ВЫБОР И ОБОСНОВАНИЕ БУРОВОГО ОБОРУДОВАНИЯ НА ШАХТЕ ИМЕНИ «ДЕСЯТИЛЕТИЯ НЕЗАВИСИМОСТИ КАЗАХСТАНА»
Общее положение
К основным производственным процессам очистной выемки руды относят: отбойку руды, вторичное дробление, выпуск и доставку отбитой руды до откаточного горизонта, процессы поддержания очистного пространства. Доставка руды – перемещение рудной массы от забоя до этажных выработок, по которым ее транспортируют к шахтному стволу. Доставка бывает самотечной, механизированной с помощью самоходного пневмоколесного оборудования, конвейеров или скреперов. Вторичное дробление руды – дробление образовавшихся при взрывной отбойке чрезмерно крупных кусков, производимое в очистном блоке или где то еще перед погрузкой руды на транспорт. Процессы поддержания очистного пространства – закладка или крепление.
Отбойка — это процесс отделения части руды от массива в блоке с одновременным дроблением ее на куски. Она должна обеспечивать более полное отделение руды от массива в пределах проектного контура, минимальные законтурные обрушения массива и хорошее качество дробления. Выбор способа отбойки руды зависит от таких факторов, как физико-механические свойства руды, горно-геологические условия и принятая система разработки. Отбойка руды осуществляется с применением буровзрывных работ, механических средств и самообрушения. Механическая отбойка применяется при добыче относительно мягких руд (марганца, калийной соли) с помощью комбайнов. Самообрушение как наиболее экономичный способ отделения руды от массива применяется крайне редко. Оно происходит в очистных блоках под действием собственного веса трещиноватых руд и давления налегающих пород. При этом способе невозможно управлять качеством отбойки. При подземной добыче в основном применяют взрывную отбойку. Применяют следующие способы взрывной отбойки: шпуровой, скважинный и минный (сосредоточенными зарядами).
|
|
Отбойка скважинными зарядами впервые начали применять в нашей стране в начале 30-х гг.
Скважинная отбойка применяется при разработке месторождений средней и большой мощности параллельными, веерными или пучковыми скважинами обычным диаметром d=45-105мм. Отбойка осуществляется вертикальными, наклонными или горизонтальными слоями на компенсационное пространство или "в зажиме".
Рисунок 9.1 – Схемы параллельного (а) и веерного (б) расположения взрывных скважин при отбойке руды: 1 — скважины; 2 — буровые выработки; W — линии наименьшего сопротивления
В настоящее время применяются следующие способы бурения скважин:
– штанговое — тяжелыми телескопными колонковыми перфораторами. Диаметр скважин 50— 85 мм. Глубина бурения от 12—15 до 20—25 м и более при крепости руды от 6 до 14. Производительность бурения 30—70 м/смену. Последние десятилетия широкое распространение при штанговом бурении получили самоходные буровые установки с мощными колонковыми пневматическими или гидравлическими перфораторами имеющий независимое вращение бура ( ударно-вращательного типа ). Диаметр 50- 85мм, глубина 10 – 50 м, производительность 300-500м/смену.
|
|
– погружными пневмоударниками. Диаметр скважин 85, 100 мм и более. Производительность бурения зависит от крепости руд и колеблется от 5—7 (очень крепкие руды) до 15— 20 м/смену;
– шарошками, армированными твердыми сплавами. Диаметр скважин 150 мм и более. Глубина бурения 50—60 м. Применяется в крепких и весьма крепких рудах. Производительность шарошечного бурения выше пневмоударного в 2—3 раза;
– вращательное твердосплавными и алмазными кольцевыми коронками. Диаметр скважин 80—100 мм. Крепость руд до 6—8. Производительность бурения 20—40 м/смену.
В шестидесятых же годах в СССР начинают изготавливать мощные перфораторы с независимым вращением бура. С помощью таких перфораторов стало возможным штанговое бурение скважин по крепким породам на глубину до 30—50 м.
Во всех применяемых методах бурения взрывных скважин буровой инструмент армируют твердыми сплавами.
|
|
В настоящее время появилась возможность использовать для бурения алмазы — как природные, так и, главным образом, синтетические. В связи с этим и дефицитностью металлов, входящих в твердые сплавы, предпринимаются попытки применить алмазное бурение (вращательное, коронками, армированными алмазами) взрывных скважин малого диаметра. Штанговое бурение является основным способом бурения скважин уменьшенного диаметра (50—90 мм).
При ударно–вращательном бурении с увеличением глубины скорость бурения снижается примерно по гиперболической зависимости. Это объясняется расходованием энергии удара на преодоление инерции удлиненной колонны штанг, ухудшением условий удаления продуктов разрушения из забоя и недостаточной величиной крутящего момента. Поэтому в крепких породах скорость бурения перфораторами с геликоидальным стержнем становится незначительной при глубине 10—12 м. Независимое вращение бурового инструмента позволяет увеличивать глубину до 30—50 м.
Для бурения скважин диаметром 51—70 мм на подземных рудниках США, Канады, Швеции, Австралии и других стран наиболее широко применяют мощные колонковые перфораторы с энергией удара до 26 кгс-м и диаметром поршня до 130 мм. Перфораторы от одного до двух монтируются на манипуляторах самоходных пневмоколесных буровых установок. Эти установки — двух- и трехперфораторные. Производительность установки 300—500 м/смену или 1000—2000 т/смену [1-3].
|
|
Бурение погружными пневмоударниками
Этот способ (предложен С. П. Юшко в 1949—1951 гг.) устранял основной недостаток перфораторного (штангового) бурения — поглощение силы удара инерцией колонны штанг. В скважину вводится только ударный механизм, вращение его осуществляется через став штанг вращателем, установленным около скважины.
Основной объем бурения скважин на рудниках производится с помощью погружных пневмоударников станками НКР-100М, диаметр скважин 105—110 мм и станками ЛПС-3, диаметр 150 мм. Выпускаются пневмоударники ПБ-85 для бурения скважин диаметром 85 мм (при диаметре менее 75—80 мм значительно уменьшается энергия единичного удара, а многопоршневые конструкции создать затруднительно).
Производительность станка "при бурении скважин диаметром 100 мм в направлении от вертикального вниз до наклонного вверх с углом наклона не более 30° на глубину до 50 м по породам с коэффициентом крепости 4—6, 10—14 и 19—20 составляет соответственно 40, 15 и 5 м/смену.
Увеличение глубины скважины снижает скорость бурения в связи с ростом продолжительности спускоподъемных операций, повышением затрат энергии на преодоление трения штанг о стенки скважин и при бурении вверх снижает давление инструмента на забой. При бурении восходящих скважин уменьшение осевого давления на забой снижает скорость, например, на 20—40% при глубине до 40—50 м.
Для современных конструкций пневмоударников оптимальное давление сжатого воздуха 5–7 кгс/см2, так как при большем давлении учащаются поломки инструмента.
На зарубежных рудниках применяются станки для бурения взрывных и вспомогательных скважин диаметром 80—200 мм и глубиной до 150 м погружными пневмоударниками, как правило, самоходные на пневмошинах с дизельным или электрическим приводом хода и гидроприводом для вращения бурового става; использование гидропривода повышает эффективность бурения на глубину более 30—40 м.
Преимущества бурения скважин погружными пневмоударниками по сравнению с шарошечным бурением (переносными станками) :
- более легкое и транспортабельное оборудование;
- меньшее число обслуживающих рабочих;
- более широкая область возможного применения, включая залежи ограниченной мощности с неправильным залеганием, где приемлемый диаметр скважин не превышает 100 мм [3].
Особенно значительные достижения в связи с применением погружных ударных машин оказались в сфере добычи полезных ископаемых при бурении в подземных условиях. Погружные ударные машины применяются сегодня для бурения во всех развитых странах мира. Использование погружных пневмоударных машин (пневмоударников) считается специалистами в настоящее время наиболее прогрессивным методом бурения.
В настоящее время особенно остро стоит задача повышения сменной производительности в процессе пневмоударного бурения. Возможным решением этой задачи может стать переход на максимально допустимых диаметр скважины (127 мм), что может позволить сократить время бурения на 30%. Предлагается проводить работу и для увеличения межзаточной стойкости инструмента, используемого при бурении, что позволит сократить вспомогательное время на проведение спускоподъемных операций, чтобы осуществлять замену инструмента.
К освоению производством предлагаются и пневмоударники, которые относятся к новому поколению, имеющие повышенную энергию удара и эффективно работающие со штыревым инструментом притом, что энергоноситель будет иметь обычное давление (0,5 МПа). В сочетании с увеличенным диаметром скважины (до 127 мм) увеличенная сменная производительность таких моделей позволит сократить время для проведения бурения блока до 2 раз.
На сегодняшний день буровые установки зарубежных фирм применяются на руднике «Кировский» ОАО «Апатит», Оленегорском руднике ОАО «ОлКОН», на месторождении «Нурказган», на подземных рудниках «Гайский ГОК», на рудниках ОАО "ГМК "Норильский никель".
Для выбора рационального варианта буровой установки для данного месторождения необходимо провести сравнительный анализ опыта применения российских и зарубежных фирм. Для сравнения показателей были выбраны буровые машины зарубежной фирмы «Sandvik – Tamrock» (Финляндия). В этом случае необходимо руководствоваться горно-геологическими условиями рассматриваемого месторождения. Для шахты имени «Десятилетия Независимости Казахстана» подходят следующие буровые установки: НКР-100М, БП-100С, SOLO-1009ZR, SANDVIK DL 420-15.
Дата добавления: 2018-08-06; просмотров: 650; Мы поможем в написании вашей работы! |
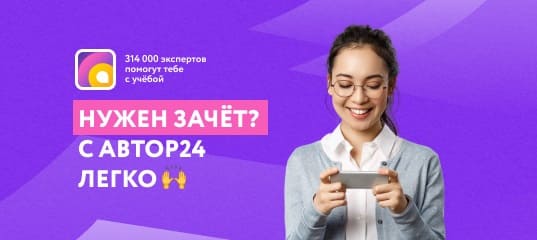
Мы поможем в написании ваших работ!