Определение расходов на металл.
Цены на листы1500х1500х8 мм 4шт-3190 р.
Цены на листы1500х2000х8мм 2шт-2485 р.
Цены на листы 200х500х8мм 4 шт-1369 р.
Цена на лист 500х500х3мм 1шт-528 р.
Цены профилированных труб 60х80х8 мм:
12000мм-1148 р.
600мм- 629 р.
Исходя из этих цен, можно определить общий расход на профилированные трубы:
.
Вывод: расход на металл равен – 25511 р.
Определение расходов на заработную плату.
Сварочные работы, при изготовлении металлического погреба, выполняются сварщиком IV разряда. Часовая тарифная ставка такого сварщика, составляет - 62,5 р. Сварка данной конструкции длится 12,60 ч, исходя из этого можно определить заработную плату сварщика:
Так же, предусматривается доплата сварщику за вредные условия труда, а именно - 8% от суммы заработной платы:
Кроме того, устанавливается надбавка за профессиональное мастерство, для сварщика IV разряда – 16% от суммы заработной платы:
Помимо этого, сварщику выплачивается премия до 30% от суммы заработной платы:
Общая сумма, выплачиваемая сварщику IV разряда равна – 1468,4 р.
Слесарные работы и стропальные работы, при изготовленииметаллического погреба, выполняются слесарем-сборщиком IV разряда. Часовая тарифная ставка такого слесаря, составляет – 32,5 р. Время работы слесаря-сборщика, на изготовлении данной конструкции, составит – 12,60 ч:
Помимо этого, слесарю-сборщику выплачивается премия до 30% от суммы заработной платы:
Общая сумма, выплачиваемая слесарю-сборщику IV разряда равна – 704,34 р.
|
|
Исходя из рассчитанных зарплат рабочик, можно посчитать общий расход на заработную плату:
1468,4
Вывод: расход на заработную плату равен – р.
Общий расход на изготовление конструкции.
Расход на заработную плату равен – р
Расход на металл равен – 25511 р
Расход на электроэнергию равен – .
Расход на сварочные материалы равен - 2683 р.
Вывод: общий расход на изготовление металлического погреба равен – 32577.68
Контроль качества.
Контроль качества металлического погреба, выполняется несколькими методами:
1. Визуально измерительный метод контроля (ВИК). Визуальный контроль качества является первичным методом неразрушающей диагностики. ВИК сварных швов - это внешний осмотр достаточно крупных сварных конструкций, как невооруженным глазом, так и при помощи различных технических приспособлений для выявления более мелких дефектов, не поддающихся первоначальной визуализации, а также с использованием преобразователей визуальной информации в телеметрическую. С помощью данного метода, проверяются: габаритные размеры конструкции, кривизна в горизонтальной и вертикальной плоскостях (не более 25 мм), геометрические параметры шва, выявляются поверхностные дефекты (поры и трещины, подрезы, кратеры, прожоги, свищи, наплывы).
|
|
2. Капиллярный метод контроля.Капиллярная дефектоскопия - является одним из основных методов неразрушающего контроля и предназначена для обнаружения поверхностных и сквозных дефектов в объектах контроля, определения их расположения и их ориентации на поверхности. Капиллярный метод неразрушающего контроля основан на капиллярном проникновении внутрь дефекта индикаторных жидкостей, хорошо смачивающих материал объекта -поверхность контроля и последующей регистрации индикаторных следов (благодаря чему так же носит название цветная дефектоскопия).
При контроле красящий пенетрант наносится на контролируемую поверхность и благодаря своим особым качествам под действием капиллярных сил проникает в мельчайшие дефекты, имеющие выход на поверхность объекта контроля. Проявитель, наносимый на поверхность объекта контроля через некоторое время после осторожного удаления с поверхности пенетранта, растворяет находящийся внутри дефекта краситель и за счет диффузии “вытягивает” оставшийся в дефекте пенетрант на поверхность объекта контроля. Имеющиеся дефекты видны достаточно контрастно. Индикаторные следы в виде линий указывают на трещины или царапины, отдельные точки - на поры.
|
|
Процесс капиллярного контроля состоит из 5 этапов:
1. предварительная очистка поверхности;
Чтобы краситель мог проникнуть в дефекты на поверхности, ее предварительно следует очистить водой или органическим очистителем. Все загрязняющие вещества (масла, ржавчина, и т.п.) любые покрытия должны быть удалены с контролируемого участка. После этого поверхность высушивается, чтобы внутри дефекта не оставалось воды или очистителя.
2. нанесение пенетранта;
Пенетрант, обычно красного цвета, наносится на поверхность путем распыления или кистью, для хорошей пропитки и полного покрытия пенетрантом. Как правило, при температуре 5…50 °С, на время 5…30 мин.
3. удаление излишков пенетранта;
Избыток пенетранта удаляется протиркой салфеткой, промыванием водой, или тем же очистителем, что и на стадии предварительной очистки. При этом пенетрант должен быть удален только с поверхности контроля, но никак не из полости дефекта. Затем поверхность высушивается салфеткой без ворса или струей воздуха.
4. нанесение проявителя;
После просушки сразу же на поверхность контроля тонким ровным слоем наносится проявитель (обычно белого цвета).
|
|
5. контроль.
Выявление имеющихся дефектов начинается непосредственно после окончания процесса проявки. При контроле выявляются и регистрируются индикаторные следы. Интенсивность окраски которых говорит о глубине и ширине раскрытия дефекта, чем бледнее окраска, тем дефект мельче. Интенсивную окраску имеют глубокие трещины. После проведения контроля проявитель удаляется водой или очистителем.
Дефектоскопические материалы для цветной дефектоскопии выбирают в зависимости от требований, предъявляемых к контролируемому объекту, его состояния и условий контроля. Их укомплектовывают в целевые наборы, в которые входят полностью или частично взаимообусловленные совместимые дефектоскопические материалы. Совместимость дефектоскопических материалов в наборах или сочетаниях обязательна. Составы набора не должны ухудшать эксплуатационные качества материала контролируемого объекта.
3. Ультразвуковой метод контроля (УЗК)
Одним из основных методов неразрушающего контроля является ультразвуковой метод контроля (УЗК). С помощью данного метода контроля, определяют внутренние дефекты. Суть ультразвукового метода заключается в излучении в изделие и последующем принятии отраженных ультразвуковых колебаний с помощью специального оборудования - ультразвукового дефектоскопа и пьезоэлектропреобразователя и дальнейшем анализе полученных данных с целью определения наличия дефектов, а также их эквивалентного размера, формы (объёмный, плоскостной), вида и глубины залегания.
Параметры выявленных дефектов определяются с помощью ультразвуковых дефектоскопов. Так например, по времени распространения ультразвука в изделии определяют расстояние до дефекта, а по амплитуде отраженного импульса - его относительный размер.
На сегодняшний день существует пять основных методов УЗК: теневой, зеркально-теневой, зеркальный, дельта-метод и эхо-метод. Одним из самых распространённых методов ультразвукового контроля, является эхо-метод. В промышленности ультразвуковой контроль металла проводят, как правило, в диапазоне ультразвуковых волн от 0,5 МГц до 10 МГц.
Способы исправления дефектов
Практически в любом случае, самым действенным и надежным способом исправления вышеперечисленных дефектов станет удаление участка сварного соединения с изъяном и заваривание деталей заново (при наплывах, свищах, прожогах, шлаковых включениях). Это даст возможность избежать в дальнейшем проблем с перегниванием, коррозией, ломкостью изделия.
Исправление дефектов всегда зависит от каждого отдельного случая. Поэтому существуют способы, применимые к конкретным случаям. Например, для борьбы с подрезами и кратерами, следует применять зачистку с дополнительной подваркой шва и срезание лишнего металла.
Для устранения трещин применяют, помимо удаления проблемного участка и новой сварки, поверхностную кислородную или воздушно-духовую резку. Участки, на которых имеются поры, тоже вырезают и сваривают заново.
Для того чтобы избежать появления непроваров, следует соблюдать одинаковый температурный режим. Это даст возможность металлу в сварном соединении равномерно прогреться до начала сварочных работ и не смещать электроды от шва.
Нельзя выключать ток до того, как кромки изделия будут полностью сварены. Если всё же непровары образовались, необходимо вырезать поврежденный участок (вырубить или выстрогать), зачистить края и вновь заварить.
Дата добавления: 2018-08-06; просмотров: 316; Мы поможем в написании вашей работы! |
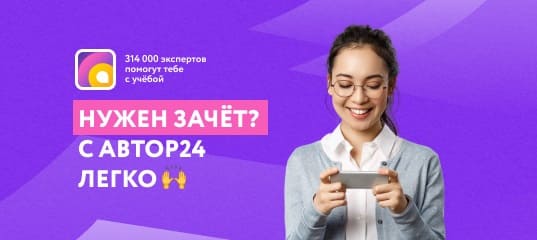
Мы поможем в написании ваших работ!