Підвищення надійності машини при експлуатації.
Надійність машин в процесі експлуатації залежить багато в чому від умов і режимів їх роботи. Істотний вплив на надійність машин, які функціонують зовні заводських приміщень, надає навколишнє середовище (температура, вологість, запиленість і ін.).
Машини іноді працюють з перевантаженнями, мають непостійні цикли роботи, у ряді випадків обслуговуються операторами невисокої кваліфікації або з відступом від інструкції з експлуатації.
Ці і інші причини порушень умов і режимів роботи машин, що мають місце при експлуатації, приводять до виникнення відмов раніше, ніж це встановлено ресурсом машини. Тому дотримання вимог інструкції по монтажу і експлуатації — одна з основних умов досягнення надійної роботи машини.
Жоден виріб, тим більше складна сучасна машина, не може обійтися без ремонту і технічного обслуговування, які є невід'ємними етапами процесу експлуатації машини і повинні забезпечити протягом всього періоду експлуатації необхідний рівень безвідмовності при якнайменших витратах часу і засобів.
Процес зношування деталей машин при експлуатації визначається трьома періодами (рис. 2): I — припрацюванням, при якому темп зношування підвищений за рахунок стирання початкових нерівностей або за рахунок перекосу поверхонь спряжених деталей; II — сталим, при якому відбувається природна зміна форм і розмірів деталей в процесі роботи машини; III — катастрофічним, характеризується різким наростанням інтенсивності зносу зважаючи на неприступні зміни в зв'язаних деталях. В цей період відбувається відмова вузла (машини).
|
|
Період нормальної експлуатації повністю (напрацювання на відмову) навіть у однотипних деталей і вузлів машин неоднаковий через дію різних випадкових чинників (попадання абразиву, води і т. д.).
Рисунок 2 – Характерний вид розвитку і розсіювання темпу зносу в процесі напрацювання.
Графік цього процесу має форму віяла (заштрихована область на рисунку 2) через розсіювання інтенсивності зношування з часом. Якщо С — граничний допуск на знос, то напрацювання для одних і тих же деталей в різних умовах експлуатації різне (t2>>t1). Таке розсіювання має велике значення для встановлення допусків на технічне обслуговування і ремонт машини.
На величину напрацювання, а отже, і на періодичність ремонтів впливає і початковий розмір деталі, одержаний при її виготовленні. Якщо, наприклад, деталь зношуватиметься не з середини номінального розміру, як показано на рисунку 2 (точка 0), а з верхнього (точка +1) або нижнього (точка —1) допуску, то картина досягнення межі С різко зміниться. У разі коли знос починається з точки +1, момент досягнення межі наступає швидко (точка 0 переноситься в точку +1); в другому випадку — повільно. Отже, при виготовленні деталей з мінусовими допусками не тільки знижується їх матеріаломісткість в процесі виробництва, але і підвищується довговічність, що приводить до зниження експлуатаційної матеріаломісткості.
|
|
Знаючи очікуваний характер розвитку зносу деталі машини в процесі експлуатації, можна встановити раціональні терміни проведення ремонту машини (рис. 3).
На рисунку 3 по осі ординат відкладені номери деталей, що зношуються, а по осі абсцис — значення напрацювання, яких досягають деталі з урахуванням розсіювання темпів зношування (розсіювання показано штриховими лініями). Вертикальні заштриховані області визначають межі профілактичних ремонтів і перевірок. З графіка видно, що деталь 2 не «дотягує» по гарантійному терміну служби до першого профілактичного ремонту П1. Деталі 1 і 3 укладаються в міжремонтний період. Деталь 4 має найбільше напрацювання і може бути змінена після другого ремонту. Деталь 5 забезпечує надійну роботу до профілактичного ремонту П2, але з урахуванням величини розсіювання може досягти граничного зносу раніше моменту настання ремонту П2. Деталь 6 повинна бути замінена при ремонті П1, оскільки вона вийде з ладу раніше настання ремонту П2.
|
|
Рисунок 3 – Графік оцінки терміну служби деталей.
Одержаний аналіз показує, що для безвідмовної роботи виробу до першого профілактичного ремонту необхідно підвищити довговічність деталі 2 або наблизити терміни першого ремонту до величини напрацювання цієї деталі. В другому випадку, природно, зменшиться міжремонтний період і збільшиться вартість експлуатації виробу. Оптимальний варіант рішення може бути знайдений при зіставленні витрат на підвищення надійності необхідної деталі і проведення додаткового профілактичного ремонту. Оптимальний міжремонтний період для машини повинен забезпечити мінімальне значення відносних ремонтних втрат за рахунок раціонального співвідношення між об'ємами робіт при періодичних ремонтах і міжремонтному обслуговуванні.
Скорочення міжремонтних періодів недоцільне не тільки з економічної точки зору, але і з погляду надійності машини. Передчасне розбирання зв'язаних деталей приводить після збірки вузла знову до прироблення поверхонь, яке характеризується інтенсивним зношуванням. Якщо розбирання все ж таки необхідне (наприклад, при технічному обслуговуванні), то деталі заздалегідь розмічають, з тим щоб після розбирання встановити їх точно на свої колишні місця.
|
|
Звичайно для експлуатації машин передбачають запасні частини, номенклатура яких відображає характер типових пошкоджень в машині, а їх кількість — термін служби замінюваних деталей. Наявність запасних частин значно скорочує час і вартість ремонту і, як правило, повністю відновлює втрачену працездатність машини, оскільки ці деталі виготовлені при тій же технології, що і встановлені в машині.
Проведення планових ремонтів або відновних робіт, виконуваних в умовах експлуатації машин за більш простою технологією, ніж при масовому виробництві, звичайно не забезпечує підвищення технічного стану машини до початкової величини. Внутрішні структурні зміни матеріалу деталей при цьому знижують вірогідність безвідмовної роботи до 5—40 %.
У зв'язку з цим при виготовленні запасних частин і проведенні відновних робіт в умовах експлуатації машин доцільно враховувати ряд особливостей і технологічних прийомів. Підвищення точності виготовлення деталей машин має велике значення при їх експлуатації. Недостатня точність при виготовленні вимагає великого об'єму підгоночних робіт, підвищеної витрати інструменту. Це ускладнює взаємозамінність деталей, здорожує ремонтні роботи.
Шорсткість поверхні робить великий вплив на швидкість зношування. Зокрема, при роботі вузлів або зв'язаних деталей з мастилом не слід прагнути одержувати на етапі відновлення деталей дуже чисту поверхню в зоні контакту. Так, операція полірування сталі і чавуну погіршує адсорбцію мастила за рахунок заволікання пір матеріалу. Для підвищення шорсткості проводять поверхні, що труїться 10—25 %-м розчином азотної кислоти протягом 3 хв з подальшим пропитуванням деталей в гарячому маслі протягом 15 хв.
Іноді виявляється, що виготовлені машини або її вузлів за своїми технічними даними не можуть забезпечити необхідні показники надійності технологічної лінії або самої машини. В цьому випадку застосовують резервування, тобто вводять надмірні машини, вузли або деталі. Цей спосіб дозволяє створювати систему машин і апаратів, надійність якої вище надійності вхідних складових. Наприклад, в хімічній, нафтовій і інших галузях промисловості встановлюють резервні насоси. Їх включення у ряді випадків проводиться автоматично при відмові основного насоса. Матеріаломісткість системи виявляється нижче, ніж матеріаломісткість одного насоса, який повинен забезпечити безвідмовну роботу протягом довгого часу.
Таким чином, підтримка і відновлення працездатності машин є складним процесом, залежним від багатьох чинників: конструкції машини, методів її експлуатації, організації системи ремонту і технічного обслуговування, економічних аспектів і ін.
Дата добавления: 2018-08-06; просмотров: 445; Мы поможем в написании вашей работы! |
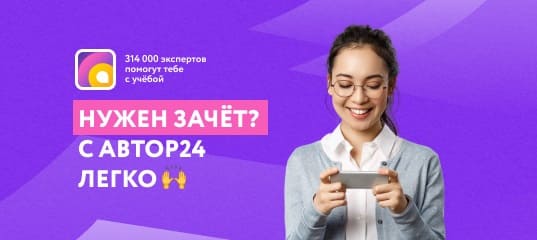
Мы поможем в написании ваших работ!