Классификация роботов по показателям, определяющим их конструкцию.
Ктаким показателям относятся:
· тип приводов;
· грузоподъемность;
· количество манипуляторов;
· тип и параметры их рабочей зоны;
· подвижность и способ размещения;
· исполнение по назначению.
Приводы,которые используются в манипуляторах и системах передвижения роботов, могут быть электрическими, гидравлическими и пневматическими. Часто их применяют в комбинации. Например, в звеньях манипулятора большой грузоподъемности уместен гидравлический привод, а в его захватном устройстве — более простой и маломощный пневматический привод. Приводы роботов рассмотрены в главе 4.
Грузоподъемность робота— это грузоподъемность его манипуляторов, а для транспортного робота еще и его шасси. Грузоподъемность манипулятора определяется массой перемещаемых им объектов и в зависимости от назначения робота может составлять от единиц грамм (сверхлегкие роботы, например, применяемые в микроэлектронной промышленности) до нескольких тысяч килограмм (сверхтяжелые, например, транспортные и космические роботы).
Количество манипуляторову роботов в большинстве случаев ограничено одним. Однако в зависимости от назначения существуют конструкции роботов с 2, 3 и совсем редко 4 манипуляторами. Обычно манипуляторы робота выполняют одинаковыми, но имеются конструкции роботов и с разными манипуляторами. Например, существуют промышленные роботы для обслуживания прессов холодной штамповки с двумя разными манипуляторами: один, основной, для взятия заготовки и установки ее в пресс и другой, упрощенной конструкции, для выполнения более простой операции изъятия готовой детали.
|
|
Тип и параметры рабочей зоны манипулятораопределяют область окружающего робот пространства, в пределах которой он может осуществлять манипуляции, не передвигаясь, т. е. при неподвижном основании. Рабочая зона манипулятора — это пространство, в котором может находиться его рабочий орган при всех возможных положениях звеньев манипулятора. Форма рабочей зоны определяется системой координат, в которой осуществляется движение рабочего органа манипулятора, и числом степеней подвижности манипулятора.
Подвижность роботаопределяется наличием или отсутствием у него системы передвижения. В первом случае роботы называют мобильными, а во втором — стационарными. В соответствии с назначением роботов в них применяют системы передвижения практически всех известных на сегодня типов: от наземных (колесных, гусеничных и др.) до предназначенных для передвижения в воде, воздухе и космосе. Специфическим способом передвижения, относящимся к робототехнике, является шагание.
|
|
По способу размещениястационарные и мобильные роботы бывают напольными, подвесными (мобильные роботы этого типа обычно перемещаются по поднятому монорельсу) и встраиваемыми в другое оборудование (например, с размещением на станине обслуживаемого им станка).
Исполнение робота по назначению зависит от внешних условий, в которых он должен функционировать. Различают исполнение нормальное, пылезащитное, теплозащитное, влагозащитное, взрывобезопасное и т. д.
Классификация роботов по способу управления.По этому признаку различают роботы с программным, адаптивным и интеллектуальным управлением.
Управление движением по отдельным степеням подвижности может быть непрерывным и дискретным. В последнем случае управление движением осуществляется заданием последовательности точек с остановкой в каждой из них. Простейшим вариантом дискретного управления является цикловое, при котором количество точек позиционирования по каждой степени подвижности минимально — чаще всего ограничено двумя — начальной и конечной.
Классификация роботов по быстродействию и точности движений.Эти параметры взаимосвязаны и характеризуют динамические свойства роботов.
Быстродействие манипулятораопределяется скоростью перемещения его рабочего органа и может быть разбито на 3 диапазона в зависимости от линейной скорости:
|
|
· малое — до 0,5 м/с;
· среднее — от 0,5 до 1—3 м/с;
· высокое — при больших скоростях.
Наибольшая скорость манипуляторов современных роботов достигает 10 м/с и выше.
Для значительной части областей применения роботов этот параметр очень важен, так как предопределяет их производительность. Основная трудность при повышении быстродействия связана с известным противоречием между быстродействием и точностью.
Точность манипулятора и системы передвижения робота характеризуется погрешностью позиционирования. Чаще всего точность роботов характеризуют абсолютной погрешностью. Точность роботов общего применения можно разбить на 3 диапазона в зависимости от линейной погрешности:
· малая — от 1 мм и более;
· средняя — от 0,1 до 1 мм;
· высокая — при меньшей погрешности.
Наименьшую точность имеют роботы, предназначенные для выполнения наиболее грубых, например, транспортных движений, а наибольшую, микронную — роботы, используемые, например, в электронной промышленности.
По сравнению с человеческой рукой существенным недостатком современных роботов пока является снижение точности с увеличением хода манипулятора, в то время как у человека эти параметры в значительной степени развязаны благодаря разделению движений на грубые (быстрые) и точные. См. главу 2.
|
|
Рассмотренные ранее параметры роботов относятся к классификационным, т. е. используются при формировании типажа роботов и, соответственно, их наименований. Например, названия: легкий пневматический промышленный робот с цикловым управлением для обслуживания прессов холодной штамповки, окрасочный гидравлический промышленный робот и т. д.
Параметры, определяющие технический уровень роботов. Кним относятся и некоторые из ранее рассмотренных параметров, которые могут иметь количественное выражение, такие, как: быстродействие, точность.
Однако, если при использовании этих параметров для классификации роботов их разбивают, как было показано ранее, на классификационные диапазоны и тип робота определяют по принадлежности значения данного параметра к одному из них, то сравнительную оценку технического уровня роботов производят, исходя из конкретных численных значений параметров. При этом широко применяются различные, основанные на указанных ранее параметрах, комбинированные и относительные показатели. К ним относятся, в частности, удельная грузоподъемность, отнесенная к массе робота, выходная мощность манипулятора (произведение грузоподъемности на скорость перемещения), отнесенная к мощности его приводов; размер рабочей зоны, отнесенный к габаритам робота.
Другими ранее не упоминавшимися параметрами, характеризующими технический уровень роботов, являются число одновременно работающих степеней подвижности, надежность, способы и время программирования.
Манипуляционные системы
Сегодня основным типом манипуляционных систем роботов являются механические манипуляторы. Они представляют собой пространственные механизмы в виде кинематических цепей из звеньев, образующих кинематические пары с угловым или поступательным относительным движением и системой приводов обычно раздельных для каждой степени подвижности. Манипуляторы заканчиваются рабочим органом.
Степени подвижности манипулятора делятся на переносные и ориентирующие. Переносные степени подвижности служат для перемещения рабочего органа в рабочей зоне манипулятора, а ориентирующие— для его угловой ориентации. Минимально необходимое число переносных степеней подвижности для перемещения рабочего органа в пространстве рабочей зоны равно 3. Однако для расширения манипуляционных возможностей и реализации более сложных траекторий движения, например, с обходом препятствий, а также для повышения быстродействия манипуляторы обычно снабжают несколькими избыточными переносными степенями подвижности, хотя это, усложняет и удорожает робота. Современные манипуляторы в среднем имеют 4—6 степеней подвижности, но существуют манипуляторы и с 8—9 такими степенями.
Максимально необходимое число ориентирующих степеней подвижности равно 3. Они реализуются кинематическими парами с угловым перемещением, обеспечивающими поворот рабочего органа манипулятора относительно его продольной и 2 других взаимно перпендикулярных осей.
На рис. 3.1—3.4 показаны конструкции манипуляторов с 3 переносными степенями подвижности в различных системах координат и их рабочие зоны.
Рис.3.1. Манипулятор с прямоугольной системой координат (а) и его рабочая зона (б)
Манипуляторы, работающие в прямоугольной системе координат (рис. 3.1), имеют рабочую зону в форме параллелепипеда. Здесь все перемещения только поступательные. Поэтому такая система координат наиболее удобна для выполнения прямолинейных движений. Кроме того, она максимально упрощает программирование робота, так как оно обычно выполняется именно в прямоугольной системе координат, и, следовательно, в этом случае не требуется пересчета программ из одной системы координат в другую. На рис. 3.5 показан пример промышленного робота, манипуляторы которого работают в прямоугольной системе координат.
Рис. 3.2. а — манипулятор с цилиндрической системой координат; 6 — его рабочая зона
Рис. 3.3. а — манипулятор со сферической системой координат
Рис. 3.3. б — его рабочая зона
Рис. 3.4. а— манипулятор с угловой системой координат; б — его рабочая зона
В манипуляторах, работающих в цилиндрической системе координат (см. рис. 3.2), наряду с поступательными перемещениями осуществляется одно угловое перемещение (по окружности). Соответственно, рабочая зона ограничена цилиндрическими поверхностями. В цилиндрической системе координат работает робот, показанный на рис. 1.5.
В сферической системе координат (рис. 3.3) осуществляются уже 2 угловых перемещения и рабочая зона ограничена сферическими поверхностями. Такую систему координат имеет, например, манипулятор промышленного робота, показанного на рис. 1.6. Манипуляторы с такой системой координат, как правило, сложнее, чем с цилиндрической системой, однако компактнее.
Показанный на рис. 3.4 манипулятор с угловой системой координат производит только угловые перемещения, т. е. все его звенья представляют собой шарниры. Поэтому часто такие манипуляторы называют шарнирными и антропоморфными. Роботы с такого типа манипуляторами благодаря возможности последних складываться, не выступая практически за габариты основания робота, обладают наибольшей компактностью, хотя и наиболее сложны в управлении.
В манипуляторе робота "Пума", показанном на рис. 3.8, двигатель привода 1-й степени подвижности вокруг вертикальной оси размещен на основании манипулятора.
Рис. 3.8. Общий вид манипулятора робота "Пума" фирмы "Юнимейшен" (а) и его кинематическая схема (б)
Двигатели степеней подвижности 2 и 3 размещены рядом на 2-м звене. С приводимыми ими осями они связаны через редукторы, а двигатель 3 еще и валом с 2 механизмами Гука. Двигатели степеней подвижности 4, 5 и 6 размещены на 3-м звене манипулятора. Передача движения от них осуществляется через валы с шарнирами Гука и зубчатые передачи. Размещение этих двигателей с другой стороны оси вращения звена относительно основной его части обеспечивает статическое уравновешивание веса этих звеньев манипулятора относительно осей их вращения и соответственно разгрузку двигателей 2 и 3.
Специфическую группу манипуляционных систем составляют манипуляторы, которые предназначены для выполнения манипуляционных операций на значительном расстоянии от своего основания, так что основная длина манипулятора служит только для переноса его рабочего органа в зону выполнения этих операций, т. е. выполняет чисто транспортную задачу. На рис. 3.11 показан пример такого манипулятора длиной до 25 м, предназначенного для строительно-монтажных и т. п. работ. На рис. 3.12 приведен другой вариант решения той же задачи.
Рис. 3.11. Складной манипулятор:
1 — шарнирный транспортный манипулятор;
2 — рабочий манипулятор (а) или платформа с рабочим (б); 3 — носитель
Рис. 3.12. Манипулятор с перемещаемыми приводами:
1 — звенья механизма манипулятора; 2 — шарниры; 3 — фиксаторы (тормоза); 4 — перемещающийся привод шарниров
Рабочие органы манипуляторов
Рабочие органы манипуляторов служат для непосредственного взаимодействия с объектами внешней среды и делятся на захватные устройстваи специальный инструмент. Рабочие органы могут быть постоянными и съемными, в том числе с возможностью их автоматической замены входе выполнения технологической операции.
Захватные устройства.Они предназначены для того, чтобы брать объект, удерживать его в процессе манипулирования и освободить по окончании этого процесса. Существуют следующие основные типы захватных устройств: механические устройства-схваты, пневматические и электромагнитные. Кроме того, в связи с большим разнообразием объектов манипулирования разработано большое количество различных комбинаций этих типов захватных устройств и множество специальных захватных устройств, основанных на различных оригинальных принципах действия (например, клейкие захватные устройства, накалывающие, использующие аэродинамическую подъемную силу и т. п.).
Схват — это механическое захватное устройство, аналог кисти руки человека. Самые простые двухпальцевые схваты напоминают обычные плоскогубцы, но снабженные приводом. На рис. 3.13 показана конструкция подобного схвата с пневматическим приводом. В зависимости от объектов манипулирования применяют схваты с 3, 4 и реже с большим числом пальцев. На рис. 3.14 показан сложный схват с 3 пальцами, каждый из которых имеет по 3 подвижных звена и может также поворачиваться относительно продольной оси. Здесь использован эффект памяти формы, проиллюстрированный на рис. 3.10, б. Однако в связи с простотой совершаемых схватами движений ("зажим-разжим") в них обычно используются нерегулируемые пневматические и электрические приводы, значительно реже — гидравлические.
На рис. 3.15 показан пневматический схват с 5 гибкими надувными пальцами. За счет разной жесткости пальцев в сечении при подаче в них сжатого воздуха они изгибаются, захватывая находящиеся в их зоне предметы.
Схваты часто очувствляют с помощью контактных датчиков, датчиков проскальзывания, усилия и дистанционных датчиков (ультразвуковых, оптических и др.), выявляющих предметы вблизи схвата и между его пальцами.
В наиболее распространенном типе вакуумного захватного устройства использованы вакуумные присоски, которые удерживают объекты за счет разряжения воздуха при его отсосе из полости между присоской и захватываемым объектом. Для захватывания объектов сложной формы применяют вакуумные захватные устройства с несколькими присосками.
Рис. 3.13. Двухпальцевый схват: 1; 2 — пальцы (губки);
3; 4 — рычажная передача; 5 — шток пневматического двигателя
![]() |
(пневмоцилиндра); 6 — возвратная пружина.
Рис. 3.15. Пневматический схват с 5 гибкими надувными пальцами:
а — внешний вид; б — разрез пальца; 1 — тонкостенная часть;
2 — гофры; 3 — толстостенная часть; 4 — подвод воздуха;
5 — деформация оси пальца при подаче сжатого воздуха
Магнитныезахватные устройства используются для взятия ферромагнитных объектов. В роботах нашли применение в основном захватные устройства с электромагнитами, но имеются устройства и с постоянными магнитами. (Для освобождения захваченного предмета они снабжены специальными механическими выталкивателями.)
Захватные устройства бывают универсальными и специальными (для работы с хрупкими и протяженными предметами, тканями и т. д.).
Захватные устройства часто присоединяют к последнему звену манипулятора через промежуточные, податливые конструктивные элементы. С их помощью осуществляется компенсация возможных неточностей позиционирования и устраняются возникающие при этом механические напряжения в звеньях манипулятора в случаях манипулирования объектами, на перемещение которых наложены механические ограничения (механическая сборка и разборка, установка заготовок в зажимы и гнезда технологического оборудования, перемещение предметов по направляющей и т. п.).
Рабочий инструмент. Вслучаях, когда объектом манипулирования является рабочий инструмент, с помощью которого робот выполняет определенные технологические операции (нанесение покрытий, сварка, завинчивание гаек, зачистка поверхностей и т. п.), этот инструмент, как правило, не берется захватным устройством, а непосредственно крепится к манипулятору вместо него. Часто при этом к инструменту необходимо обеспечить подвод энергии или какого-либо рабочего тела. Для окрасочного робота — это краска и воздух к пульверизатору, для сварочного робота — сварочный ток к сварочным клещам при точечной сварке или проволочный электрод, газ и охлаждающая вода при дуговой сварке и т. д. Для этого требуется разработка специальной конструкции всего манипулятора.
Дата добавления: 2018-08-06; просмотров: 2794; Мы поможем в написании вашей работы! |
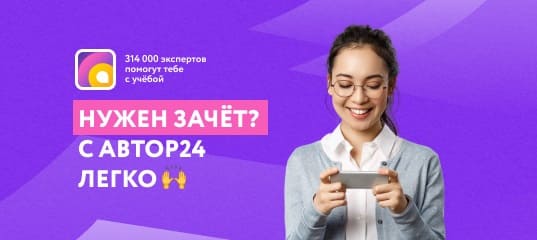
Мы поможем в написании ваших работ!