Расчет и проектирование сварочного контура машины
Введение
Под контактной сваркой понимают процесс образования неразъёмных соединений конструкционных металлов в результате их кратковременного нагрева электрическим током и пластического деформирования усилия сжатия.
Соединение свариваемых деталей при контактной сварке происходит путём образования связей между атомными агрегатами в зоне контакта этих деталей. При этом для образования физического контакта и активации соединяемых поверхностей затрачивается тепловая и механическая энергия, подводимая извне.
Точечная сварка – способ контактной сварки, при котором детали свариваются по отдельным ограниченным поверхностям касания (по ряду точек).
Область применения контактной сварки чрезвычайно широка – от крупногабаритных строительных конструкций до миниатюрных полупроводниковых устройств и плёночных микросхем. По имеющимся данным в настоящее время около 30% всех сварных соединений выполняются различными способами контактной сварки.
Контактной сваркой можно успешно соединять практически все известные конструкционные материалы.
Точечная сварка – наиболее распространенный способ, на долю которого приходится около 80% всех соединений, выполняемых контактной сваркой. Этот способ сварки широко используется в автомобиле – и вагоностроении, строительстве, радиоэлектронике и т.д. Например, в конструкциях современных лайнеров насчитывается несколько миллионов сварных точек, легковых автомобилей – 5000 точек. Диапазон свариваемых толщин – от нескольких микрометров до 10-30мм. Точечной сваркой соединяются элементы жесткостей и крепёжные детали с листами, тонкостенными оболочками и панелями.
|
|
Контактная сварка, применяется, как правило, в крупносерийном и массовом производстве. Это обусловлено высокой производительностью машин контактной сварки, легкостью механизации и автоматизации процесса сварки, а также стоимостью оборудования.
Назначение, описание конструкции изделия и условия его работы
Изделие представляет собой лист металла свёрнутый в трубу, свариваемый с нахлестом 18мм.
Данная конструкция при ее использовании не воспринимает никаких больших нагрузок. Герметичность конструкции не требуется, поэтому сварку можно производить на точечных машинах. Данное изделие применяется как кожух, внутри которого проходит вал, передающий вращающий момент от двигателя к ленточному конвейеру.
Характеристика материала изделия и оценка его свариваемости
Материал изделия - сталь 45 относится к классу среднеуглеродистых сталей обыкновенного качества. Сталь 45 содержит: углерода 0,42-0,50%; марганца 0,35-0,65%; кремния 0,17-0,37%; фосфора 0,040%; серы 0,040%; хрома 0,25%; никеля 0,25%; меди 0,25%.
|
|
Под технологической свариваемостью понимают способность металлов образовывать прочные соединения без существенного ухудшения их технических свойств в самом соединении и в прилегающей к нему околошовной зоне.
Свариваемость является переменным свойством материала. С усовершенствованием технологий и оборудования можно улучшить свариваемость материалов.
Расчет режимов сварки
Величина сварочного тока, необходимая для образования сварной точки, может быть определена по закону Джоуля-Ленца.
Iсв,А. – действующее значение тока;
Qээ, Дж. – теплота, выделяемая при протекании тока через участок электрод- электрод;
mr – коэффициент, учитывающий изменения сопротивления во время сварки.
mr=1,1 – среднеуглеродистых сталей.
Rд.кон. = 90*10-6 – сопротивление детали к концу нагрева;
tсв.=0,15 – технологически целесообразное время сварки;
где
энергия, затрачиваемая при нагреве до температуры плавления столбика металла свариваемых высотой 2d и диаметром основания dя = 5мм.
с=461Дж/(кг*°К) – теплоёмкость;
г=7,8*103 кг/м3 – плотность свариваемого материала;
|
|
∆Тпл = Тпл.-273°=1803-273=1530°К;
d=1,2мм – толщина одной пластины;
dя = 5мм – диаметр литого ядра сварной точки;
dя = dк – диаметр контакта электрода.
теплота, расходуемая на нагрев до Тпл./4 °К свариваемого металла в виде
кольца шириной Х2.
где К1≈0,8 – коэффициент учитывающий, что средняя температура кольца ниже средней температуры ∆Тпл./4 в связи со сложным распределением температуры;
Х2 – ширина кольца окружающего ядра.
Для среднеуглеродистых сталей Х2=1,2* 10-2=1,2*
*10-2=0,004м.
потери теплоты в электроде при нагреве условного цилиндра высотой Х3 до средней температуры Тэ=∆Тпл./8
где сэ и гэ – теплоёмкость и плотность металла электрода ≈3,3*106Дж.
Х3 – определяется временем сварки и температуропроводностью, м.
Следовательно,
Сопротивление шунта находится по формуле:
где Кп=1,1 – коэффициент поверхностного эффекта [1,c.9],
ст =80*10-8 Ом*м – удельное электрическое сопротивление материала изделия при температуре 0,2*Тпл.
h/l=1,2 [1,c.10], где h-ширина полосы по которой шунтируется ток; м.
l-шаг между точками; м.
h=1,2*40*10-3=48*10-3м
Ток шунтируется через ранее сваренную точку
Ток во вторичном контуре машины:
|
|
Эквивалентное сопротивление:
Расчет и проектирование сварочного контура машины
Сварочный контур – это система токоведущих элементов и электрических контактов, обеспечивающих подвод тока от вторичного витка трансформатора к свариваемым деталям и передачу к ним усилия сжатия.
рис.2 – Сварочный контур машины
Габаритные размеры контура: полный вылет L=500мм, Н=100мм.
Определяем сечения элементов контура, сечение q элемента контура и площадь контакта рассчитывают по допустимой плотности тока j:
ПВ=50% - относительная продолжительность включения.
j – допустимая плотность тока, А/мм2
По табл. 8 (1,с.20) выбираем j:
для электродов с полым сечением 20-30 А/мм2;
для хобота 2-3 А/мм2;
Определяем поперечное сечение хобота
где - вторичный ток на номинальной ступени.
Определяем расчетную нагрузку:
где Рс=6*105Н/м2 – давление сжатого воздуха.
dц – диаметр пневмоцилиндра
Предварительно определяется dц
Рсв.=1200Н – усилие свариваемых деталей;
Р=3,5*105
Принимается по ГОСТ dц=0,080м.
Из электрического расчета определяем диаметр хобота
из конструктивных соображений принимаем dx=120мм.
Проверяем на прочность
где [у]=290 Мпа – предельное напряжение для меди М1.
W=0.1*dx3=0.1*0.123=1,7*10-4 м3.
М=Fp*500*10-3=3014.4*500*10-3=1507,2 H*м.
Проверка на жесткость
- Момент инерции хобота
Е=0,8*109 Н/м2
Дата добавления: 2018-09-22; просмотров: 279; Мы поможем в написании вашей работы! |
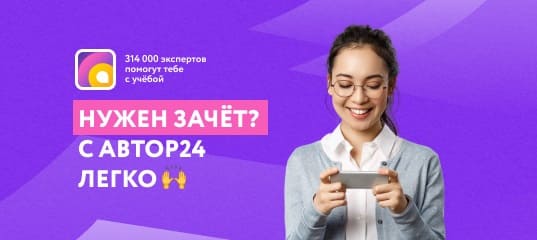
Мы поможем в написании ваших работ!