МЕТОДЫ И МЕТОДИКИ ИССЛЕДОВАНИЯ
Nbsp;
РЕФЕРАТ
Отчет по производственной практике выполнен на 34листах и содержит 8 рисунков, 8 формул и 6 таблиц.
Цель производственной практики: закрепление теоретических знаний, полученных при изучении инженерных дисциплин. Для выполнения поставленной цели необходимо решить следующие задачи:
- изучить иотработать способы пробоподготовки образцов к материаловедческим исследованиям;
- методом гидростатического взвешивания определить плотность образца из углеродистой стали, определить погрешности измерений;
- определение среднего условного диаметра зерна или количества зерен;
- изучить спектральный анализ металлов;
- приобретение организаторского и профессионального опыта;
- приобретение навыков командной работы, компетенций корпоративных принцип управления
СОДЕРЖАНИЕ
1 Литературный обзор. 6
1.1. Нержавеющая сталь. 6
1.2. Классификация стали. 6
1.3. Применение нержавеющей стали. 7
2.Методы и методики исследования. 9
2.1 Шлифование. 9
2.2 Полирование. 10
2.4. Спектральный анализ металлов. 12
2.5. Измерение плотности методом гидростатического взвешивания. 14
2.6. Методы оптической микроскопии. 15
2.7. Выявление зерна в стали. 16
2.8. Метод сравнения. 16
2.9.Подсчет количества зерен, приходящихся наединицу поверхности шлифа. 18
2.10. Определение среднего условного диаметра зерна или количества зерен в 1 мм2 18
2.11. Метод планиметрирования. 19
|
|
3 РЕЗУЛЬТАТЫ.. 20
3.1.Определение плотности образца методом гидростатического взвешивания. 20
3.2. Результаты спектрального анализа. 20
4. Расчетный часть. 23
4.1 Определение размера зерна образцов. 23
5. Безопасность и охрана труда. 26
5.1 Общая положения. 26
5.2 Радиационная безопасность. 26
5.3. Средство индивидуальной защиты органов дыхания. 27
5.3.1. Правила пользования респиратором ШБ-1 «Лепесток». 29
5.4. Электробезопасность. 29
5.6. Пожарная безопасность. 31
5.7. Оказания первой доврачебной помощи при несчастных случаях. 32
Заключение. 33
Литературный список. 34
ВВЕДЕНИЕ
Институт атомной энергии (ИАЭ) создан в 1992 году на базе Объединенной экспедиции научно-производственного объединения «Луч» Министерства атомной энергии РФ.
Основные направления деятельности Института атомной энергии в настоящее время:
— развитие атомной энергетики в РК;
— экспериментальные исследования по проблемам безопасности -атомной энергетики;
— экспериментальные исследования конструкционных материалов ядерной и термоядерной техники;
— участие в работах по выводу из эксплуатации реактора на быстрых нейтронах БН-350;
— участие в работах по созданию Казахстанского материаловедческого термоядерного реактора КТМ;
|
|
— участие в работах по утилизации радиоактивных отходов.
Наиболее значимые результаты исследований были получены в работах по моделированию и изучению процессов, сопровождающих отдельные стадии развития тяжелых аварий на АЭС с плавлением активной зоны реактора, проводимых в сотрудничестве с японскими энергетическими компаниями и научно-исследовательскими организациями NuclearPowerEngineeringCorporation, JapanAtomicEnergyAgency и JapanAtomicPowerCorporation.Одним из направлений деятельности ИАЭ НЯЦ РК является участие в исследованиях в области реакторного материаловедения, в том числе в поддержку международного проекта ИТЭР. Завершаются работы по созданию в г. Курчатове Казахстанского материаловедческого токамака КТМ, основной задачей которого является изучение новых перспективных конструкционных материалов для будущих термоядерных реакторов. Эта установка в будущем может стать основой создания международного научного центра по термоядерным исследованиям.
В настоящее время коллектив ИАЭ способен решать самые сложные экспериментальные задачи на реакторных и внереакторных исследовательских установках. Главным направлением деятельности ИАЭ является участие в работах по созданию и развитию атомной энергетики в Республики Казахстан. Отдавая себе отчет в том, что масштабная задача создания атомно-энергетической отрасли может быть решена только в условиях широкой кооперации научных и технологических сил разных отраслей и стран ИАЭ приглашает к сотрудничеству все заинтересованные организации и предприятия как Казахстане, так и за рубежом.
|
|
В соответствии с Постановлением Правительства Республики Казахстан «О развитии атомной энергетики Республики Казахстан» от 18.10.95 г. за №1344 Национальный ядерный центр заключил ряд соглашений и договоров с ведущими учебными заведениями Республики и зарубежных стран по подготовке кадров ядерного профиля. С 1997 г. на экспериментальной базе центра проводят занятия филиалы кафедр региональных университетов, ежегодно проводится набор в аспирантуру по специальностям «Физика», «Ядерные энергетические установки», «Экология».
Более 200 студентов региональных ВУЗов ежегодно проходят обучение на базе лабораторий и экспериментальных установок НЯЦ РК.
В период с 28 мая по 30 июнябыла пройдена производственная практика в отделе материаловедческих исследований в лаборатории испытаний конструкционных и топливных материалов.[1].
|
|
ЛИТЕРАТУРНЫЙ ОБЗОР
Нержавеющая сталь
Нержавеющая сталь (коррозионно-стойкие стали, в простонародье «нержавейка») — легированная сталь, устойчивая к коррозии в атмосфере и агрессивных средах. Основной легирующий элемент нержавеющей стали — хром Cr (12-20 %); помимо хрома, нержавеющая сталь содержит элементы, сопутствующие железу в его сплавах (С, Si, Mn, S, Р), а также элементы, вводимые в сталь для придания ей необходимых физико-механических свойств и коррозионной стойкости (Ni, Mn, Ti, Nb, Co, Mo).
Причина коррозионной стойкости нержавеющей стали объясняется, главным образом, тем, что на поверхности хромсодержащей детали, контактирующей с агрессивной средой, образуется тонкая плёнка нерастворимых окислов, при этом большое значение имеет состояние поверхности материала, отсутствие внутренних напряжений и кристаллических дефектов.
В сильных кислотах (серной, соляной, фосфорной и их смесях) применяют сложнолегированные сплавы с высоким содержанием Ni и присадками Mo, Cu, Si.
Повышенная атмосферная коррозионностойкость стали достигается, как правило, целенаправленным изменением её химического состава. Считается, что наиболее эффективно повышают сопротивление строительных сталей атмосферной коррозии небольшие добавки никеля, хрома, и особенно фосфора, и меди. Так, легирование медью в пределах 0,2-0,4 % повышает на 20-30 % стойкость против коррозии открытых конструкций в промышленной атмосфере[2-3].
Классификация стали
Нержавеющие стали делят на три группы:
1. Коррозионностойкие стали — от них требуется стойкость к коррозии в несложных промышленных и бытовых условиях (из них можно изготавливать детали оборудования для нефтегазовой, легкой, машиностроительной промышленности, хирургические инструменты, бытовую нержавеющую посуду и тару).
2. Жаростойкие стали — от них требуется жаростойкость — то есть стойкость к коррозии при высоких температурах в сильно агрессивных средах (напр. на химических заводах).
3. Жаропрочные стали — от них требуется жаропрочность — то есть хорошая механическая прочность при высоких температурах.
По химическому составу нержавеющие стали делятся на:
— хромистые, которые, в свою очередь, по структуре делятся на;
—мартенситные;
—полуферритные (мартенисто-ферритные);
—перритные;
— хромоникелевые;
—аустенитные;
—аустенитно-ферритные;
—аустенитно-мартенситные;
—аустенитно-карбидные;
— хромомарганцевоникелевые (классификация совпадает с хромоникелевыми нержавеющими сталями).
Различают аустенитные нержавеющие стали, склонные к межкристаллитной коррозии, и стабилизированные — с добавками Ti и Nb. Значительное уменьшение склонности нержавеющей стали к межкристаллитной коррозии достигается снижением содержания углерода (до 0,03 %).
Нержавеющие стали, склонные к межкристаллитной коррозии, после сварки, как правило, подвергаются термической обработке.
Широкое распространение получили сплавы железа и никеля, в которых за счёт никеля аустенитная структура железа стабилизируется, а сплав превращается в слабо-магнитный материал.[4-5].
Применение нержавеющей стали
Нержавеющую сталь используют во всех сферах деятельности человека, начиная от тяжелого машиностроения, заканчивая электроникой и точной механикой.
Наибольшее применение нержавеющей стали в:
— ядерных реакторах;
— строительстве и архитектуре;
— бытовых приборах;
— химической и нефтехимической промышленности;
— целлюлозно-бумажном производстве;
— охране окружающей среды;
Благодаря своим антикоррозийным свойствам нержавеющая сталь имеет достаточно широкую сферу применения.
Аустенитные нержавеющие стали успешно применяются в качестве материала оболочек твэлов и других деталей тепловыделяющих сборок в исследовательских и энергетических реакторах, охлаждаемых водой высоких параметров. Широко распространенные аустенитные хромоникелевые стали обладают важными преимуществами перед цирконием, алюминием и их сплавами: высокой жаропрочностью и жаростойкостью вплоть до 600 °С, хорошей коррозионной стойкостью в воде вплоть до критических параметров и перегретом паре высокого давления до 600 °С, хорошей свариваемостью.
Наиболее знакомое всем использование – бытовое. Посмотрите на свою квартиру многое в ней сделано из нержавеющей стали – столовые приборы, посуда, кухонные мойки, декоративные элементы мебели и даже бритвенные лезвия. Или, напримербытовая техника – внутренняя часть микроволновой печи и барабан стиральной машины тоже сделаны с применением нержавеющей стали.
Кровля и фасады некоторых зданий сделаны из нержавейки, несущие конструкции, опоры осветительных уличных столбов из нержавеющей стали, автобусные остановки, уличная мебель тоже из нержавейки, перила в супермаркете также делаются с использованием нержавеющей стали.
Далее транспорт. Многие узлы и агрегаты автомобилей, автобусов и других средств транспорта изготовлены с применением нержавеющей стали: отделка салона выхлопные системы, трубы, решетки автомобиля, топливные баки и так далее. Специализированные автоцистерны, например, для перевозки молока, сделаны с применением нержавеющей стали. Но все это мелочи, пожалуй, самое широкое применение нержавеющая сталь нашла в промышленности.
Химическая и фармацевтическая промышленности, работающие с агрессивными средами, не могут обойтись без специальных нержавеющих сталей. Здесь используются стали из нержавейки с очень высокой коррозионной стойкостью не только к воде, но и к различным химическим растворам: кислотам, щелочам и другим. В частности нержавеющую сталь применяют для изготовления емкостей, работающих под высоким давлением, технологических трубопроводов, производственного и измерительного оборудования и инструмента.
Нефтегазовая промышленность – лидер по применению нержавеющих труб, нержавеющая сталь используется при производстве морских буровых платформ, да и на суше добыча углеводородов не обходится без применения нержавеющей стали.[6].
МЕТОДЫ И МЕТОДИКИ ИССЛЕДОВАНИЯ
Шлифование
Один из этапов подготовки образцов к материаловедческим исследования это шлифование.
Для удобства приготовления шлифов образцы помещают в металлические оправки - кольца круглой или эллипсовидной формы и заливают легкоплавким веществом: серой. Поэтому залитые образцы можно при необходимости освобождать из оправки, нагревая их.
Поверхность образца шлифуют с малой подачей при интенсивном охлаждении. Припуск на шлифовку должен быть не менее 0,3 мм на сторону. Шероховатость поверхности должна соответствовать 7-8 классу частоты по ГОСТ 2789-59.
Образец обрабатывают на вращающемся шлифовальном круге или опиливают напильником. При большой скорости вращения шлифовального круга подготовку поверхности ведут с охлаждением образца и малым нажимом. Перегрев образца и сильное механическое воздействие могут вызвать изменение микроструктуры, что приведет к ошибочному результату исследования. Полученная поверхность должна быть плоской и не иметь завалов.
Существуют два способа шлифования образцов ручной и механический.
При ручном способе шлифования на жесткую плоскую подкладку (толстое стекло или лист металла), расположенную горизонтально, кладут наждачную бумагу. Затем образец ставят на бумагу заторцованной плоскостью и шлифуют с легким нажимом. Шлифование ведут до полного уничтожения рисок, оставшихся после торцовки. Когда на шлифе останутся риски только от бумаги, шлифование прерывают.
Шлифовальную бумагу удаляют с подкладки, стряхивая с нее выкрошившиеся абразивные зерна и частицы металла. Остатки абразива удаляют также с подкладки и шлифа, протирая их куском чистой мягкой ткани или ватным тампоном. После этого операцию шлифования повторяем на бумаге с более мелким зерном. При повторном шлифовании направление движения образца должно быть перпендикулярно направлению рисок, оставшихся от первого шлифования. Образцы шлифуют, применяя последовательно бумагу с меньшим номером зернистости и каждый раз изменяя направление движения шлифа на 90°.
Исследования проводились на двух цилиндрических образцах диаметром ~ 20 мм, высотой ~ 3 мм. Пробоподготовка образцов для исследований на оптическом микроскопе включала в себя следующие этапы:
1. предварительное выравнивание торцов цилиндрических образцов шлифовкой на крупнозернистой наждачной бумаге (зернистость 80-220);
2. последовательное шлифование торцов на наждачной бумаге зернистостью: 80, 120, 160, 220, 400, 600, 800, 1000, 1500, 2000.[7-9].
Полирование
После завершения шлифования на поверхности шлифа остаются тонкие риски. Чтобы окончательно выровнять поверхность, шлиф полируют до зеркального блеска. Применяют два способа полирования шлифов: механический и электролитический.
Механический способ. Шлиф механическим способом полируют на полировальном станке. Принципиальное устройство его такое же, как и шлифовального. Иногда один и тот же станок применяют и для шлифования, и для полирования. Над полировальным станком прикрепляю бачок для полировочной жидкости, которая через тонкую трубку с краном подается на полировальный круг. Полировальный круг помещен в кожух, имеющий патрубок для отвода жидкости, которая через тонкую трубку с краном подается на полировальный круг. Полировальный круг помещен в кожух, имеющий патрубок для отвода жидкости. Круг покрывают мягкой тканью: сукном, фетром, драпом, шелком и др. Чем мягче полируемый металл, тем тоньше должно быть строение ткани. Если из шлифа могут выкрашиваться хрупкие фазы, то полировать его следует на ткани без ворса.
При полировке ткань равномерно смачивается полировочной жидкостью - смесью абразивного материала с водой. Для полировки стальных шлифов применяют оксиды хрома и алюминия (Сr2О3 и А12О3), а шлифов цветных металлов - оксид магния. Полировочную жидкость готовят, размешивая и 1 л воды примерно 2 г порошка оксида металла; смеси дают отстояться в течение 1 ч. За это время наиболее крупные частицы оксида оседают на дно, а мелкодисперсные остаются в воде. Чем дольше отстаивается полировочная жидкость, тем дисперснее в ней частицы. Оксид магния размешивают в дистиллированной воде; эту жидкость применяют только свежеприготовленной. Скорости вращения полировальных кругов такие же, как и шлифовальных (20 - 140 рад/с). Мягкие сплавы полируют при меньшей частоте вращения круга.
При полировке шлиф периодически поворачивают для более равномерной обработки всей поверхности.
1 – катод, 2-постоянный ток, 3-электролизная ванна, 4-электрот,
5-мешалка, 6-выпрямителем
Рисунок 1 – Схема установки для электролитического полирования и электролитического травления шлифов
Электролитическое полирование. При электролитическом полировании гладкая и блестящая поверхность, на металлическом образце получается в результате анодного растворения выступов микрорельефа. Для электролитического полирования шлифов используют специальную установку, принципиальная схема которой показана на рис. 8. Отшлифованный образец 2 (анод) включают в цепь постоянного тока, создаваемого выпрямителем 6, и помещают в электролизную ванну 3, заполненную электролитом 4. Катодом 1 служит металлическая пластинка. Для равномерного протекания процесса полирования электролит перемешивают механической или электрической мешалкой 5.
Электролизные ванны изготовляют из кислотоупорных материалов. Неподогреваемые ванны делают из стекла, фарфора, фторопластов; подогреваемые - из нержавеющей стали. Катоды вырезают из листового металла; меди, свинца, нержавеющей стали и др.
Круг покрывают мягкой тканью: сукном, фетром, драпом, шелком и др. Чем мягче полируемый металл, тем тоньше должно быть строение ткани.
Последовательная полировка торцов на сукне с применением алмазных паст с размерами абразивных частиц: 10\7, 7\5, 5\3, 3\2, 1\0 мкм.
После каждой стадии шлифовки и полировки образцы тщательно протирают смоченным в спирте тампоном и промывают под струей воды, для удаления абразивных частиц и связующего алмазной пасты.На рисунке 2 показан внешний вид образца после травления.[10-11].
Рисунок 2 – Внешний вид образца после травления
Спектральный анализ металлов
Один из методов определить химический состав материалов– спектральный анализ. Он основан на взаимодействии материй со спектром излучений, включая электромагнитное и акустическое. Атомы каждого химического элемента имеют свои резонансные частоты, на которых они излучают или поглощают свет. От количества и состояния вещества зависит количество и интенсивность линий, которые показывает спектрометр. В зависимости от целей проводят разные методы спектрального анализа.
Преимущество спектрального анализа состоит в том, что он дает возможность определить марку стали не только на образцах при нормальной температуре.Последний позволяет определять одновременно несколько элементов на весьма малых образцах, без порчи изделий, в короткое время
Спектрометр Supermini200 основанный на методе флуоресцентного анализа с дисперсией по длине волны, является предпочтительным для анализа металлургических шлаков, сталей, специальных сплавов, аэрокосмических материалов и лопаток турбин.
Рисунок3 – Спектрометр Supermini200
При анализе образцов, содержащих лёгкие элементы, Supermini200 использует принцип дисперсии по длине волны с несравненно лучшим, чем у энергодисперсионных спектрометров спектральным разрешением и с минимальным взаимным наложением линий. Необходимо заметить, что измерение легких элементов всегда было более тяжелой задачей поскольку выход флуоресценции пропорционально зависит от атомного номера определяемого элемента в четвертой степени. При этом легкие элементы не только имеют слабое флуоресцентное излучение, но и их пики взаимно перекрываются между собой, а так же могут перекрываться L и M линиями тяжелых элементов.На рисунке 6 показано устройство использованного нами рентгеновского спектрометра последовательного действия
Рисунок 4–устройстворентгеновского спектрометра последовательного действия
Характеристика спектрометра:
— анализ элементов от кислород до урана (O → U);
— анализ: твердые тела, жидкости, порошкообразные материалы,сплавы и тонкие пленки;
— атмосфера: воздух, гелий или вакуум;
— рентгеновская трубка: 50 кВ, 200 Вт Pd-анод;
— первичная фильтрация пучка: Zr (стандарт),Al (опция);
— детекторы: Проточный пропорциональный счетчик и сцинтилляционный счетчик;
— кристаллы-анализаторы: 3-позиционный загрузчик;
— автосменщик образцов: стандартный 12-позиционный;
— вакуум: стандартный ротационный насос;
— энергоснабжение: 100 – 120В (50/60 Гц) 15A или 200 – 240В (50/60 Гц) 10A.
Цельные образцы, такие как металлы или сплавы, так же как и прессованные из порошка таблетки, анализируются в вакууме. Жидкие пробы, например водные растворы или масла, помещаются в специальные жидкостные кюветы, покрываются пленкой и измеряются в гелиевой атмосфере. Стандартный 12-позиционный механизм для смены образцов (чейнджер) позволяет операторам равномерно осуществлять ежедневный анализ. Дополнительную гибкость оператору предоставляет возможность замены образцов на чейнджере, не прерывая измерение.[13-17].
Дата добавления: 2018-08-06; просмотров: 224; Мы поможем в написании вашей работы! |
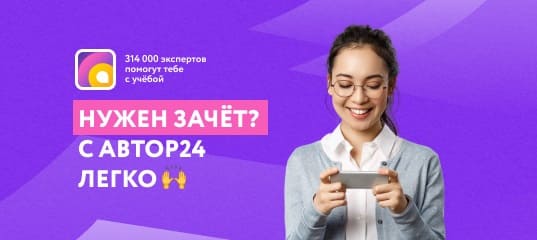
Мы поможем в написании ваших работ!