Получение пеностекла порошковым способом
Состав шихты | Температура и время вспенивания | Коэффициент вспенивания | Характеристика пеностекла | ||
объемная масса, кг/м3 | водопоглощение, % | предел прочности при сжатии, МПа | |||
Термическая обработка стекла
Отжиг
К термической обработке стекла относят процессы отжига, закалки, огневой полировки, кристаллизации и др.
Одной из важных технологических операций при производстве стеклоизделий является отжиг стекла – охлаждение изделия по определенному режиму, обеспечивающему такое распределение напряжений в стекле, которое гарантирует сохранность и длительную службу стеклоизделия в условиях тепловых и механических воздействий.
Технология отжига связана с релаксацией внутренних напряжений, то есть процессом постепенного самопроизвольного их исчезновения (ослабления) в стекле. В связи с этим, прежде всего, следует рассмотреть механизм возникновения напряжений в стекле, мысленно разбив торцевую сторону листа стекла на три слоя – ориентировочно по границам, на которых меняется знак напряжений (рис. 4.1).
Допустим, исходный образец имеет комнатную температуру, и напряжения в нем столь малы, что ими можно пренебречь. Если такой образец поместить в среду с повышенной температурой, то его поверхность нагреется, а центр ещё останется холодным. Появление температурного градиента вызовет появление напряжений, знаки которых на поверхности и в центре будут противоположными. В механике принято напряжения сжатия считать отрицательными, напряжения растяжения – положительными. Для того чтобы уверенно определять эти знаки в каждом конкретном случае, целесообразно использовать следующую схему рассуждений (рис. 4.2).
|
|
На рис. 4.2 Тн обозначает температуру наружных слоев стекла, Твн – внутреннего слоя. Пока эти температуры равны друг другу, напряжения в образце отсутствуют (рис. 4.2, а). Проведем мысленный эксперимент. Отсоединим друг от друга три рассматриваемых слоя (предположим, что сделаны тонкие распилы по границам слоев) (рис. 4.2, б).
При нагреве стекла температура наружных слоев превышает температуру внутреннего слоя. Соответственно линейные размеры наружных слоев оказались больше, чем размер внутреннего слоя (рис. 4.2, в). Такие размеры, которые соответствовали бы ненапряженному состоянию слоев, часто называют «свободными размерами». Но на самом деле в стекле слои связаны друг с другом, представляют единое целое, и их фактический линейный размер должен быть одинаков. Чтобы все слои привести к одному размеру, наружные слои следует сжать, а внутренний – растянуть. Действительно, в процессе нагревания стекла (как и любого другого твердого материала) в поверхностных его слоях возникают напряжения сжатия, а в центре – растяжения (рис. 4.2, г).
|
|
Рассуждая аналогичным образом, легко прийти к заключению, что в процессе охлаждения стекла в области температур ниже Тg, на его поверхности появляются напряжения растяжения, а в центре – сжатия.
Напряжения, о которых речь шла выше, появляются при возникновении температурного градиента по толщине изделия и исчезают после того, как исчез этот градиент. Напряжения эти называются временными. Возникновение временных напряжений характерно для всей области температур, где стекло можно рассматривать в качестве твердого тела (при температурах ниже Тg), то есть где эффектами релаксации напряжений можно полностью пренебречь.
Рассмотрим закономерности образования напряжений при охлаждении листа стекла от температур, существенно превышающих Тg.
Допустим, что при какой-то достаточно высокой температуре То лист стекла находился некоторое время, и температурный градиент по толщине листа отсутствовал. После этого температуру окружающей среды начали уменьшать с постоянной скоростью. Сначала начнут охлаждаться наружные слои листа, а затем его центральная часть (рис. 4.3)
|
|
![]() |
Скорость изменения температуры центра стекла сначала отстает от скорости охлаждения его поверхности, но через некоторое время она достигает той же величины. В результате создаются условия, при которых величина градиента температур по толщине листа стекла не будет меняться в процессе охлаждения.
Очевидно, что как только начнется процесс охлаждения листа стекла от Т0 и, следовательно, возникнет и будет постепенно увеличиваться градиент температур по толщине листа, в стекле должны возникать напряжения растяжения на поверхности и сжатия внутри. Однако вязкость стекла при этих температурах невелика, и напряжения будут очень быстро релаксировать.
После того, как будут достигнуты условия охлаждения листа с постоянной скоростью, в результате чего градиент температур по толщине стекла практически перестанет меняться во времени, новые напряжения не должны возникать. Это действительно так вплоть до того момента, когда температура поверхностного слоя не достигнет интервала стеклования. В интервале стеклования резко уменьшается термический коэффициент линейного расширения (ТКЛР) стекол (у листового стекла почти в три раза). В связи с разницей температур поверхности и центра охлаждаемого стекла, дилатометрические кривые, характеризующие изменение длин соответствующих слоев во времени, смещены относительно друг друга (рис. 4.4).
|
|
![]() |
В довольно широком временном интервале (Δτσ) ТКЛР внутреннего и наружных слоев оказываются различными. Это значит, что свободный размер внутреннего слоя будет уменьшаться быстрее, чем свободные размеры наружных слоев. На поверхности листа стекла возникнут напряжения сжатия, в центре – растяжения. Конечно, эти напряжения также будут релаксировать. Однако в интервале стеклования вязкость уже относительно велика, и процессы релаксации в этой области идут с гораздо меньшей скоростью, чем при более высоких температурах. В итоге большая часть возникающих в рассматриваемой области напряжений сохраняется, и равномерно охлаждаемый лист стекла после затвердевания находится в напряженном состоянии. При этом в листе сохраняется постоянный температурный градиент. На каком-то этапе, при приближении к комнатной температуре, скорость охлаждения затвердевшего стекла начинает уменьшаться. Одновременно уменьшается и градиент температур, который при завершении охлаждения исчезает вовсе. Температура внутреннего слоя на завершающем этапе охлаждения изменится сильнее, чем температура наружных слоев. В результате свободный размер внутреннего слоя уменьшится в большей степени, чем свободные размеры наружных слоев. Это приведет к усилению напряжений сжатия на поверхности. Общая температурная зависимость напряжений в центре образца, охлажденного по описанному выше режиму, имеет характер, изображенный на рис. 4.5.
Согласно рассмотренному механизму при охлаждении стекла от температур существенно выше Тg возникают постоянныеилиостаточные напряжения.На уменьшение величины этих напряжений направлен процесс отжига стеклоизделий. Приведенные рассуждения показывают, что уменьшить остаточные напряжения можно путем снижения скорости охлаждения стеклоизделия в интервале стеклования
Процесс отжига характеризуется следующими терминами и параметрами.
Верхняя температура отжига (Тво) –температура, отвечающая вязкости стекла 1012 Па∙с. При этой температуре напряжения в стекле уменьшаются в 10 раз за время, равное 5 мин.
Нижняя температура отжига (Тно)– температура, отвечающая вязкости 1013,5Па∙с. При ней напряжения уменьшаются в 10 раз за время в 100 раз большее, чем при верхней температуре отжига. Отжиг может идти и ниже этой температуры, но крайне медленно.
Зона отжига– интервал между верхней и нижней температурами отжига. Обычно он составляет 50…60° в зависимости от состава стекла. На практике увеличивают этот интервал до 100…150°С.
Нормы допустимых напряжений (Δ, нм/см) задаются стандартами и техническими условиями в зависимости от вида, назначения изделий и условий их эксплуатации. Так, для оптики допустимые напряжения составляют 2…50; листового флоат стекла – 25…30; прокатного – 40…60; листового тянутого (ВВС) – до 100; тара – 50…300 нм/см.
Процесс отжига состоит из следующих стадий:
1. Предварительного нагрева или охлаждения – изделия должны быть доведены до заданной температуры отжига со скоростью, не вызывающей их разрушения.
2. Выдержки при верхней температуре отжига в течение времени, достаточного для заданного уменьшения напряжений.
3. Медленного охлаждения – изделия охлаждаются до нижней температуры отжига с достаточно малой скоростью, не допускающей возникновения новых постоянных напряжений, превышающих заданные.
4. Быстрого охлаждения – изделия охлаждаются со скоростью, обеспечивающей допустимые временные напряжения.
Работа 4.1.Расчет режима отжига
Режим отжига определяется физико-химическими свойствами стекла, формой и размерами изделий, технологией их изготовления, конструкцией печи отжига, допустимой величиной остаточных напряжений.
Существует целый ряд методов расчета, предложенных различными авторами. Далее приводится расчет, основанный на рекомендациях Адамса и Вильямсона.
Скорость на первом этапе отжига рассчитывают по формуле, град/мин:
где а – полутолщина листа стекла, см. При расчете режима отжига для полых равнотолщинных изделий принимают удвоенную толщину стенки, в случае разнотолщинных изделий – наибольшую толщину.
Продолжительность выдержки на втором этапе при верхней температуре отжига, мин:
.
Выдержку можно производить при любой температуре, лежащей в зоне отжига, однако следует учитывать, что понижение температуры на каждые 10°С увеличивает время релаксации напряжений примерно в 2 раза. Время выдержки при любой температуре (Т) зоны отжига рассчитывают по формуле, мин:
.
Значительно понижать температуру выдержки нецелесообразно в связи с лишними энергетическими затратами.
Скорость ответственного охлаждения на третьем этапе отжига составляет, град/мин:
.
Скорость быстрого охлаждения, град/мин:
.
Результатом расчета является установление температурно-временного режима отжига.
Пример. Рассчитать режим отжига бесцветной бутылки вместимостью 0,5 л следующего химического состава (марка БТ-1), мас. %: 72,5 SiO2; 2,5 Al2O3; 8 CaO; 3 MgO; 14 Na2O. Толщина стенки изделия составляет 3 мм (а = 0,6 см).
Вычисляют верхнюю температуру отжига (°С) любым известным способом, например, по методу Охотина,:
Т12 = –6,14.14 + 3,15.11 + 3,78.2,5 + 598,03 = 556,17 ≈ 556.
Штучные изделия помещают в печь отжига после формования. При этом для закрепления формы они охлаждаются до температуры ниже верхней температуры отжига (450…500°С). Для расчета принимаем эту температуру 480оС.
Первым этапом отжига является нагрев до Тво. Рассчитывают V1, град/мин, и время τ1, мин, первой стадии:
Время выдержки при Тво составит, мин:
τво = 95×0,62 = 34,2.
Нижнюю температуру отжига принимают на 150° ниже Тво, то есть Тно= (556 – 150) = 406. Определяют скорость и время ответственного охлаждения:
Рассчитывают скорость и время охлаждения изделий до комнатной температуры (20°С) на последней стадии процесса отжига:
Таким образом, общая продолжительность процесса отжига составит, мин:
τ = 1,1 + 34,2 + 15,5 + 11,1 = 61,9.
Расчет режима отжига по приведенной методике рекомендуется выполнять в курсовых и дипломных проектах.
Закалка
Закалкой называется процесс тепловой обработки (нагрев и быстрое охлаждение) стекла, приводящий к образованию остаточных напряжений сжатия во внешних слоях и растяжения во внутренних (см. рис. 4.1), в результате чего повышается механическая прочность, термостойкость и характер разрушения.
Процесс закалки отличается от процесса отжига двумя особенностями.
1. Температура окружающего воздуха не снижается постепенно, а резко изменяется до 20°С.
2. Интенсивность движения воздуха, отбирающего тепло от листа стекла, во много раз превышает конвективное движение воздуха.
В результате характер изменения во времени температур поверхности и центра охлаждаемой пластины (рис. 4.6) резко отличается от такового при отжиге (см. рис. 4.3).
Как видно из рис. 4.6, зависимость разности температур ∆Т от времени, которая играет решающую роль в процессах закалки, может быть разделена на две части. Сначала величина ∆Т быстро возрастает, а потом начинает постепенно уменьшаться. Область, расположенная правее максимума ∆Т, называется областью регулярного охлаждения. В этой области скорость охлаждения не зависит от Т0.
При интенсивной закалке, в отличие от отжига, температура отдельных участков стекла может различаться на десятки градусов, иметь сильно отличающиеся вязкости и, следовательно, совершенно различные скорости релаксации напряжений. В результате эпюры напряжений в процессе закалки стекла имеют весьма сложный характер.
Степень закалки ∆ зависит от свойств и толщины стекла и интенсивности охлаждения и может быть рассчитана по формуле:
где В – оптическая постоянная напряжений, МПа–1; α – термический коэффициент линейного расширения, град–1; Е – модуль Юнга, МПа; μ – коэффициент Пуассона; Тg – температура стеклования, °С; φ(δ) – функция, зависящая от параметров охлаждения.
Важные задачи рационального выбора режима закалки – определение температуры Т0 и интенсивности охлаждения. Влияние начальной температуры (Т0) и толщины листа стекла на степень закалки в условиях естественной конвекции, то есть при охлаждении на воздухе без дополнительного обдува показано на рис. 4.7.
![]() |
Как видно, характер зависимости степени закалки от начальной температуры одинаков для образцов любой толщины: при значениях Т0, превышающих некоторую критическую величину (в данном случае ~ 580°С), степень закалки остается постоянной и максимальной. Если Т0 опускается ниже этого критического значения, градиент температур по толщине образца не успевает к моменту подхода температуры поверхности стекла к Тg достичь своего максимального значения, а возникающие в результате роста градиента напряжения не успевают полностью релаксировать. Очевидно, что чем ниже Т0, тем в меньшей степени успевает пройти релаксация напряжений и в результате тем ниже степень закалки. При Т0 < 450°С стекло практически является твердым телом, возникновение температурного градиента приводит лишь к появлению временных, неспособных к релаксации напряжений, которые исчезают, как только в охладившемся стекле устанавливается постоянная температура.
Очевидно также, что степень закалки при прочих равных условиях должна сильно возрастать с толщиной стекла, что показано на рис. 4.7.
Для обычного закаленного стекла типичные напряжения сжатия на поверхности составляют около 200 МПа. Если принять прочность отожженного стекла на растяжение, равной 50 МПа, и учесть, что на его поверхности напряжения сжатия равны 2…4 МПа, то можно считать, что прочность закаленного стекла составляет 250 МПа, то есть в ~ 5 раз превышает прочность отожженного стекла.
Повышение прочности – не единственное преимущество закаленного стекла. Второе его достоинство, в ряде случаев не менее важное, заключается в том, что при разрушении закаленное стекло разлетается на мелкие осколки сотообразной формы. Эти осколки менее опасны, чем крупные, острые, нередко имеющие ножевидную форму осколки отожженного стекла. Описанный характер разрушения закаленного стекла связан с тем, что при первоначальном разломе этого стекла на поверхности оказываются участки, находящиеся под сильным напряжением растяжения. От этих участков многочисленные трещины проходят вглубь образца, разветвляясь и соединяясь друг с другом.
Однако неизбежное разрушение закаленных листов стекла при любом нарушении их целостности имеет и отрицательное значение: такое стекло после закалки нельзя резать, сверлить и т.п. Закаленное стекло нужно изготовлять на заводе такой формы и размеров, которые позволяют сразу же монтировать их в соответствующие оконные проемы. Это легко осуществить при изготовлении закаленных стекол для остекления транспорта, но пока что этот фактор является серьезным препятствием для широкого применения закаленных стекол в строительстве.
Технологическая схема закалки стеклянных изделий включает две стадии:
− нагревание изделий до температуры закалки по определенному режиму, зависящему от химического состава стекла, формы и размеров изделий, а также интенсивности его последующего охлаждения;
− охлаждение изделий при помощи различных охлаждающих сред по определенному режиму, обеспечивающему большие теплосъемы с поверхности подвергаемого закалке изделия в короткие промежутки времени.
Процесс нагревания стекла до температуры закалки должен протекать равномерно. Температура закалки (Тз) зависит от химического состава стекла и может быть рассчитана как (Тg + 80)°С или как соответствующая логарифму вязкости 9 (Па.с).
Температура и продолжительность нагревания стекол взаимосвязаны. Чем выше температура в печи, тем менее продолжительным должно быть нагревание. Продолжительность нагревания при температуре закалки может быть определена из расчета 35…50 с на 1 мм толщины стекла.
Нагревание стекла проводится в электрических печах сопротивления.
Скорость охлаждения определяет степень закалки, а, следовательно, и основные свойства закаленного стекла: механическую прочность, термостойкость, характер осколков при разрушении.
Охлаждение производится при помощи различных охлаждающих сред: воздуха, масел, жиров, металлов и др. Наибольшее распространение получили способы закалки стекол воздухом. В зависимости от способа омывания воздушным потоком и его направления по отношению к закаляемым поверхностям различают такие способы закалки, как:
− закалка в условиях воздушной конвекции, при которой закаляемое изделие подвергается естественному охлаждению за счет излучения в окружающую среду и конвекционных потоков окружающего изделие воздуха, образующихся благодаря местному нагреванию воздуха у горячих стенок изделия;
− воздухоструйная закалка, при которой на поверхность закаляемого изделия симметрично под давлением подается множество перпендикулярно направленных воздушных струй;
− центрированная закалка, предусматривающая перпендикулярную подачу в центры охлаждаемых поверхностей по одной мощной воздушной струе под давлением;
− метод отсоса воздуха, характеризуемый параллельным направлением воздушных потоков по отношению к закаляемым поверхностям изделия.
Создание равномерно распределенных напряжений при закалке полых изделий (сортовая посуда, колпаки, изоляторы и др.) осложняется разнотолщинностью и сложностью их геометрической формы.
Дата добавления: 2018-08-06; просмотров: 326; Мы поможем в написании вашей работы! |
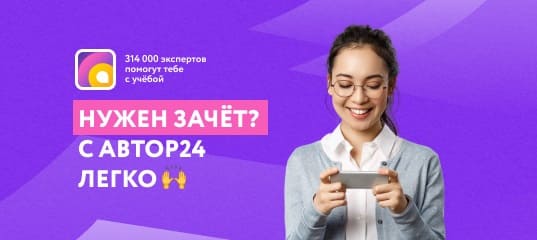
Мы поможем в написании ваших работ!