Получение машиностроительных профилей волочением. Сущность, схема и назначение волочения. Достоинства и недостатки волочения. Показатели деформации при волочении.
Сущность процесса пластического деформирования металлов. Место и роль обработки металлов давлением в машиностроении. Основные технико-экономические показатели процессов обработки металлов давлением: коэффициент использования металла, коэффициент точности поковки.
Обработка Ме давлением объединяет технологические процессы формоизменения за счет пластической деформации, в результате воздействия на деформируемое тело(заготовку) внешних сил. При пластической деформации изменение формы и размеров, вызванные действием внешних сил, сохраняются после прекращения действия этих сил.
Значительным преимуществом обработки давлением перед резанием является возможность существенного снижения отхода Ме, а также, повышения производительности, поскольку в результате однократного приложения нагрузки можно значительно изменить форму и размеры тела, кроме того пластическая деформация сопровождается изменением физико-механических свойств материала заготовки, что позволяет получать изделия с заданными эксплуатационными характеристиками.
В процессе пластической деформации Ме упрочняется. Упрочнением называется увеличение сопротивляемости материала деформации. Упрочнение при пластической деформации называется наклепом.
Наклеп объясняется значительным повышением количества дефектов кристаллического строения в процессе деформации. Наибольшее значение имеет повышение дислокации.
|
|
В результате деформации уменьшается плотность Ме, снижается сопротивляемость к коррозии, повышается электросопротивление.
Основным показателем прогрессивности норм расхода материалов является коэффициент использования. Чем ближе коэффициент использования к единице, тем более прогрессивна выбранная технология изготовления той или иной детали. Коэффициент использования металла (КИМ) определяется, как отношение массы детали (чистого веса) к норме расхода металла на изготовление детали.
Для сопоставления различных технологических процессов и оборудования по их эффективности применяют обобщенный показатель точности, называемый коэффициентом использования металла поковки при механической обработке:
Kим=МД/ МЗ
Где МД и МЗ- масса готовой детали и заготовки.
Этот показатель характеризует степень совершенства формы поковки. В идеальном случае, когда для поковки не требуется механическая обработки, Kим = 1. Для поковок свободной ковки Kим = 0,05-0,3; для горячей объемной штамповки 0,5-0,8; для холодной объемной и листовой штамповки 0,8-1
Коэффициент точности поковки это отношение массы деталей, изготовленных из одной поковки к массе поковки
|
|
где Кп - коэффициент точности поковки; Мд - масса детали; Мп - масса поковки
Этот коэффициент показывает объем последующей механической обработки. При ковке его значение составляет – 0,3; при штамповке на молоте, в открытом штампе – 0,45; при штамповке на горизонтальной ковочной машине в закрытом штампе – 0,55.
Факторы, влияющие на пластичность металлов: температура, скорость, степень деформации; химический состав и микроструктура материала. Понятие о механической схеме деформации. Схемы напряженного и деформированного состояния при обработке металлов давлением.
Температура оказывает наиболее значительное влияние. Обычно с повышением температуры пластичность возрастает.
Степень и скорость деформации оказывают на Ме одновременно упрочняющие и разупрочняющие действия.
С увеличением степени деформации с одной стороны – увеличивается наклеп Ме, следовательно, снижается пластичность с другой стороны, интенсивнее протекает процесс рекристаллизации, что ведет к разупрочнению Ме и повышении пластичности.
Аналогично увеличение скорости деформации уменьшает время протекания процесса рекристаллизации, следовательно, ухудшает пластичность, но с увеличением скорости деформации увеличивается количество выделившееся теплоты, которое не успевает рассеется в ОС, в результате Ме нагревается, пластичность повышается.
|
|
Химический состав материала заготовки регламентируется ГОСТом. К вредным примесям ухудшающим пластичность относят серы фосфор и газы(азот, кислород, водород).
Микроструктура: пластичность тем выше, чем мельче зерно и однороднее структура.
Механическая схема деформации это совокупность схем главных напряжений и их главных деформаций.
Всего существует 9 различных схем главных напряжений:
- 2 линейные
- 3 плоские схемы
- 4 объемных
При всем многообразии схем главных напряжений может реализоваться только 3 схемы главных напряжений:
Механические схемы деформации определяют характер формообразования.
Влияние схем деформации на пластичность тем заметнее(больше), чем менее пластичен материал по природе.
Наилучшей схемой, с точки зрения пластичности, является неоднородное всестороннее сжатие.
Нагрев Ме перед обработкой давлением. Назначение. Выбор температурного интервала обработки металлов давлением. Дефекты, возникающие при нагреве заготовок: перегрев, пережог. Понятие о горячей и холодной деформации, их влияние на структуру.
|
|
Для повышения пластичности и снижения сопротивления деформированию, Ме и сплавы перед деформацией нагревают. Температура нагрева, как правило, превышает температуру рекристаллизации. При нагреве на поверхности заготовок образуется слой оксидов, который называют окалиной. Толщина этого слоя зависит от температуры нагрева и времени. Наиболее сильно Ме и сплавы окисляются при температурах выше 9000 С. Нагрев углеродистых сталей приводит также к выгоранию углерода поверхностного слоя на глубину до 2-х мм. Этот процесс называют обезуглероживанием. Обезуглероживание приводит к снижению прочности поверхностного слоя и является наиболее опасным для заготовок небольших размеров с небольшими припусками на механическую обработку.
Для снижения окалинообразования и обезуглероживания применяют нагрев в защитных атмосферах , скоростной нагрев, различные обсыпки и обмазки.
Выбор температуры нагрева определяется природой материала. Для стали: нижней границей температурного интервала является температура 7270 С, верхняя граница на 1000-1500 С ниже температуры плавления. При нагреве на более высокие температуры в сталях возникают 2 вида дефектов:
- перегрев
- пережог
При перегреве значительно увеличивается размер зерен, что уменьшает пластичность. В большинстве случаев этот вид брака может быть устранен дополнительной обработкой давлением и нормализацией.
Пережог возникает при нагреве стали до температур близких температуре плавления и заключается в окислении границ зерен, в результате связь между зернами нарушается и Ме рушится в процессе обработки давлением. Пережог является неисправимым дефектом. Время нагрева определяют исходя из 2-х противоречивых факторов: с одной стороны для уменьшения времени окалинообразования и повышения производительности труда необходимо сократить время нагрева, с другой стороны, чтобы избежать образования трещин, необходимо уменьшать скорость нагрева, т.е. увеличить продолжительность. В первом, приближенное время нагрева определят по формуле Доброхотова
здесь D – диаметр или сторона квадрата заготовки, k – коэффициент, зависящий от марки стали(для углеродистых и низкоуглеродистых сталей – k = 10, для высоколегированных сталей – k = 20), α – это коэффициент, учитывающий способ укладки заготовки в печи(чем плотнее уложены заготовки, тем выше α: 1≤ α ≤1,25)
Процесс охлаждения при обработке давлением является не менее ответственны, чем нагрев. Скорость охлаждения не должна превышать критических значений, во избежание коробления и образования трещин. В особых случаях в процессе охлаждения возможны выдержки при одной, 2-х, редко 3-х температурах.
Деформирование Ме подразделяют на холодное и горячее, в зависимости от температуры.
Холодное деформирование проводят при температурах ниже температуры рекристаллизации, Ме при этом наклепывается и сохраняет наклеп.
Горячее деформирование проводят при температурах выше температуры рекристаллизации, при этом наклеп, полученный в результате пластической деформации, частично или полностью снимается параллельно протекающим процессам рекристаллизации.
В отличие от статической рекристаллизации(протекающая при нагреве), рекристаллизация, протекающая во время деформации называется динамической.
Изготовление машиностроительных профилей методом прокатки Ме. Сущность и назначение прокатки. Показатели величины деформации процесса прокатки. Основные виды прокатки (продольная, поперечная и поперечно-винтовая), их схемы. Условие захвата Ме валками при продольной прокатке. Инструмент для прокатки. Понятие о ручье и калибре валков.
Машиностроительный профиль-это длинномерное изделие с определенной формой поперечного сечения. Наиболее распространенным методом получения машиностроительных профилей является прокатка.
В основе прокатки лежит схема ротационного обжатия вращающимися валками, которая обусловлена силами трения между вращающимся инструментом и заготовкой. Благодаря силе трения заготовка перемещается в зазоре между инструментами одновременно деформируясь.
Наиболее распространенный вид прокатки – продольная. При продольной прокатке оси валков параллельны, валки вращаются в противоположных направлениях.
При поперечной прокатке, валки вращаются в боковом направлении, оси валков параллельны. Валки придают вращение заготовке одновременно.
При поперечно-винтовой прокатке, валки расположены под определенным углом и сообщают заготовке одновременно при деформировании вращательное и поступательное.
Условие захвата Ме при продольной прокатке
Для осуществления процесса прокатки необходима определенная величина сил трения. На заготовку со стороны валков действует нормальная сила N и сила трения. Спроецировав эти силы можно вывести условие захвата заготовки валками.
Nx < Tx
Nsinα < Tcosα
T=fN (f – коэффициент трения)
Nsinα < fNcosα
f>tgα –условие захвата
При горячей прокатке угол захвата α составляет 150 – 200, при холодной 50 – 80.
В процессе деформирования толщина заготовки уменьшается, длина и ширина – увеличиваются.
Величина деформации определяется относительным обжатием:
Для определения величины деформации используют также коэффициент выдержки, который определяется
l0 и F0 – длина и площадь поперечного сечения заготовки, l1 и F1 – длина и площадь поперечного сечения готовой детали.
Инструментом для прокатки являются валки. Валки могут быть гладкими(для прокатки листа), ступенчатыми(для прокатки полосы) и ручьевыми(для фасонного проката).
Формообразующей частью валка является бочка. Трефа служит для передачи крутящего момента от движения к валку. Переходная часть от трефы к бочке называется шейкой.
Ручьем называют вырез на боковой поверхности валка, а совокупность двух ручьев образуют калибр, соответствующий профилю проката.
Каждая пара ручьевых валков как правило образует несколько калибров.
Получение машиностроительных профилей волочением. Сущность, схема и назначение волочения. Достоинства и недостатки волочения. Показатели деформации при волочении.
Волочение заключается в протягивании заготовки через сужающееся отверстие в инструменте. Инструмент называется волоока или фильера.
При волочении S поперечное сечение заготовки уменьшается, принимая форму и размеры отверстий волооки. Следовательно длина изделия увеличивается.
Степень деформации оценивают коэффициентом вытяжки:
В заготовке при волочении притягивается тянущая сила, поэтому в очаге деформации Ме испытывает растягивающее напряжение, поэтому коэффициент вытяжки за 1 проход не превышает 1,3.
Волочение используют как для получения сплошных профилей, так и для изменения диаметра труб.
При волочении труб без оправки изменяется только внешний диаметр трубы без изменения толщины стенки.
При волочении с оправкой изменяется как диаметр, так и толщина трубы, которая определяется зазором между диаметрами оправки и выходного отверстия.
Для изменения сил трения при волочении применяют различные смазки, а также полирование выходного отверстия волооки.
Обычно для получения требуемого профиля требуется значительная деформация, которую невозможно обеспечить за один проход, поэтому применяют волочение через ряд последовательно расположенных фильер с постоянно уменьшающимся сечением. Т.к. при деформации имеет место значительный наклеп между проходами, проводят отжиг, снимающий напряжение. Волочение позволяет получить высокую точность геометрических размеров, низкую шероховатость поверхности и обеспечивает получение очень тонкостенных профилей.
Получение машиностроительных профилей прессованием. Виды прессования (прямое, обратное и комбинированное), их схемы. Показатели деформации при прессовании. Неоднородность пластического течения при прессовании.
Прессование заключается в выдавливании Ме из замкнутой полости через отверстие необходимого профиля. Прессованием можно получать изделия сплошного и полого сечения.
При прямом прессовании направление течения Ме совпадает с направлением движения пуансона.
При обратном прессовании направление течения Ме противоположно направлению движения пуансона.
При комбинированном прессовании направление Ме как против, так и по направлению пуансона.
При прессовании весь Ме не может быть выдавлен из пресс формы. Часть его остается в виде прессостатка.
При прямом прессовании объем прессостатка составляет 18-20%, при обратном 5-6%.
При прессовании Ме подвергается всестороннему неравномерному сжатию, что позволяет деформировать Ме с малой пластичностью, которое невозможно обработать другими методами.
Изготовление поковок машиностроительных деталей свободной ковкой. Сущность, область применения. Понятие о свободной осадке: разновидности, схемы, инструмент, достоинства. Неоднородность деформации при свободной осадке цилиндрической заготовки.
Для получения крупногабаритных поковок, массой выше 1 тонн, единственно возможным методом является ковка. Ковка – вид горячей обработки давлением, при котором Ме деформируется с помощью универсального инструмента. Универсальным инструментом для ковки являются бойки, которые могут быть плоскими или вырезными.
При ковке Ме свободно течет в стороны неограниченными рабочими поверхностями инструмента. Процесс ковки состоит из чередования в определенной последовательности основных и вспомогательных операций.
К основным операциям ковки относят:
-осадка
-протяжка
-прошивка
-гибка
-отрубка
Осадкой называется операция уменьшения высоты заготовки при увеличении ее площади поперечного сечения.
Осадку проводят бойками или подкладными плитами.
Разностью осадки является высадка, при которой Ме осаживается только на часть длины заготовки.
Заготовки с соотношением более 2,5 осадке не подвергают из-за опасности потери устойчивости.
Течение Ме при осадке сопровождается скольжением его по поверхности инструмента. В результате на поверхности заготовка-инструмент возникают силы контактного трения, которые направлены против течения материала. Наличие сил контактного трения повышают износ инструмента, увеличивают деформирующие усилия и являются причиной неоднородности деформации.
Паковка после осадки имеет характерную бочкообразную форму. Распределение деформации в объеме заготовки неоднородно. Выделяют 3 характерные зоны.
Зона 1. Зона затрудненной деформации(застойная зона). Из-за действия сил трения деформация в этой зоне минимальна.
Зона 2. Зона интенсивной пластичной деформации. Называется деформационный крест.
Зона 3. Промежуточная. Деформация больше чем в первой, но меньше чем во второй.
В зоне 2 напряженное состояние соответствует всестороннему сжатию на боковой поверхности, в зоне 3 возникают растягивающие напряжения, что может привести к образованиям трещин на бочке образца.
Дата добавления: 2018-08-06; просмотров: 775; Мы поможем в написании вашей работы! |
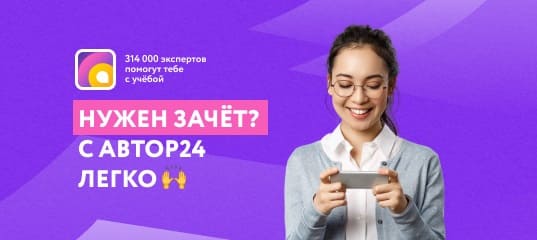
Мы поможем в написании ваших работ!