Объясните схему и принцип действия инерционно-центробежного пылеуловителя.
Конструкция инерционно-центробежного пылеуловителя представлена на рисунке. Аппарат включает корпус, внутри которого размещен завихритель, выполненный в виде полого диска, состоящего из верхней и нижней стенки. Внутри завихрителя расположены закручивающие лопатки. По оси корпуса проходит патрубок ввода запыленного газа, примыкающий к нижней стенке завихрителя. Концентрично снаружи патрубка ввода установлен патрубок вывода очищенного газа. По наружному нижнему краю диска завихрителя установлен экран в виде усеченного конуса. В нижней части корпуса расположен бункер для сбора пыли.
Рисунок - Конструкция инерционно-центробежного пылеуловителя
1-корпус; 2-завихритель; 3-верхняя стенка; 4-нижняя стенка; 5-закручивающие лопатки; 6-патрубок ввода запыленного газа; 7-патрубок вывода очищенного газа; 8-экран; 9-бункер для сбора пыли
Пылеуловитель работает следующим образом. Запыленный газ через входной патрубок поступает в завихрительное устройство, в котором расположены лопатки, способствующие закручиванию пылегазового потока.
Отделение частиц пыли в закрученном потоке происходит под действием центробежных сил в пространстве между корпусом и экраном. Вихревой поток, опускаясь по спирали вниз, поворачивает на 180° и по внутренней спирали меньшего радиуса попадает под экран. Далее, снова изменив свое направление на 180°, уже очищенный газ поступает в патрубок вывода. Отделившаяся пыль по стенке корпуса под действием силы тяжести опускается в нижнюю часть корпуса и собирается в бункере.
|
|
Расположение входного патрубка по центру аппарата обеспечивает сохранение высокой скорости газа (до 20 м/с) в верхней части аппарата, в отличие от обычных циклонов, где в зоне ввода очищаемого потока скорость падает до 2-4 м/с. Такое конструктивное решение существенно увеличивает центробежную силу и тем самым значительно повышает эффективность пылеулавливания.
Эффективность разделения пылевоздушной смеси – 98,6%.
Расскажите о защите атмосферы от вредных выбросов прокатного производства.
Около 90% всей выплавляемой стали поступает на прокатку. Прокатка- это деформация металла, сдавливание его вращающимися валками.
По сравнению с другими переделами черной металлургии в прокатном производстве образуется меньше пыли и газов. Основными источниками загрязнения атмосферного воздуха в прокатном производстве являются:
· нагревательные печи,
· травильные агрегаты,
· станы горячей прокатки, над которыми образуются пылевыбросы, содержащие окалину (оксиды железа) и другие металлы в зависимости от степени легирования стали и сплава.
|
|
Эти выбросы поступают через аэрационный фонарь в атмосферу.
Выбросы нагревательных печей содержат оксиды азота. Для очистки дымовых газов нагревательных печей прокатных цехов от оксидов азота предусматриваются ванадиевые катализаторы, встроенные в котлы-утилизаторы.
При горячей прокатке металла пыль образуется в результате измельчения окалины валками и испарения вследствие мгновенного увеличения давления и повышения температуры.
Локализацию и удаление пыли, выделяющейся при прокатке, осуществляют различными способами. В мелких прокатных станах устанавливают зонты на высоте 2,4 м, чтобы не мешать обслуживанию стана (рисунок).
1-зонт; 2-бесфланцевое соединение; 3-воздухопровод запыленного воздуха |

Рисунок - Обеспыливание клетей прокатных станов
Наилучшие результаты в пылеподавлении показал смыв пыли компактной струей воды в месте её образования.
Вода подается на прокатываемый металл в месте выхода его из валков и отводится по специальному желобу. При прокате листа толщиной 2 мм коэффициент обеспыливания составляет 98-99%. При этом дополнительного, нежелательного охлаждения листа практически не происходит.
|
|
Рисунок - Схема системы гидросмыва на клети прокатного стана
1 - прокат; 2 - гибкий шланг, 3 - водопроводная труба, 4 - сдвижной хомут, 5 - сопло.
При прокатке специальных сталей подача воды недопустима. В этом случае следует применять вентиляционные системы с зонтами.
При холодной прокатке металла на валки стана для охлаждения подается эмульсия. Часть эмульсии испаряется из-за разогрева валков и в виде паров распространяется по цеху, конденсируясь на конструкциях и оборудовании. Пары эмульсии очень агрессивны и наносят большой вред оборудованию, особенно электроаппаратуре и отопительным агрегатам.
Для локализации паров эмульсии на стане холодной прокатки предусматривают укрытия, из которых отсасывается воздух на каждом межклетевом пространстве 70% из верхней зоны и 30% - из нижней.
Для удаления окалины с поверхности горячекатаных изделий на большинстве заводов применяют травление в серной или соляной кислоте, которое можно осуществлять периодически и непрерывно.
При травлении металлов в кислотах в атмосферу выделяется большое количество вредных газов и паров: оксиды азота, фтористый водород, пары серной кислоты, соли металлов.
|
|
Периодическое травление применяют в трубном производстве и при подготовке листов к нанесению защитных покрытий (например, оцинкование).
Рисунок - Борьба с выбросами паров в травильных отделениях
1 -двойная крышка; 2-гидравлические затворы у бортов
Для уменьшения выделений паров кислот из ванн ванны снабжают двойными крышками и гидравлическими затворами у бортов (рисунок). Также сокращению испарений способствуют пенообразующие добавки.
Для обезвреживания выбросов травильных агрегатов применяются газоочистные системы, где могут использоваться пенные аппараты (рисунок а), полые скрубберы (рисунок б), низконапорные скрубберы Вентури (рисунок в):
Рисунок - Возможные схемы очистки газов травильных отделений от паров кислот
1-травильное отделение; 2-пенный фильтр; 3-дымосос; 4-дымовая труба; 5-скруббер;
6-труба Вентури; 7- каплеуловитель
Билет № 16.
Дата добавления: 2018-08-06; просмотров: 350; Мы поможем в написании вашей работы! |
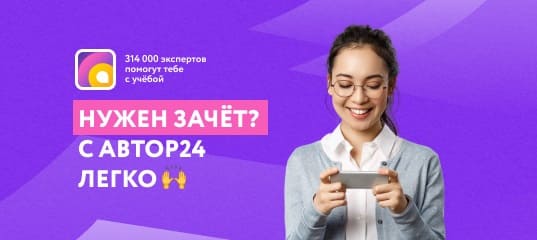
Мы поможем в написании ваших работ!