сырьё нефтехимии, а также производства технического углерода и кокса. Процесс протекает в присутствии алюмосиликатов при t=450-530 и при давлении = 0,07-0,3МПа. Существует несколько процессов, протекающих при каталитическом крекинге, заключающихся в следующих реакциях: расщепление высокомолекулярных углеводородов (крекинг), изомеризация, дегидрирование циклоалканов в арены. Деструкция тяжёлого нефтяного сырья приводит к образованию светлых моторных топлив, наибольшее значение из которых имеет бензин. Реализация всех типов реакций приводит к повышению октанового числа бензина. При одинаковой структуре октановое число углеводородов возрастёт по мере уменьшения молекулярной массы. Октановые числа циклоалканов выше, чем у алканов нормального строения, а октановые числа аренов выше, чем у циклоалканов и алканов.
Каталитический риформинг.
Это процесс, предназначенный для повышения детонационной стойкости бензинов и для получения аренов, главным образом бензола, толуола, ксилола. Процесс осуществляется при повышенной температуре 5000С и под давлением 1,5-4МПа. Процесс проводят на бифункциональном катализаторе, который сочетает функции кислотную и гидрирующую. Кислотную функцию обычно выполняет оксид алюминия, а дегидратационную функцию выполняют МЕ S группы и платина. Химич. основы процессов. В основе каталитического риформинга лежат 3 типа реакций 1) ароматически исходного сырья путём дегидроциклических алканов и дегидрирующие циклогексанов. 2) изомеризация углеводородов. 3) гидрокрекинг. Как и при каталитическом крекинге, каталитическом риформинге осуществление всех 3-х реакций приводит к увеличению октанового числа бензина.
Дата добавления: 2018-09-23; просмотров: 290; Мы поможем в написании вашей работы! |
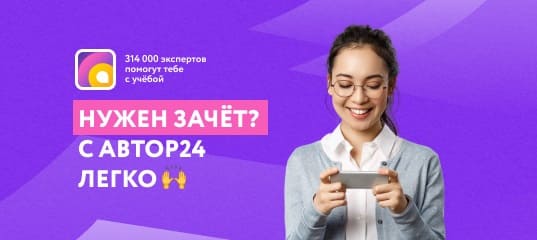
Мы поможем в написании ваших работ!